Ölçüm odasında, üretimde, gelen mallarda ve geliştirme alanında kalite kontrol için yüksek kaliteli metroloji.
Gear Metering Pumps & Meter Mix Dispense Machines with highest accuracy for processing liquids and pastes.
High-precision rotary stroke bearings for backlash-free linear and rotational movements for use in machine and device construction.
Metrology Form ve pozisyon metrolojisi Mil ölçüm teknolojisi Dişli ölçüm teknolojisi Optik metroloji İkinci el makine portalı
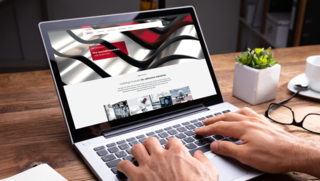
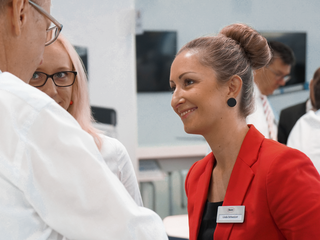
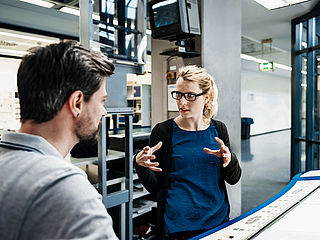
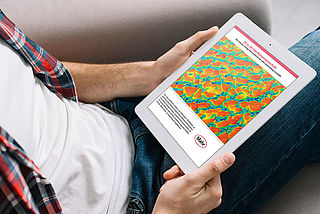
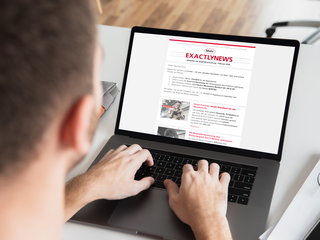
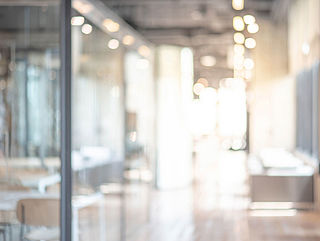
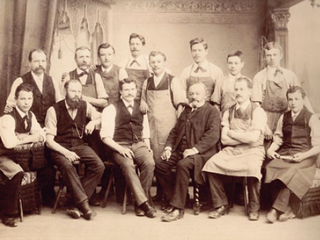
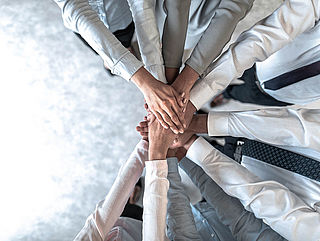
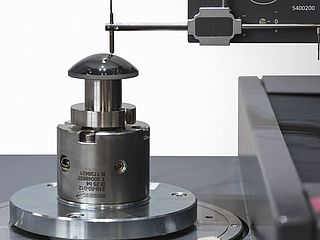
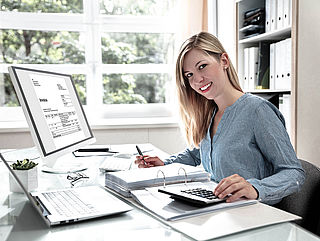
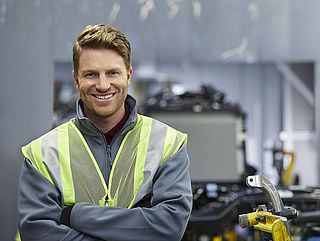
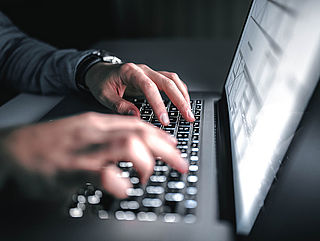
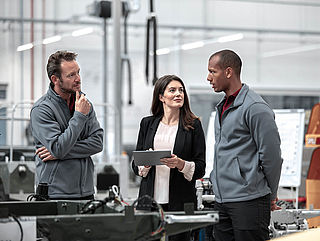
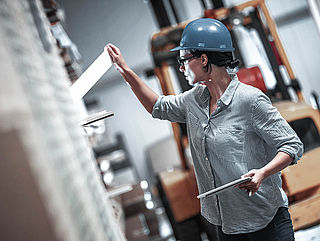
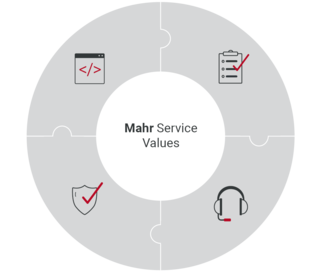
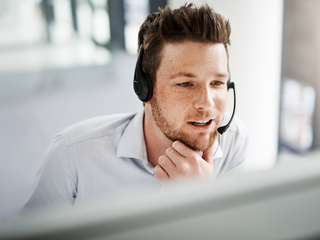
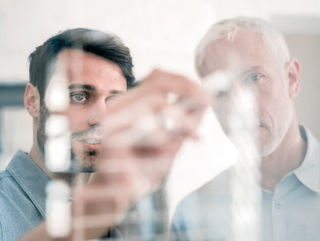
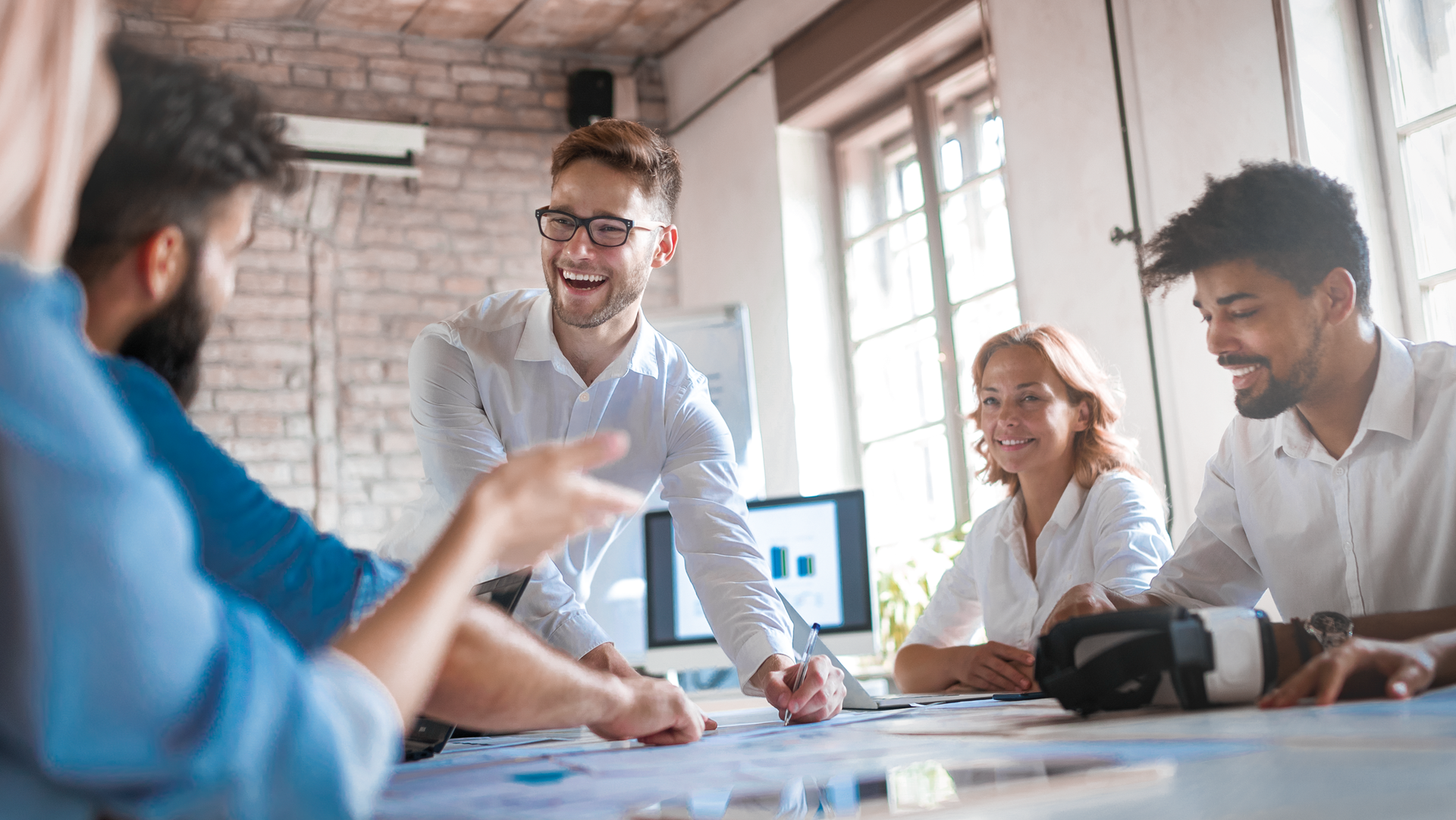
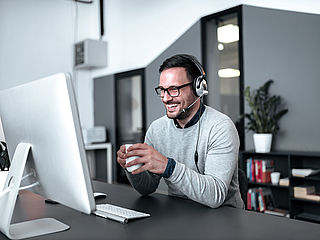
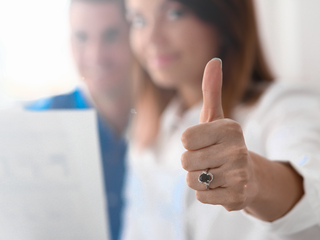
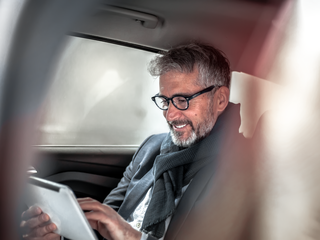
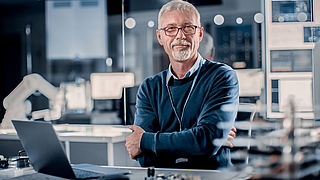
As an internationally active company, Mahr holds its patents not only in Germany, but worldwide.
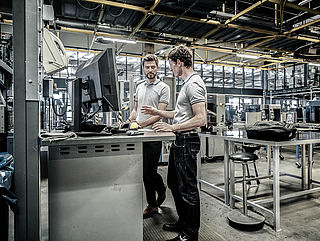
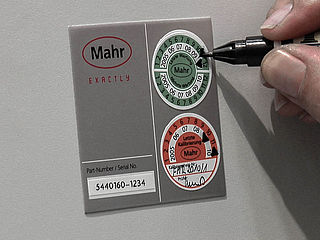
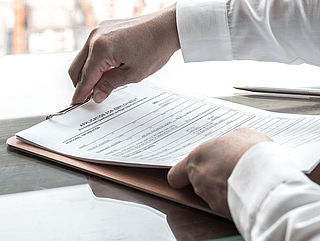
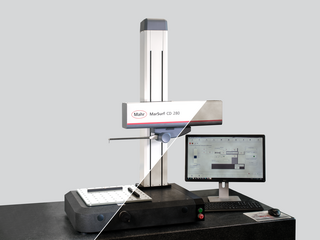
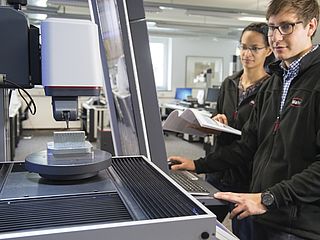
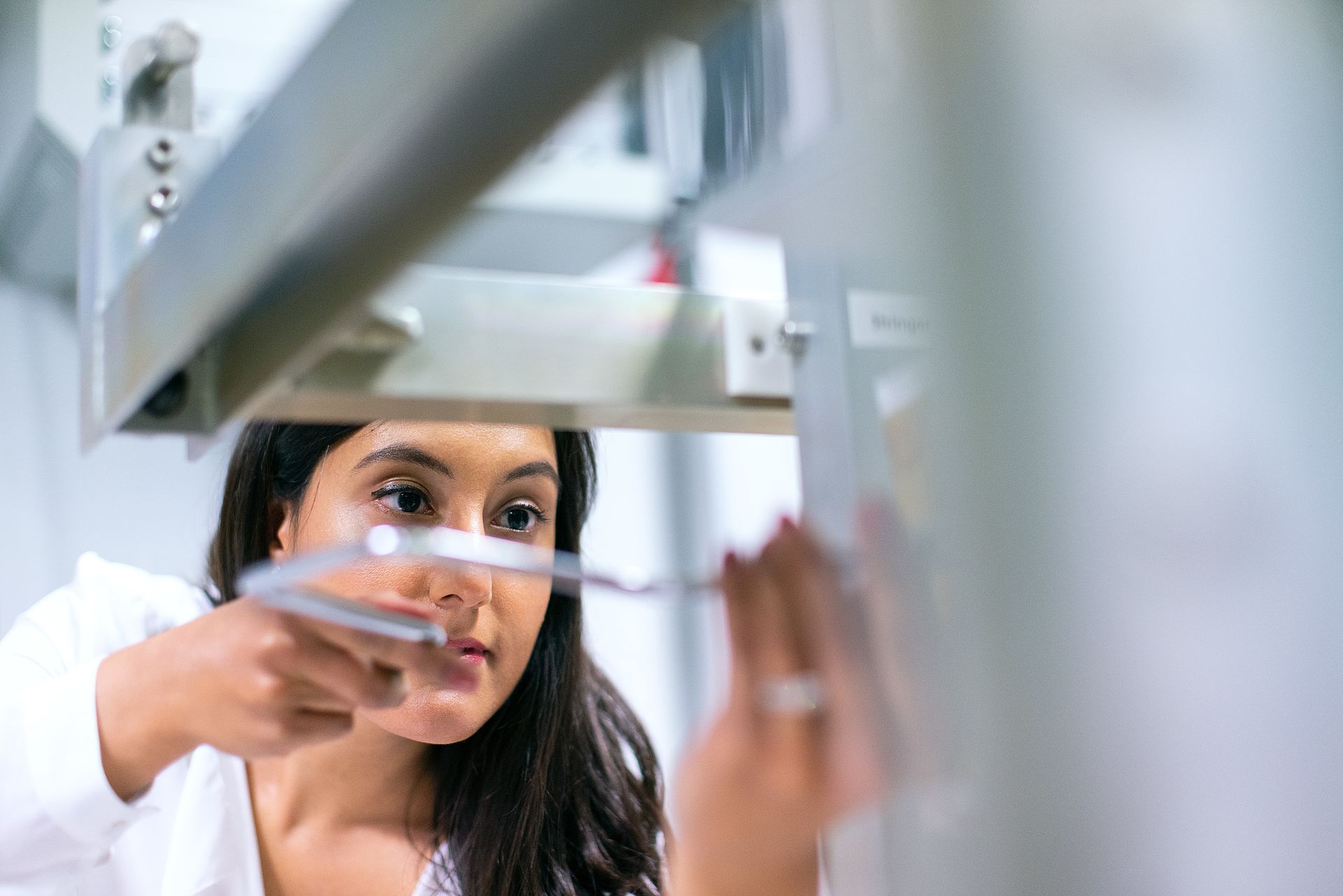
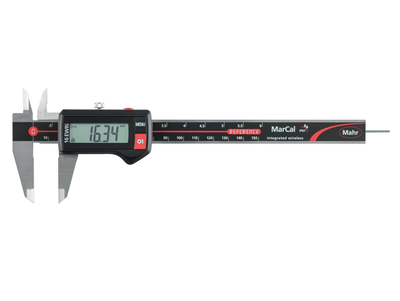
Mahr'dan yenilikçi el tipi ölçüm ekipmanları: Kumpaslar, mikrometre vidaları ve analog indikatörler #96, analogdan dijitale entegre kablosuz aktarımlı modellere. Mahr'ın karşılaştırmalı ölçüm aletleri ve referans standartları vazgeçilmezdir
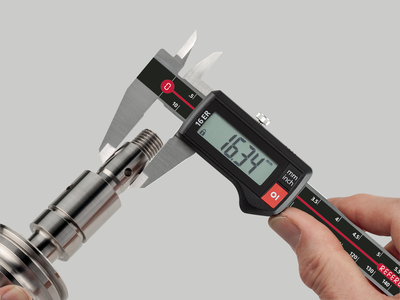
Analogdan dijitale, her çeşit kumpas yelpazesi. Kolay kullanım, kablosuz ve son derece hassas. Üretimde verimli kullanım için mükemmel.
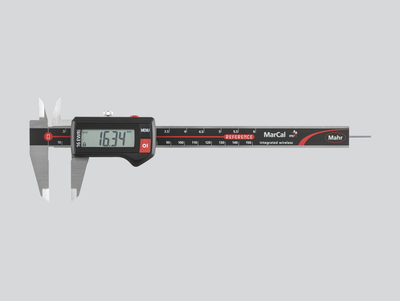
Güvenli, okunması kolay dijital ekran, modern tasarım ve her zamanki Mahr hassasiyeti dijital kumpaslarımızın ayırt edici özelliğidir. Ürün gamında, tüm uygulamalar için ölçüm aletleri bulunur. Veri aktarımı için çeşitli arabirimler ve IP 67'ye kadar koruma derecesi ile karşılanmadık talep kalmaz.
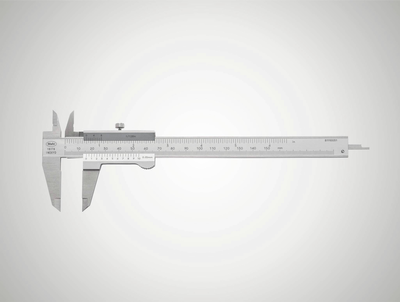
Skalayı korumak ve en yüksek hassasiyeti sağlamak için yansıma önleyici okuma ünitesi, sertleştirilmiş çelik, yükseltilmiş kılavuzlar. Klasik nonius kumpas ile Mahr'dan kaliteli kumpas özellikleri.
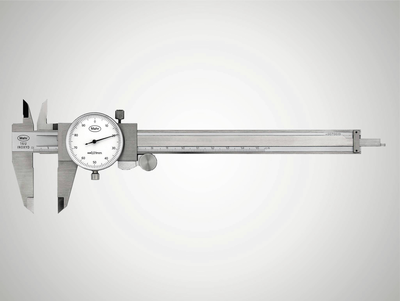
Uzun süreli hassasiyet için büyük, yüksek kontrastlı kadran ve darbeye karşı korumalı ölçüm aleti. Hızlı ve güvenli okuma için denenmiş ve test edilmiş mekanik tasarım.
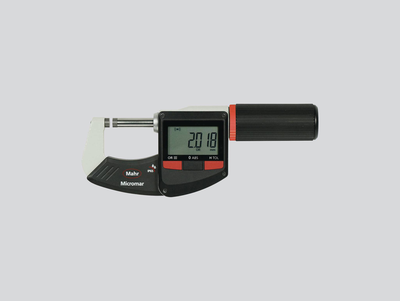
Çeşitli tasarımlarda maksimum hassasiyet. Mahr'ın mikrometre vidaları geleneksel mekanik, dijital ve kablosuz versiyonlarda mevcuttur.
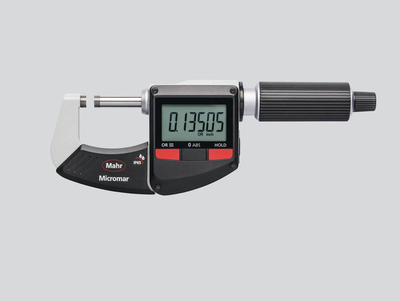
Net dijital ekran, modern tasarım ve her zamanki Mahr hassasiyeti dijital dış mikrometrelerimizin öne çıkan özellikleridir. Ürün gamında, tüm uygulamalar için ölçüm aletleri bulunur. Veri aktarımı için çeşitli arabirimler ve IP 65'e kadar yüksek koruma derecesi ile karşılanmadık talep kalmaz.
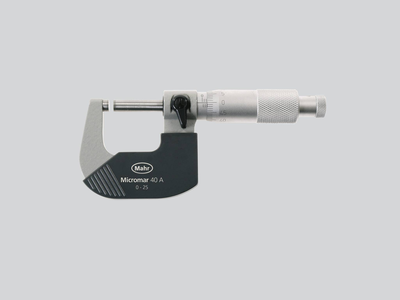
Yansıma önleyici okuma ünitesi, ısı yalıtım plakaları ve maksimum duyarlılık için hassas topraklanmış mil. Mahr'dan kaliteli mikrometre özellikleri.
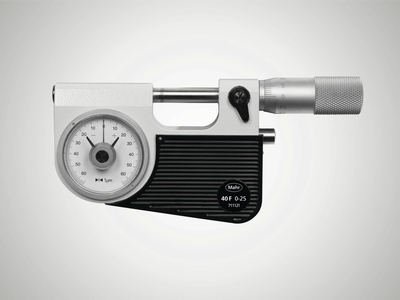
Seri parçaların (mil, cıvata, şaft) güvenilir ve hızlı testi için özellikle uygundur. Boyutsal hassasiyet, analog komparatörde bir bakışta tanınır ve okunur.
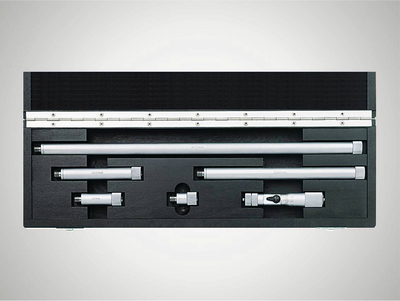
2.500 mm'ye kadar büyük çapları ve test mesafelerini ölçmek için uygundur
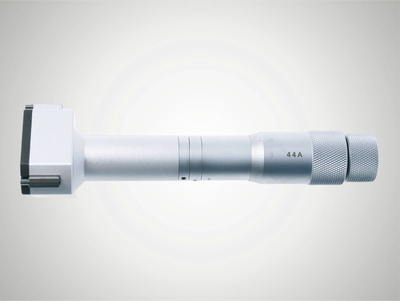
Skalalı veya dijital ekranlı veya tabanca tipi kabzalı hızlı ölçüm aleti olarak mevcuttur. Mahr 3 noktalı iç ölçüm cihazları, otomatik merkezleme sayesinde her zaman güvenilir ölçüm sonuçları sağlar.
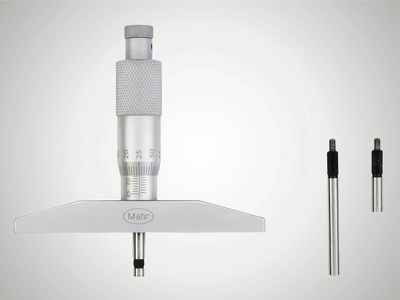
Yansıma önleyici okuma ünitesi ve maksimum duyarlılık için hassas topraklanmış mil. Mahr'dan kaliteli mikrometre özellikleri.
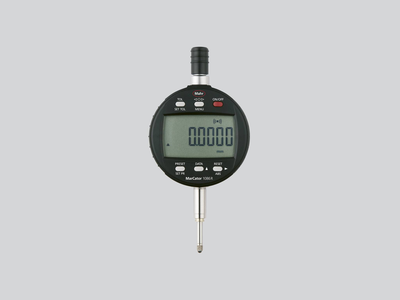
Analogdan dijitale, tüm kadranlı mastar, analog komparatör ve kadran testi indikatörleri yelpazesi. Kolay kullanım, kablosuz (isteğe bağlı), ve son derece hassas. Üretimde verimli kullanım için mükemmel.
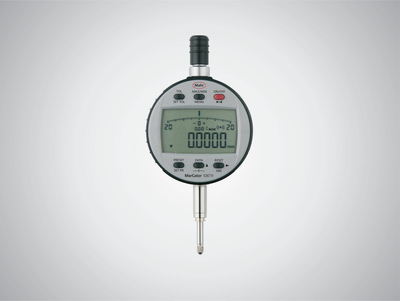
Net dijital ekran, sağlam yapı ve yüksek Mahr hassasiyeti, dijital kadranlı mastarlarımızı niteler. Ürün gamında, tüm uygulamalar için ölçüm aletleri bulunur. Veri aktarımı için çeşitli arabirimler ve IP 54'e kadar koruma derecesi ile karşılanmadık talep kalmaz.
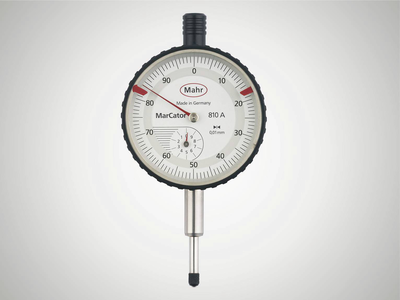
Aşağıdaki özellikler sayesinde yüksek duyarlılık ve hassasiyet: Ölçüm aleti eksenlerinin, hassas dişli çarkların ve pinyonların sağlam montaj bağlantısı, yüksek hassasiyette monte edilmiş ölçüm pimi
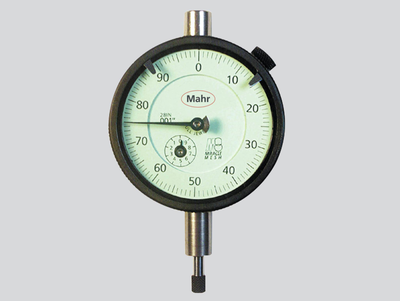
Aşağıdaki özellikler sayesinde yüksek duyarlılık ve hassasiyet: Ölçüm aleti eksenlerinin, hassas dişli çarkların ve pinyonların sağlam montaj bağlantısı, yüksek hassasiyette monte edilmiş ölçüm pimi
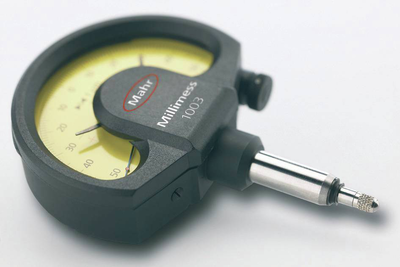
Analog kadranlı indikatörlerle karşılaştırıldığında, Millimess kadran komparatörleri daha da hassas bileşenlere sahiptir, bu da daha iyi ölçüm hassasiyeti ve çok daha iyi bir histerezis hatası sağlar. Bu avantajlar özellikle kaçıklık testlerinde, doğruluk ve düzlük ölçümlerinde ve karşılaştırmalı ölçümlerde belirgindir.
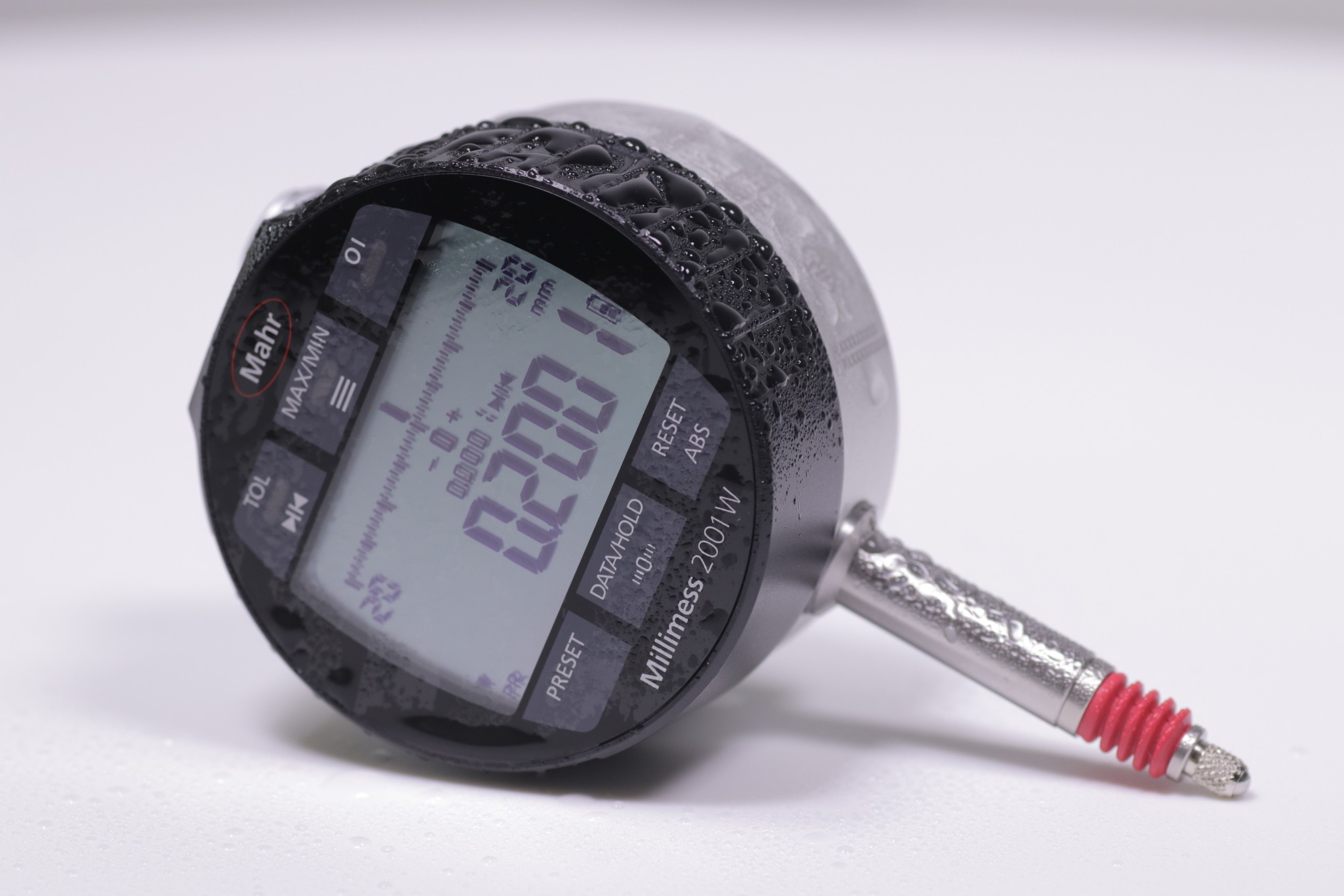
Yüksek hassasiyetli endüktif Millimess analog komparatörler 0,2 μm'ye kadar dijital artışlar yapabilir. Tolerans izleme, dinamik ölçümler için minimum veya maksimum kayıt, birleşik sayısal ve skala ekranı ve kolay veri aktarımı gibi kullanıcı dostu işletim işlevleri, cihazı vazgeçilmez bir hassas ölçüm aleti haline getirir.
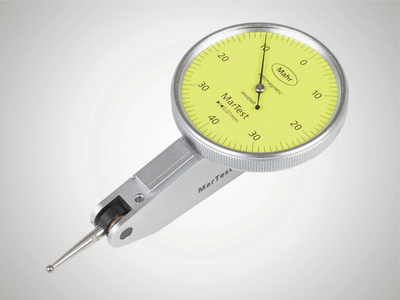
Bilgisayarla optimize edilmiş hassas ölçüm aracı, maksimum güvenilirlik ve hassasiyet sağlar. Zorlu atölye kullanımı için ekran, sertleştirilmiş bir mineral cam panel tarafından çizilmeye veya kırılmaya karşı mükemmel bir şekilde korunur ve ayrıca sızdırmaz, nüfuz eden sıvılara karşı güvenilir koruma sağlar.
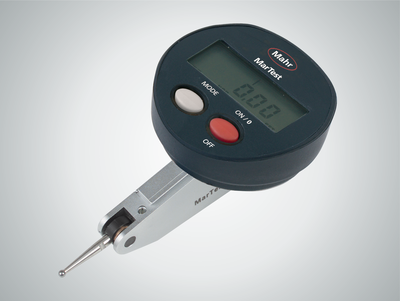
Okunması kolay dijital ekran, sağlam tasarım ve yüksek Mahr hassasiyeti, dijital kadranlı test indikatörlerimizi niteler.
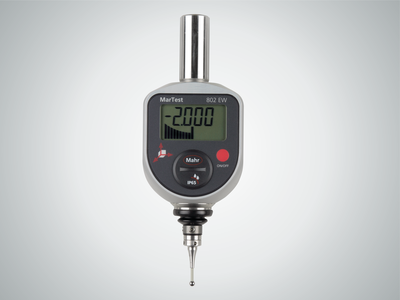
NC tezgahları, işleme merkezleri ve aşındırma tezgahları için Mahr 3D ölçüm probları, kurulum ve arıza sürelerini kısaltır. İş parçaları ve fikstürlerdeki referans kenarlarına hassas şekilde temas etmek için mükemmeldir.
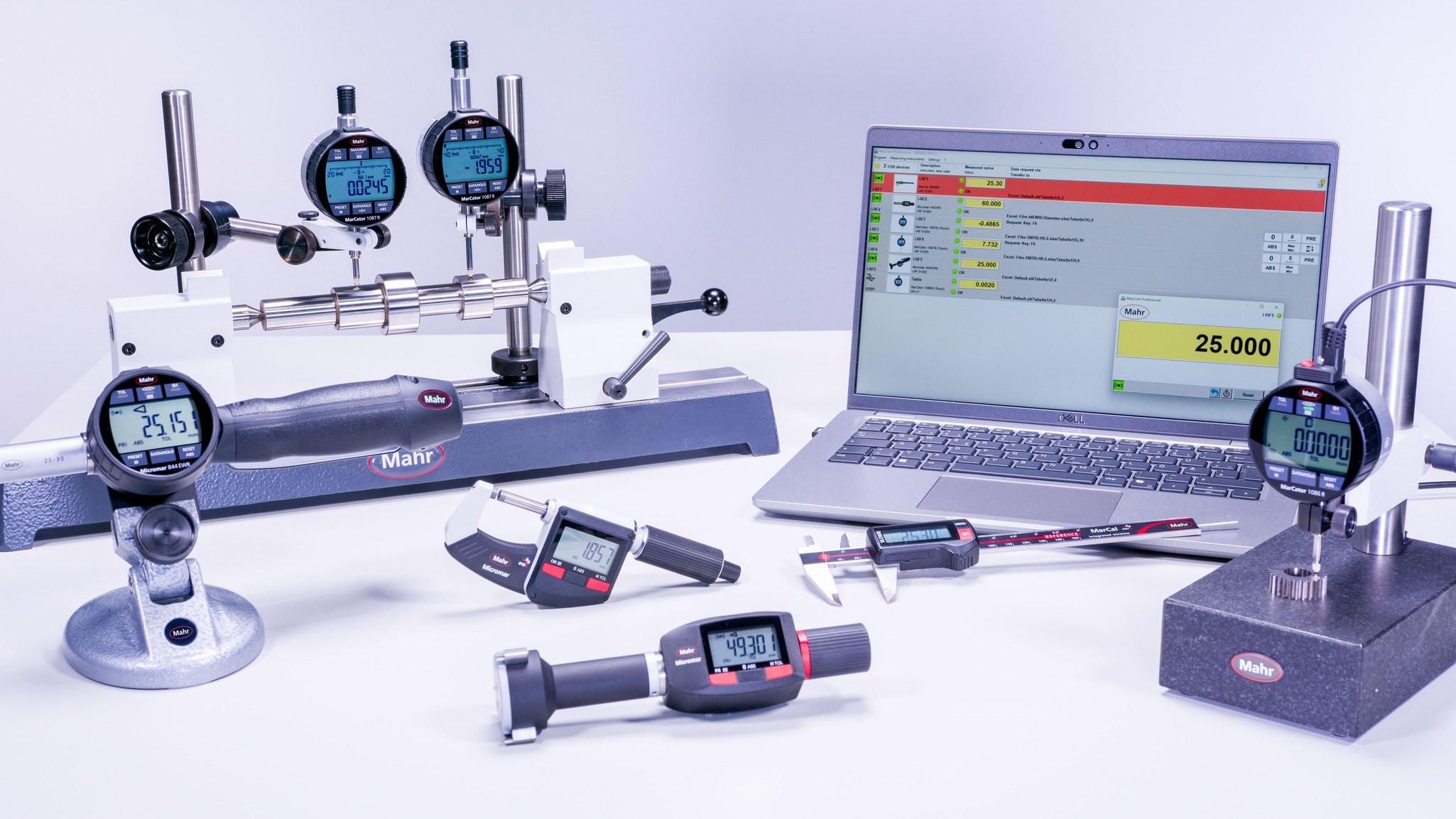
Entegre Kablosuz, harici kablosuz modüller, USB, Opto RS232 veya Digimatic olsun: Kullandığınız arabirim standardından bağımsız olarak MarConnect, her zaman en iyi bağlantıyı sağlar.
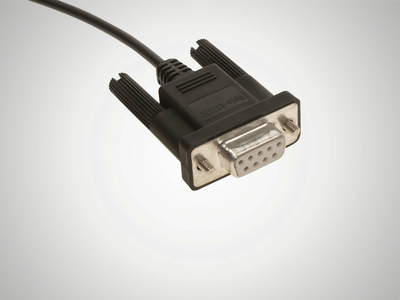
Birçok Mahr hassas mastarı, MarConnect arabirimi ile bir veri çıkışına sahiptir. USB, Opto RS232 veya Digimatic; kullandığınız arabirim standardından bağımsız olarak MarConnect, her zaman en iyi bağlantıyı sağlar.
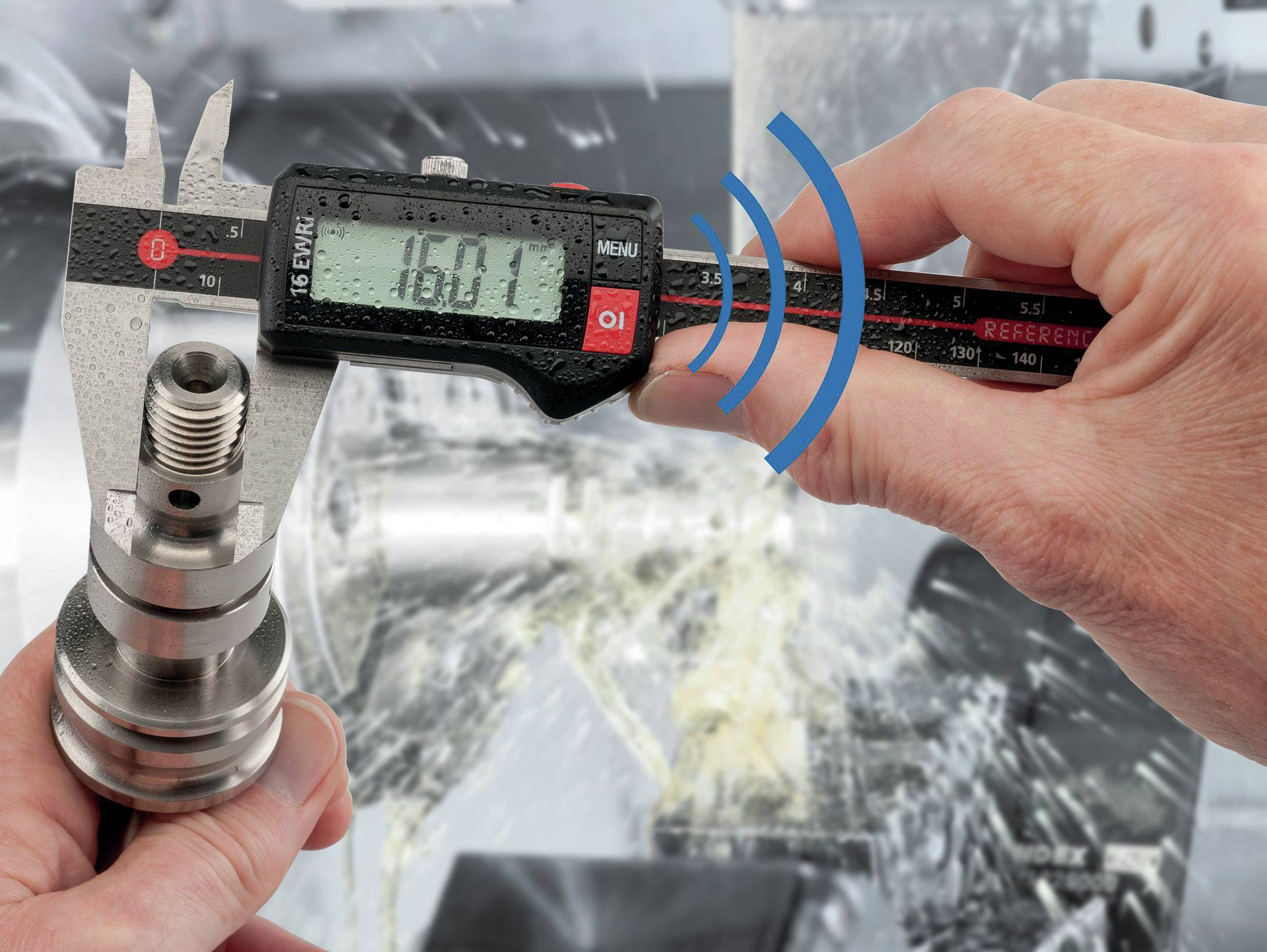
Mahr'ın Kablosuz serisi, tam mobilite ile hassas ölçüm sonuçları sağlar. Kablolu teknolojinin kısıtlamaları olmadan ölçmenin modern ve kolay yolu.
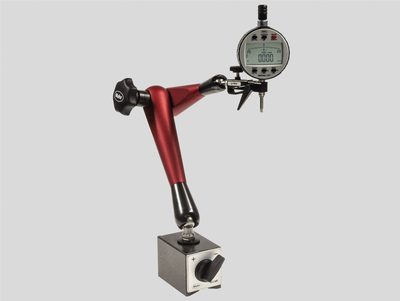
MarStand ölçüm tripodları, ölçüm tablaları ve radyal salgı mastarları, hassas ölçüm sonuçlarının dayanağı olan yüksek stabilite sunar. Analog indikatörleriniz, analog komparatörleriniz, analog test indikatörünüz, ölçüm cihazlarınız ve ölçüm problarınız için gerekli desteği sunarlar.
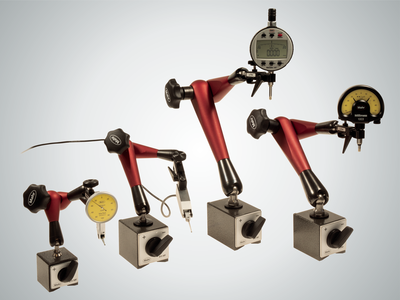
Ölçüm tripodları, kararlı tasarımları sayesinde hassas ölçüm sonuçları için dayanak sağlar. Analog indikatörleriniz, analog komparatörleriniz, analog test indikatörünüz, ölçüm cihazlarınız ve ölçüm problarınız için gerekli desteği sunarlar.
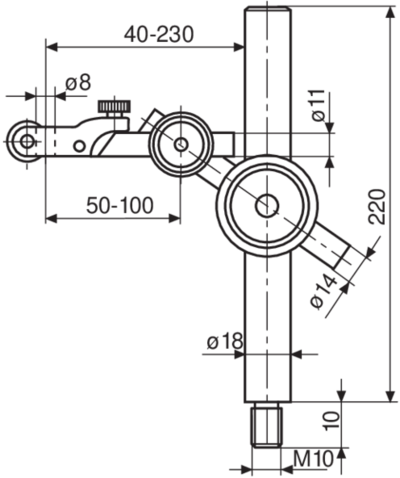
MarStand direk ve destek tertibatları, bağımsız çözümler için kullanılır ve hassas ölçüm sonuçları için gerekli olan yüksek stabilite sunar. Analog indikatör, analog komparatör, analog test indikatörü ölçüm cihazları ve ölçüm probları için gerekli desteği sunarlar.
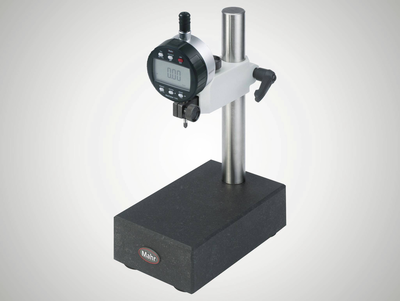
Ölçüm tablaları, hassas ve seviyeli bir ölçüm tablasını, sabit bir ölçüm sütununu ve güçlü kol parçalarını birleştirir. MarStand ölçüm tablaları, ekstra kararlı tasarımları sayesinde hassas ölçüm sonuçları için dayanak sağlar.
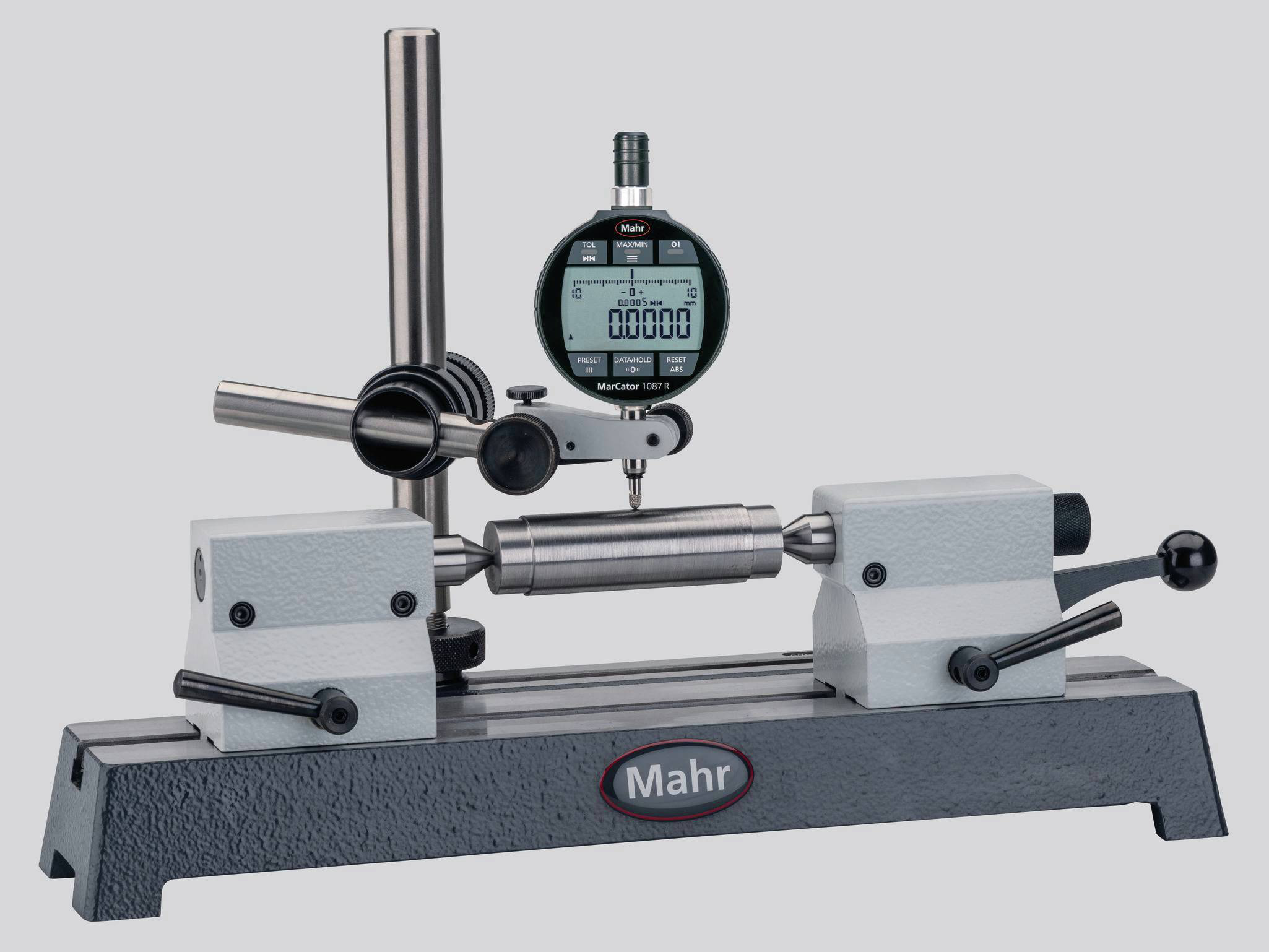
Radyal salgı mastarları, üretime yakın bir ortamda millerdeki konum ve biçim hatalarını tespit etmenin en basit yöntemidir. Model çeşitliliği nedeniyle, sağlam MarStand radyal salgı mastarları, çok çeşitli iş parçası gereksinimleri ve hassas ölçüm sonuçları için temel oluşturur.
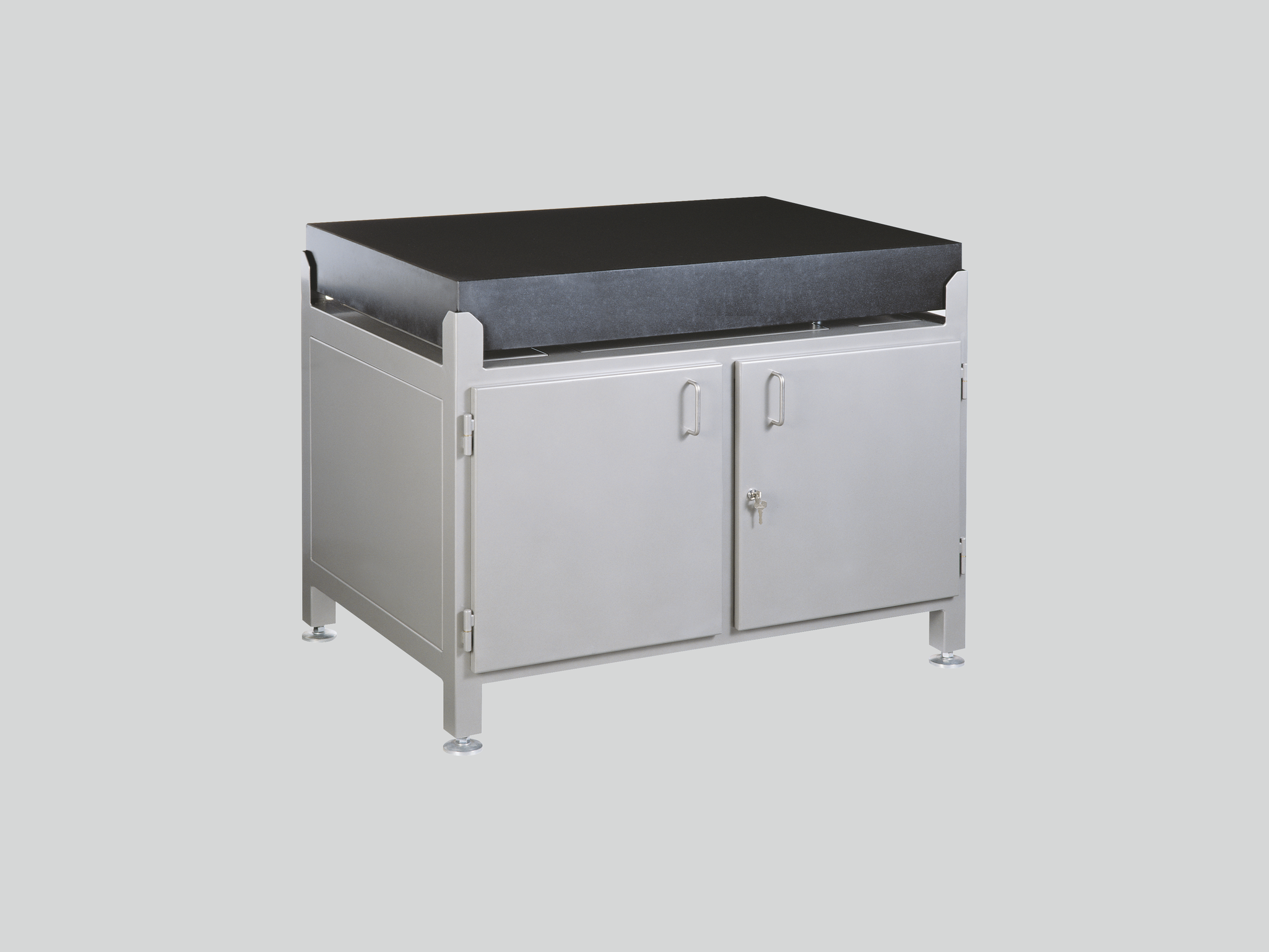
Sert granitten yapılmış test plakaları, plakaların yüksek mukavemeti ve boyutsal kararlılığı nedeniyle yükseklik ölçüm aletleriniz için mükemmel bir yüzeydir.
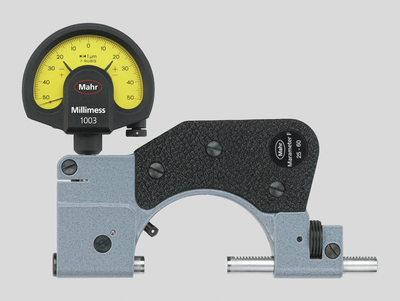
Gösterge mastarlarının karşılaştırmalı mastarlar olarak kullanılması, üretimde hassas ölçümler için mükemmel bir araçtır. Mastarı bir referans standardına ayarlamak sapma marjını azaltır ve sıcaklık dalgalanmalarının ölçüm sonucu üzerindeki etkisini en aza indirir.
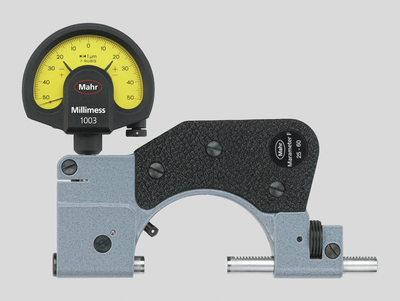
Hassas ibre tutma mastarları, özellikle seri parçalar üzerinde güvenli ve hızlı testler için mil, cıvata ve şaft gibi silindirik parçaların hassas ölçümleri için mükemmel ölçüm araçlarıdır. Boyutsal hassasiyet, komparatörde bir bakışta tanımlanır ve okunur.
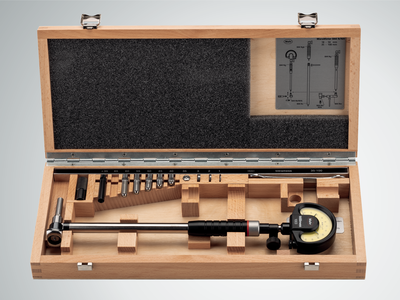
İç ölçüm cihazları, deliklerin çap, yuvarlaklık ve konikliğinin hassas bir şekilde ölçümü için mükemmel araçlardır.
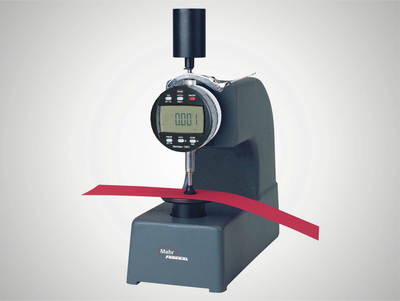
Kalınlık ölçerlerimiz, çeşitli film, sac ve levhaların özellikle hızlı ölçümü için sağlam ve basit bir aralık sunar.
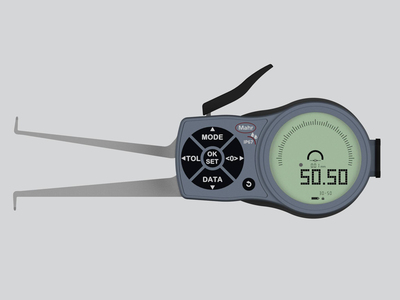
İş parçası geometrisi nedeniyle kumpas veya iç mikrometre vidaları gibi yaygın ölçüm aletleri kullanılamıyorsa kumpas mastarları mükemmel çözümdür!
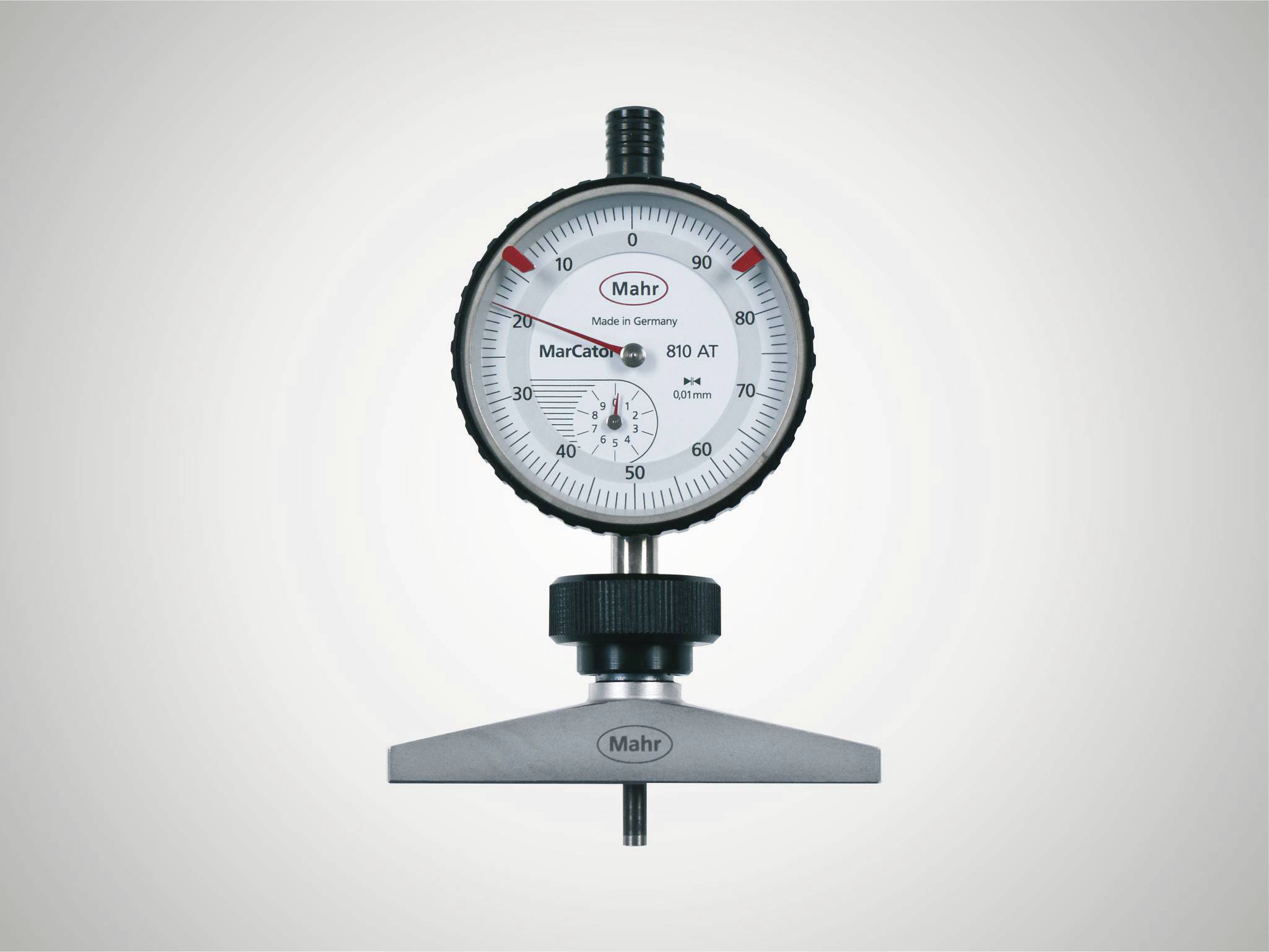
Derinlik mastarlarımız, özellikle hızlı derinlik ölçümleri için sağlam ve basit bir aralık sunar. 8 mm'lik montaj mili, ölçüm görevine göre analog indikatör, komparatör ve probların kullanımına uygundur.
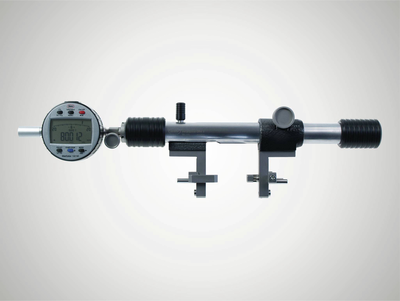
Çok amaçlı ölçüm aletleri, üretimde hassas ölçümler için mükemmel ortaklardır, çünkü bir referans standartla karşılaştırmalı ölçüm, sıcaklık dalgalanmalarının ölçüm sonucu üzerindeki etkisini en aza indirir.
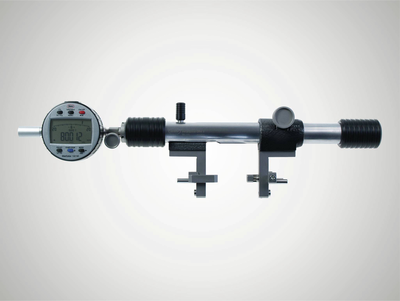
Dişli, diş, konik veya girinti fark etmez. Multimar çok amaçlı ölçüm aletleri, standart ölçüm aletlerinin uygun olmadığı hemen hemen tüm iç ve dış ölçümler için ideal bir çözümdür. Temel ünite seçenekleri ve geniş bir aksesuar yelpazesi mevcuttur.
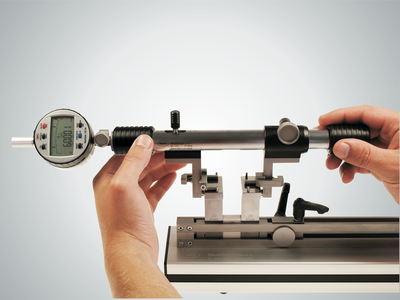
İç ve dış çap ölçüm aletlerinizi doğru şekilde ayarlayın. 844 S ayar aletlerini kullanırken daha büyük boyutlar için bile her ölçüm görevi amacıyla mükemmel bir donanıma sahipsiniz.
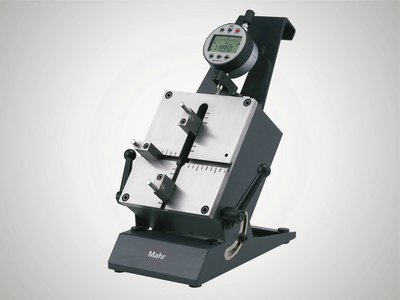
Merkezleme omuzları, dar bilezikler, veya girintiler fark etmez: Multimar 36B çok amaçlı ölçüm aletleri, neredeyse tüm iç ve dış ölçümler için ideal bir çözümdür. Temel ünite seçenekleri ve geniş bir aksesuar yelpazesi mevcuttur.
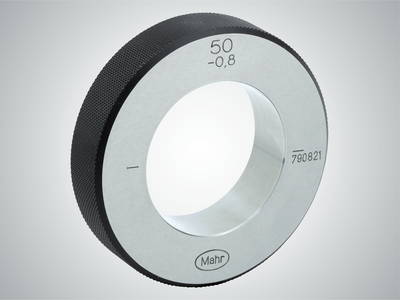
Mahr'ın ayar standartlarına ve mastarlarına güvenin - çünkü bunlar hassas ölçüm sonuçlarının dayanağıdır.
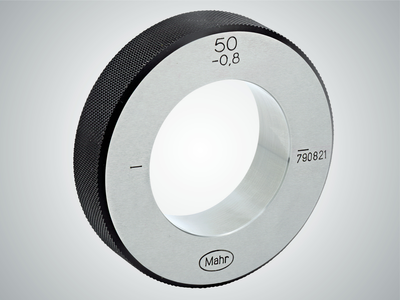
Mahr'ın ayar standartlarına güvenin, çünkü bunlar hassas ölçüm sonuçlarında referans olarak kullanılır
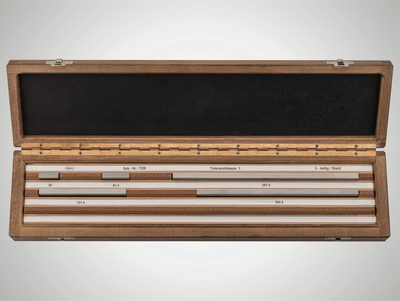
Mahr mastar blokları, yüksek kaliteli referans ve çalışma standartlarına sahip olmanızı sağlar. Atölyenizin, üretiminizin veya kalite güvencenizin gereksinimlerine uygun dört tolerans sınıfı ve iki malzeme arasından seçim yapın.
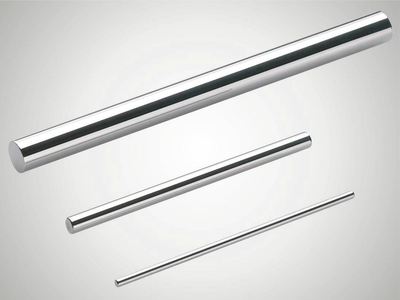
Mahr pim mastarları üç tolerans sınıfında ve çeşitli tasarımlarda mevcuttur. Atölyenizin, üretiminizin veya kalite güvencenizin gereksinimlerine uygun cihazı seçin.
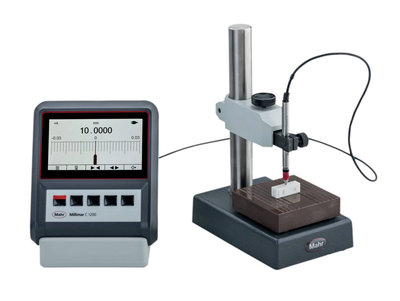
Elektriksel uzunluk ölçüm aletlerinin gereksinimleri, uygulamaları kadar çeşitlidir. Mükemmel güvenilirlik, hassasiyet ve kolay kullanım aranır.
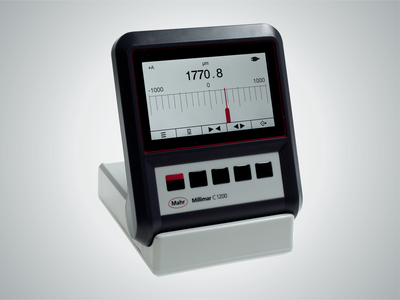
Elektriksel uzunluk ölçüm aletlerinin gereksinimleri, uygulamaları kadar çeşitlidir. Mükemmel güvenilirlik, hassasiyet ve kolay kullanım aranır. Millimar kompakt ve sütun ölçüm aletleri, bu gereksinimleri karşılamaktadır.
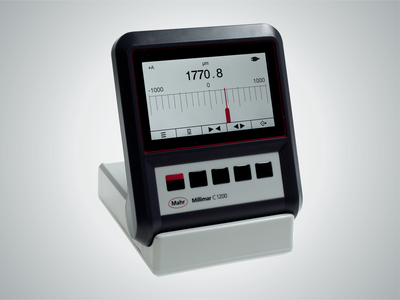
Millimar uzunluk ölçüm aletleri kompakt, sağlam ve kullanımı kolaydır. Üretim alanında ve ölçüm odasında yönetilebilir karmaşıklıktaki görevleri ölçmek için çok yönlü değerlendirme ve görüntüleme aletleridir.
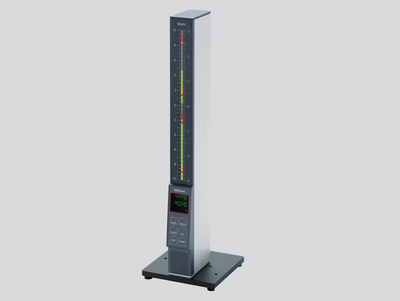
Ölçüm sonuçları 101 adet üç renkli LED üzerinde görüntülenir ve uzaktan kolayca okunabilir. Programlanabilir uyarı ve tolerans sınırları aşıldığında, segmentlerin rengi yeşilden sarıya veya kırmızıya değişir.
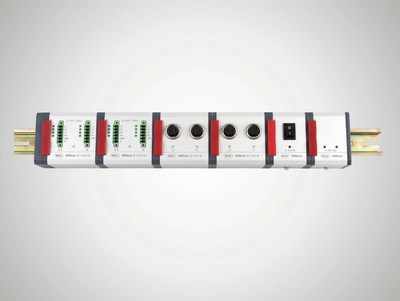
Modüllerin ve yazılımın farklı kombinasyon seçenekleri, çalışma ortamını ve araçları her zamankinden daha farklı olarak tasarlama fırsatı sunar.
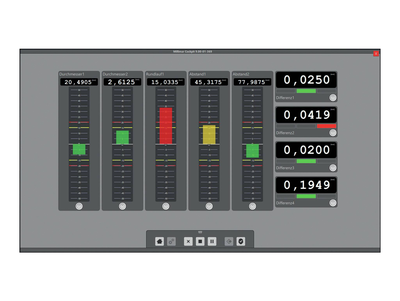
Smart and universally applicable software for complex measurement tasks in the manufacturing sector
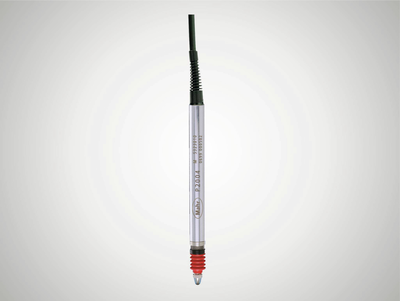
Millimar dönüştürücüler, bir ölçüm zincirinin en önemli bileşenleridir. Özellikleri, tüm ölçümün kalitesini belirler. Uygulamaya bağlı olarak bu amaç için çeşitli teknolojiler mevcuttur. Örneğin Millimar endüktif ölçüm probları: Bu ürünler dayanıklı, çok yönlü ve cazip fiyatlıdır.
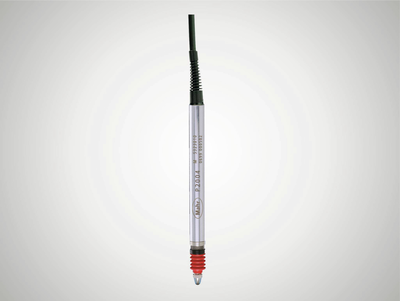
Kalınlık ölçümü, radyal kaçıklık veya eş merkezlilik fark etmez: Endüktif problarla, şekil, destek veya radyal kaçıklık sapmalarından bağımsız olarak ölçülen değerleri ve sapmaları kaydedebilirsiniz. Büyük avantajları, geniş doğrusallık aralığı ve parazite karşı göreceli duyarsızlıktır. Problar esas olarak üretimde karşılaştırmalı ölçümler için kullanılır, ancak sensörün belirli görevleri değişebilir.
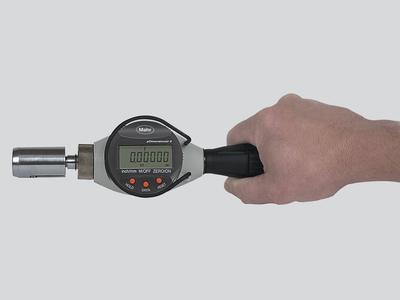
Pnömatik uzunluk ölçüm aletleri, yüksek hassaslıkları ve uzun vadeli kararlılıkları ile bilinir. Ölçüm nozulları ile temassız ölçüm, iş parçalarına zarar vermez. Temizlenmemiş, üzerinde madde bulunan, yağlanmış veya kaplanmış iş parçaları bile
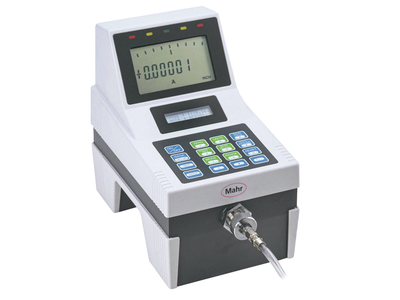
Millimar uzunluk ölçüm aletleri kompakt, sağlam ve kullanımı kolaydır. Üretim alanında yönetilebilir karmaşıklıktaki görevleri ölçmek için çok yönlü görüntüleme ve değerlendirme cihazlarıdır.
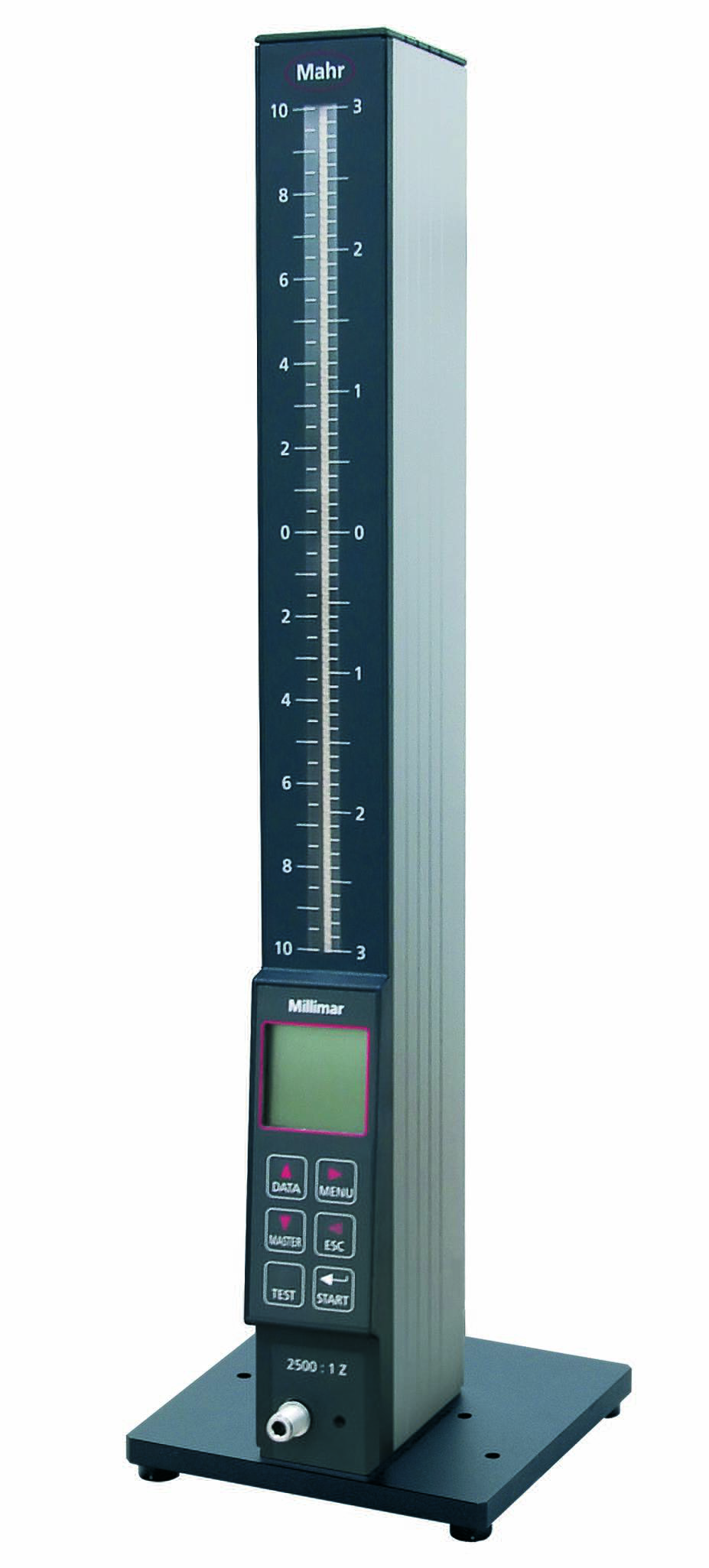
Ölçüm sonuçları 101 adet üç renkli LED üzerinde görüntülenir ve uzaktan kolayca okunabilir. Programlanabilir uyarı ve tolerans sınırları aşıldığında, segmentlerin renkleri yeşilden sarıya veya kırmızıya değişir.
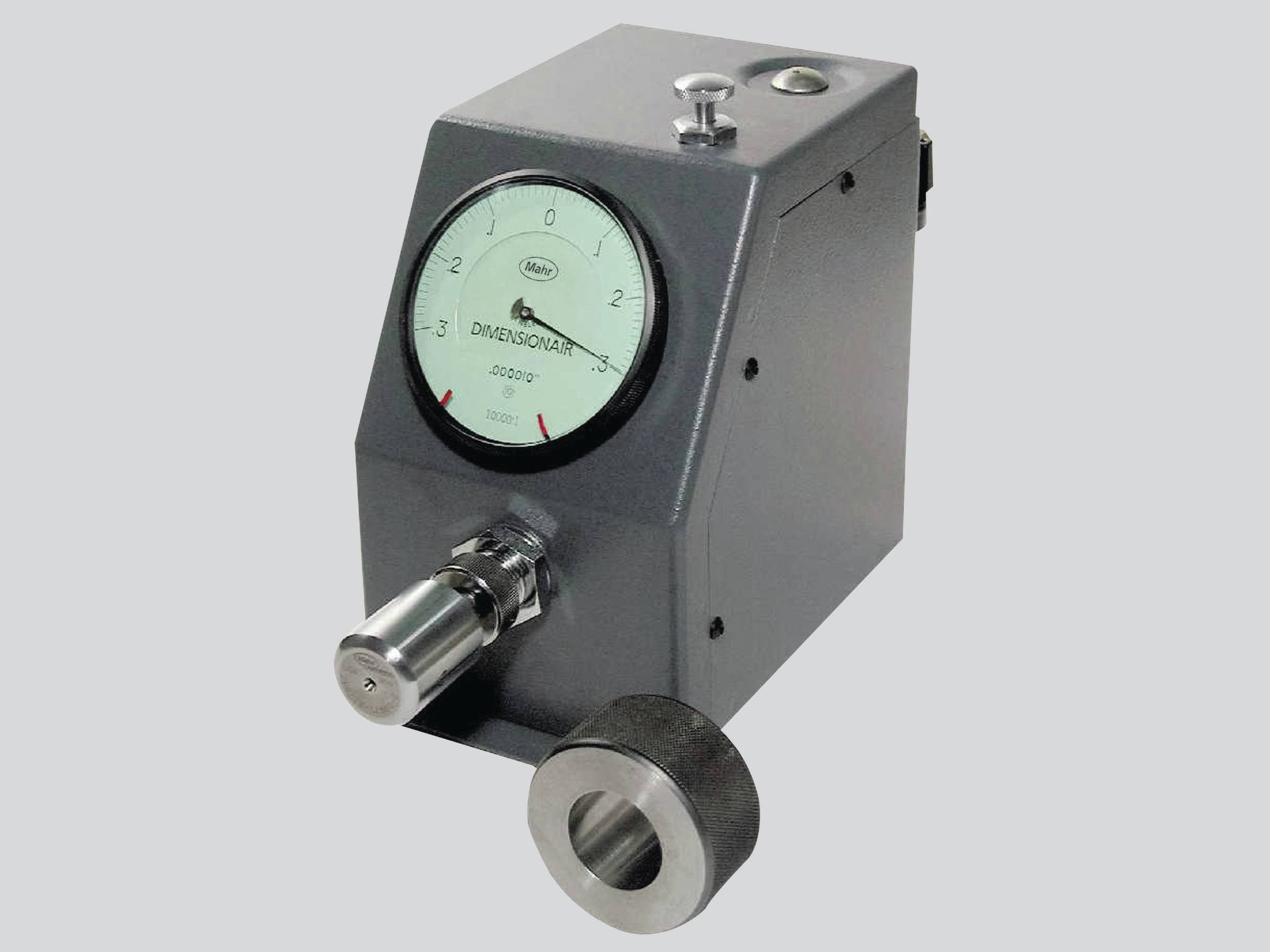
Millimar pnömatik ölçüm cihazları, boyutsal sapmaları hızlı ve doğru bir şekilde kaydeder. Endüstriyel üretim ve ölçüm odaları konusunda uzun yıllardır kendini kanıtlamıştır.
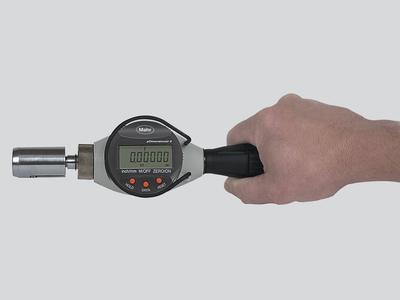
Hareket halindeyken ölçüm ve değerlendirme için.
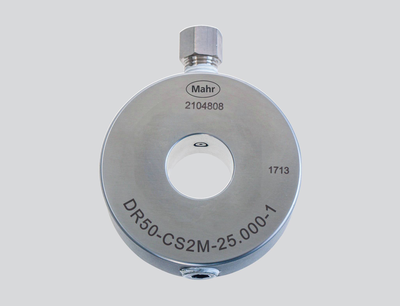
Pnömatik ölçüm halkaları kullanarak temassız ölçüm, iş parçalarına zarar vermez.
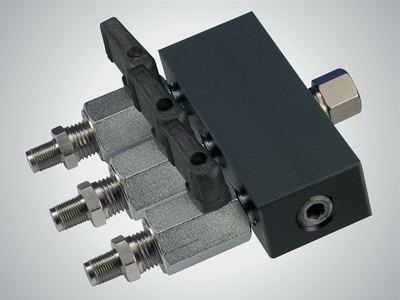
Hava ölçüm teknolojisi için aksesuarlarla ölçüm istasyonunu ölçümünüze uyarlayın.
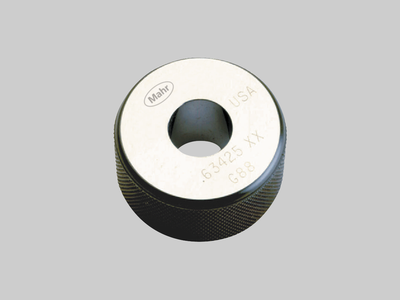
Mahr'ın ayar standartlarına güvenin, çünkü bunlar hassas ölçüm sonuçlarında referans olarak kullanılır
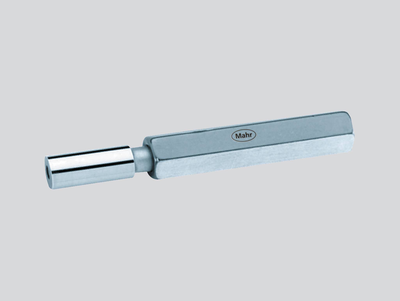
Pnömatik ölçüm aletleri ayarı (nozul halka mastarlar) Titizlikle sertleştirilmiş, eskitilmiş, tornalanmış ve bindirilmiş.
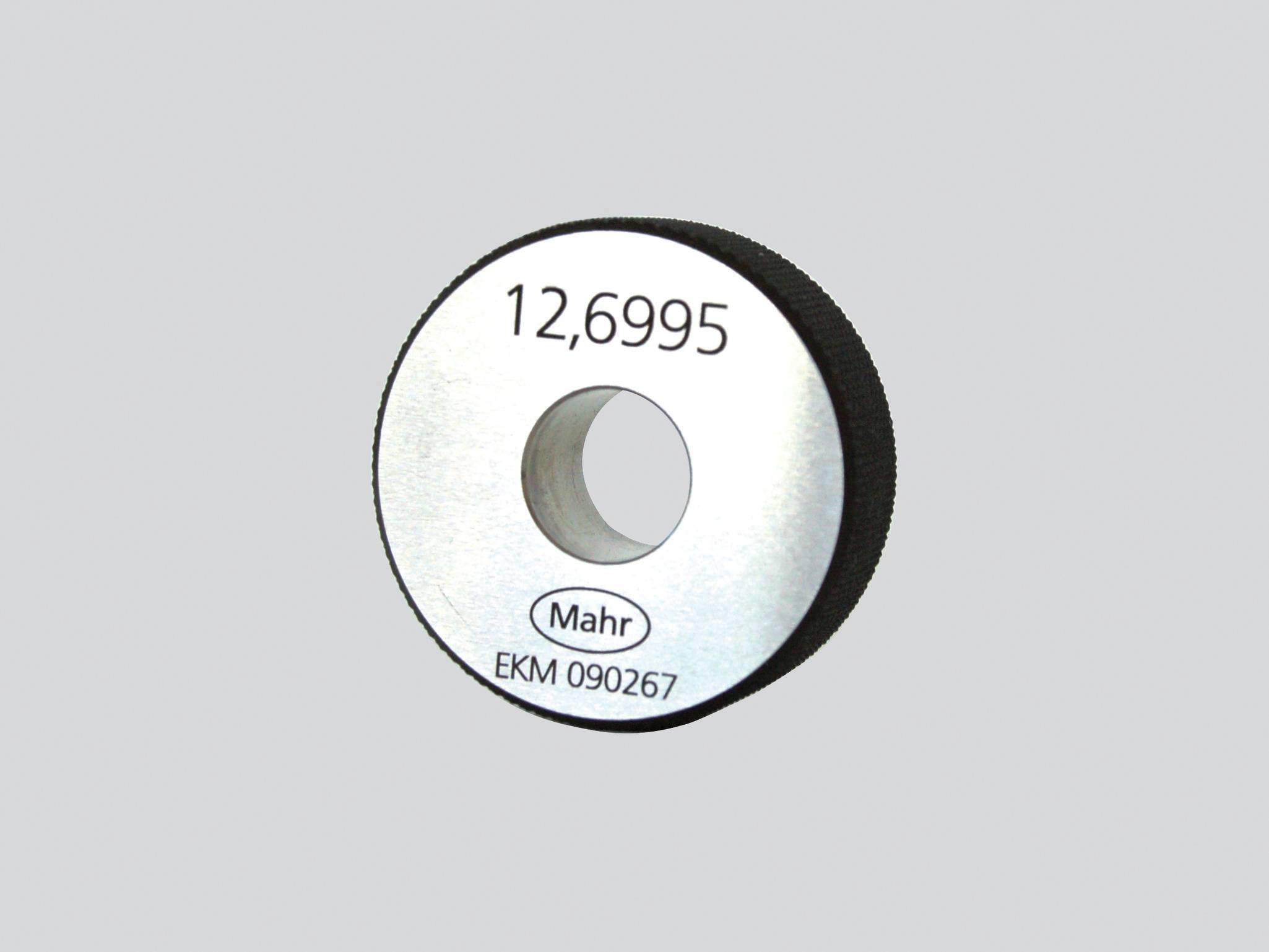
Pnömatik ölçüm aletleri ayarı (nozul delik mastarları) Titizlikle sertleştirilmiş, eskitilmiş, tornalanmış ve bindirilmiş.
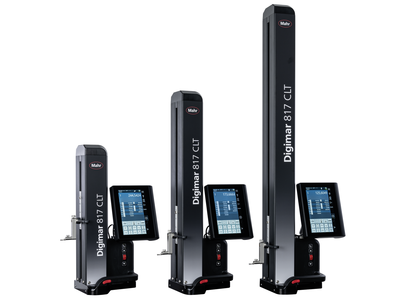
Ölçümlerinizle yüksekleri hedeflemek ister misiniz? Digimar tam size göre!
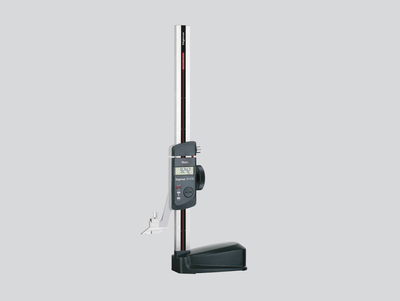
Atölyede iş parçalarını çizmek ve işaretlemek için. Yükseklik ve mesafelerin kolay ölçümü.
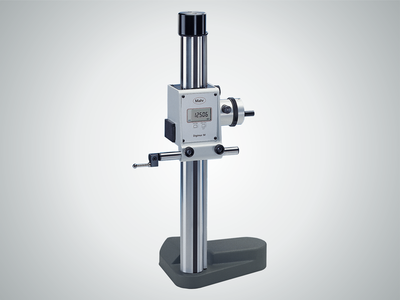
Delik, yüzey ve kenar arasındaki yükseklik ve mesafelerin kolay ölçümü. Ek aksesuarlarla iş parçalarının çizimi ve işaretlenmesi için uygundur.
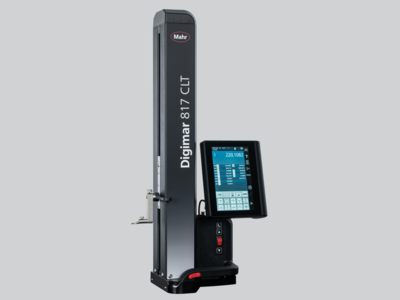
Touch operation, ergonomic handling and a wide range of evaluation options: This is what the Digimar 817 CLT height measuring device stands for.
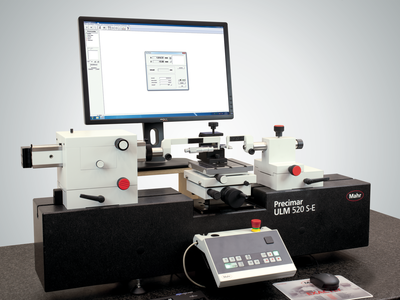
Hassas uzunluk metrolojisi, hem mutlak hem de bağıl ölçümler için yüksek hassasiyetli boyut metrolojisi anlamına gelir.
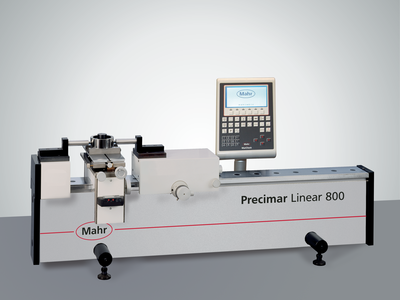
Atölye için çok amaçlı, kullanımı kolay uzunluk ölçüm ve ayar cihazları

Atölye için çok amaçlı, kullanımı kolay uzunluk ölçüm ve ayar cihazları
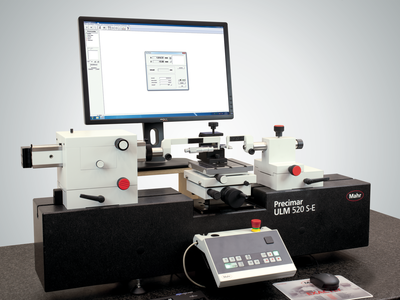
Basit mastar blok test standı, tam otomatik komparatör test standı ve ULM cihazlarından ultra hassas ve kısmen otomatikleştirilmiş CiM çok amaçlı ölçüm makinesine kadar geniş ürün yelpazesi sayesinde Mahr, üretim, ölçüm odaları ve kalibrasyon laboratuvarları için her zaman pratik çözüm sunar. Diğer bir ifadeyle: Maksimum hassaslık ve son derece verimli ölçüm süreçleri bir arada.
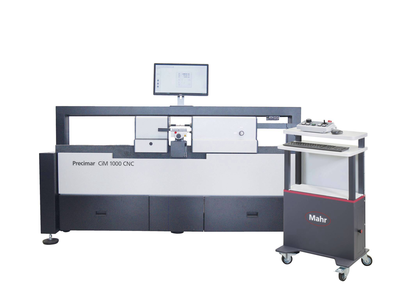
İster klasik ULM ister motorlu PLM ve CiM aletleri. Mahr çok amaçlı uzunluk ölçüm makineleri, minimum belirsizlikle kullanıcı dostu, hızlı ve güvenilir ölçüm sağlar.
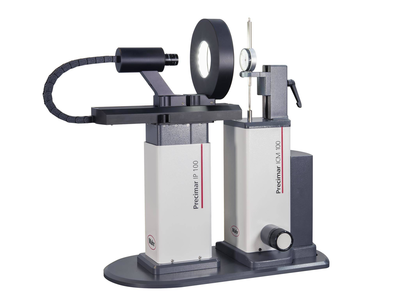
Analog indikatörlerin, analog test indikatörlerin ölçüm cihazlarının, analog komparatörlerin ve probların yarı otomatik ve tam otomatik testi verimli ve hassas bir şekilde yapılır.
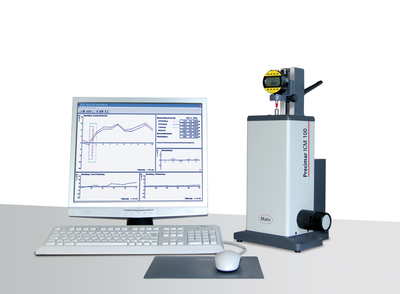
Analog indikatörlerin, analog test indikatörlerin ölçüm cihazlarının, analog komparatörlerin ve probların yarı otomatik ve tam otomatik testi verimli ve hassas bir şekilde yapılır.
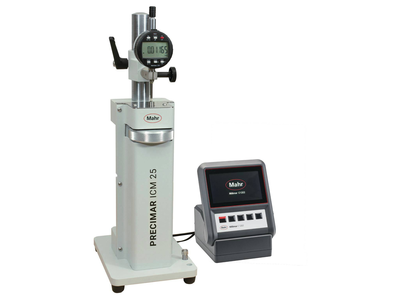
Manual testing of dial gages, dial test indicators and comparators - easy and precise
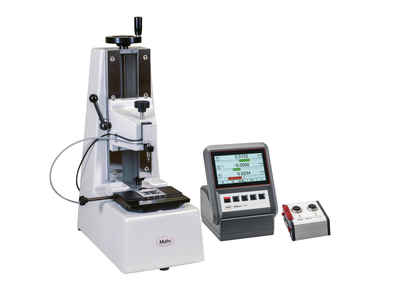
Mahr mastar blok karşılaştırıcılarına güvenin, çünkü bunlar, standartlarınızın hassas şekilde test edilmesinin dayanağıdır
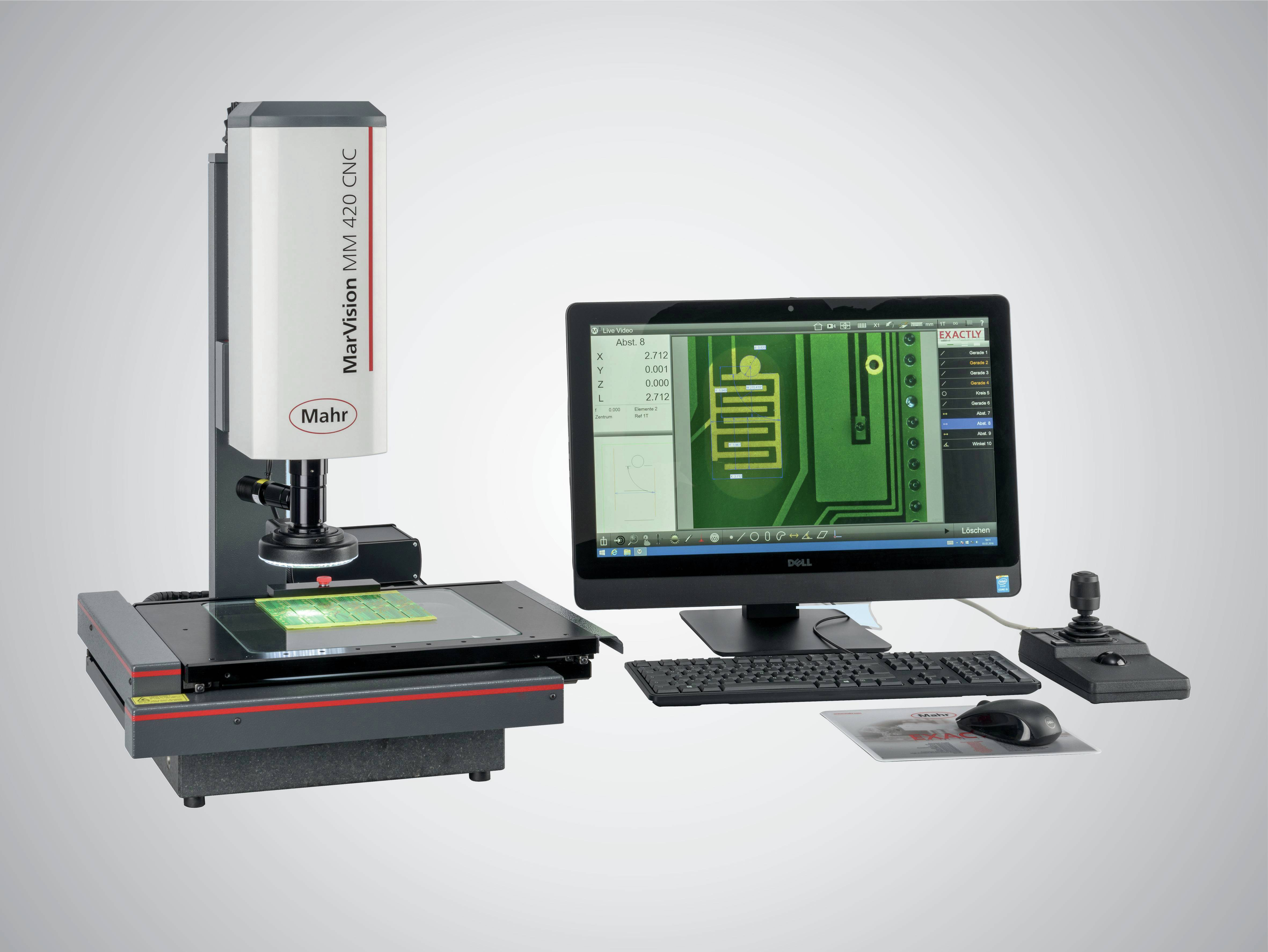
Mikroskoplar, hemen hemen tüm sektörlerde mesafe, yarıçap ve açıların hızlı bir şekilde incelenmesi için kullanılır. Laboratuvarda veya üretim alanına yakın metroloji.
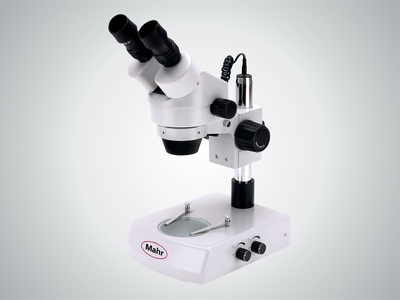
Parlak, keskin üç boyutlu görüntüler için yüksek kaliteli lensli stereo zoom mikroskoplar. Dijital kameraların ek kullanımı ile dürbün veya üç mercekli dürbün.
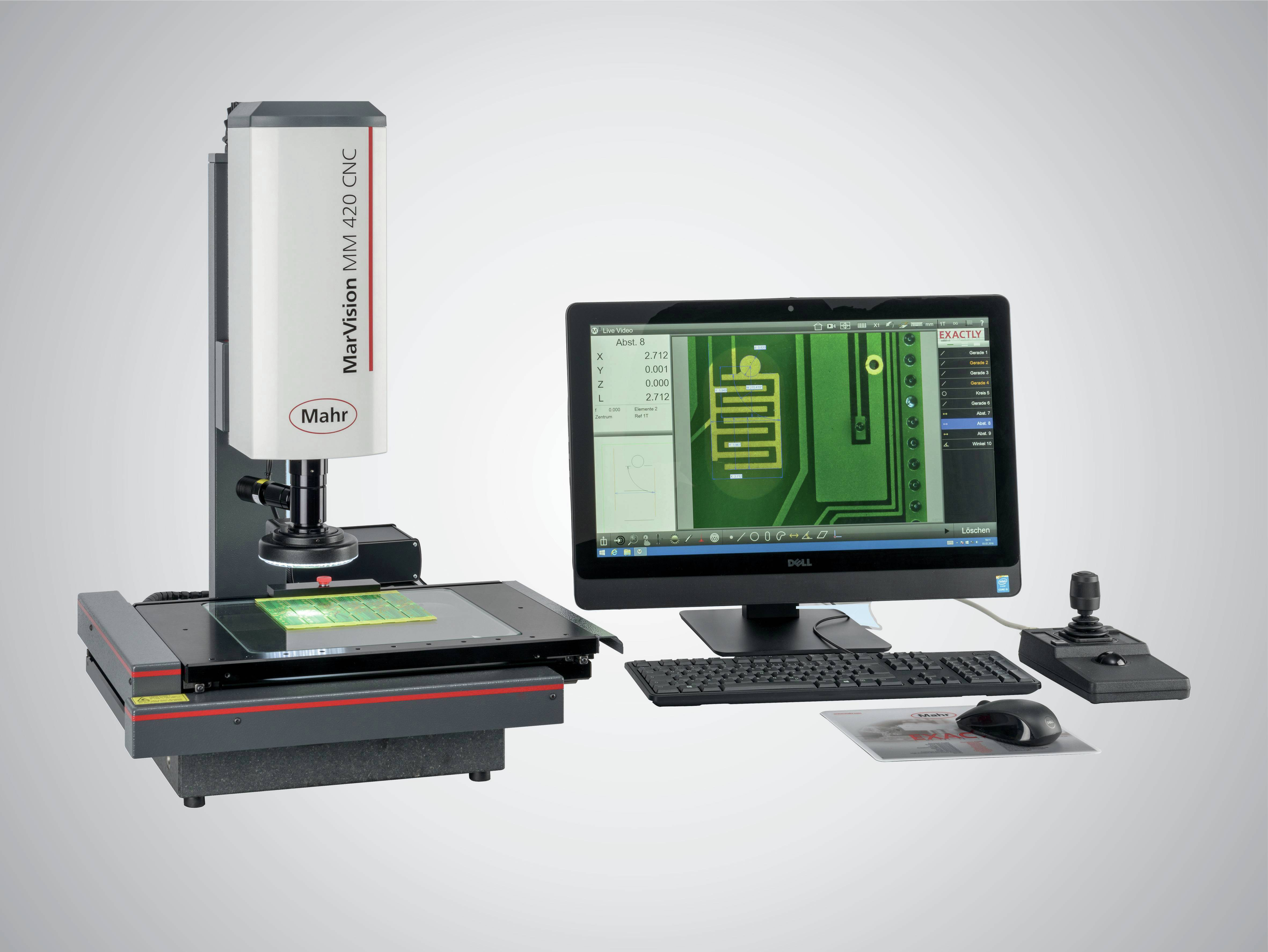
Mikroskoplar, hemen hemen tüm sektörlerde mesafe, yarıçap ve açıların hızlı bir şekilde incelenmesi için kullanılır. Laboratuvarda veya üretim alanına yakın metroloji.
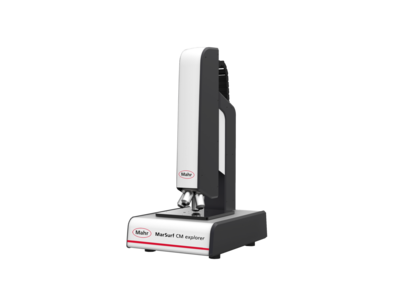
Endüstri ve araştırma için yüzey metrolojisi
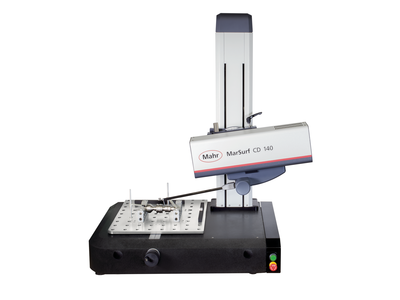
Sıkı toleranslara sahip yapılandırılmış işlevsel yüzeylerde, bir iş parçasının veya nesnenin topografisini kısa bir alanda minimum sürede kaydeden yüksek hassasiyetli ölçüm sistemleri gerekir.
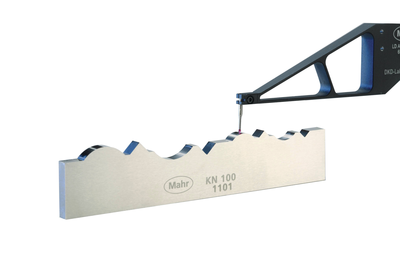
Kaba şekil sapmalarını belirlemek için kontur ölçüm teknolojisi kullanılır.
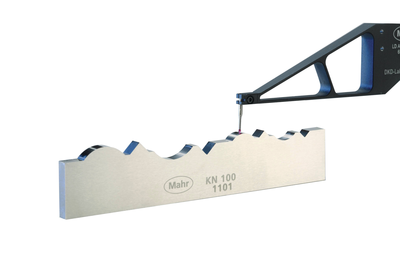
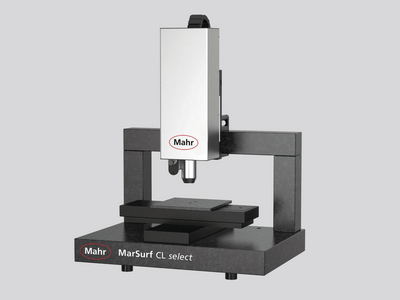
Optik ölçüm aletleriyle konturları hassas bir şekilde ölçün
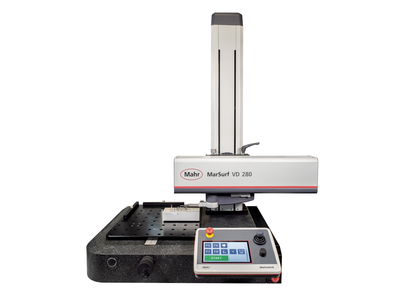
Kontur ve pürüzlülük ölçümü bir arada: Profesyonel çok yönlü
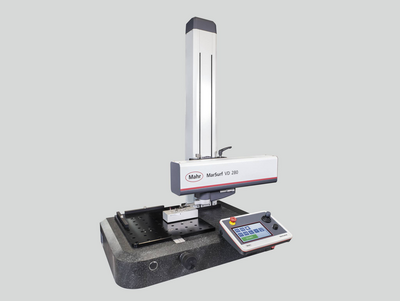
Kontur ve pürüzlülük ölçümü bir arada: Profesyonel çok yönlü
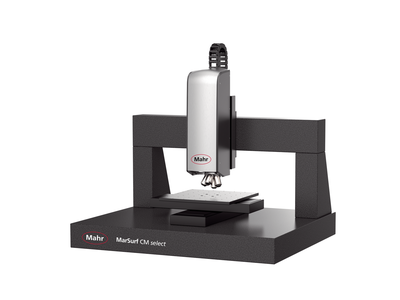
2D/3D Kontur ölçümü ve ayrıca ISO 25178 / ISO 4287'ye göre pürüzlülük ölçüm aksesuarları
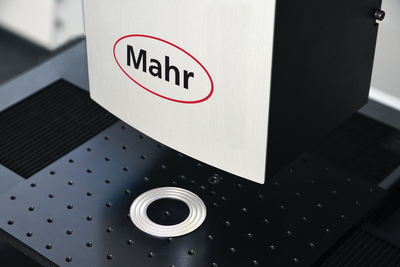
Endüstri ve araştırma için 3D yüzey metrolojisi
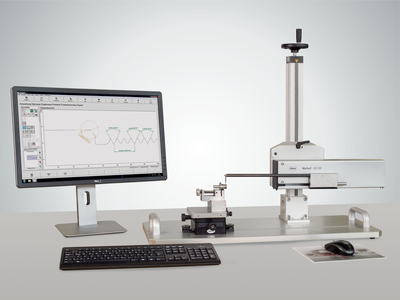
Mobil ölçüm cihazları ile her yerde ölçüm yapın!
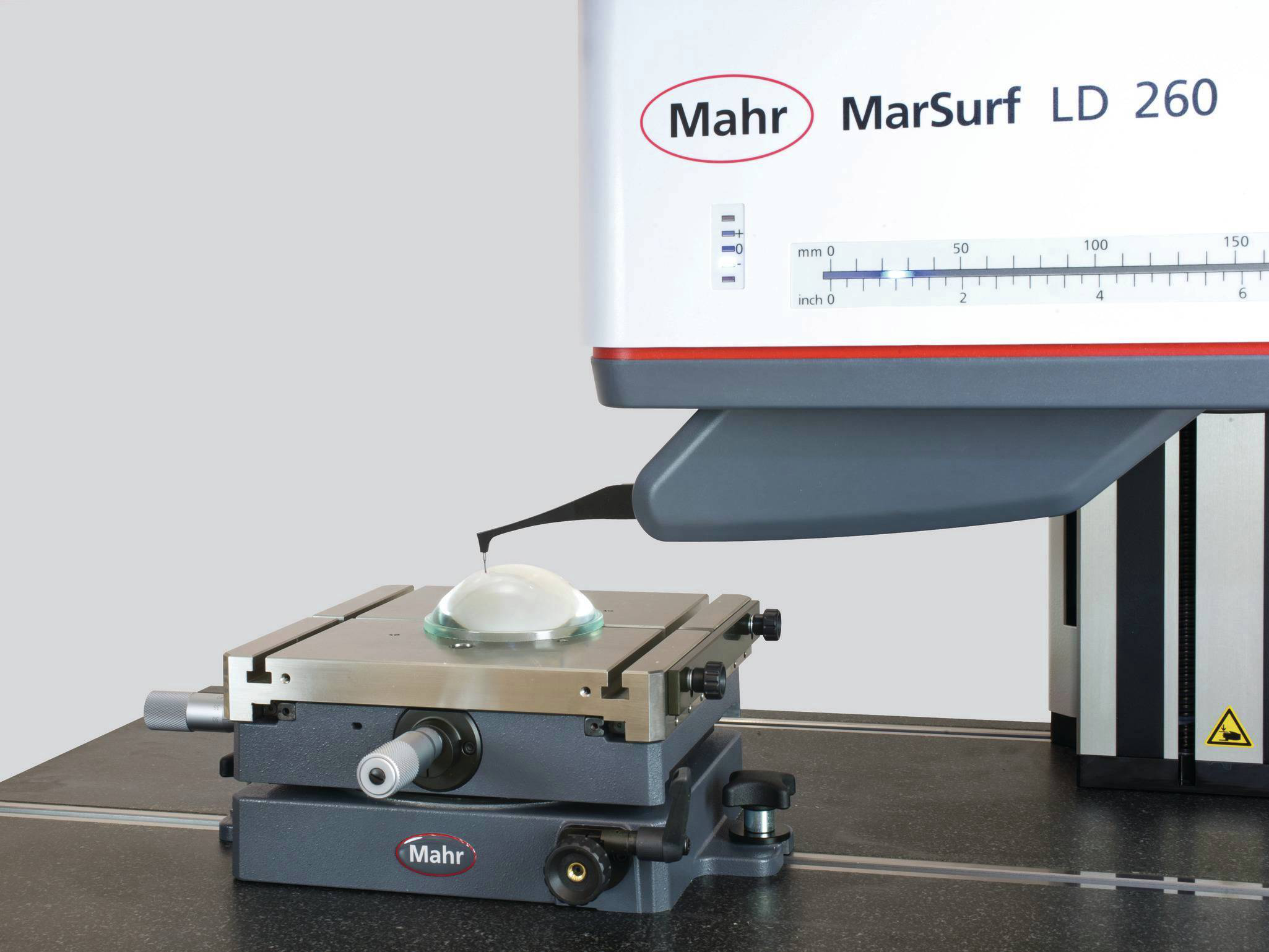
Yüksek hassasiyetli objektiflerin ölçümü için ölçüm istasyonları
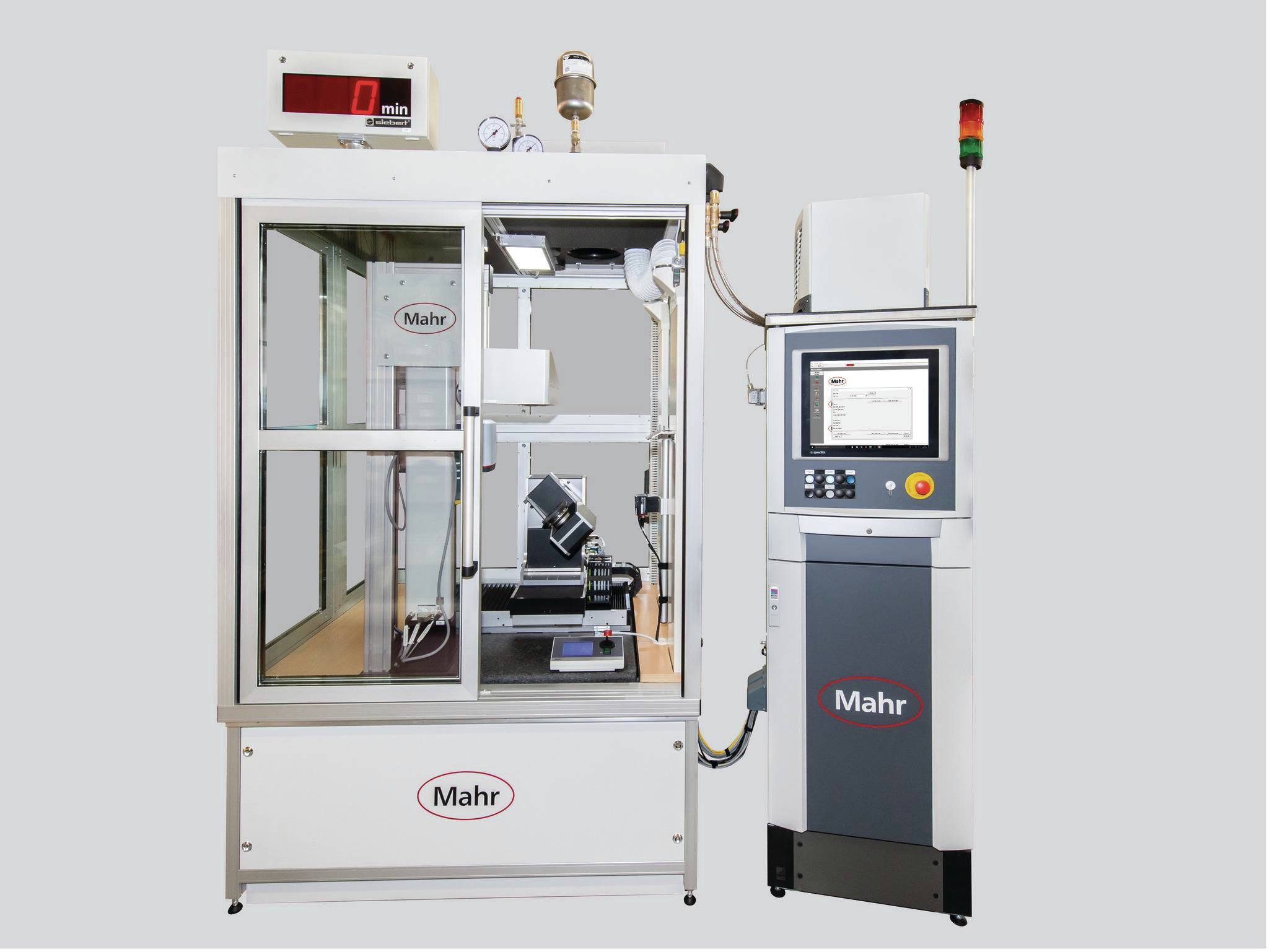
Standart çözümler artık yeterli olmadığında: Bağımsız özelleştirilmiş çözümler
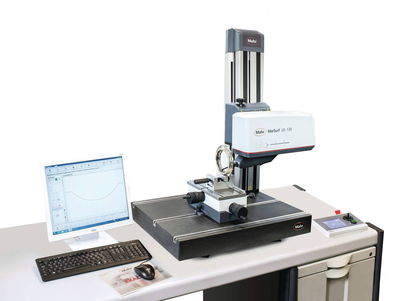
Sıkı toleranslara sahip yapılandırılmış işlevsel yüzeylerde, bir iş parçasının veya nesnenin topografisini kısa bir alanda minimum sürede kaydeden yüksek hassasiyetli ölçüm sistemleri gerekir.
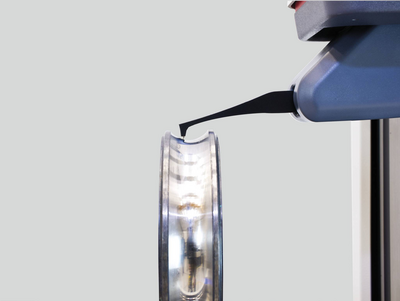
Ölçüm odalarında ve laboratuvarlarda çok yönlü ve güçlü kullanım
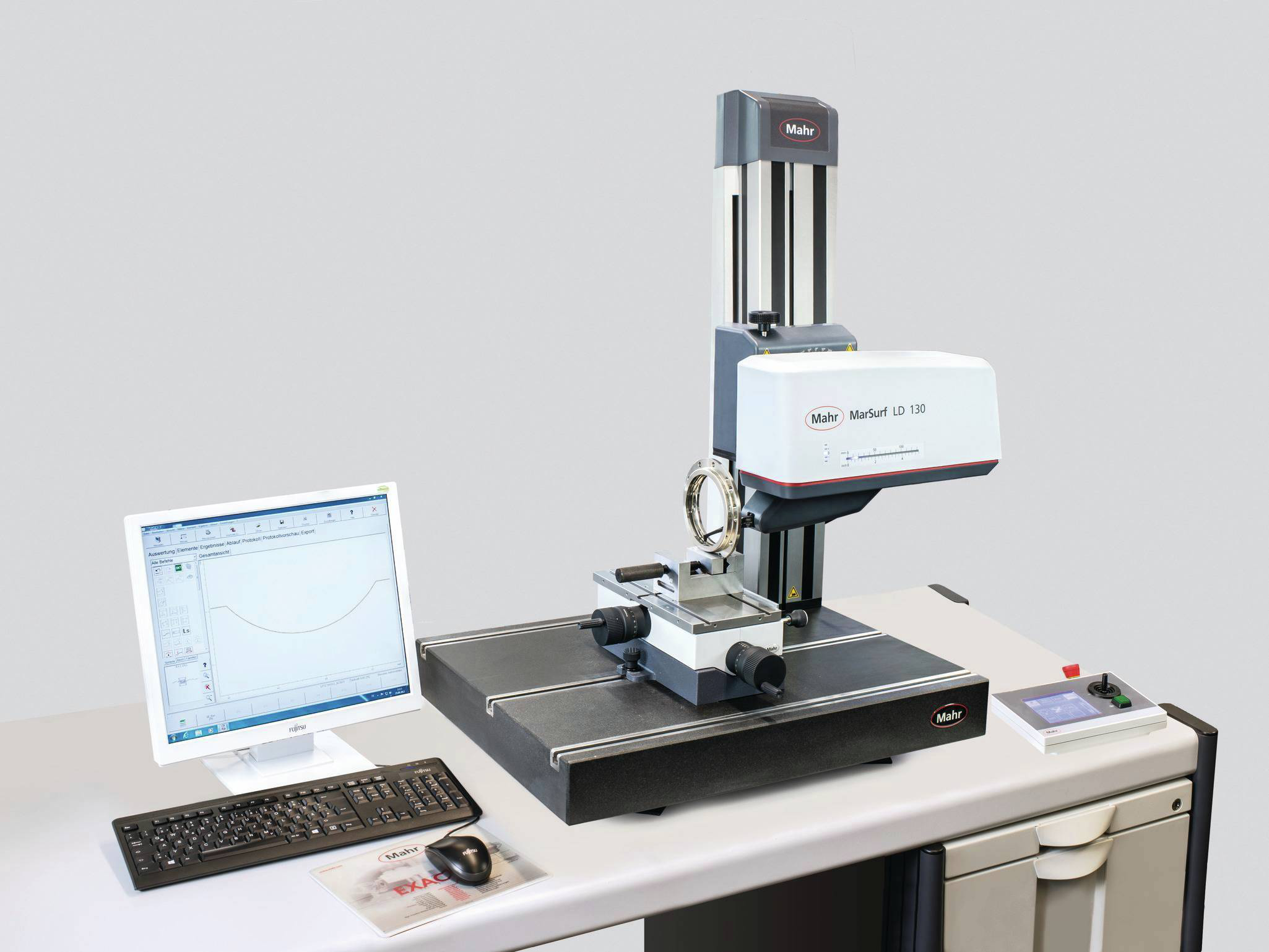
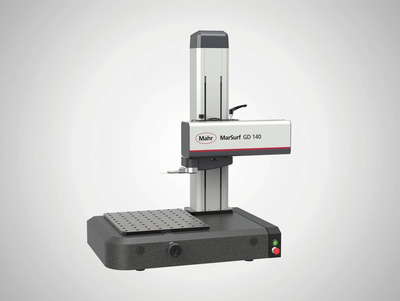
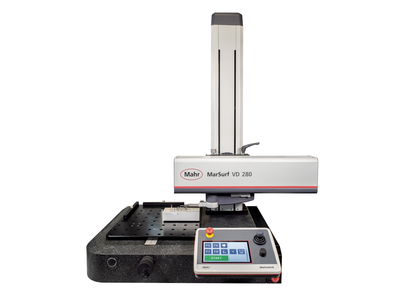
Kontur ve pürüzlülük ölçümü bir arada: Profesyonel çok yönlü
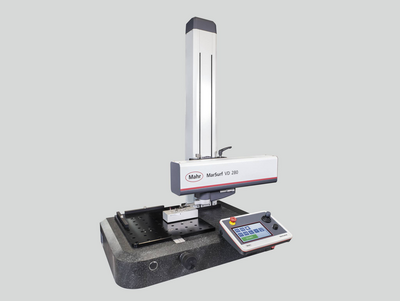
Kontur ve pürüzlülük ölçümleri için temaslı ölçüm istasyonları
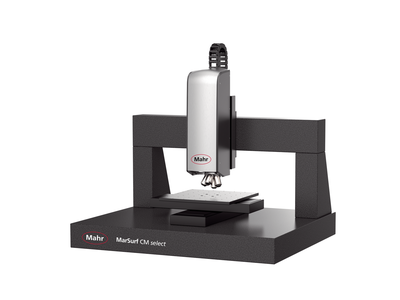
ISO 25178 / ISO 4287'ye göre 2D/3D kontur ve pürüzlülük ölçüm aksesuarları
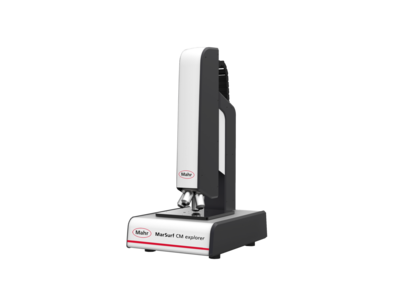
Endüstri ve araştırma için 3D yüzey metrolojisi
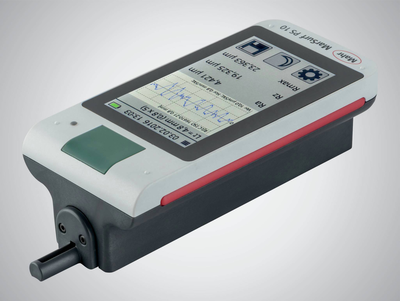
Mobil ölçüm cihazları ile her yerde ölçüm yapın!
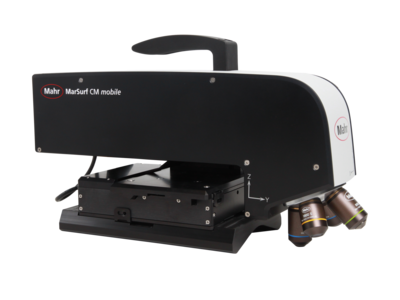
Kullanım için çok yönlü
mobil 3D yüzey metrolojisi
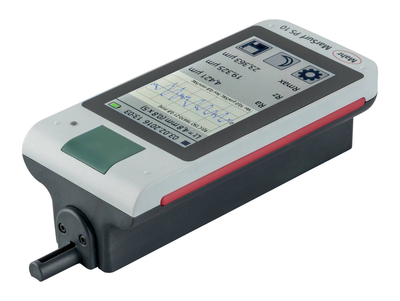
Mobil ölçüm aletleri, sonuçlara tam olarak ihtiyaç duyduğunuz yerde ölçüm yapmanızı sağlar.
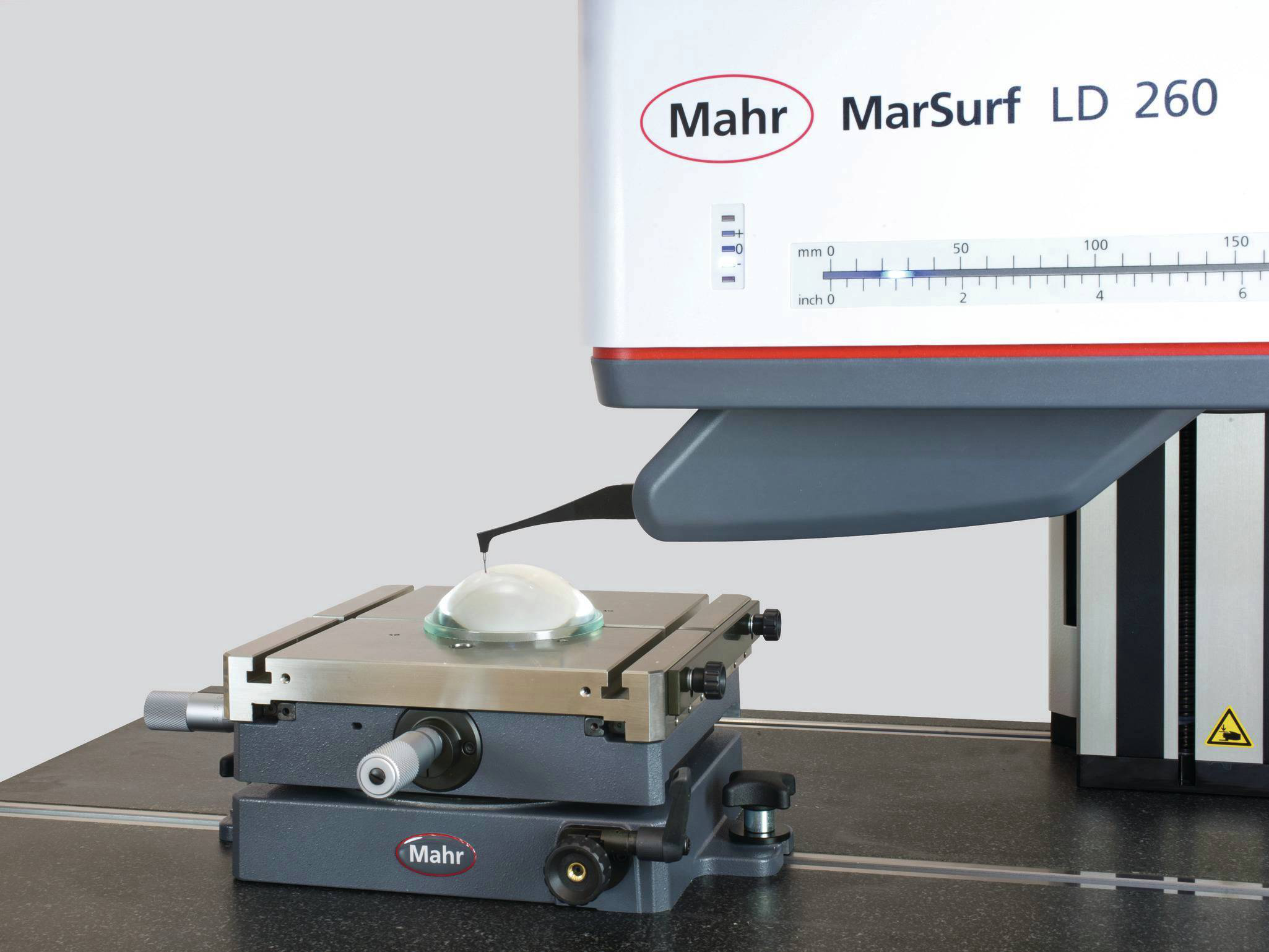
Ultra yüksek hassasiyetli objektiflerin ölçümü için ölçüm istasyonları
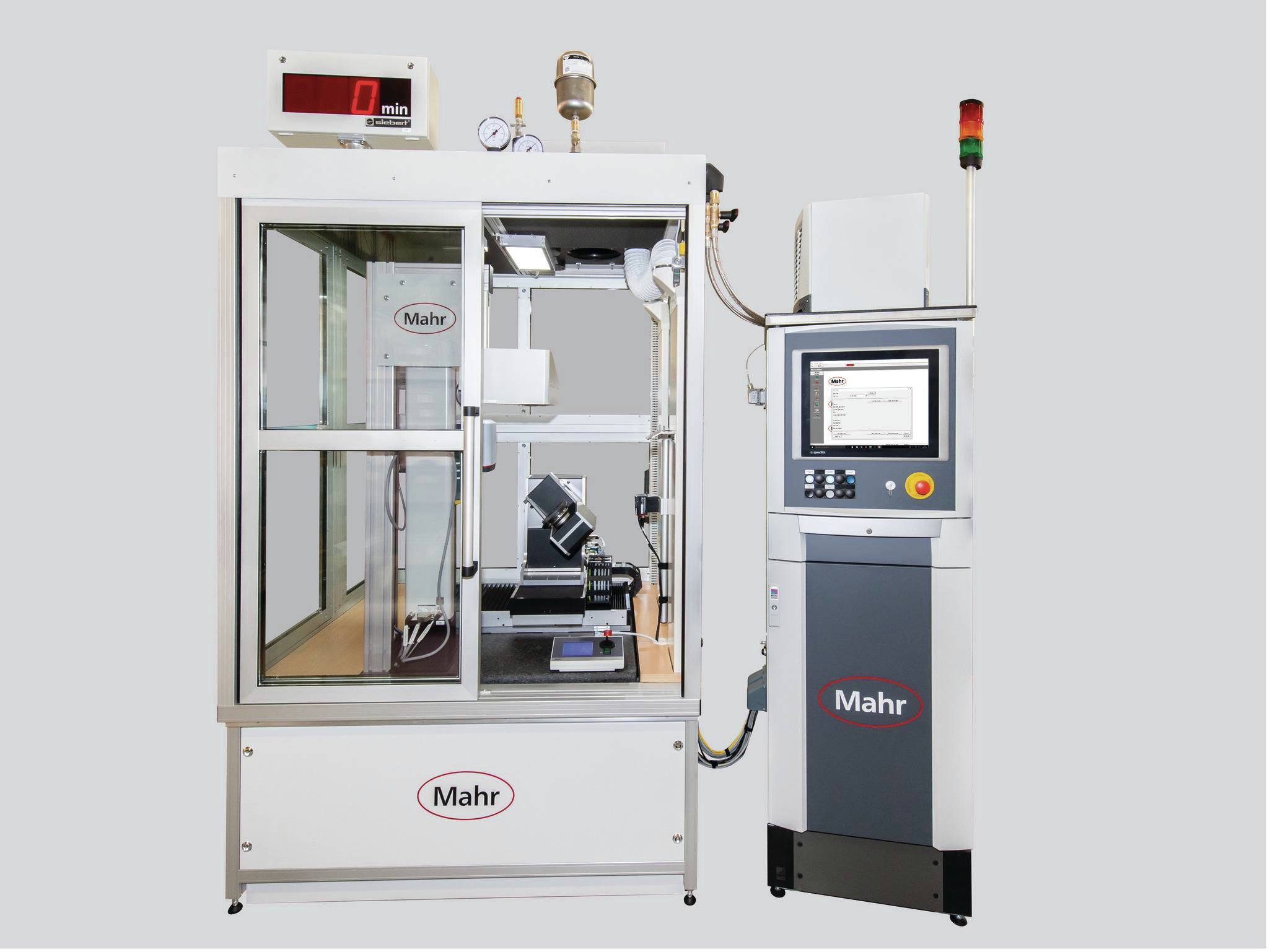
Standart çözümler artık yeterli olmadığında: Bağımsız özelleştirilmiş çözümler
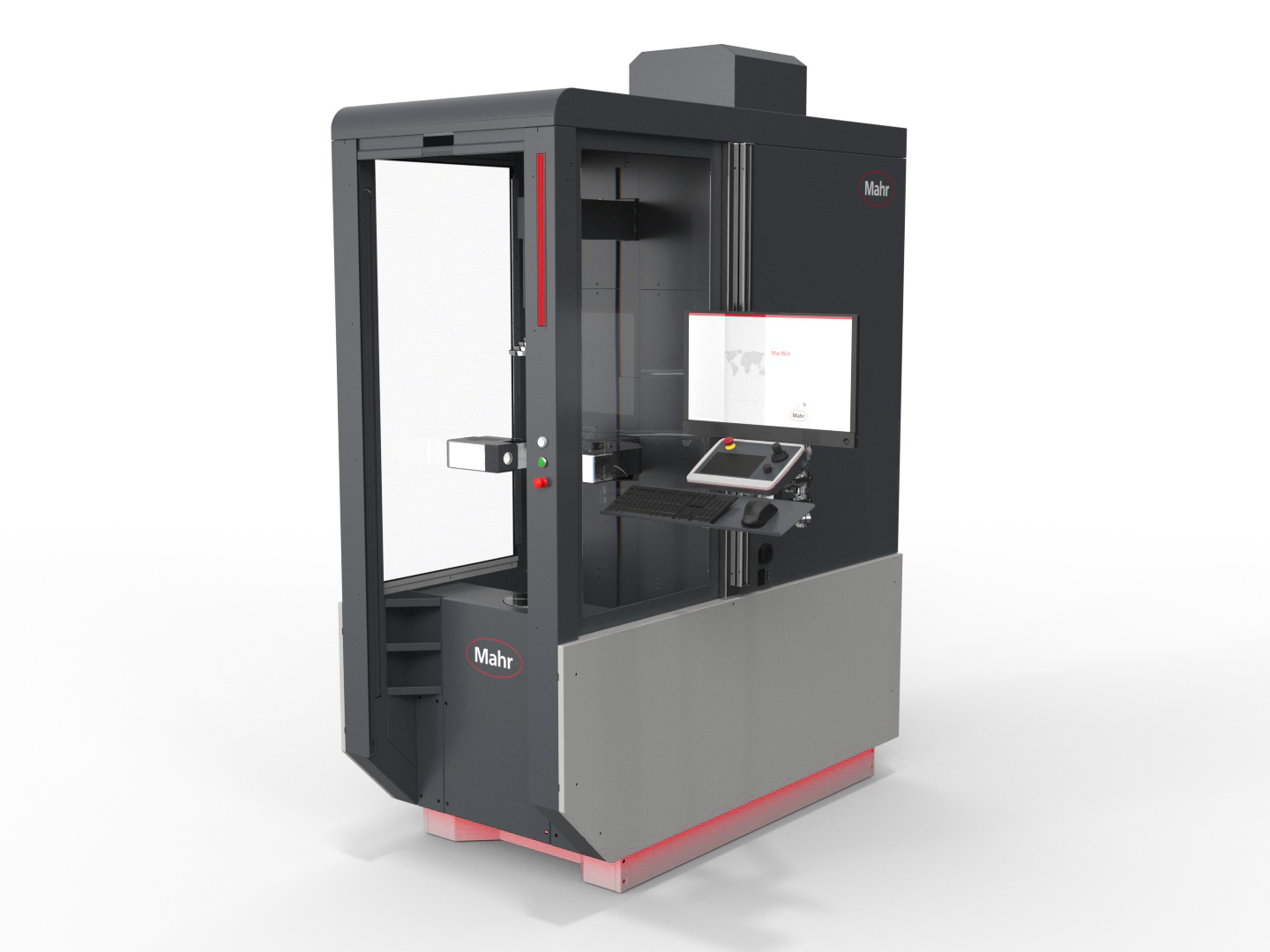
Metrology
Experience outstanding features combined with extreme flexibility in workpiece size and increase your productivity in the production environment.
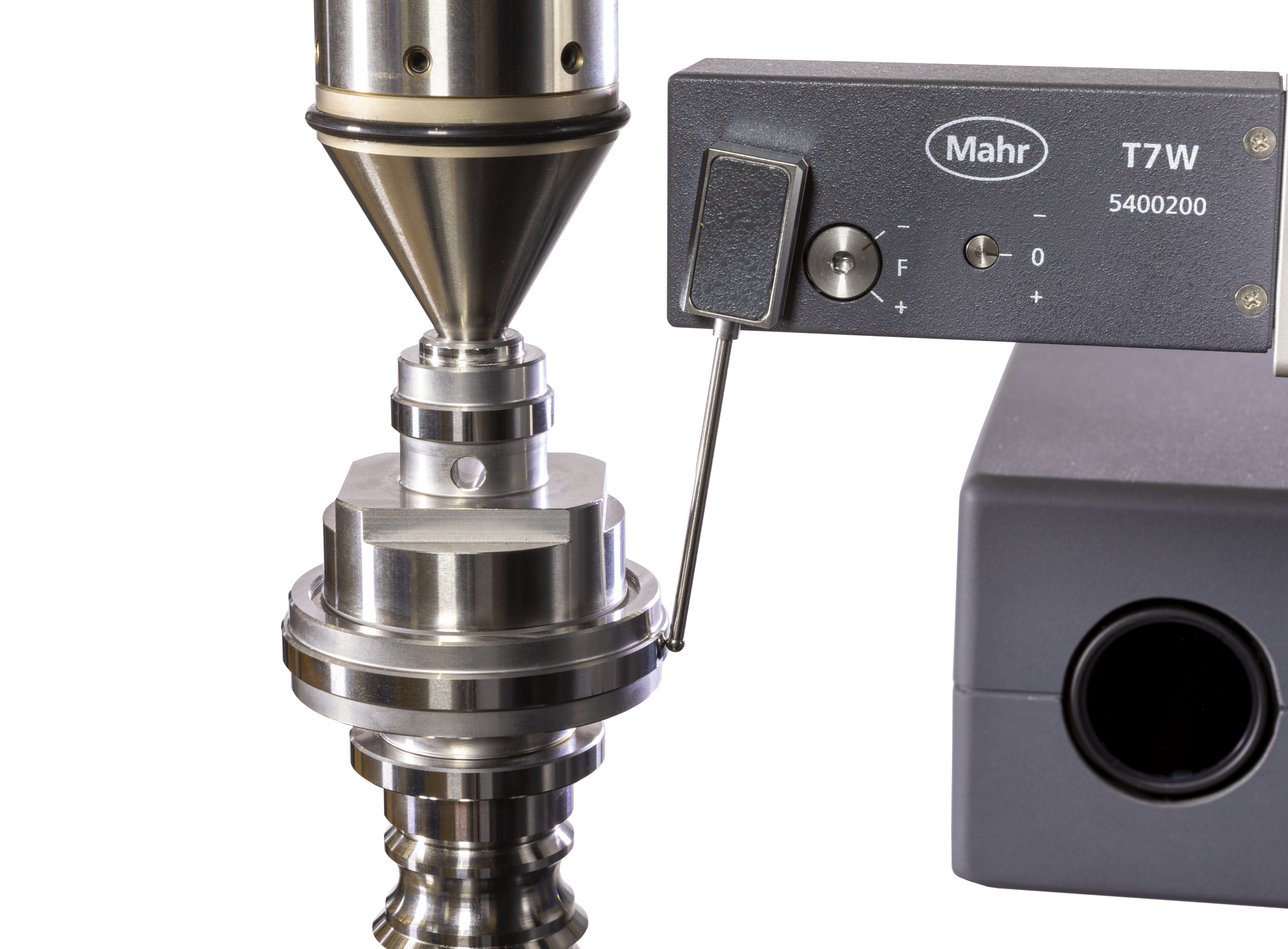
Fast optical matrix camera in combination with high-precision touch probes for measuring a large number of features on rotationally symmetrical workpieces.
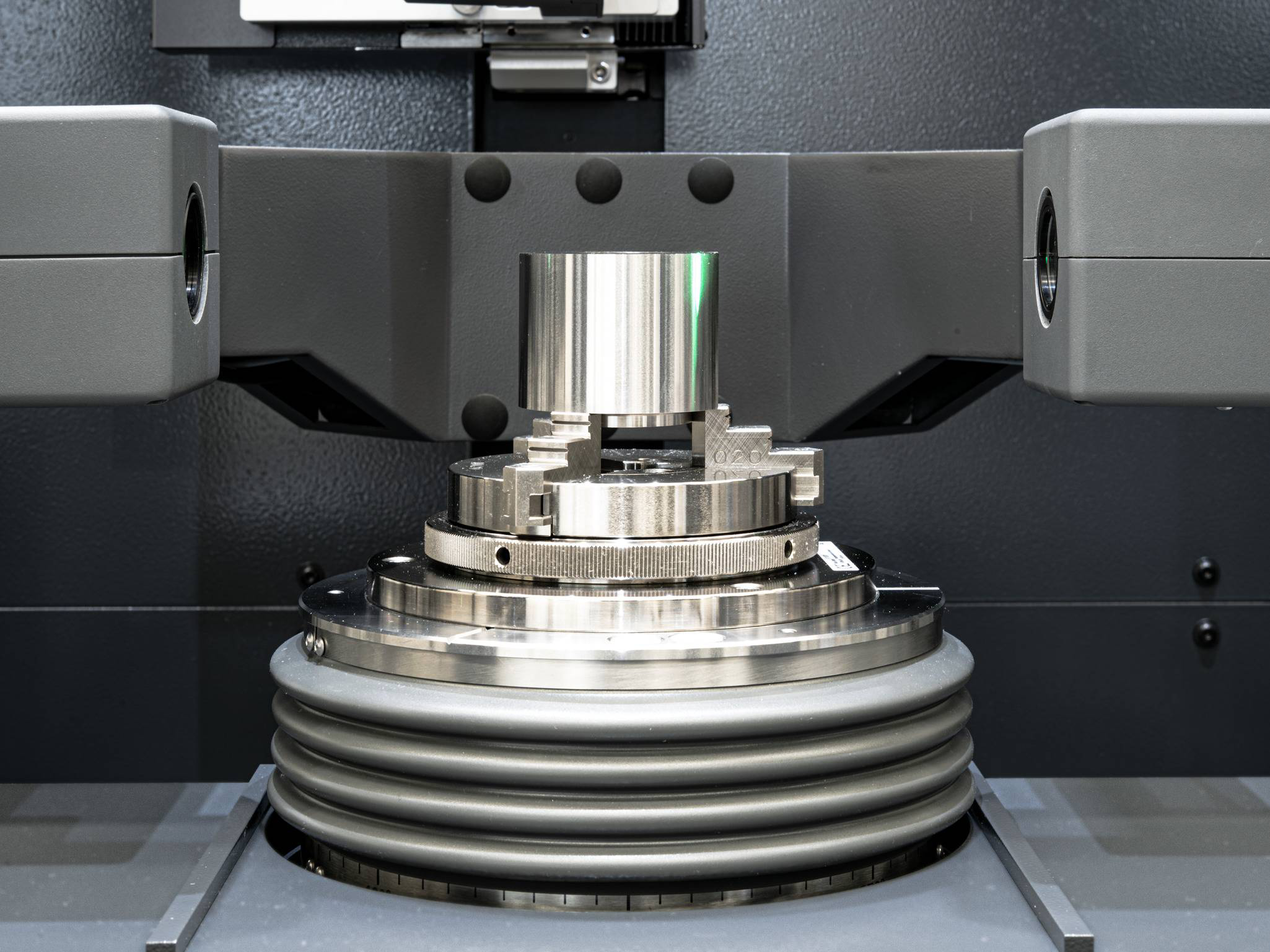
Fast optical matrix camera in combination with high-precision touch probes for measuring a large number of features on rotationally symmetrical workpieces. Addition of a fully automatic centering and tilting table for extremely fast, mechanical alignment, flexible clamping options and, for example, internal measurements.
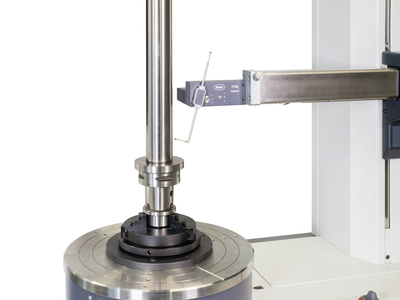
Yuvarlaklık, düzlük, doğrusallık, eş eksenlilik ve diğer ölçüm görevleri gibi form ve konum toleranslarını test etmek için sistemler. Manuelden tam otomatiğe.
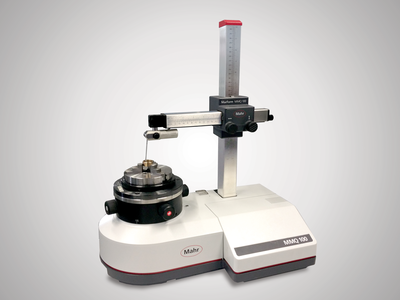
Cihaz yuvarlaklık, düzlük ve eş merkezlilik gibi özellikleri kolay, uygun maliyetli ve yüksek hassasiyetle ölçer. Manuel form ölçüm aletlerimiz hem ölçüm odası hem de üretime yakın ölçümler için uygundur.
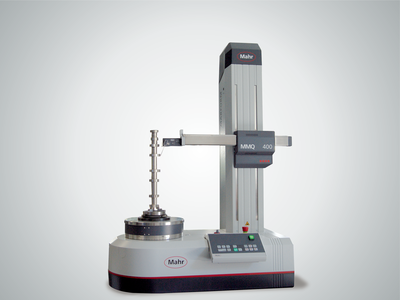
Otomatik form ölçüm sistemlerimizle, en yüksek otomasyon, esneklik ve hassasiyet seviyesine sahip kararlı, yenilikçi cihazlar aracılığıyla denetim maliyetlerinizi artırmadan süreç maliyetlerinizi düşürürsünüz.
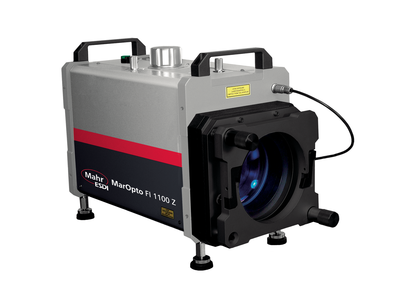
Güçlü MarOpto Fizeau interferometreleri, düz ve küresel yüzeylerde temassız ölçümler sağlayabilir.
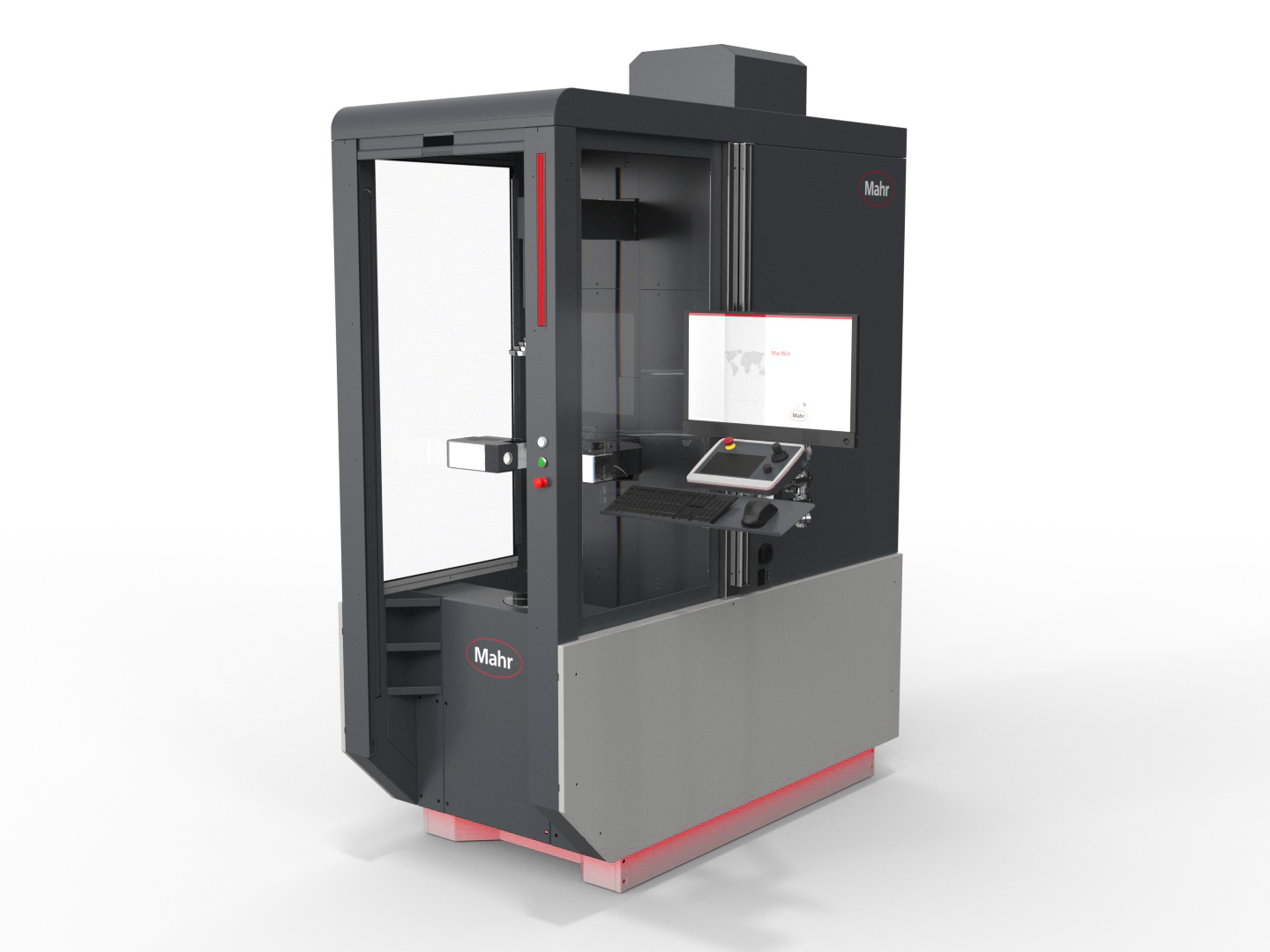
Metrology
Experience outstanding features combined with extreme flexibility in workpiece size and increase your productivity in the production environment.
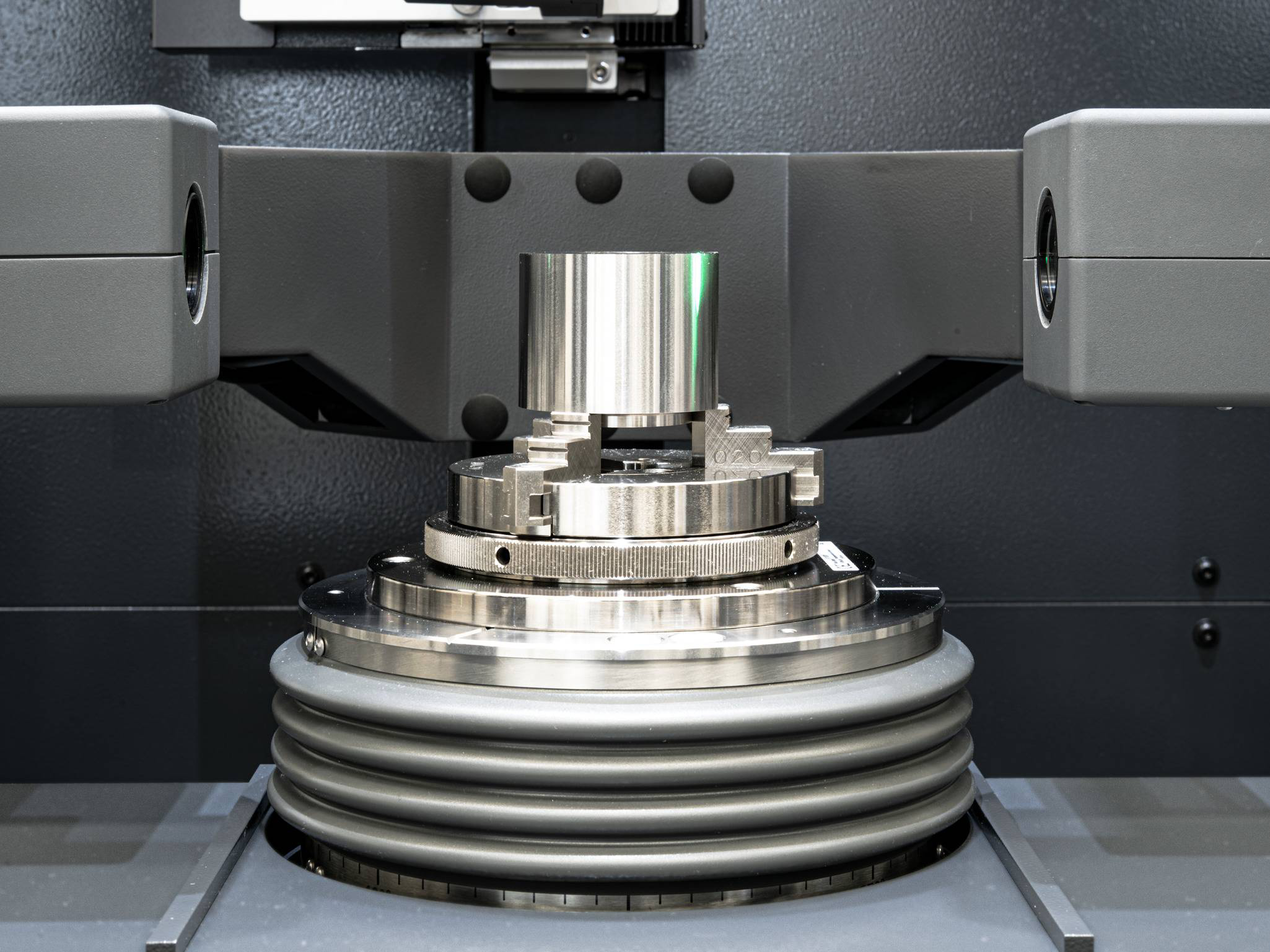
Fast optical matrix camera in combination with high-precision touch probes for measuring a large number of features on rotationally symmetrical workpieces. Addition of a fully automatic centering and tilting table for extremely fast, mechanical alignment, flexible clamping options and, for example, internal measurements.
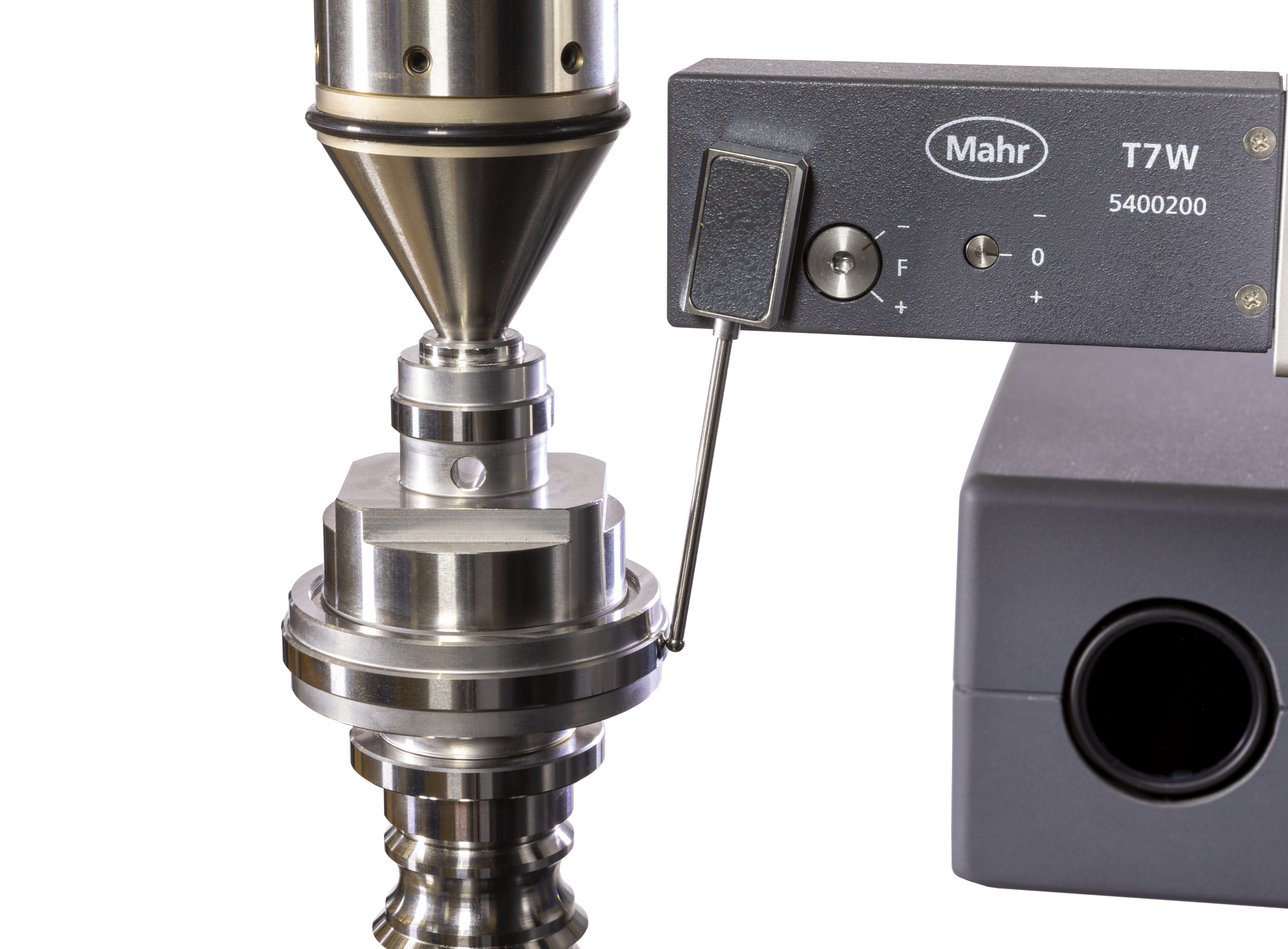
Fast optical matrix camera in combination with high-precision touch probes for measuring a large number of features on rotationally symmetrical workpieces.
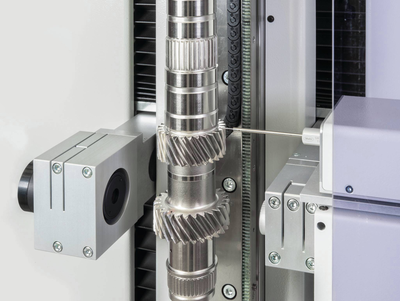
Zorlu üretim ortamlarında kullanım için optik ve temaslı mil ölçüm sistemleri. Tüm yaygın döner simetrik iş parçalarının eksiksiz ölçümü.
.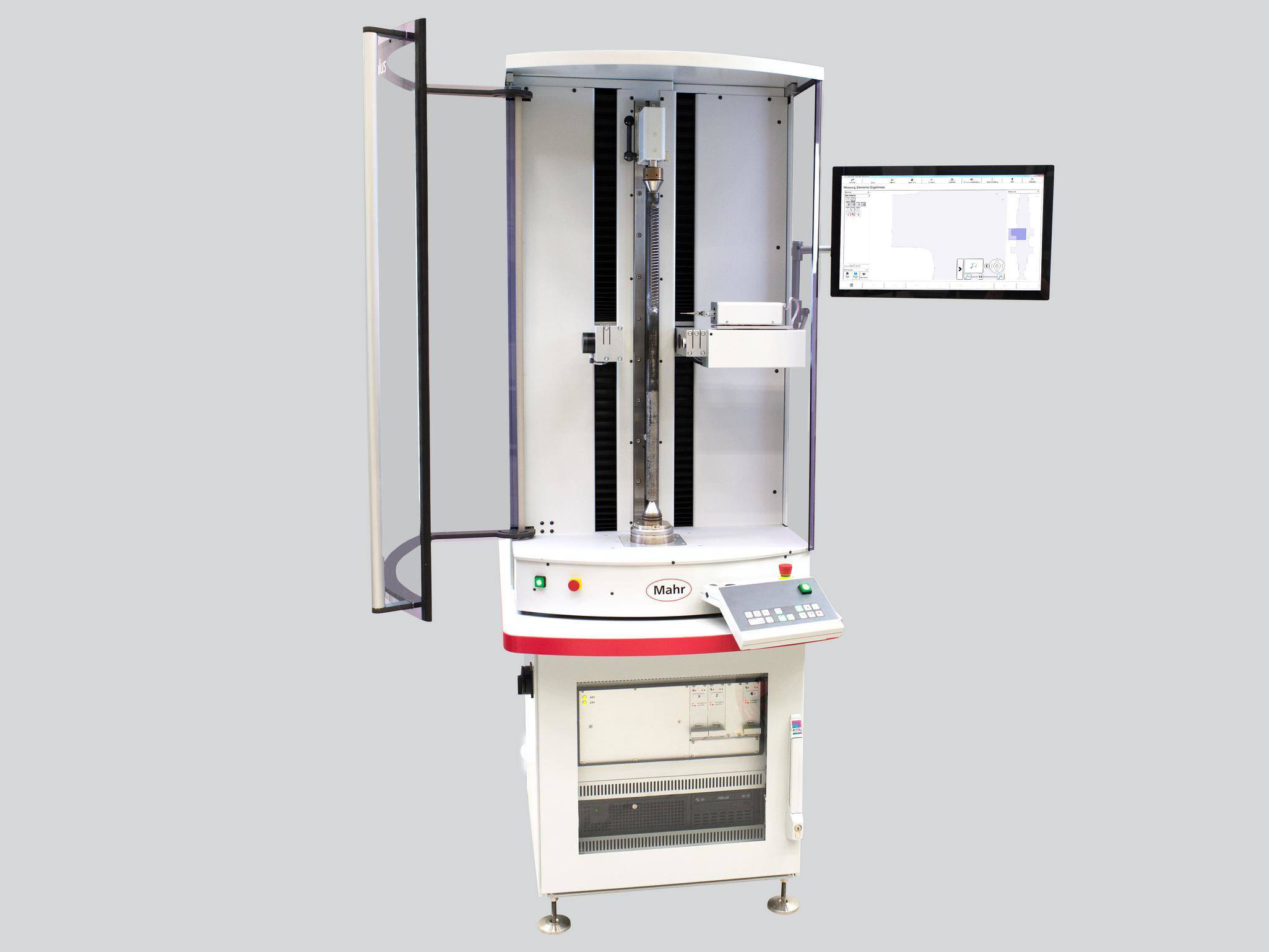
Zorlu üretim ortamlarında kullanım için optik ve temaslı mil ölçüm sistemleri. Tüm yaygın döner simetrik iş parçalarının eksiksiz ölçümü.
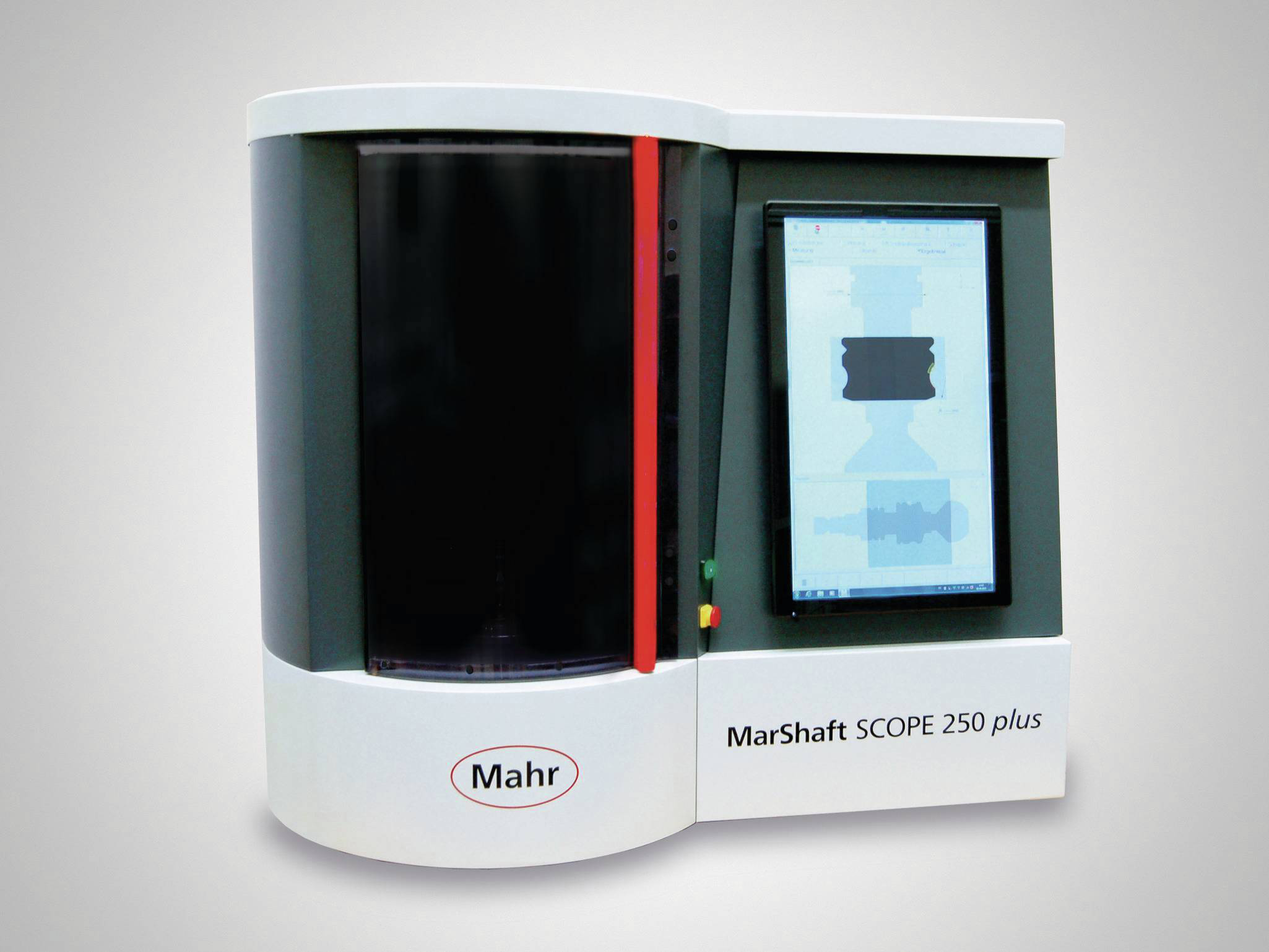
Zorlu atölye ortamlarında kullanım için çok amaçlı, tam otomatik ve sağlam optik mil ölçüm makineleri.
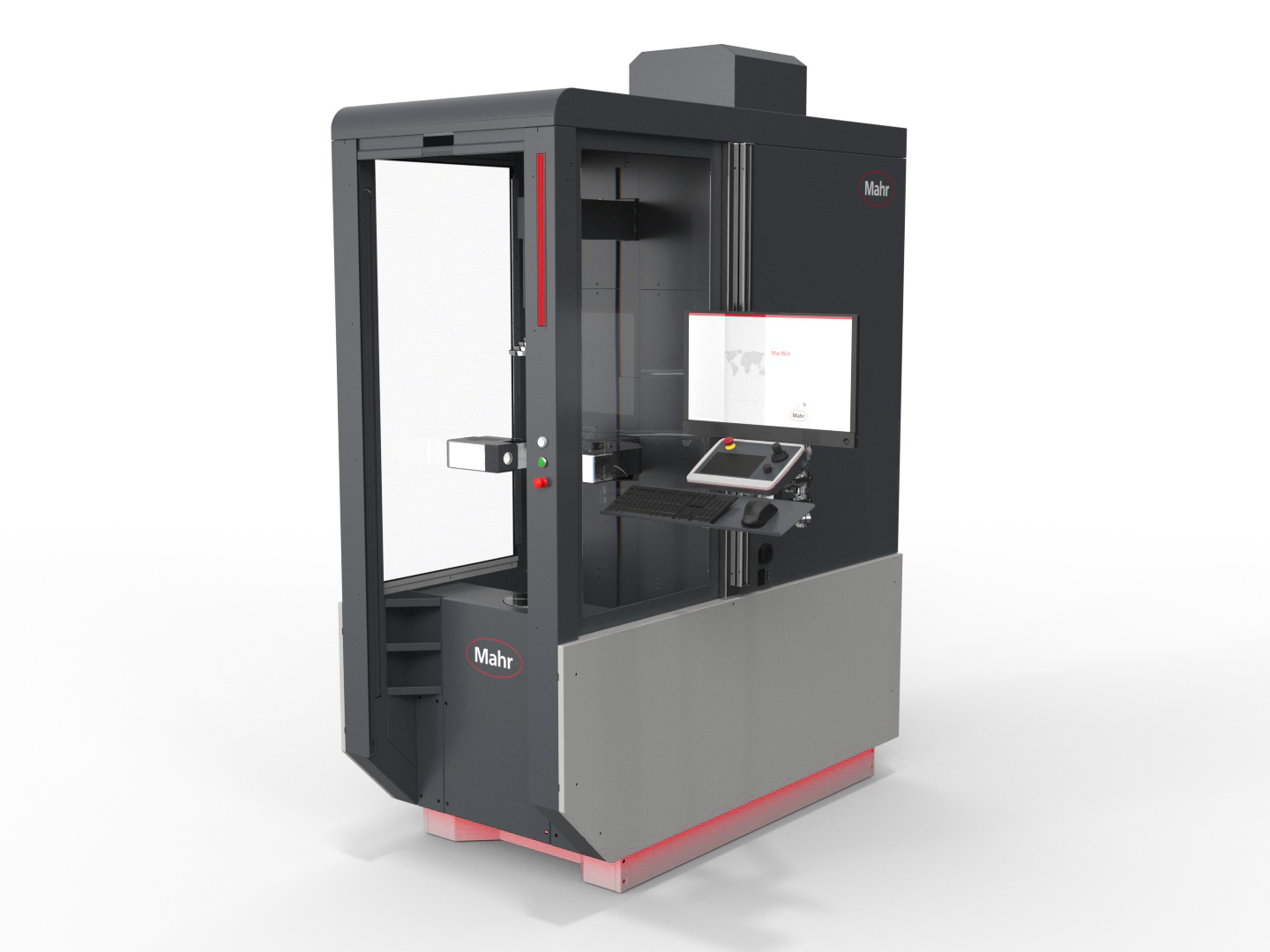
Metrology
Experience outstanding features combined with extreme flexibility in workpiece size and increase your productivity in the production environment.
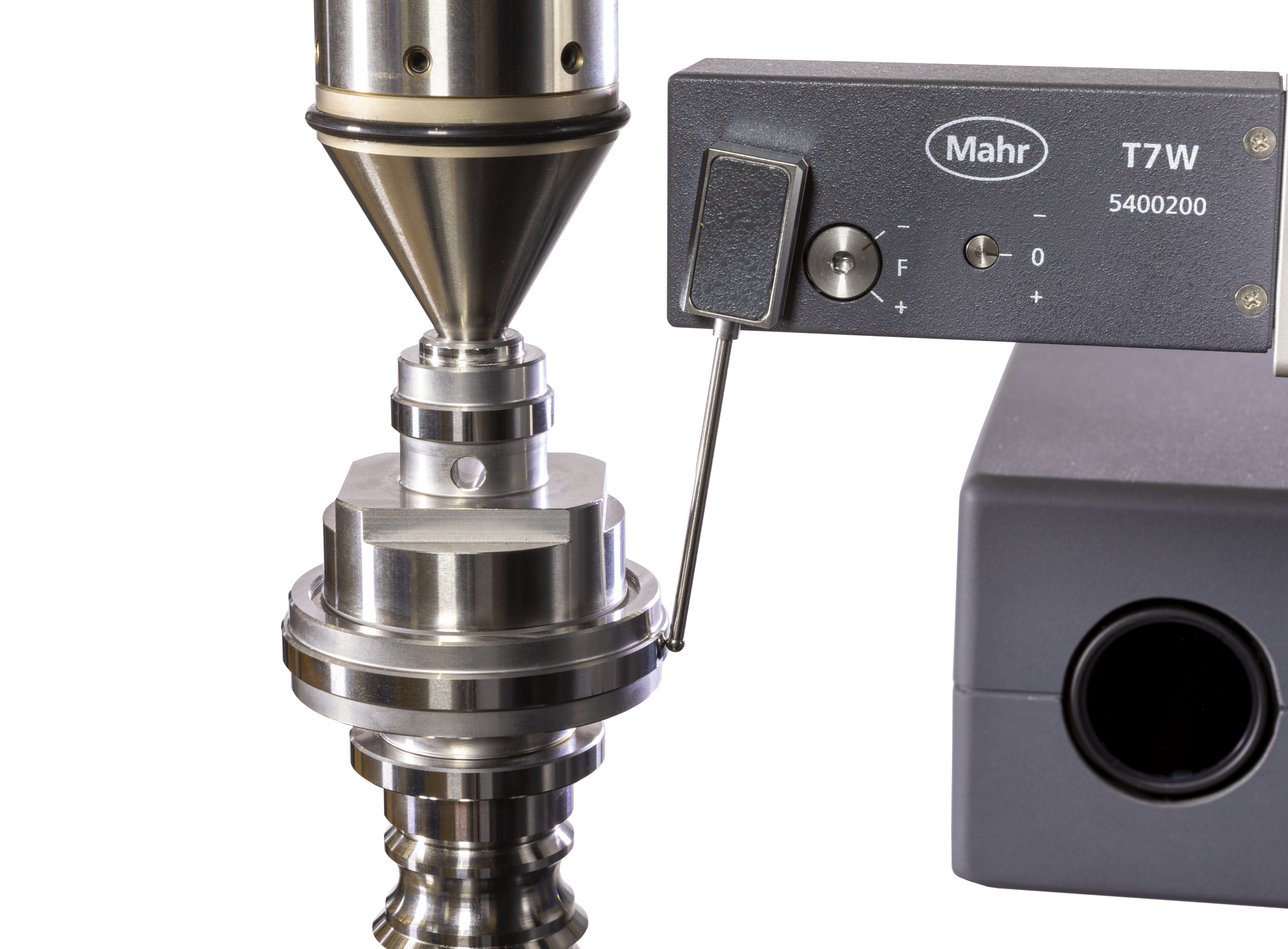
Fast optical matrix camera in combination with high-precision touch probes for measuring a large number of features on rotationally symmetrical workpieces.
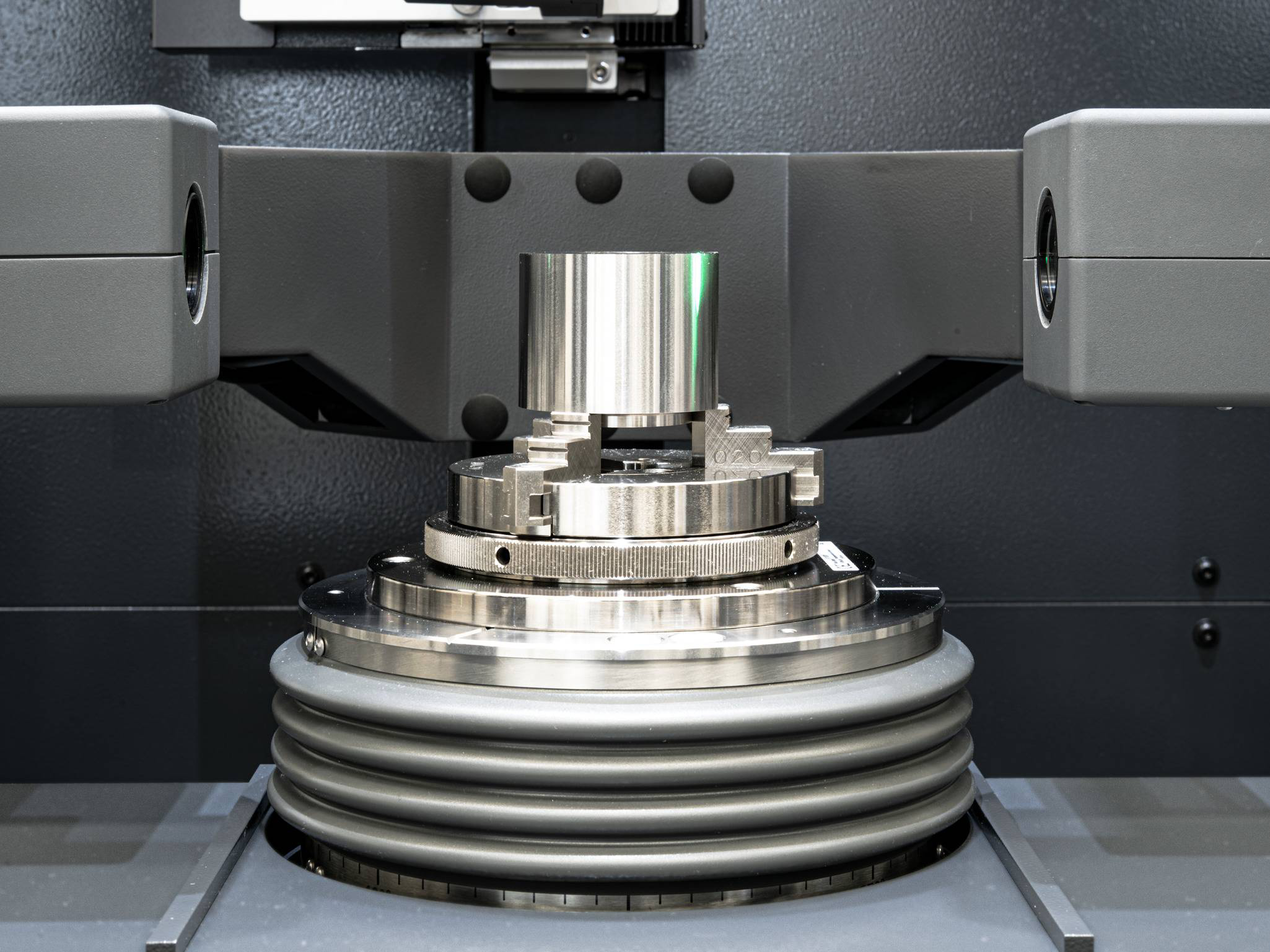
Fast optical matrix camera in combination with high-precision touch probes for measuring a large number of features on rotationally symmetrical workpieces. Addition of a fully automatic centering and tilting table for extremely fast, mechanical alignment, flexible clamping options and, for example, internal measurements.
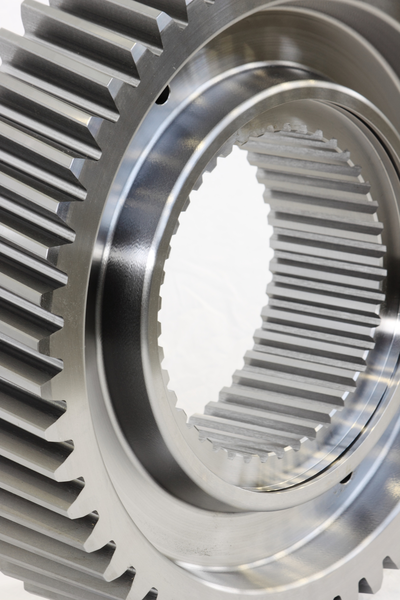
Son derece özel dişli analizlerinden tam entegre seri ölçüme kadar, Mahr, modern dişli ve dişli kutusu üretiminin her seviyesinde güvenilir ortağınızdır.
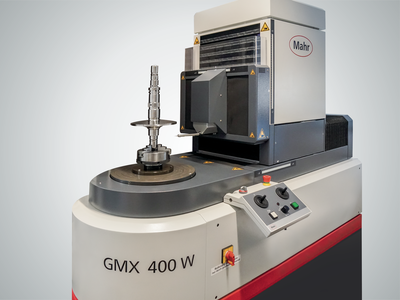
MarGear, esnek dişli ve silindir koordinat ölçüm aletlerimizdir. Birkaç farklı özelliğin eş zamanlı üretiminde hızlı geri bildirim gerektiğinde, MarGear doğru seçimdir. Dişlilerin biçim ve konum, boyut veya yüksek hassasiyetli ve tam otomatik incelemesi olsun: MarGear ölçüm görevini halleder.
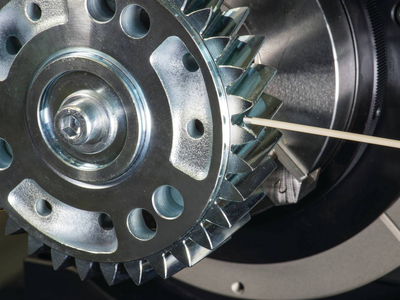
Atığı önlemek için üretim sürecine hızlı geri bildirim dahil olmak üzere ürününüzü çıkış noktasında ölçün.
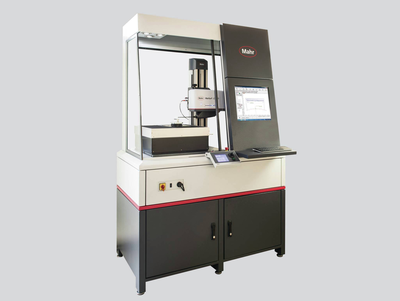
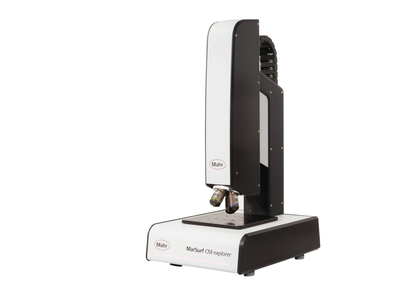
Yüzeylerin ve geometrilerin hızlı ve temassız kaydı için geniş teknoloji ve ürün yelpazesi.
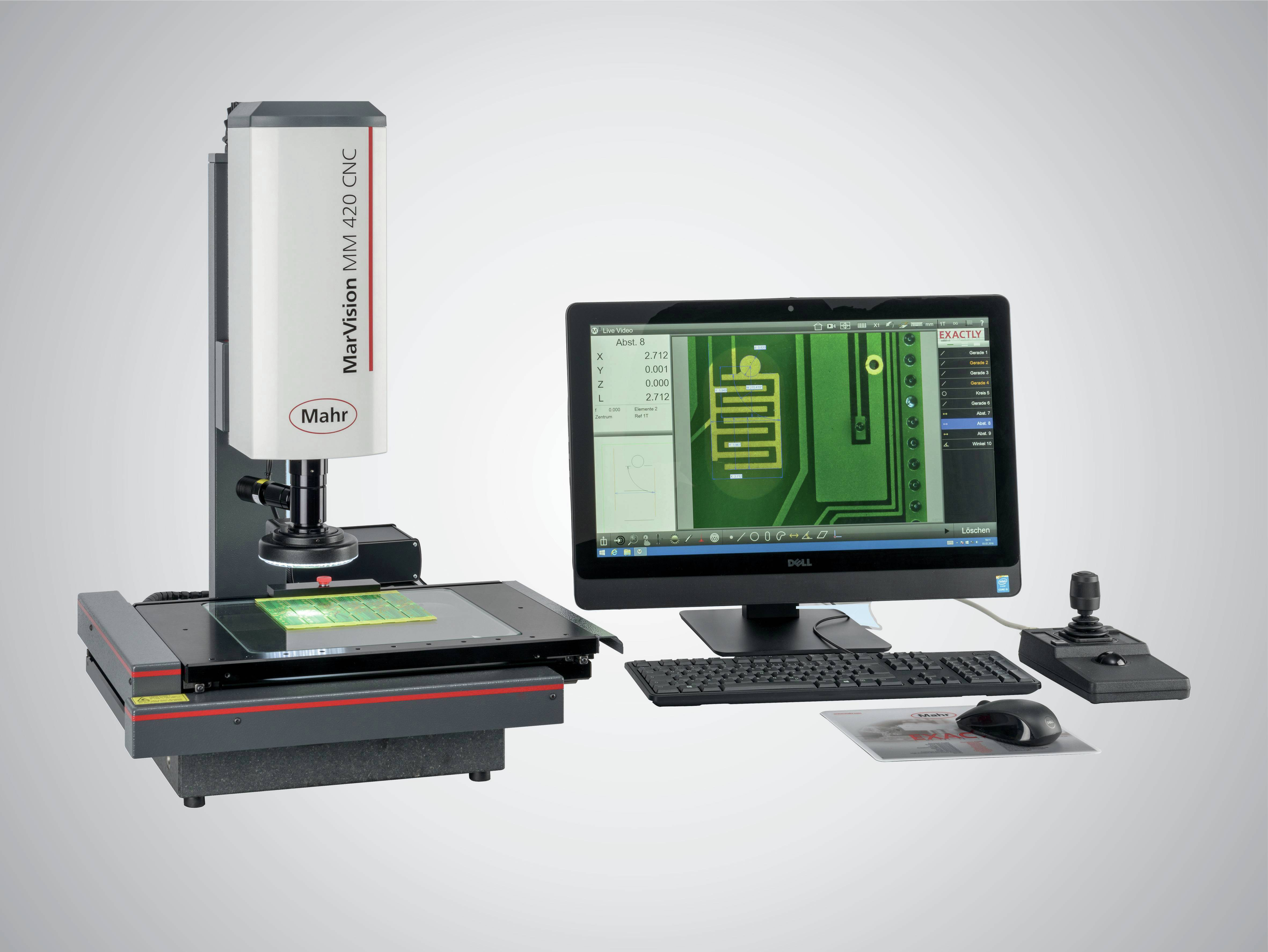
Mikroskoplar, hemen hemen tüm sektörlerde mesafe, yarıçap ve açıların hızlı bir şekilde incelenmesi için kullanılır. Laboratuvarda veya üretim alanına yakın metroloji.
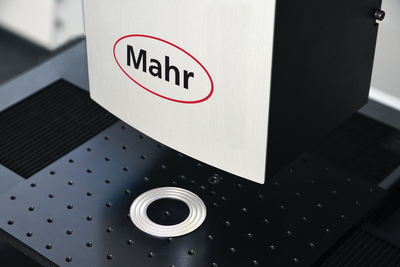
Pürüzlülük, kontur ve diğer birçok yüzey parametrelerinin belirlenmesi.
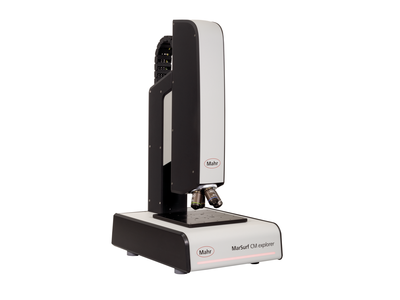
Endüstri ve araştırma için yüzey metrolojisi
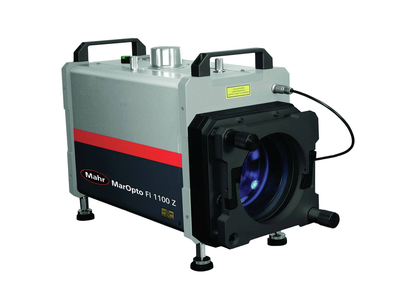
İster beyaz ışık ister lazer interferometre olsun, uygulamanız için doğru çözümü bulacaksınız.
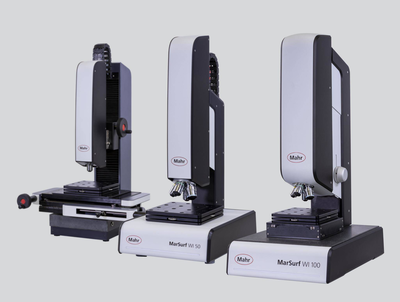
Nanometreye kadar hassas minimum pürüzlülük
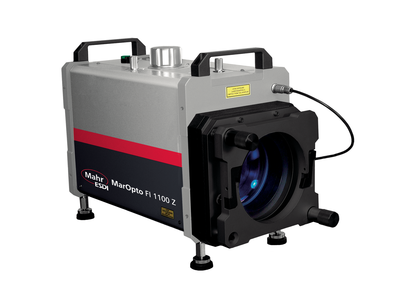
Güçlü MarOpto Fizeau interferometreleri, düz ve küresel yüzeylerde temassız ölçümler sağlayabilir.
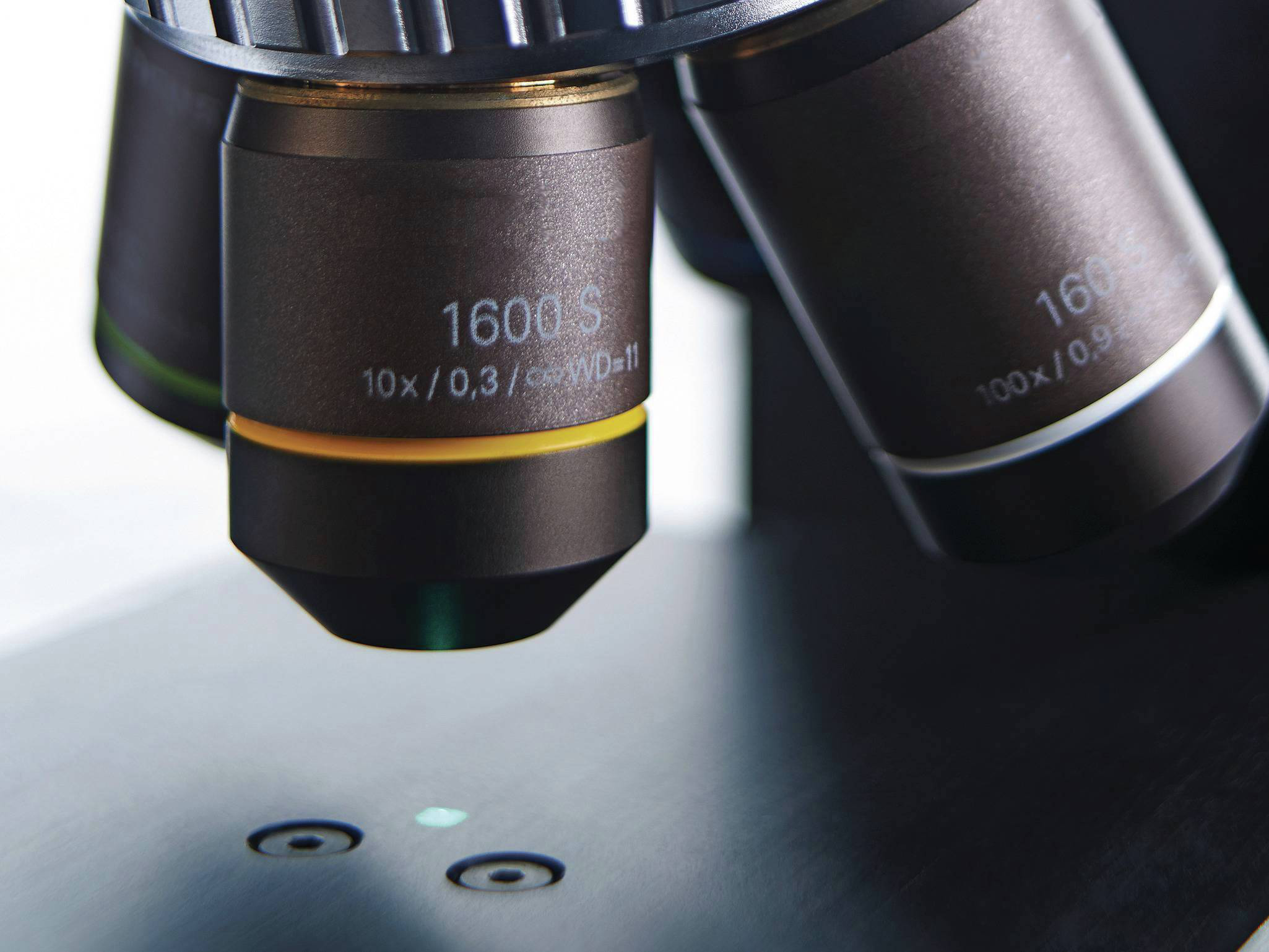
Yüzey topografyalarının ve geometrilerinin optik analizi
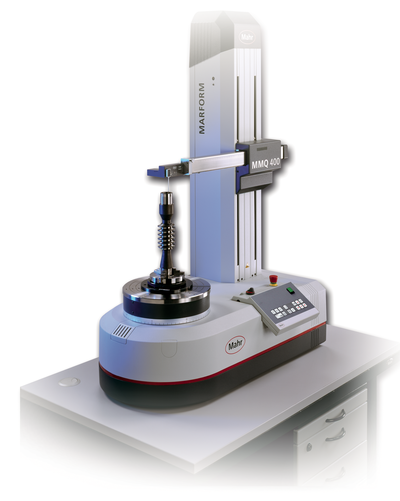
Kanıtlanmış Mahr kalitesinde yenilenmiş sistemler
Measuring large and complex components fully automatically
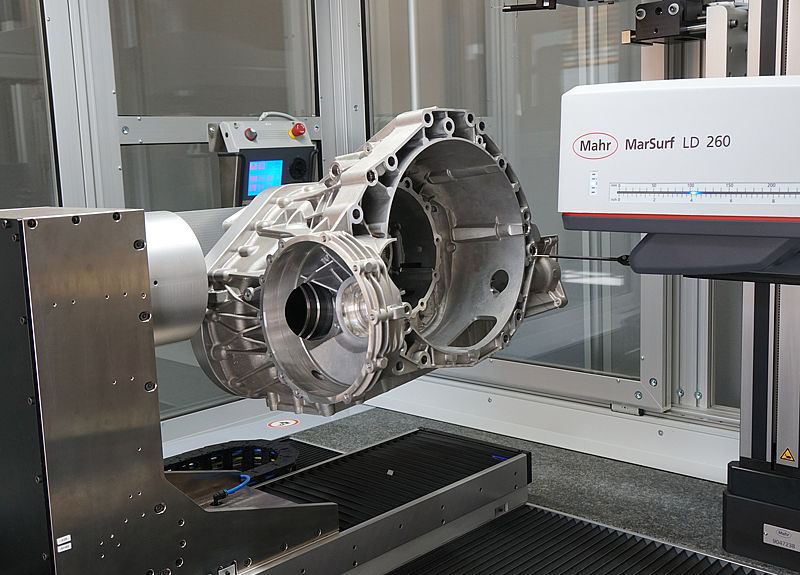
With the Series 2200 CNC measuring station with six positioning axes and a probe arm changing unit (TWE), roughness and contour features can be automatically and reliably inspected at almost all points on large components – even at difficult-to-reach measuring locations. "Some measuring points can only be reached with certain probe arms, and this requires a probe arm change. The TWE probe arm changing unit takes care of this fully automatically, so that the measurements are carried out without interruption," explains Karl-Josef Gödecke from the Mahr ServiceCenter and responsible for application technology in the surface area. Within 2:15 hours, a maximum of 292 features can be determined on a component in this way.
Short paths, fast results
The user-friendly CNCplus software ensures that users can operate the measuring station reliably after only a short training period. They can also quickly work through the test plans thanks to the fast positioning options for individual measuring points. The measurement results are quickly available, making it possible to intervene in the production process if necessary. This lowers costs due to reduced scrap rates, because tool change intervals are extended. "Thanks to the active vibration damping system, the CNC measuring station can also be integrated directly near the production line – short distances and fast test results are guaranteed," says Gödecke.
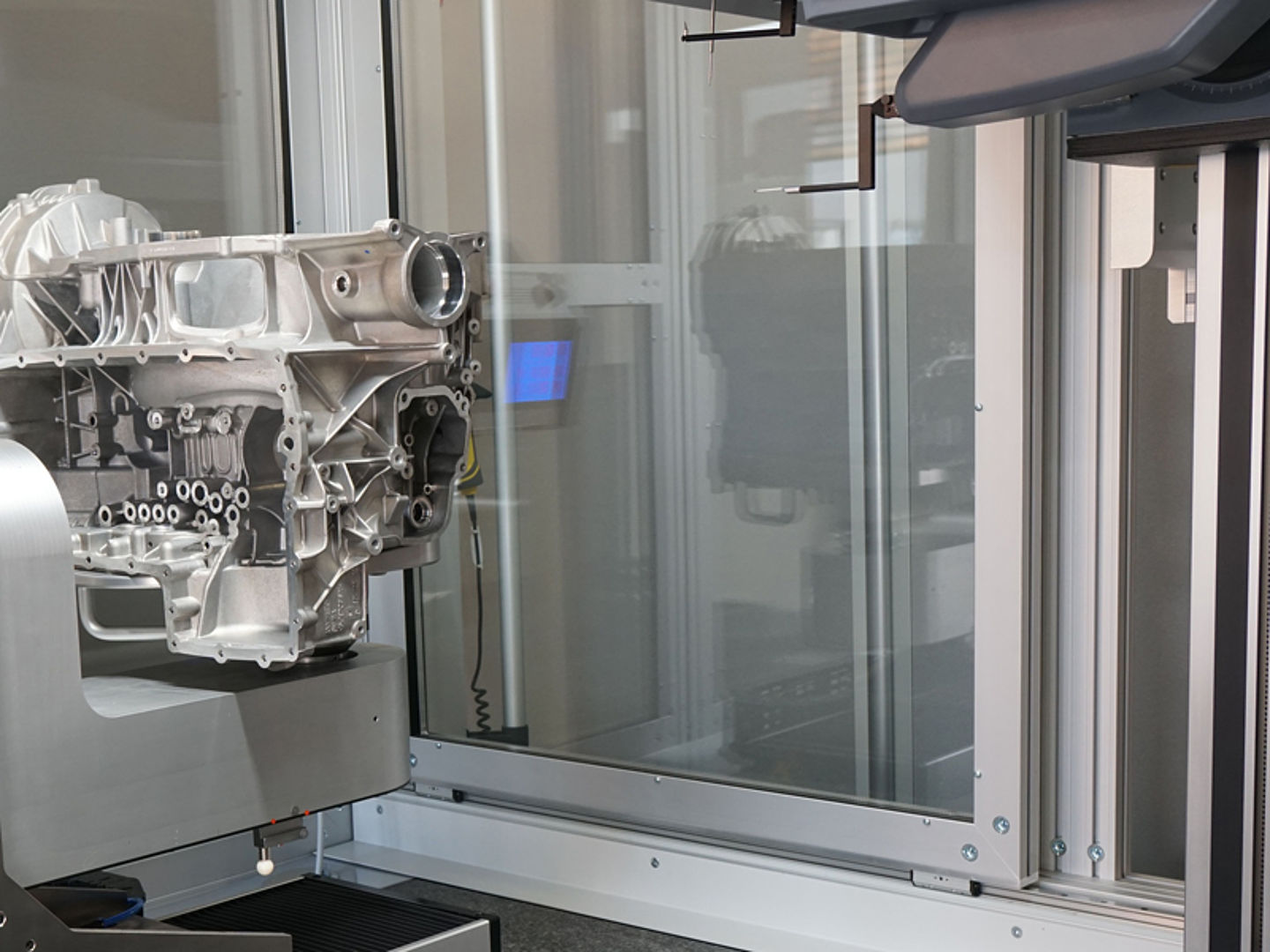
Automatic measuring sequences
Due to the fully automatic sequences, the operator only has to position the component with the hoist in the pneumatically clamping fixture and read in the DMC code via laser scanner. This starts the associated measuring program, and the operator can devote himself to other tasks. The data from the scanned DMC codes is automatically transferred to the log header. Incorrect or incomplete logging is thus ruled out, and unambiguous traceability is guaranteed. The measurement results are logged comprehensively and displayed in a table with tolerance bars. According to the customer-specific data structure, they are exported to the respective folders and files. It couldn't be simpler! Manual testing of the same component, on the other hand, would take more than 16 hours in total. It would also require a consistently high level of concentration on the part of the tester to ensure that he does not forget any measuring points and performs all measurements reliably.
Conclusion: Fully automatic measurements are completed seven times faster and take the tester only five minutes – instead of 16 hours or 960 minutes.
The system consists of the following components:
- Measuring stand ST 750 CNC and hard stone plate with vibration damping system and base frame
- Measuring station enclosure
- Storage cabinet and hoist
- Control panel
- Laser scanner for reading DMC codes
- Measurement of the clamping position
- Table positioning axes
- Drive unit and touch probe LD 260
- Probe arm changing unit
- Probe arms
- Positioning axes and clamping system
- Measuring station ergonomics
- Enclosure
- Traffic light and runtime display
All advantages at a glance
- Fully automatic roughness and contour measurements on large components
- Measurement of all roughness and contour features also with double probe arms
- Automatic workpiece recognition with DMC
- Automatic workpiece recognition with DMC laser
- Automatic probe arm change
- Safety concept for fast and safe measuring sequences
- Measuring housing and vibration damping system for use close to production
- Maximum measuring accuracy for the smallest tolerances and best repeatability
- Extremely easy operation thanks to the operator guidance of the CNCplus program
- Fast amortization thanks to fully automatic measuring sequences and minimum personnel requirements
For more information about the CNC roughness and contour measuring station for large components Series 2200, please contact Christopher Mollenhauer: Tel. +49 (551) 7073-99538 Christopher.Mollenhauer@mahr.com
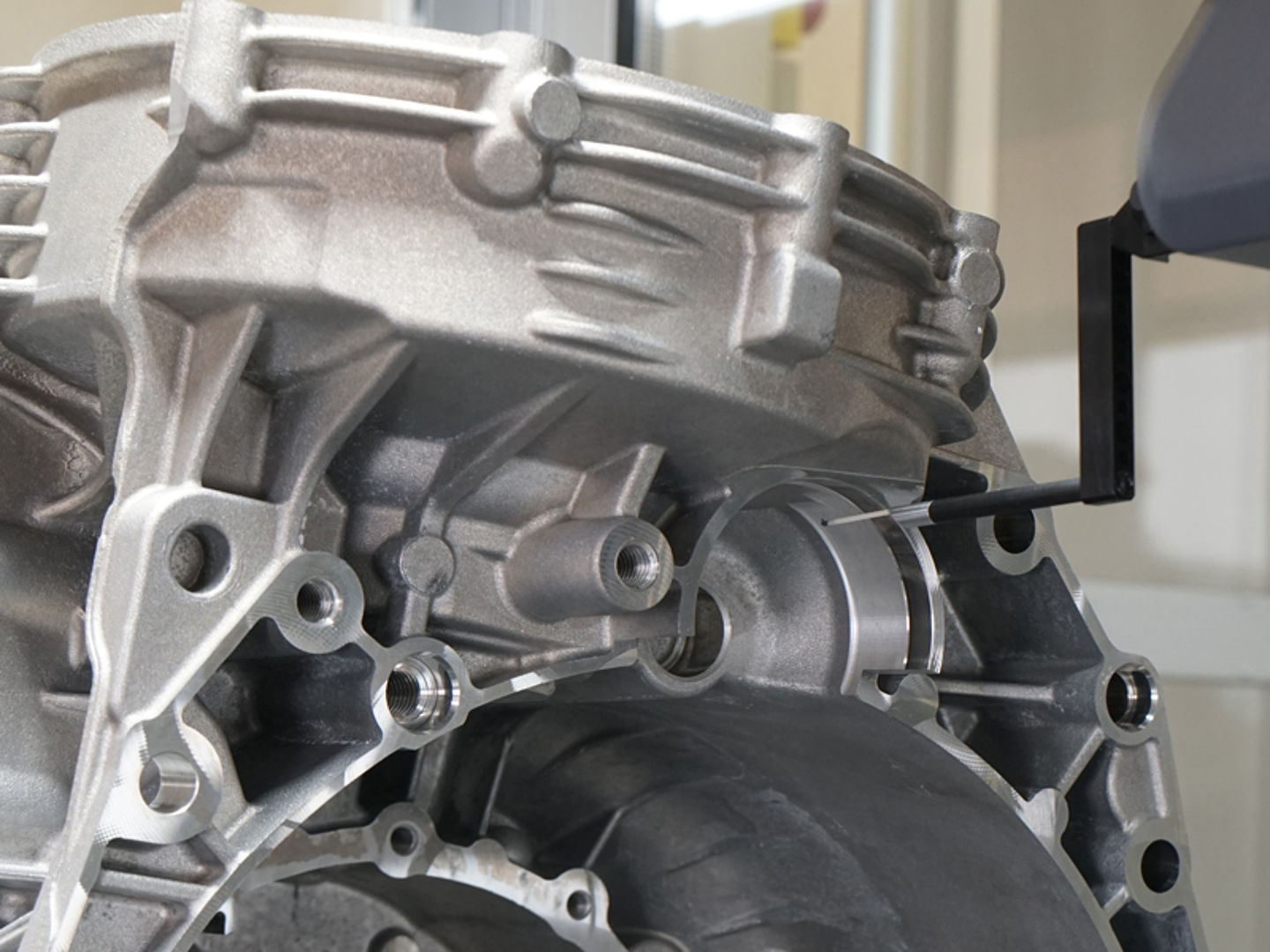