Gear Metering Pumps & Meter Mix Dispense Machines with highest accuracy for processing liquids and pastes.
High-precision rotary stroke bearings for backlash-free linear and rotational movements for use in machine and device construction.
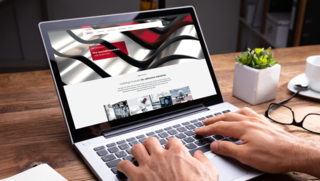
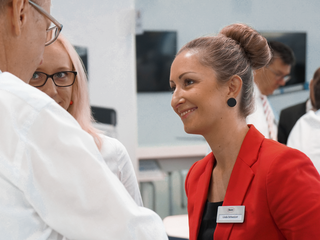
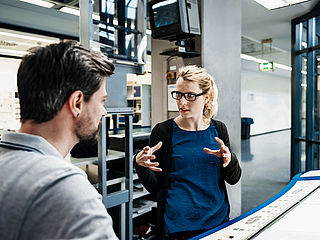
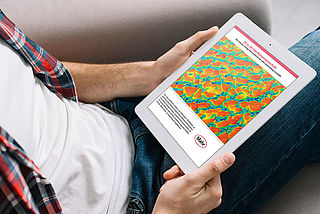
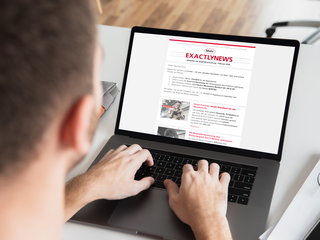
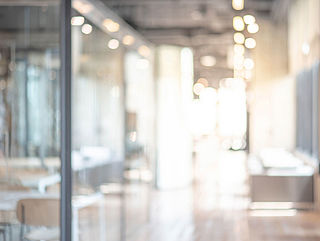
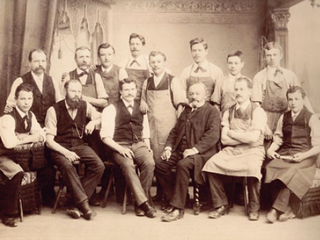
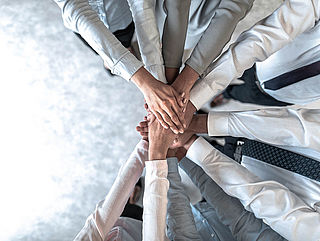
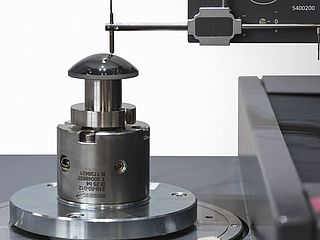
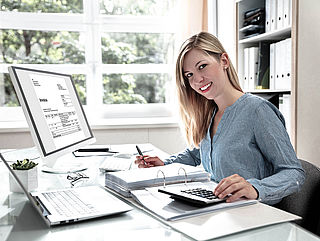
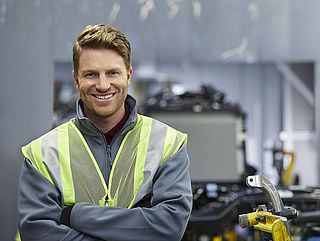
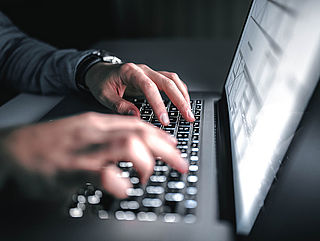
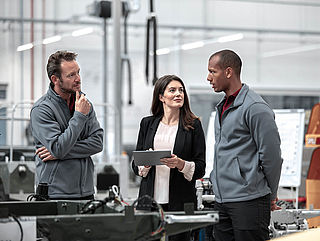
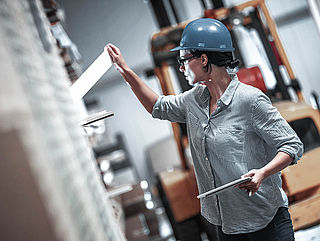
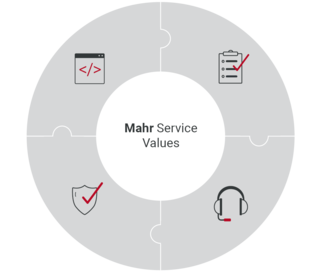
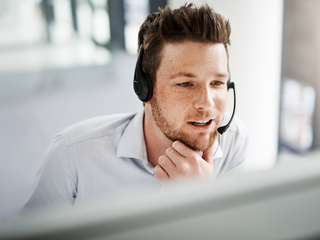
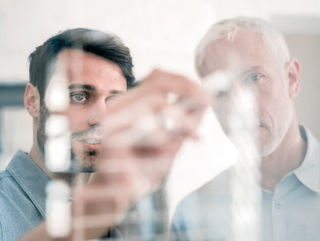
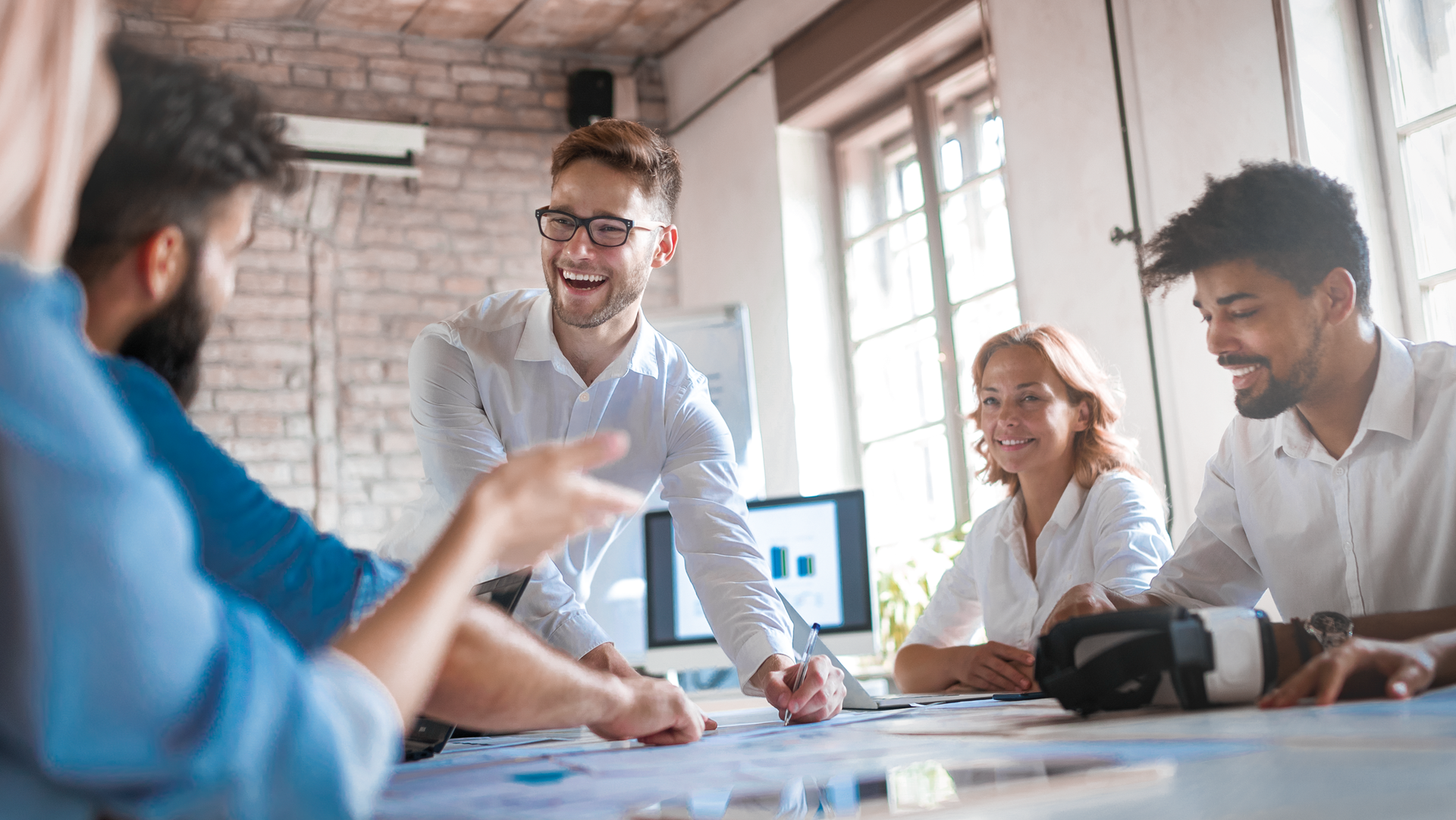
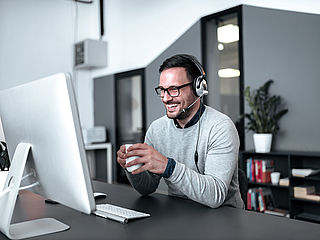
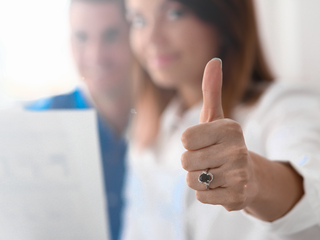
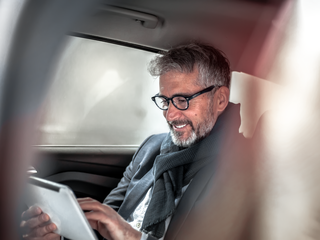
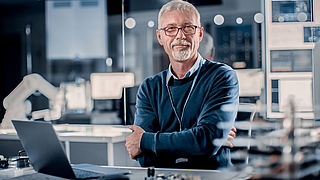
Mahr는 다국적 글로벌 기업으로서 독일뿐만 아니라 전 세계에 걸쳐 특허를 보유하고 있습니다.
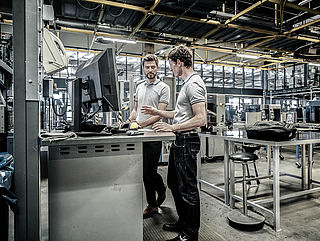
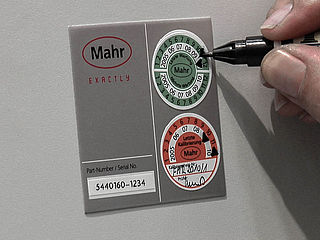
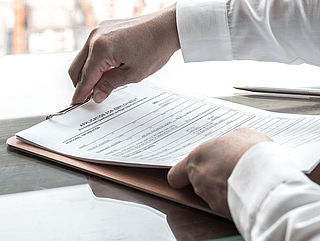
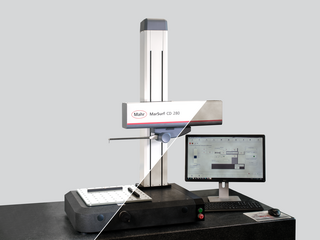
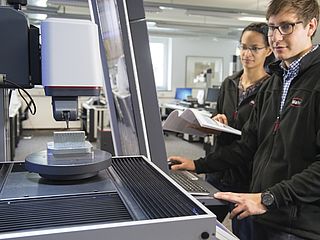
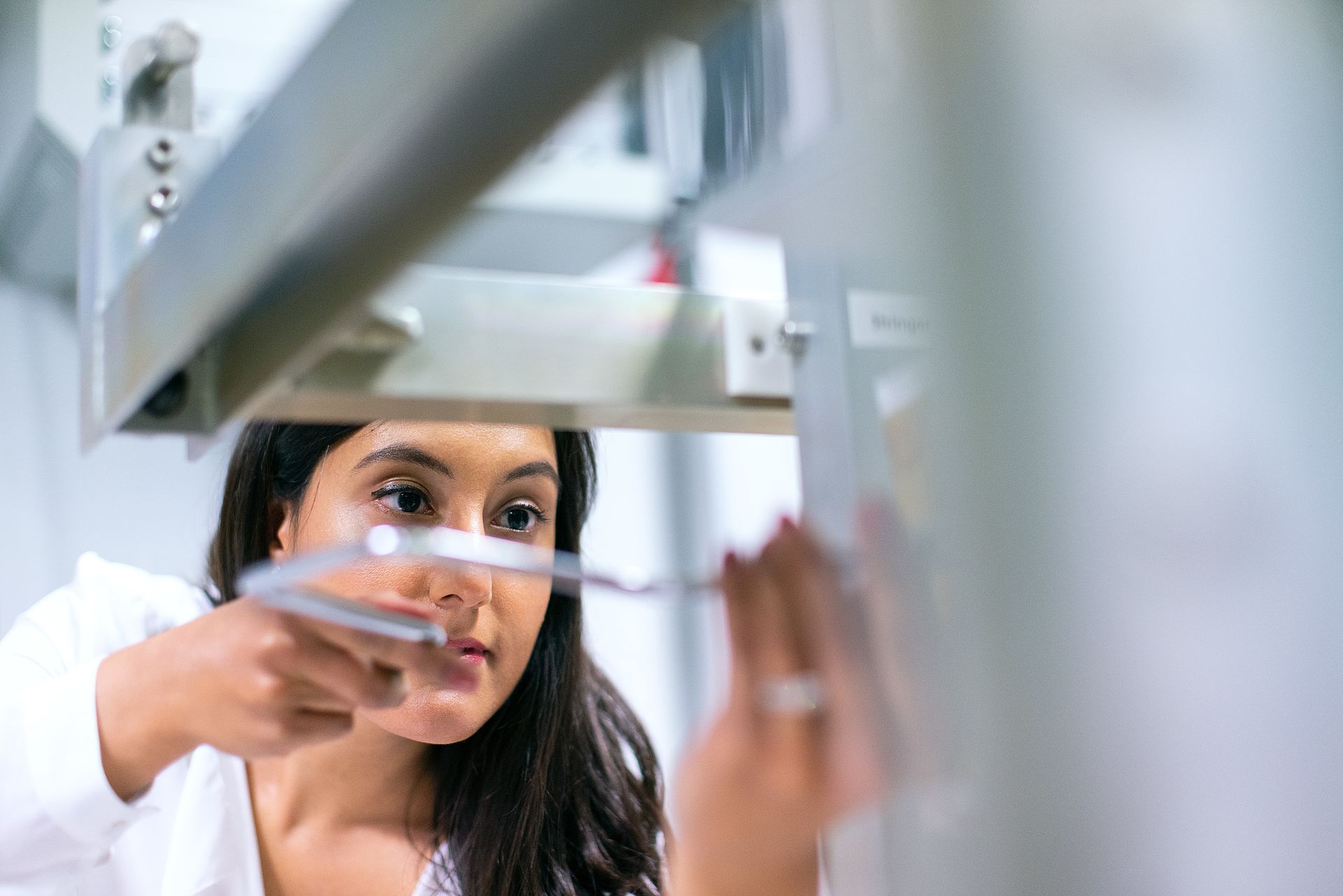
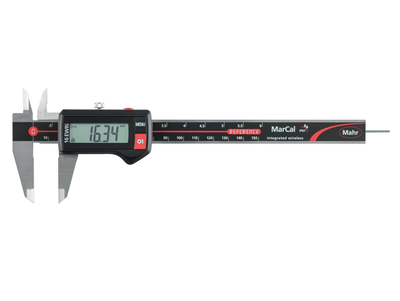
Mahr의 혁신적인 휴대용 측정 장비: 아날로그부터 디지털 모델까지 무선 데이터 전송 기능을 갖춘 캘리퍼스, 마이크로미터 나사 및 다이얼 인디케이터 #96. Mahr의 비교 측정기기 및 기준 시편
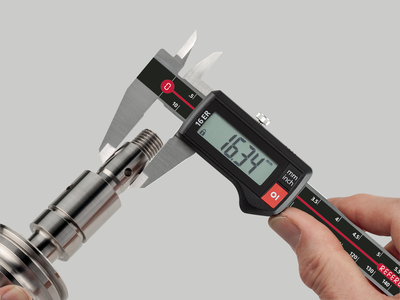
아날로그부터 디지털까지 전체 캘리퍼스 범위를 지원합니다. 쉬운 취급, 무선 및 높은 정확도. 제조 분야에서 효율적인 사용을 위해 완벽한 솔루션입니다.
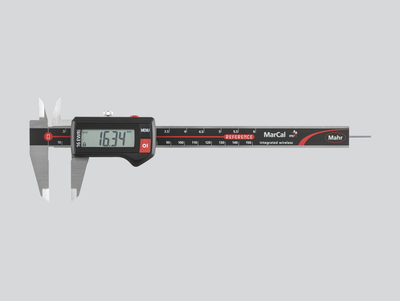
안전하고 판독하기 쉬운 디지털 디스플레이, 현대적인 디자인, 일관된 Mahr의 정확도는 디지털 캘리퍼스를 설명하는 특징입니다. 이 범위에는 모든 응용 분야를 위한 측정기기가 포함됩니다. 데이터 전송을 위한 다양한 인터페이스와 최대 IP 67의 보호 등급은 어떤 요구도 거뜬히 충족합니다.
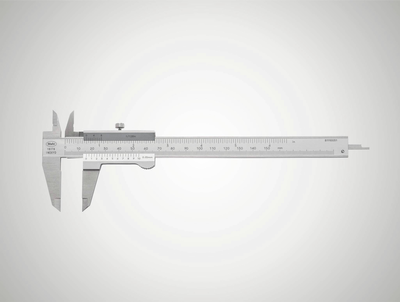
눈부심 없는 판독, 경화 금속, 스케일을 보호하고 최고의 정확도를 제공하기 위해 양각 처리된 가이드웨이. 클래식 노니우스 캘리퍼스를 포함한 Mahr의 우수한 캘리퍼스의 특징.
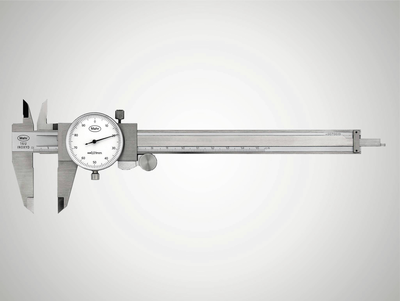
정밀도 지속을 위한 대형 고대비 다이얼 및 충격 방지 측정 툴. 빠르고 안전한 판독을 위해 확실히 믿을 수 있는 기계적 설계.
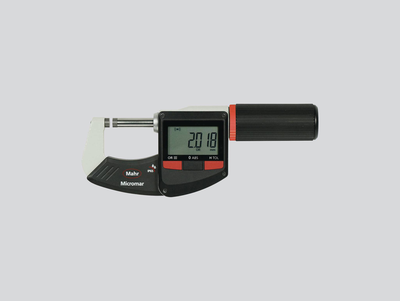
다양한 설계로 최대한의 정밀도 지원 Mahr의 마이크로미터 나사는 기존의 기계식 버전과 디지털 및 무선 버전으로 제공됩니다.
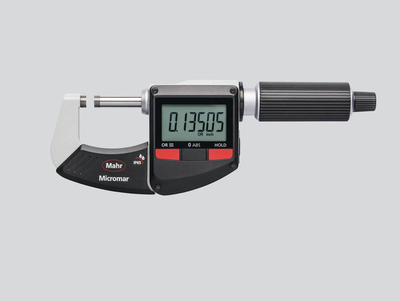
명확한 디지털 디스플레이, 현대적인 디자인, 일관된 Mahr의 정확도는 디지털 외측 마이크로미터를 설명하는 특징입니다. 이 범위에는 모든 응용 분야를 위한 측정기기가 포함됩니다. 데이터 전송을 위한 다양한 인터페이스와 최대 IP 65의 높은 보호 등급은 어떤 요구도 거뜬히 충족합니다.
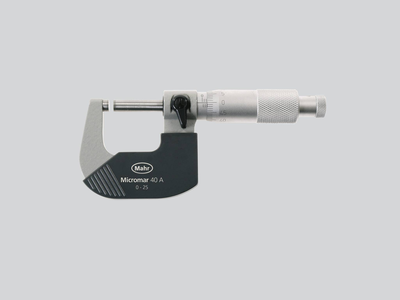
눈부심 방지 판독, 단열 플레이트 및 최대한의 정확도를 위한 정밀한 스핀들. Mahr의 우수한 캘리퍼스의 특징.
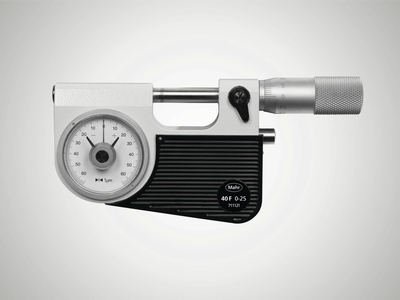
일련의 부품(샤프트, 볼트, 섕크)에 대해 믿을 수 있고 빠른 테스트에 특히 적합합니다. 다이얼 컴퍼레이터에서 한 눈에 치수 정확도를 인식하고 판독할 수 있습니다.
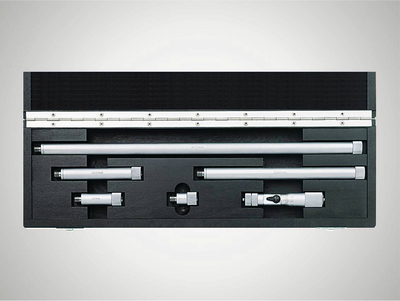
큰 지름을 측정하고 최대 2,500 mm의 거리를 테스트하는 데 적합
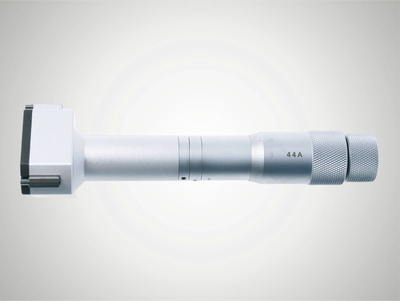
스케일 또는 디지털 디스플레이와 함께 또는 피스톨 타입 그립을 포함한 퀵 측정기기로 사용할 수 있습니다. Mahr 3점 내경 측정 장치는 자동 셀프 센터링 기능을 통해 항상 믿을 수 있는 측정 결과를 제공합니다.
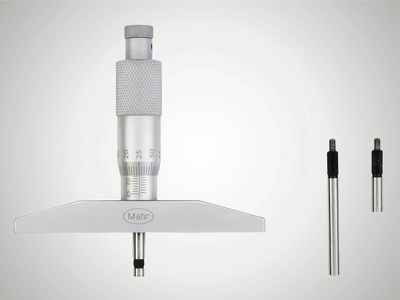
눈부심 방지 판독, 최대한의 정확도를 위한 정밀한 스핀들. Mahr의 우수한 캘리퍼스의 특징.
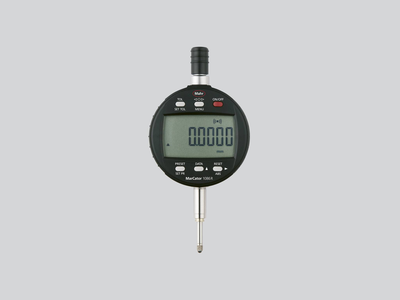
아날로그부터 디지털까지 전체 다이얼 게이지, 다이얼 컴퍼레이터 및 다이얼 테스트 인디케이터 스펙트럼. 쉬운 취급, 무선(선택적) 및 높은 정확도. 제조 분야에서 효율적인 사용을 위해 완벽한 솔루션입니다.
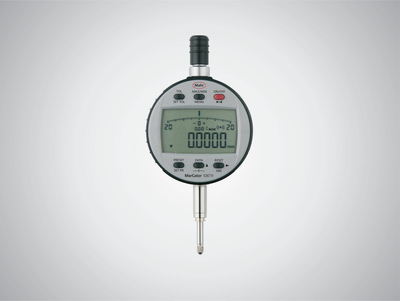
명확한 디지털 디스플레이, 튼튼한 구조, 높은 Mahr 정확도는 디지털 다이얼 게이지의 특성을 나타냅니다. 이 범위에는 모든 응용 분야를 위한 측정기기가 포함됩니다. 데이터 전송을 위한 다양한 인터페이스와 최대 IP 54의 높은 보호 등급은 어떤 요구도 거뜬히 충족합니다.
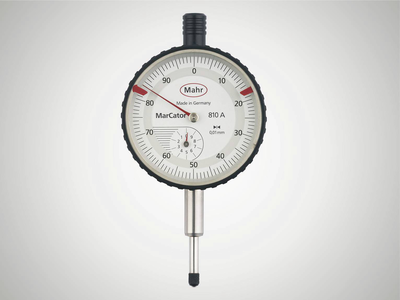
고감도 및 정확도: 측정 툴 축의 견고한 마운트, 정밀 기어 휠 및 피니언, 고정밀 마운트 측정 핀.
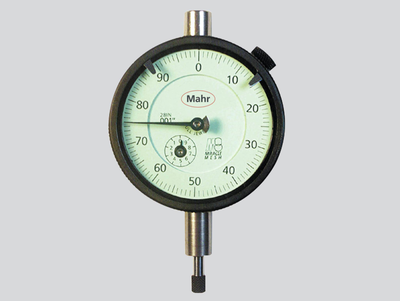
고감도 및 정확도: 측정 툴 축의 견고한 마운트, 정밀 기어 휠 및 피니언, 고정밀 마운트 측정 핀
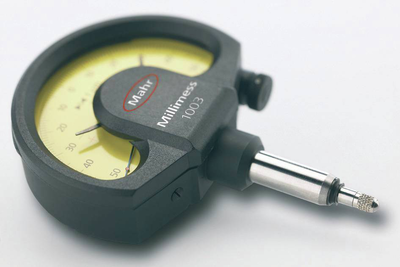
아날로그 다이얼 인디케이터에 비해 Millimess 다이얼 컴퍼레이터는 훨씬 정밀한 구성품을 갖추고 있어 보다 나은 측정 정확도와 훨씬 향상된 히스테리시스 오차를 제공합니다. 이러한 이점은 흔들림 테스트, 진직도 및 평탄도 측정, 비교 측정에서 특히 두드러지게 나타납니다.
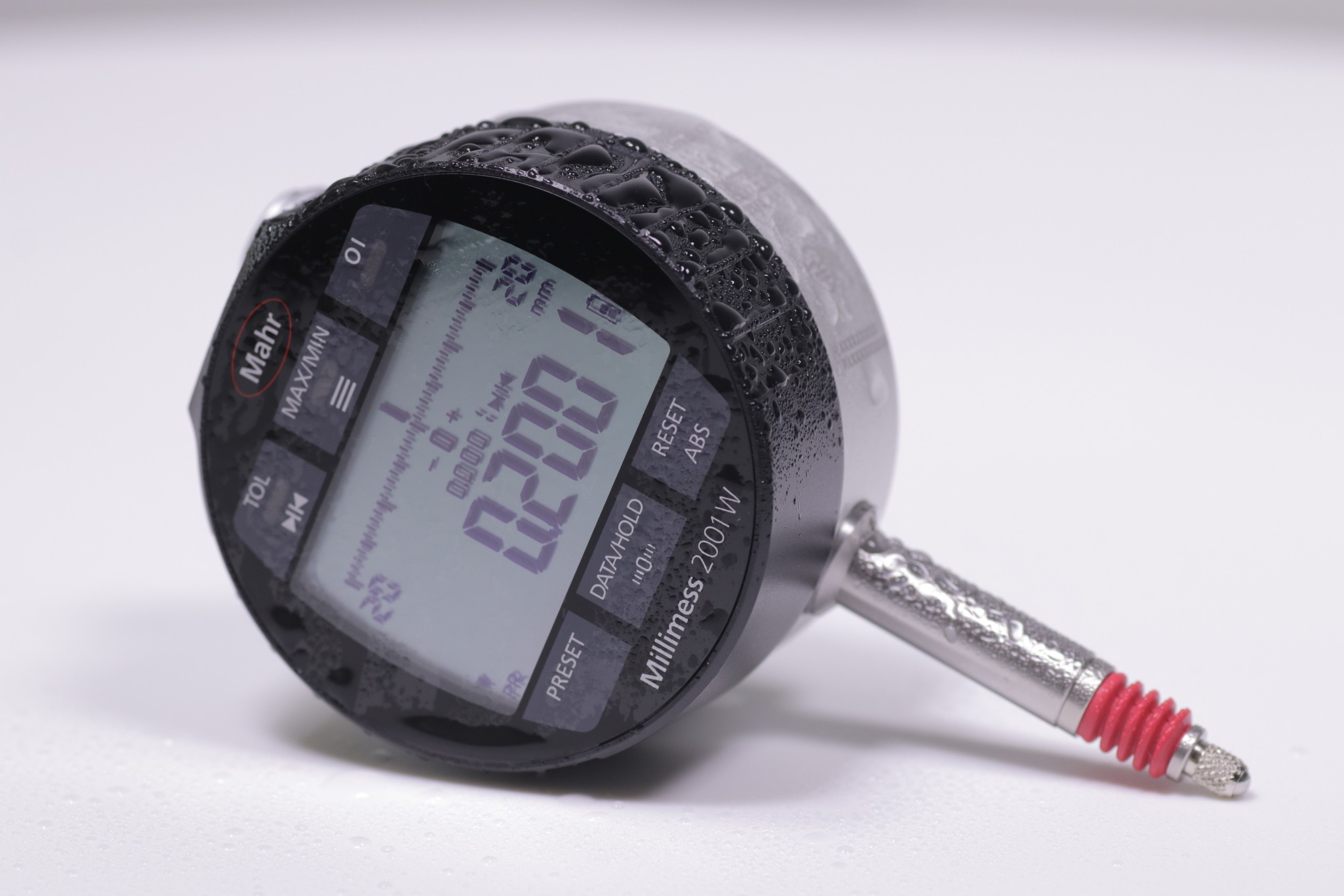
고정밀 인덕티브 Millimess 다이얼 컴퍼레이터는 최대 0.2 μm까지 디지털 증분이 가능합니다. 공차 모니터링, 최소 또는 최대 동적 측정값 기록, 숫자 및 스케일 표시 결합, 간단한 데이터 전송과 같이 사용자에게 익숙한 조작 기능 덕분에 필수불가결한 정밀 측정기기로 자리매김하였습니다.
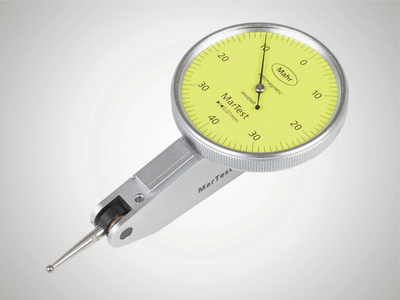
컴퓨터에 최적화된 정교한 측정 툴은 최대한의 신뢰성과 정밀도를 보장합니다. 거친 워크샵 분야에서 사용할 경우, 강화 처리된 미네랄 유리패널에 의해 디스플레이의 긁힘 또는 파손이 효과적으로 보호됩니다. 또한 씰은 액체가 침투하지 않도록 효과적인 보호 기능을 제공합니다.
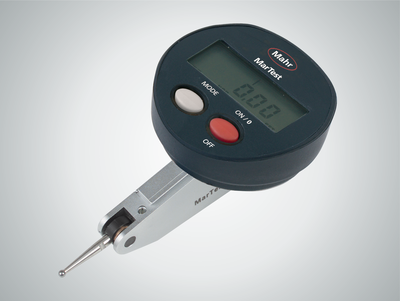
판독이 쉬운 디지털 디스플레이, 견고한 디자인, 뛰어난 Mahr 정확도는 디지털 다이얼 테스트 인디케이터의 특성을 나타냅니다.
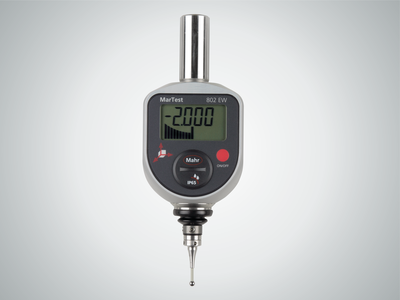
NC 기계, 가공 센터 및 침식 기계를 위한 Mahr 3D 측정 프로브는 설치 및 가동 중단 시간을 단축시켜 줍니다. 측정물 및 고정물에서 기준 가장자리를 정확히 접촉하기 위한 완벽한 방법.
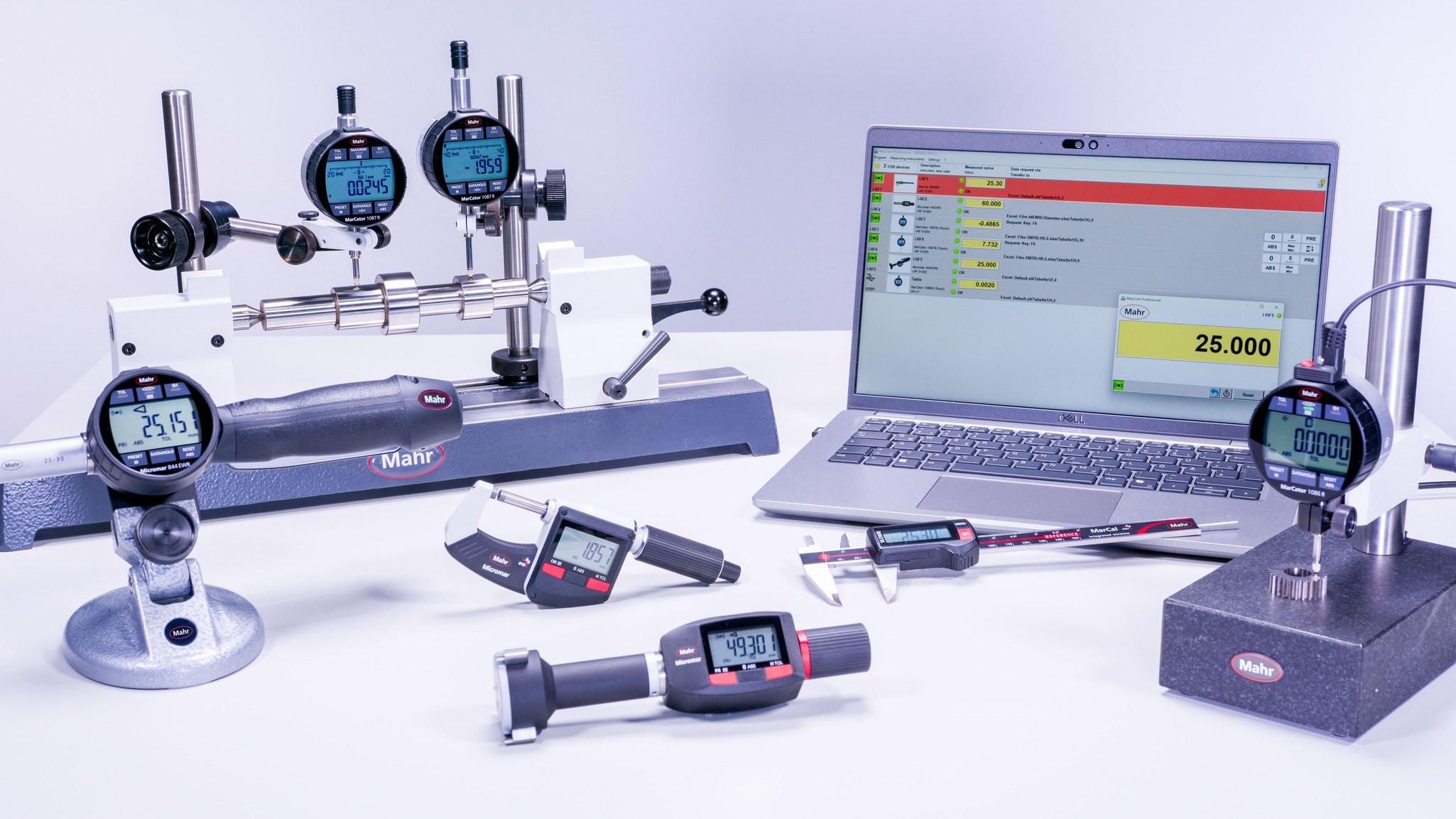
무선 데이터 통신, 외측 무선 모듈, USB, Opto RS232 또는 Digimatic: 어떤 인터페이스 표준을 사용하든 MarConnect는 늘 최상의 연결을 제공합니다.
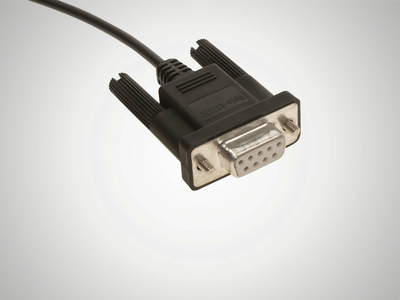
다양한 Mahr 정밀 게이지는 MarConnect 인터페이스를 통해 데이터 출력을 지원합니다. 어떤 인터페이스 표준(USB, Opto RS232, Digimatic)을 사용하든 MarConnect는 늘 최상의 연결을 제공합니다.
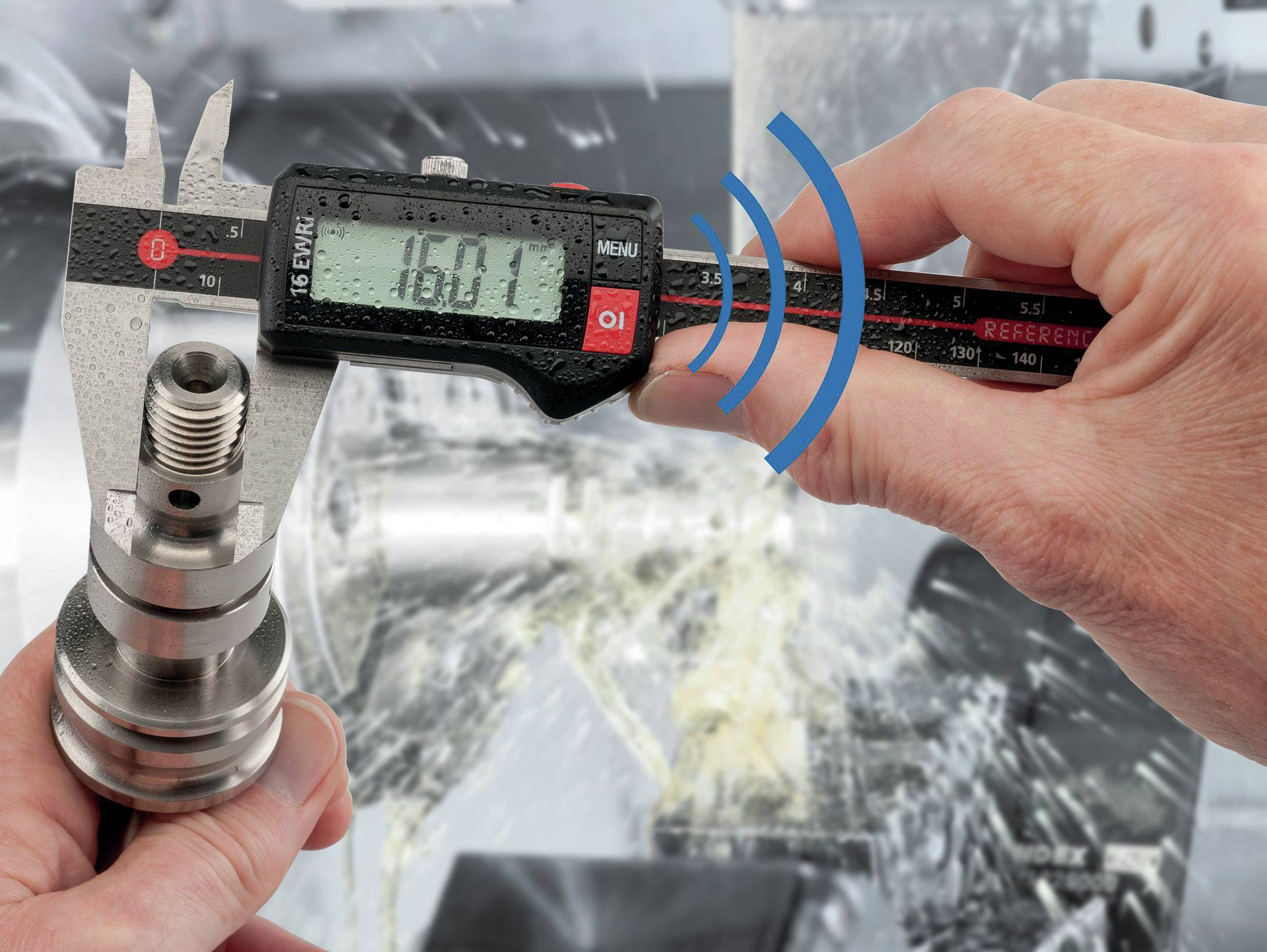
Mahr의 무선 범위는 완벽한 이동성과 함께 정밀한 측정 결과를 보장합니다. 유선 기술의 제한 없이 간편한 첨단 방식으로 측정을 수행할 수 있습니다.
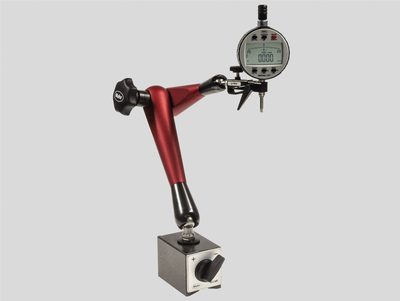
MarStand 측정 삼각대, 측정 테이블 및 원주방향 흔들림 게이지는 정밀한 측정 결과의 기초가 되는 높은 안정성을 제공합니다. 이 어셈블리는 다이얼 인디케이터, 다이얼 컴퍼레이터, 다이얼 테스트 인디케이터 측정 장치 및 증분 측정 프로브에 필요한 지지를 제공합니다.
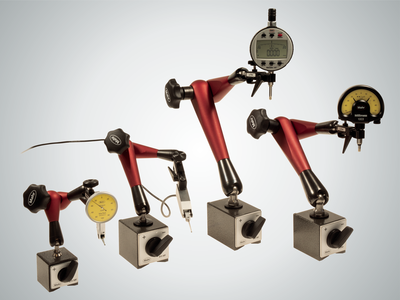
측정 삼각대는 테이블은 안정적인 설계를 바탕으로 정밀한 측정 결과를 위한 토대를 제공합니다. 이 어셈블리는 다이얼 인디케이터, 다이얼 컴퍼레이터, 다이얼 테스트 인디케이터 측정 장치 및 증분 측정 프로브에 필요한 지지를 제공합니다.
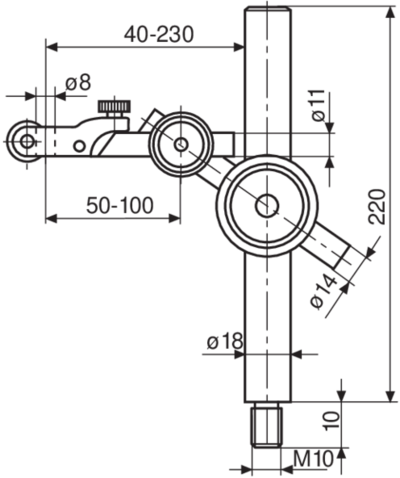
MarStand 포스트 및 서포트 어셈블리는 개별 솔루션에 사용되며, 정밀 측정 결과를 위한 기초 요소인 높은 안정성을 제공합니다. 이 어셈블리는 다이얼 인디케이터, 다이얼 컴퍼레이터, 다이얼 테스트 인디케이터 측정 장치 및 증분 측정 프로브에 필요한 지지를 제공합니다.
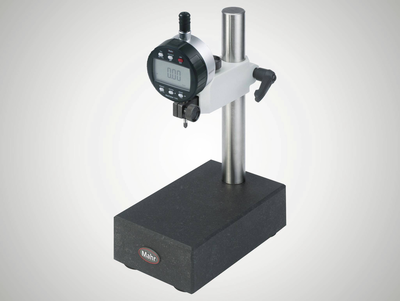
측정 테이블에는 정밀 및 레벨 측정 테이블, 안정적인 측정 컬럼 및 튼튼한 암 부품이 통합되어 있습니다. MarStand 측정 테이블은 한층 더 안정적인 설계를 바탕으로 정밀한 측정 결과를 위한 토대를 제공합니다.
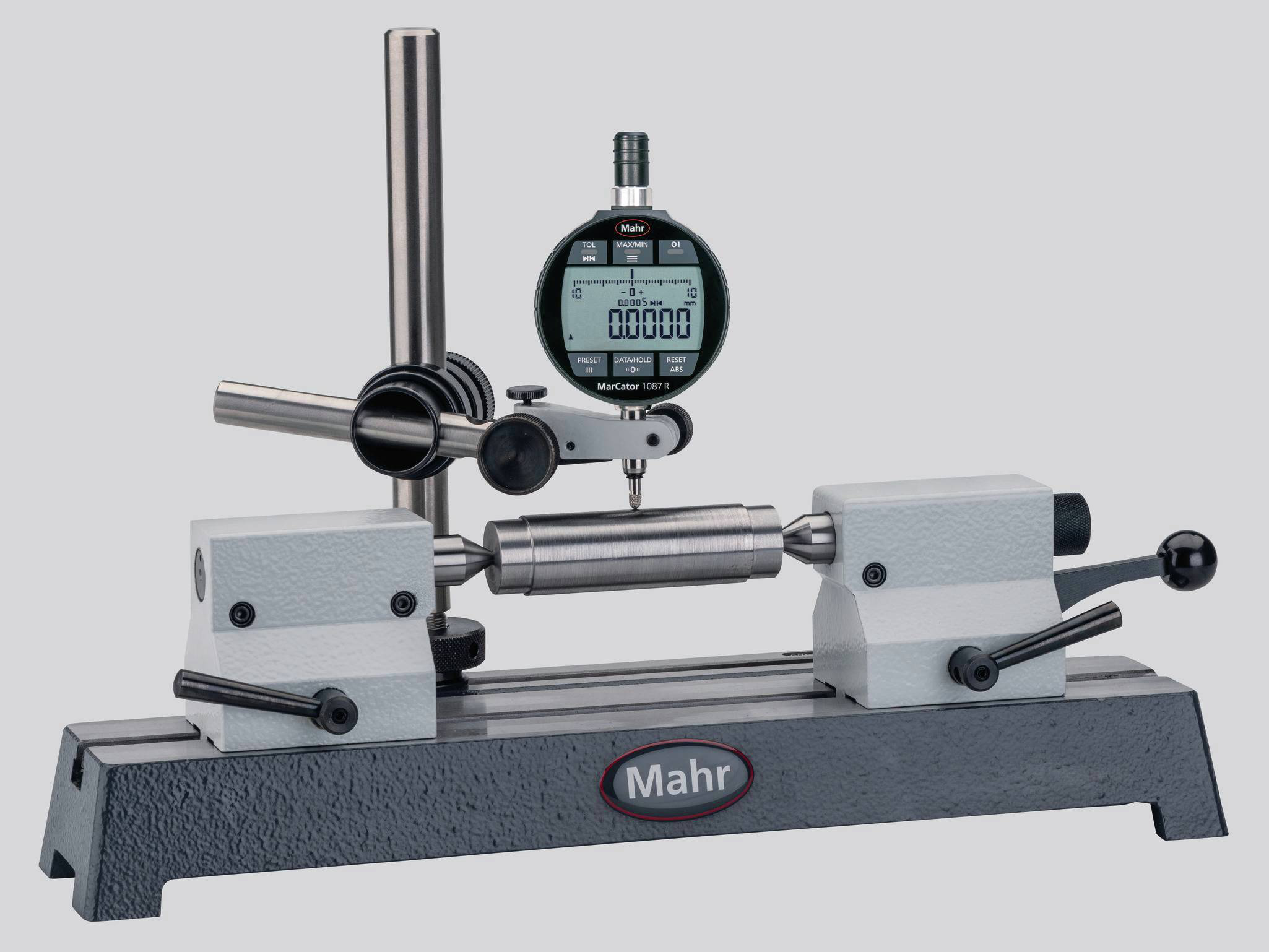
원주방향 흔들림 게이지는 생산 환경 가까이에서 샤프트의 위치 및 형상 오차를 감지하는 가장 간단한 방법입니다. 다양한 모델 덕분에 강력한 MarStand 원주방향 흔들림 게이지는 광범위한 측정물 요건 및 정밀 측정 결과를 위한 기초를 형성합니다.
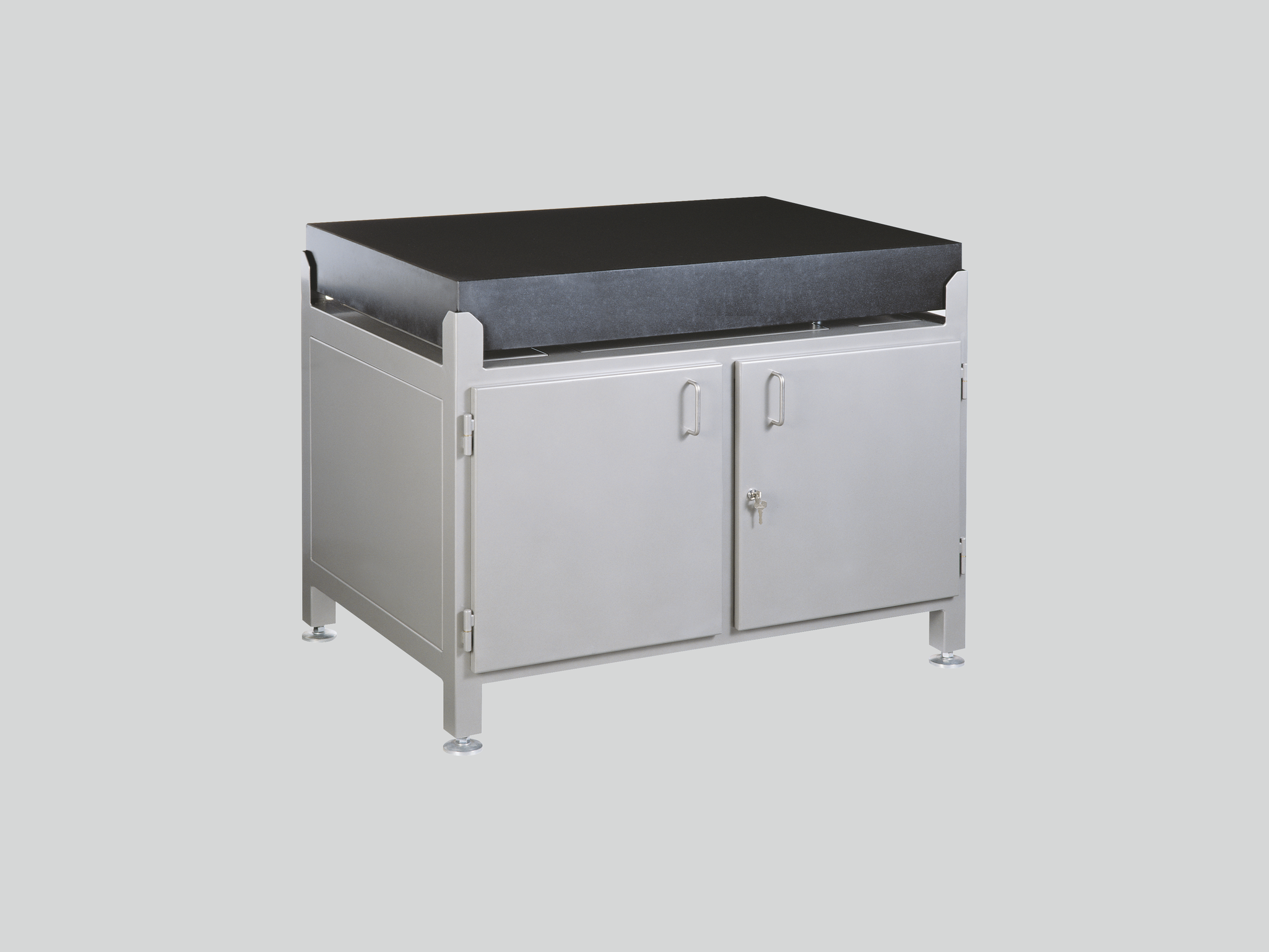
경질 화강암으로 제작된 테스트 플레이트는 높은 강도와 치수상의 안정성 덕분에 높이 측정기기에 대해 완벽한 표면이 됩니다.
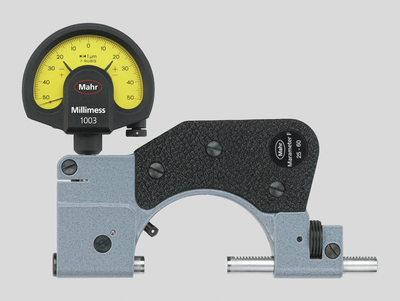
지시 게이지를 비교 게이지로 이용하면 제조 분야에서 정밀 측정을 위한 완벽한 툴을 갖출 수 있습니다. 게이지를 기준 시편으로 설정하면 편차가 줄어들고, 온도 변동이 측정 결과에 미치는 영향을 최소화할 수 있습니다.
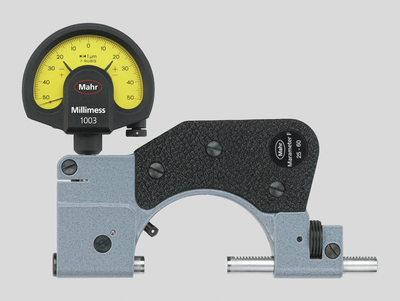
정밀 포인터 스냅 게이지는 샤프트, 볼트, 섕크와 같은 원통형 부품의 정밀 측정을 위한 완벽한 측정 툴로, 특히 일련의 부품에서 안전하고 빠른 테스트에 적합합니다. 다이얼 컴퍼레이터에서 한 눈에 치수 정확도를 식별하고 판독할 수 있습니다.
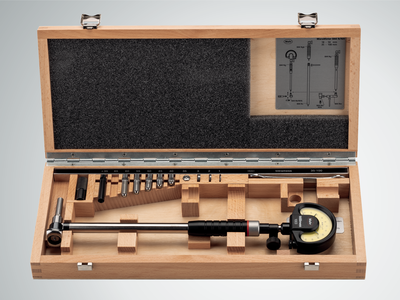
내측 측정 장치는 구멍의 지름, 진원도 및 원뿔도를 정밀하게 측정하기에 완벽한 툴입니다.
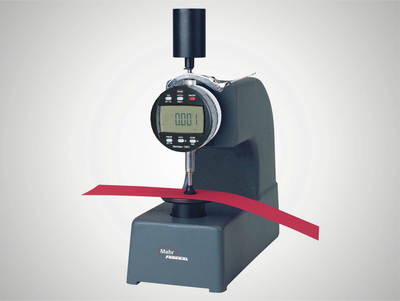
두께 게이지는 다양한 필름, 시트 및 플레이트의 신속한 측정을 위한 강력하고 단순한 제품 라인을 제공합니다.
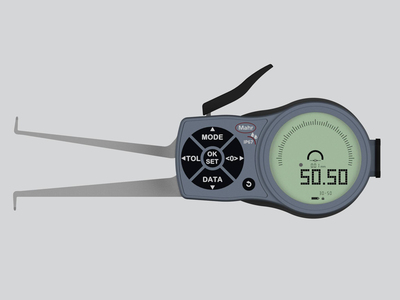
측정물의 기하구조 때문에 캘리퍼스 또는 내측 마이크로미터 나사와 같은 일반적인 측정기기를 사용할 수 없을 경우, 캘리퍼스 게이지가 완벽한 솔루션이 됩니다!
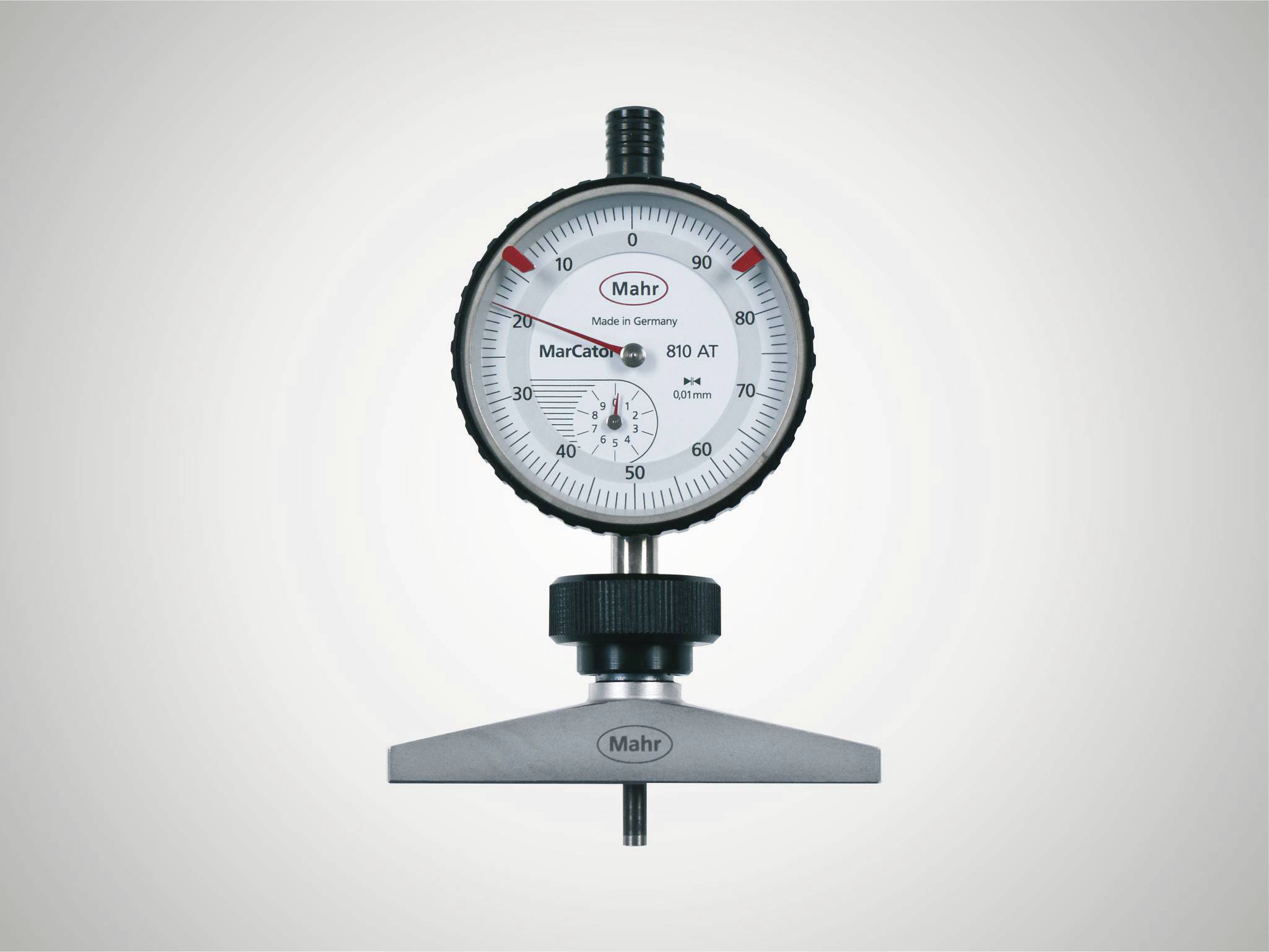
깊이 게이지는 특히 신속한 깊이 측정을 위한 강력하고 단순한 제품 라인을 제공합니다. 8mm 장착 샤프트 덕분에 측정 작업에 따라 다이얼 인디케이터, 다이얼 컴퍼레이터 및 프로브를 사용할 수 있습니다.
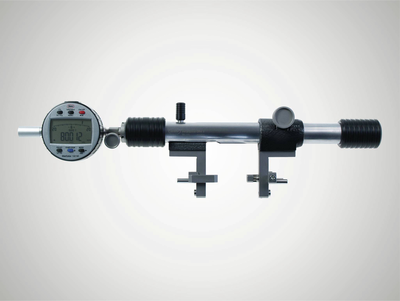
유니버셜 측정기는 기준 시편에 대한 비교 측정을 통해 온도 변동이 측정 결과에 미치는 영향을 최소화함으로써 생산 환경에서 정밀한 측정을 위한 완벽한 파트너입니다.
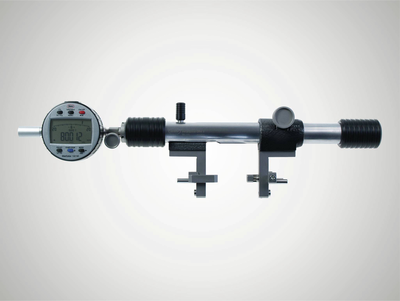
기어, 나사산, 테이퍼, 오목한 홈 등 어떤 요소든 측정 가능: Multimar 유니버셜 측정기기는 표준 측정기기로는 수행할 수 없는 거의 모든 내측 및 외측 측정에 사용하기 적합한 솔루션입니다. 기본 유닛을 비롯해 다양한 부속품을 선택할 수 있습니다.
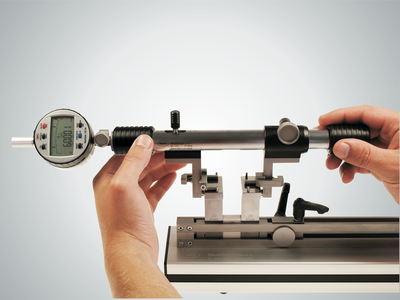
내/외경 측정기기를 정확히 조정합니다. 844 S 설정 기기를 사용하면 모든 측정 작업을 위한 완벽한 장비를 갖추게 되며, 큰 치수라도 상관이 없습니다.
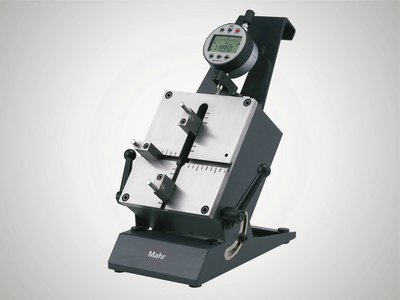
센터링 숄더, 좁은 칼라, 홈 등 분야에 관계없이 사용 가능: Multimar 36B 유니버셜 측정기기는 거의 모든 내측 및 외측 측정에 사용하기 적합한 솔루션입니다. 기본 유닛을 비롯해 다양한 부속품을 선택할 수 있습니다.
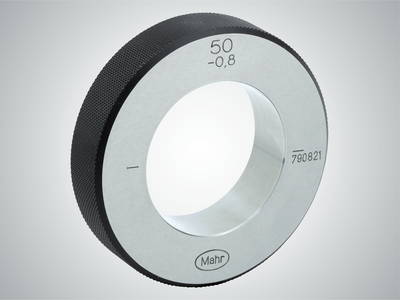
뛰어난 성능의 Mahr 설정 시편과 게이지 - 정밀한 측정 결과를 위한 기초.
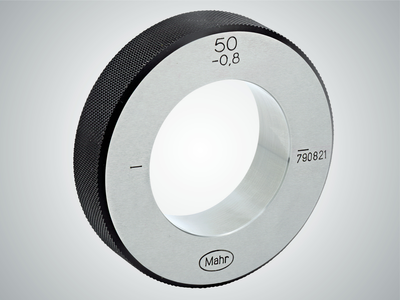
뛰어난 성능의 Mahr 설정 시편 - 정밀한 측정 결과를 위한 기초.
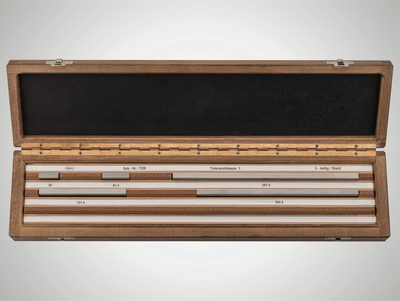
Mahr 게이지 블록을 통해 원하는 대로 우수한 품질의 기준 및 작동 시편을 갖출 수 있습니다. 4가지 공차 등급과 2가지 재료 중에서 선택하여 워크샵, 생산 또는 품질 보증의 요건을 충족할 수 있습니다.
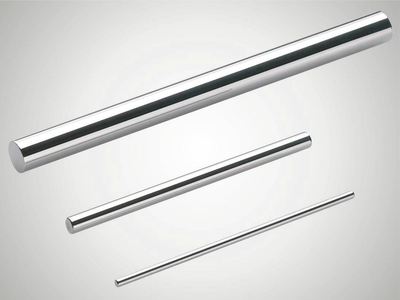
Mahr 핀 게이지는 3가지 공차 등급 및 다양한 디자인으로 제공됩니다. 워크샵, 생산 또는 품질 보증의 요건에 적합한 장치를 선택하십시오.
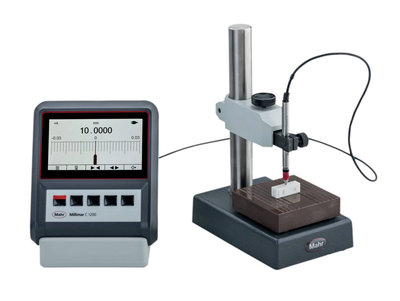
전기적 길이 측정기기의 요구 사항은 해당 적용 범위만큼이나 방대합니다. 우수한 신뢰성, 정밀도, 단순한 조작 등의 특성이 요구됩니다.
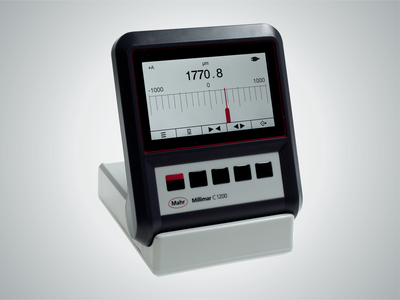
길이 측정기의 요구 사항은 해당 적용 범위만큼이나 방대합니다. 우수한 신뢰성, 정밀도, 단순한 조작 등의 특성이 요구됩니다. Millimar 컴팩트 및 컬럼 측정기기는 이러한 요구 사항을 충족합니다.
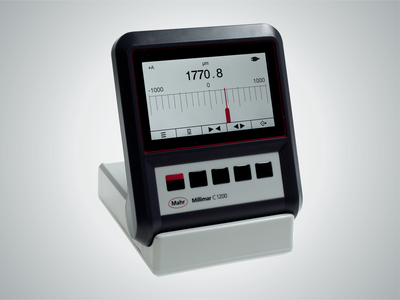
Millimar 길이 측정기기는 컴팩트하고 견고하며 사용이 간편합니다. 생산 영역과 측정실에서 간편하게 측정 작업을 수행할 수 있도록 지원하는 다목적 평가 및 지시 기기입니다.
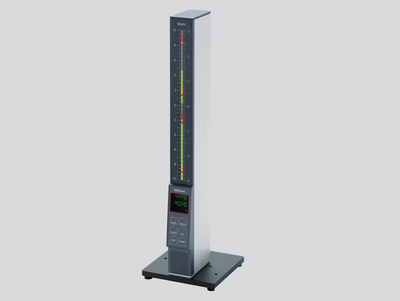
측정 결과가 101가지 3색 LED에 표시되고 먼 거리에서도 손쉽게 판독할 수 있습니다. 프로그래밍한 경고 및 공차 한계를 넘을 경우, 세그먼트가 녹색에서 노란색 또는 빨간색으로 변합니다.
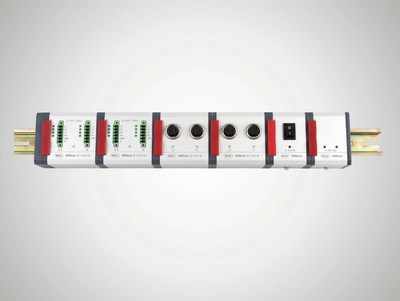
모듈과 소프트웨어의 다양한 조합은 전보다 훨씬 더 개별적인 특성에 맞춰 작업 환경과 툴을 설계할 수 있는 기회를 선사합니다.
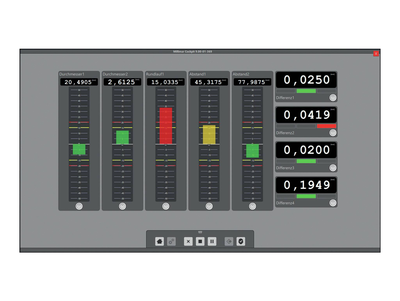
Smart and universally applicable software for complex measurement tasks in the manufacturing sector
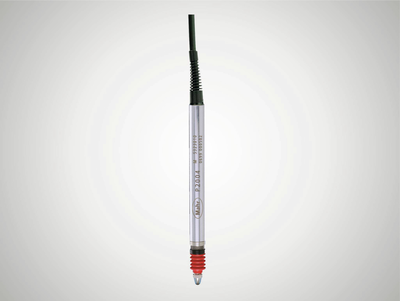
Millimar 트랜스듀서는 측정 체인에서 가장 중요한 구성품입니다. 이들 특성이 전체 측정의 품질을 결정합니다. 응용 분야에 따라 다양한 기술을 사용할 수 있습니다. 예를 들어, Millimar 인덕티브 측정 프로브의 경우: 이러한 제품은 견고하고, 다양한 용도로 활용할 수 있으며, 저렴한 가격대로 판매됩니다.
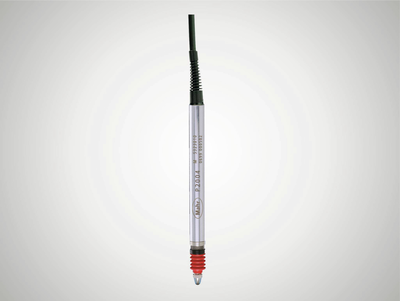
두께 측정, 원주방향 흔들림 또는 동심률 등 어떤 작업이든 상관 없습니다. 인덕티브 프로브를 사용해 형상, 지지 또는 원주방향 흔들림 편차에 관계없이 측정값과 편차를 기록할 수 있습니다. 넓은 선형 범위, 상대적으로 간섭에 덜 민감한 특성은 뛰어난 장점으로 여겨집니다. 이 프로브는 주로 생산 환경에서 비교 측정에 사용되지만, 센서의 특정 작업은 다양할 수 있습니다.
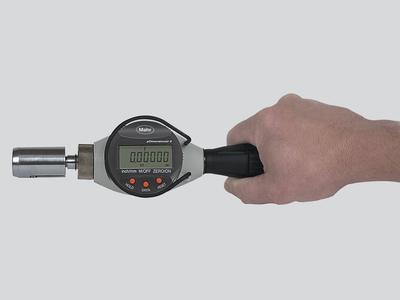
공압 길이 측정기기는 높은 정확도와 장기의 안정성 특성을 갖추고 있습니다. 측정 노즐을 사용한 비접촉식 측정 때문에 측정물이 손상될 염려가 없습니다. 측정물이 깨끗하지 않고 오일이 묻었거나 윤활 처리 또는 코팅 처리된 경우도 상관 없습니다.
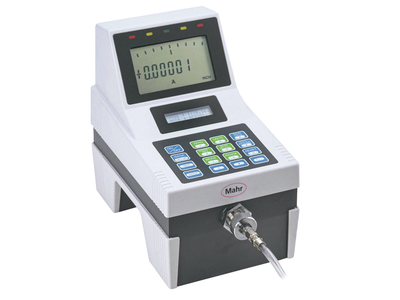
Millimar 길이 측정기기는 컴팩트하고 견고하며 사용이 간편합니다. 생산 영역에서 간편하게 측정 작업을 수행할 수 있도록 지원하는 다목적 디스플레이 및 평가 장치입니다.
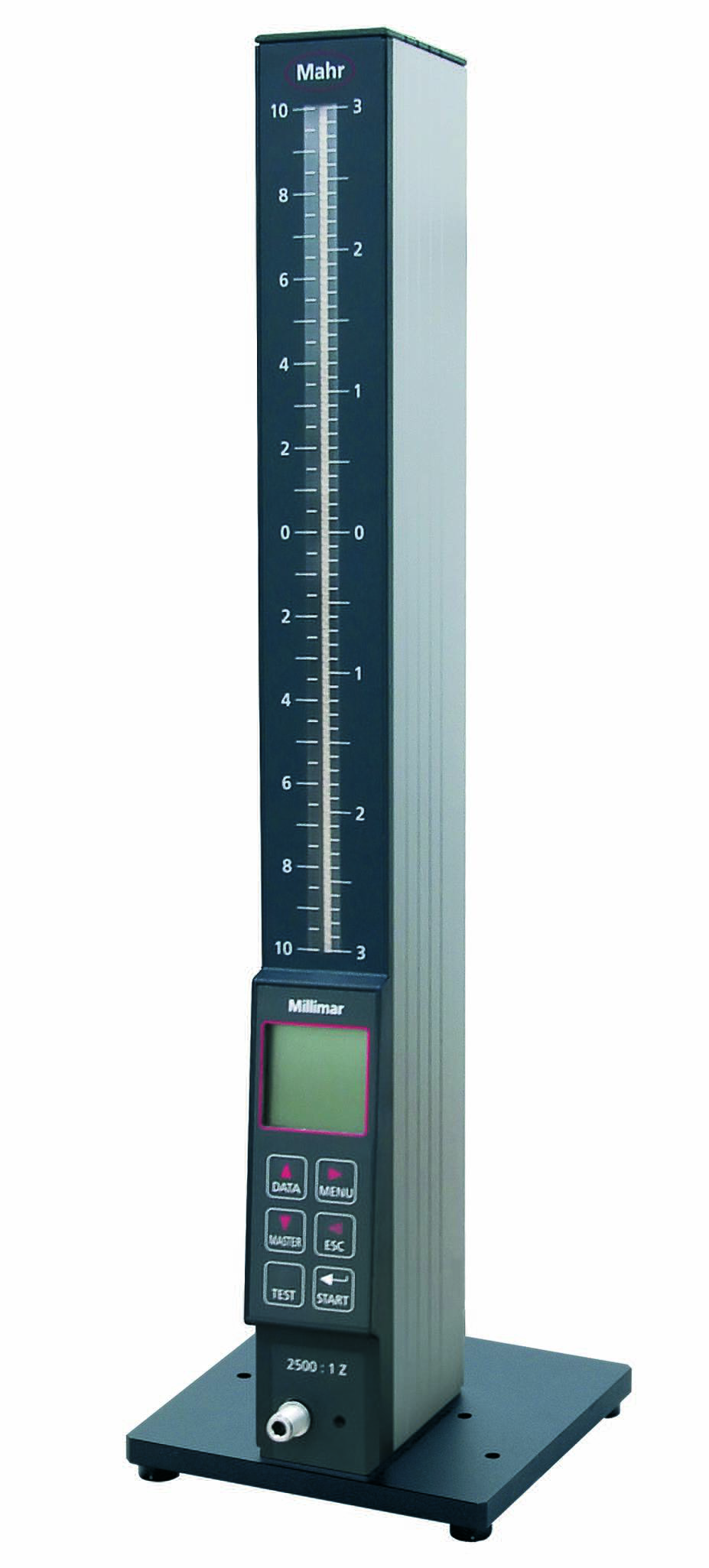
측정 결과가 101가지 3색 LED에 표시되고 먼 거리에서도 손쉽게 판독할 수 있습니다. 프로그래밍한 경고 및 공차 한계를 넘을 경우, 세그먼트가 녹색에서 노란색 또는 빨간색으로 변합니다.
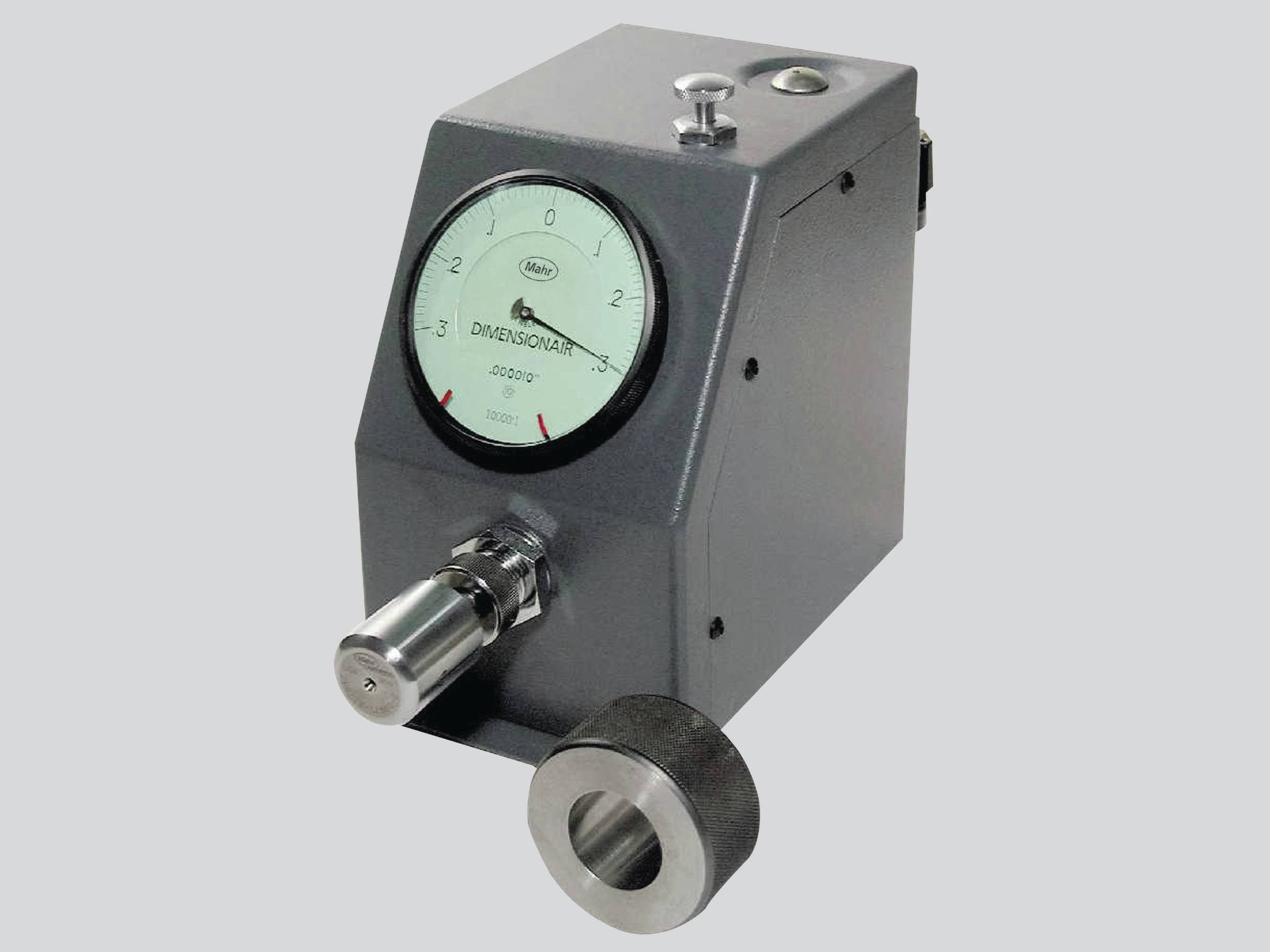
Millimar 공압 측정 장치는 빠르고 정확하게 치수 편차를 기록합니다. 수년 동안 산업 생산 현장과 측정실에서 그 성능이 검증되었습니다.
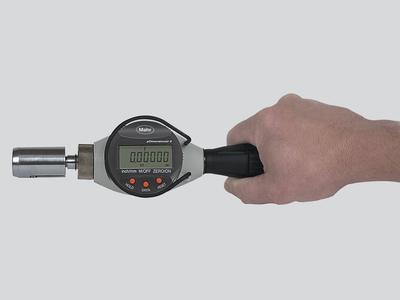
이동 중 측정 및 평가
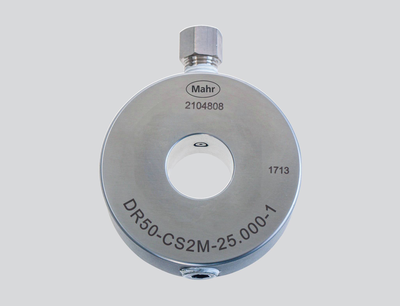
비접촉식 측정, 공압 측정 링 사용, 측정물에 대한 손상 없음.
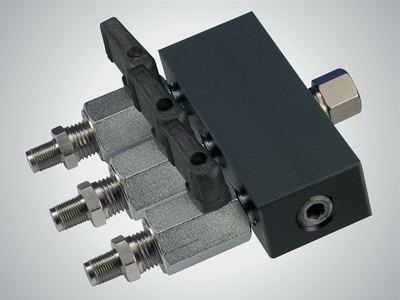
에어 측정 기술을 위한 부속품을 사용해 측정 작업에 맞게 측정 스테이션을 조정할 수 있습니다.
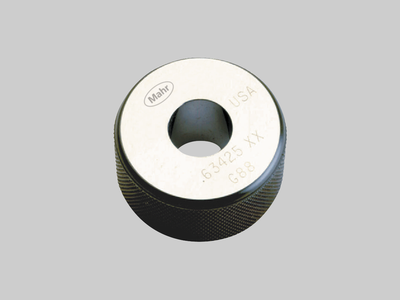
뛰어난 성능의 Mahr 설정 시편 - 정밀한 측정 결과를 위한 기초
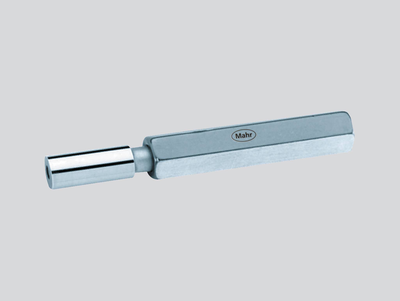
공압 측정기기의 설정(노즐 링 게이지), 꼼꼼한 경화, 숙성, 연삭, 래핑.
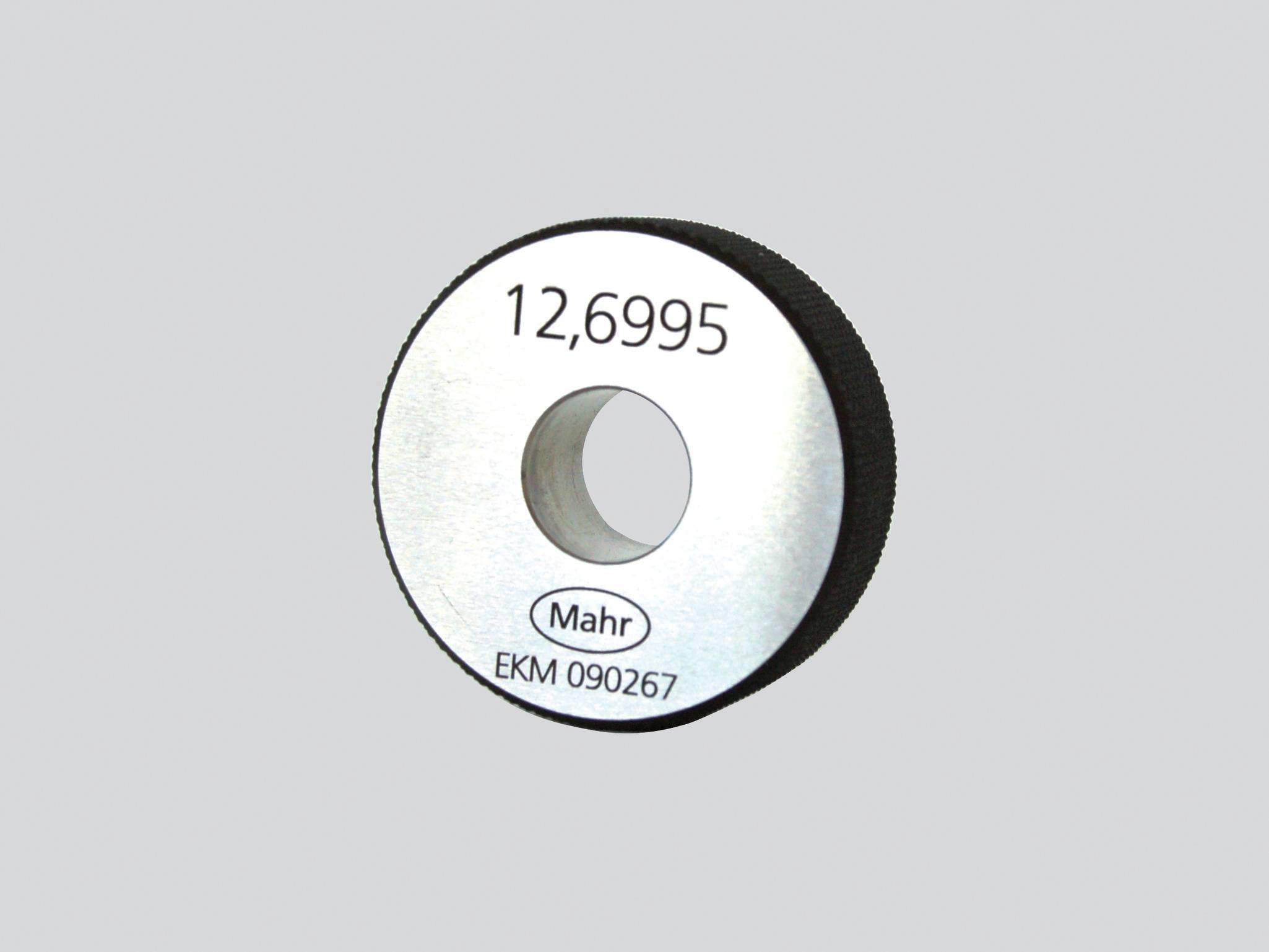
공압 측정기기의 설정(노즐 플러그 게이지), 꼼꼼한 경화, 숙성, 연삭, 래핑.
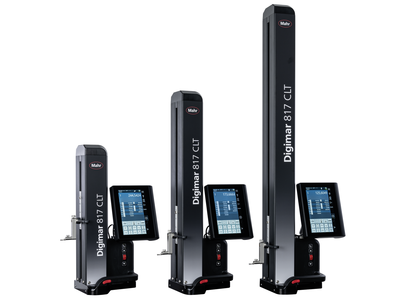
수준 높은 측정을 원하십니까? Digimar를 이용해 보십시오!
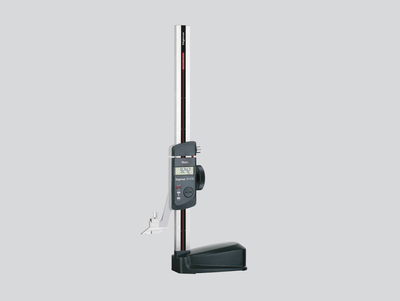
워크샵에서 측정물의 스크라이빙 및 마킹에 사용됩니다. 간편한 높이 및 거리 측정.
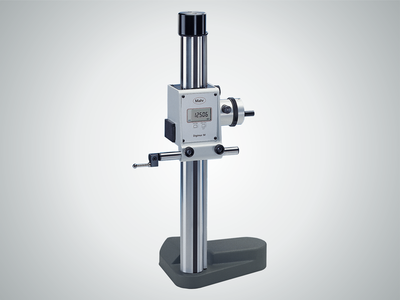
구멍, 표면 및 가장자리 사이의 간편한 높이 및 거리 측정. 추가 부속품을 이용해 측정물의 스크라이빙 및 마킹에 사용하기 적합합니다.

Touch operation, ergonomic handling and a wide range of evaluation options: This is what the Digimar 817 CLT height measuring device stands for.
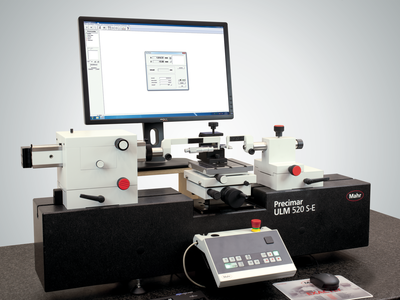
정밀 길이 측정기는 절대 및 상대 측정을 위한 고정밀 치수 계측을 상징합니다.
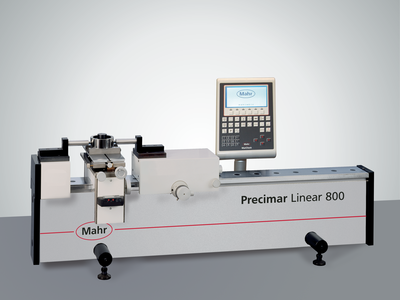
작업 현장을 위해 사용하기 쉬운 범용 길이 측정 및 설정 장치

작업 현장을 위해 사용하기 쉬운 범용 길이 측정 및 설정 장치
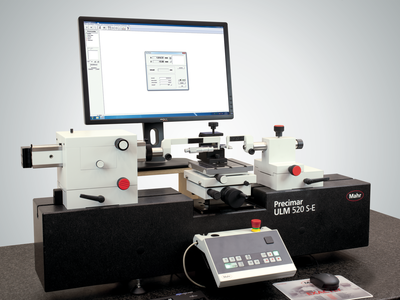
단순 게이지 블록 테스트 스탠드에서부터 완전 자동식 다이얼 게이지 테스트 스탠드, ULM 장치, 초정밀 및 부분 자동식 CiM 유니버셜 측정기의 광범위한 제품 덕분에 Mahr는 언제나 생산, 측정실 및 교정 실험실에 실용적인 솔루션을 제공합니다. 즉: 최대 정밀성과 지극히 효율적인 측정 프로세스의 결합입니다.
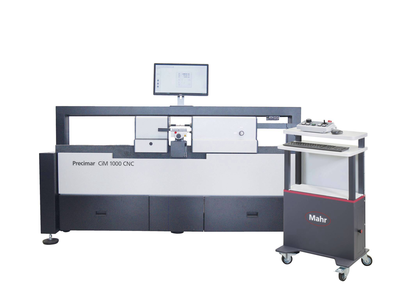
클래식 ULM 또는 모터 구동식 PLM이나 CiM 기기든 상관 없습니다. Mahr 범용 길이 측정기기는 불확도를 최소한으로 낮추면서 간편하면서 빠르고 믿을 수 있는 측정을 가능케 합니다.
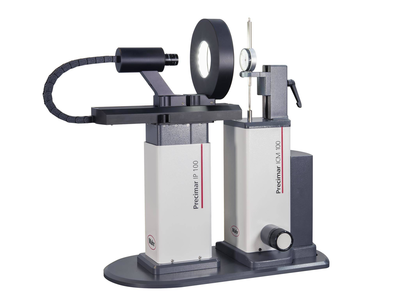
반자동 및 완전 자동식 다이얼 인디케이터 테스트, 다이얼 테스트 인디케이터 측정 장비, 다이얼 컴퍼레이터 및 프로브 - 효율 및 정밀도.
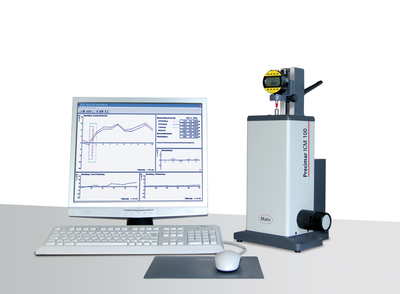
반자동 및 완전 자동식 다이얼 인디케이터 테스트, 다이얼 테스트 인디케이터 측정 장비, 다이얼 컴퍼레이터 및 프로브 - 효율 및 정밀도.
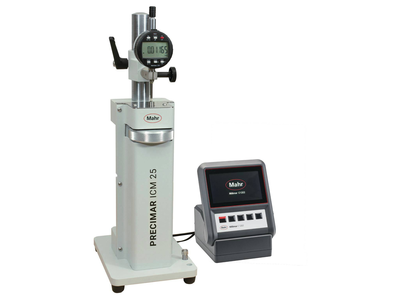
Manual testing of dial gages, dial test indicators and comparators - easy and precise
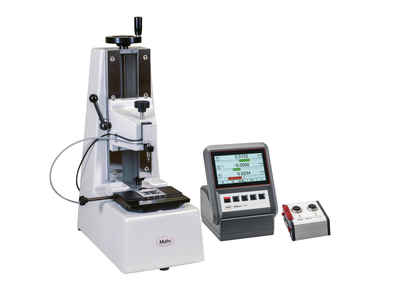
믿을 수 있는 성능을 갖춘 Mahr 게이지 블록 컴퍼레이터 - 정밀한 시편 테스트를 위한 기초
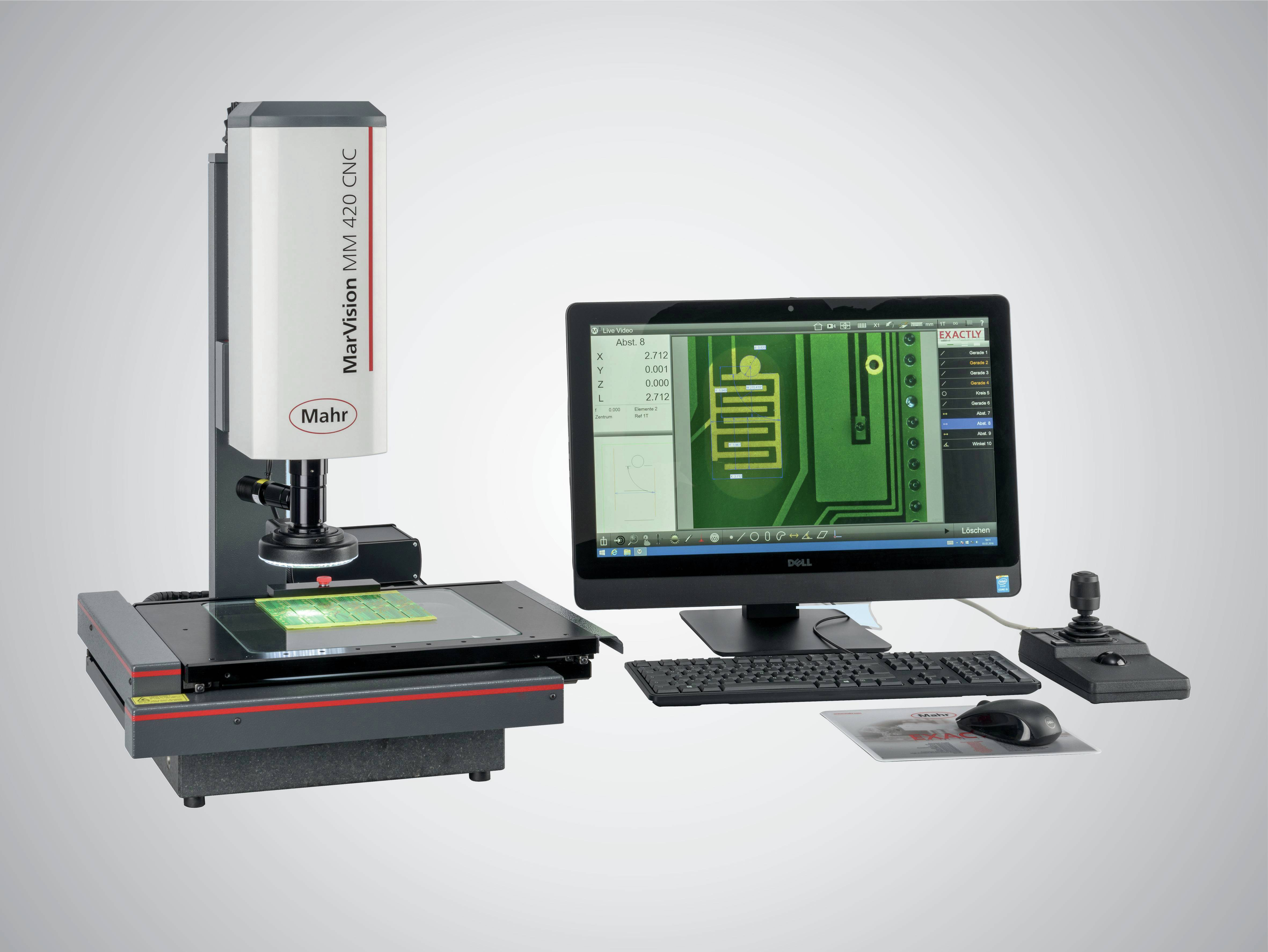
현미경은 거리, 반지름, 각도의 빠른 검사를 위해 거의 모든 산업에서 사용됩니다. 실험실 또는 생산 현장 가까이에서 사용됩니다.
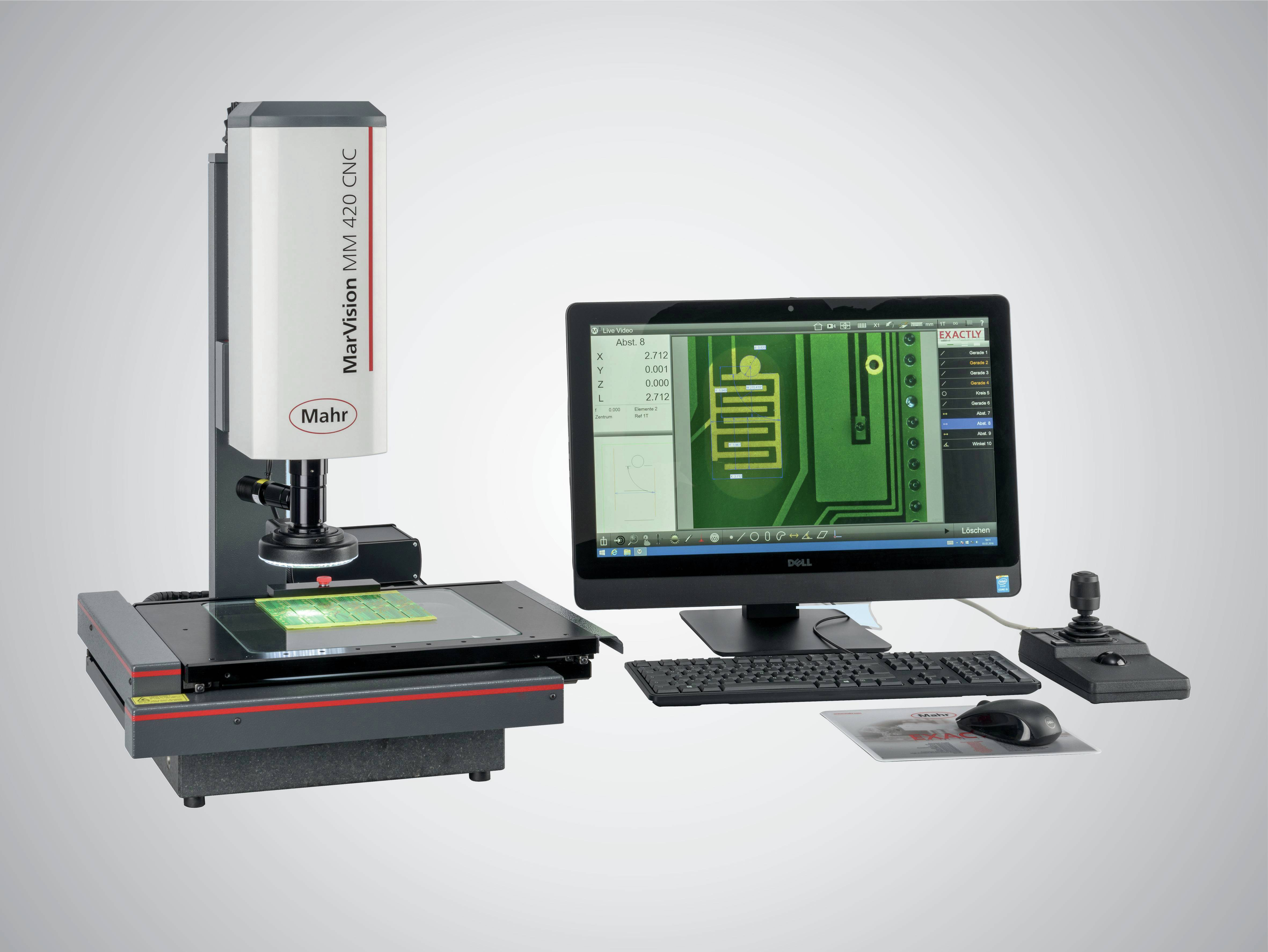
현미경은 거리, 반지름, 각도의 빠른 검사를 위해 거의 모든 산업에서 사용됩니다. 실험실 또는 생산 현장 가까이에서 사용됩니다.
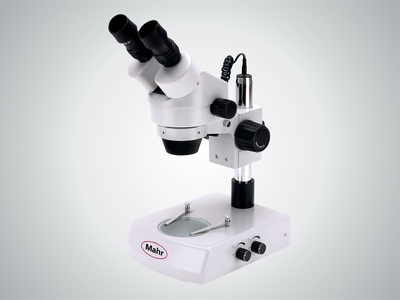
밝고 선명한 삼차원 이미지를 위해 우수한 품질의 렌즈를 탑재한 스테레오 줌 현미경. 추가적인 디지털 카메라 사용을 포함한 양안 또는 3안 현미경.
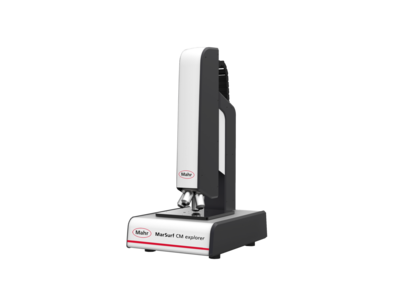
산업 및 연구를 위한 표면 측정기
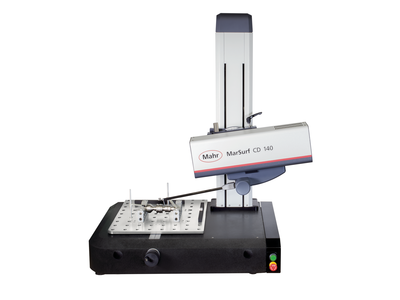
엄격한 공차를 가진 구조적 기능 표면에는 최소한의 시간으로 짧은 영역에서 측정물 또는 물체의 토포그래피를 기록하는 고정밀 측정 시스템이 필요합니다.
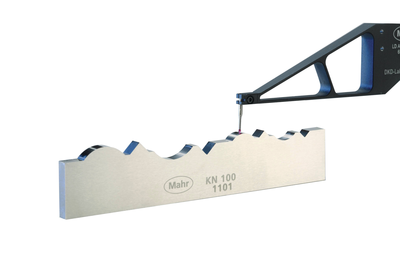
형상 측정 기술은 거친 형상 편차를 결정하는 데 사용됩니다.
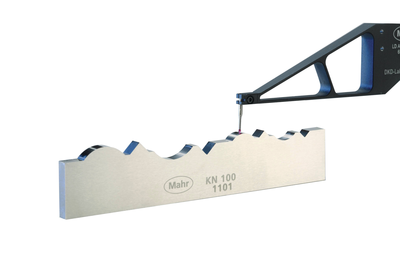
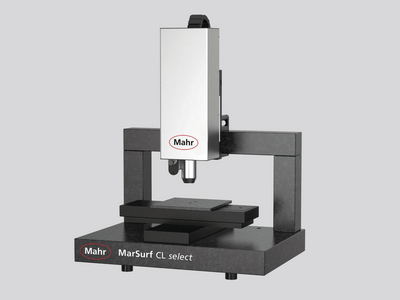
광학 측정기기로 정밀하게 형상 측정
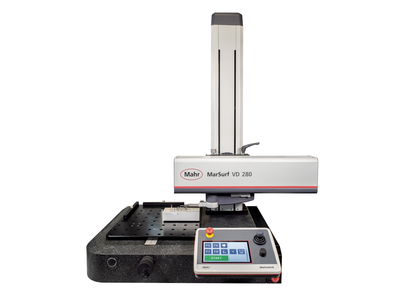
형상 및 거칠기 측정 결합: 다목적 전문 솔루션
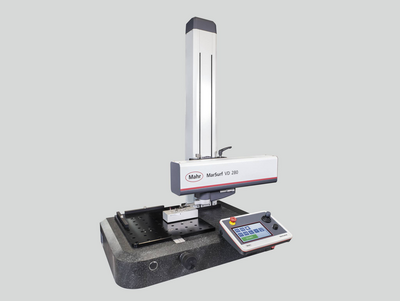
형상 및 거칠기 측정 결합: 다목적 전문 솔루션
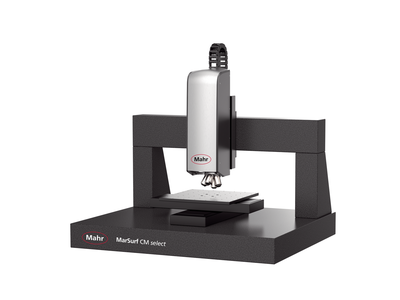
ISO 25178 / ISO 4287에 따른 2D/3D 형상 측정 및 거칠기 측정
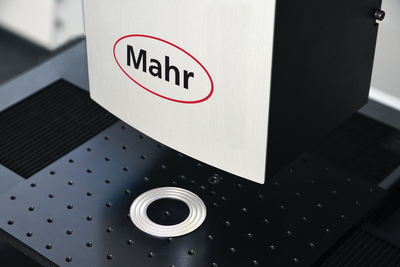
산업 및 연구를 위한 3D 표면 측정기
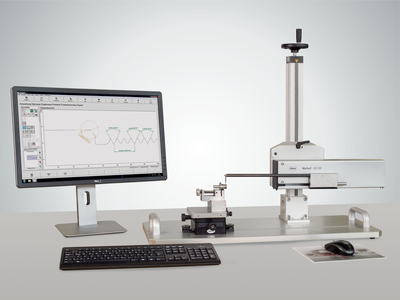
휴대용 측정 장치로 모든 분야를 측정합니다!
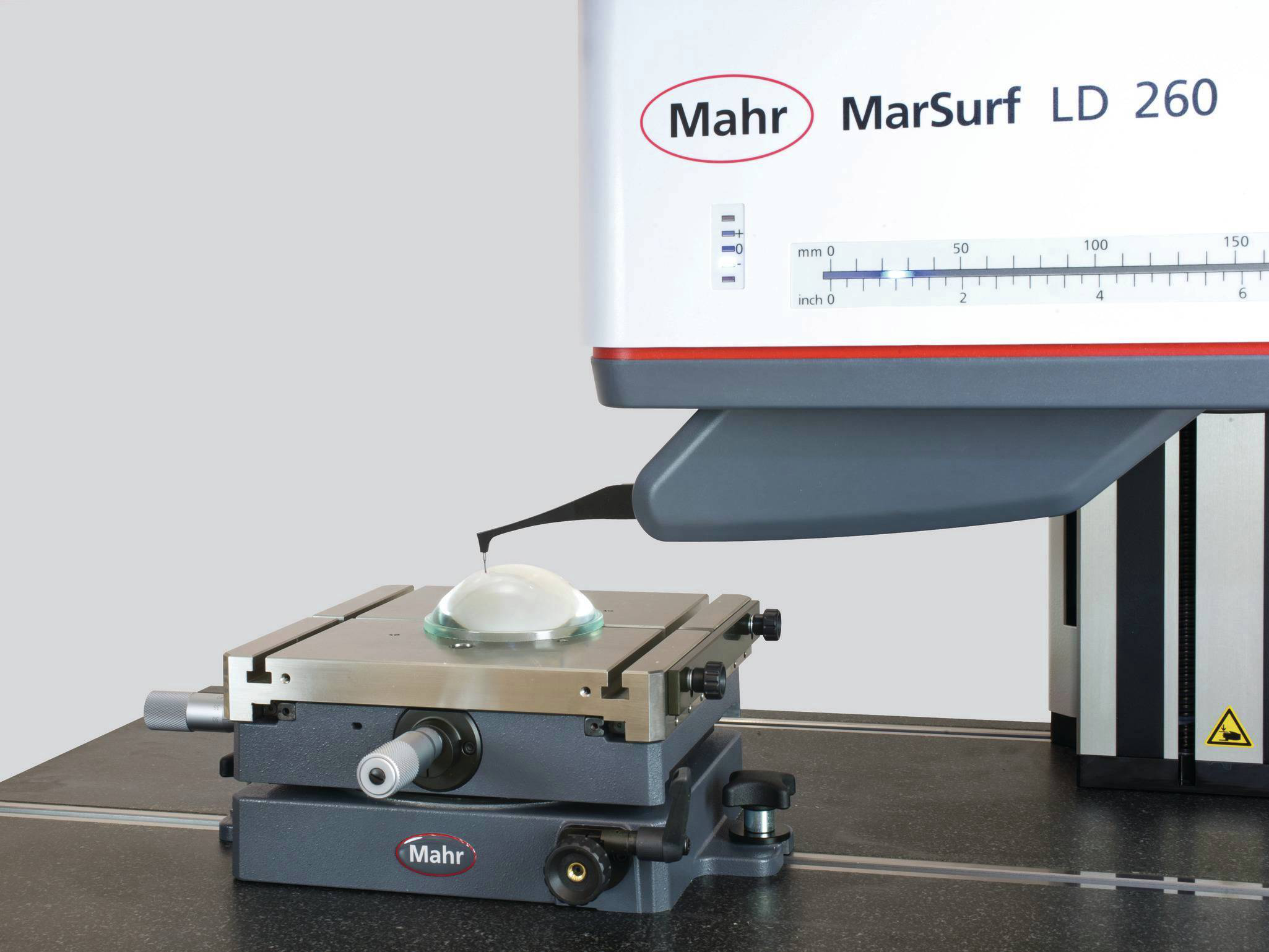
고정밀 렌즈 측정을 위한 측정 스테이션
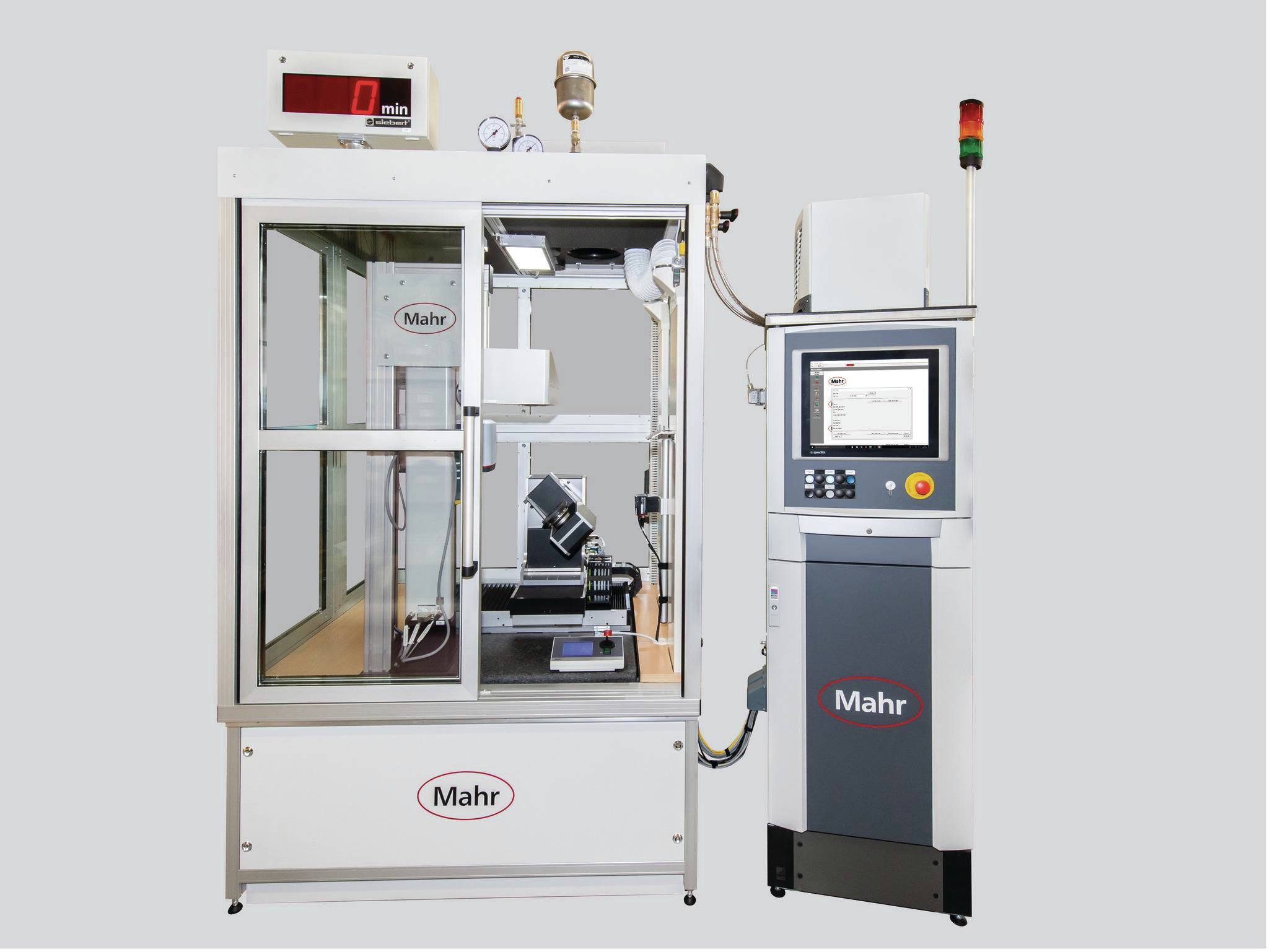
표준 솔루션으로 더 이상 충분하지 않을 경우: 개별 커스터마이즈 솔루션
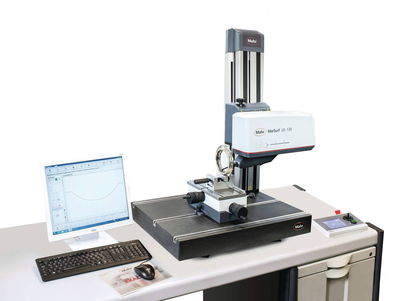
엄격한 공차를 가진 구조적 기능 표면에는 최소한의 시간으로 짧은 영역에서 측정물 또는 물체의 토포그래피를 기록하는 고정밀 측정 시스템이 필요합니다.
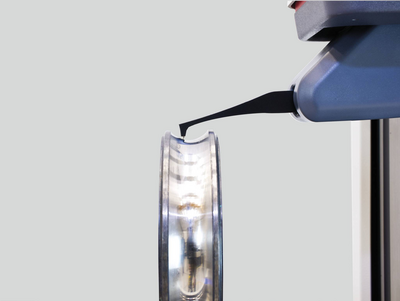
측정실 및 실험실에서 다목적성 및 강력한 기능
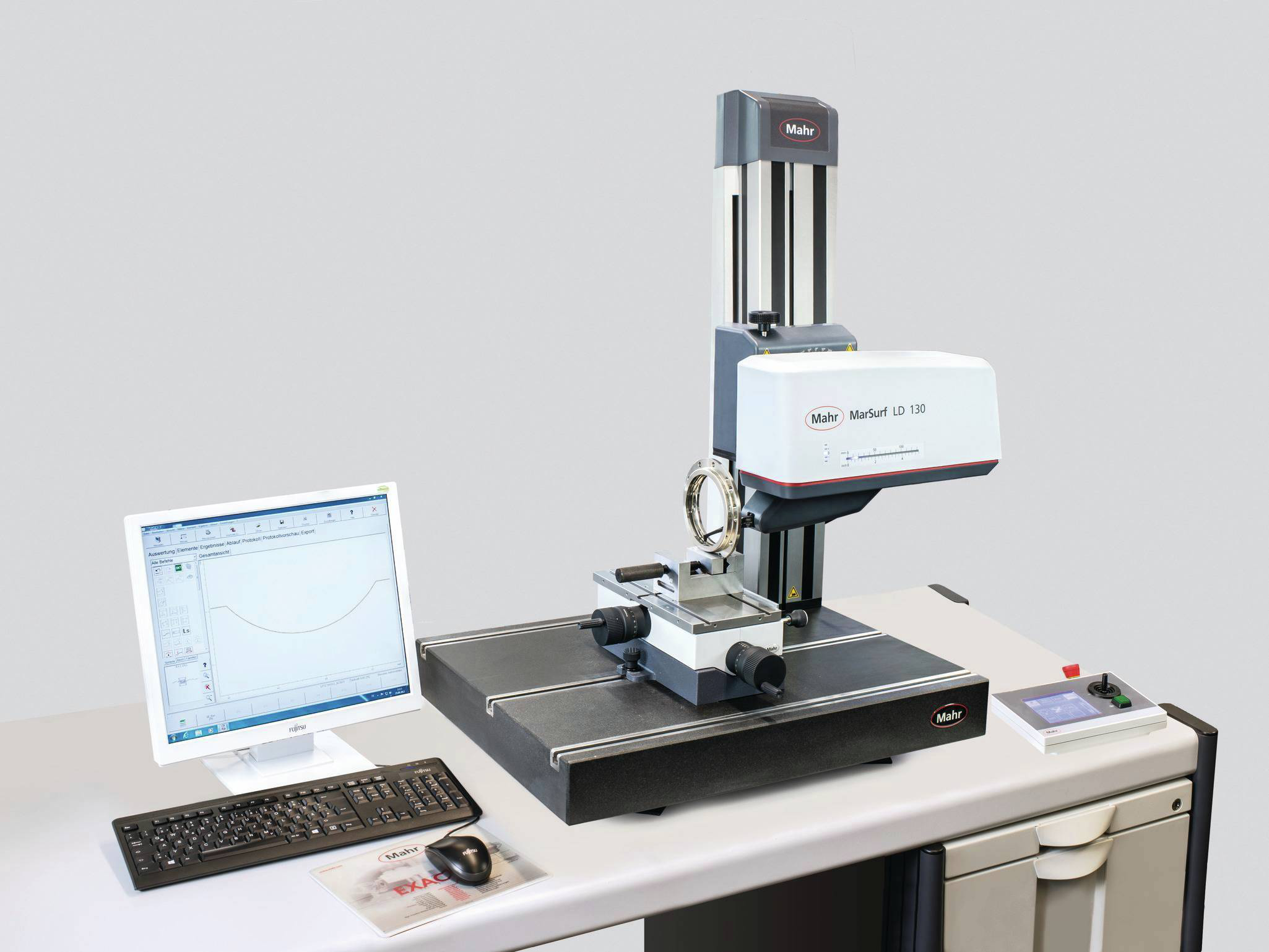
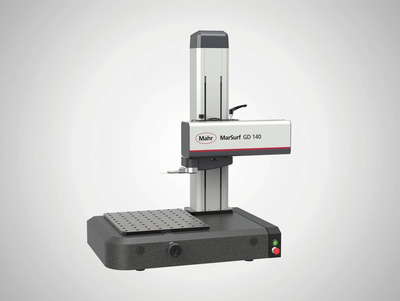
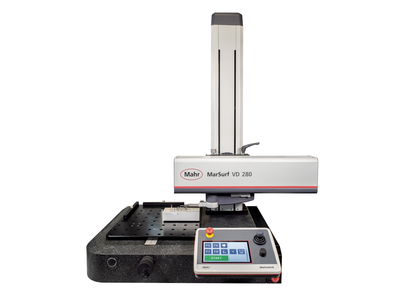
형상 및 거칠기 측정 결합: 다목적 전문 솔루션
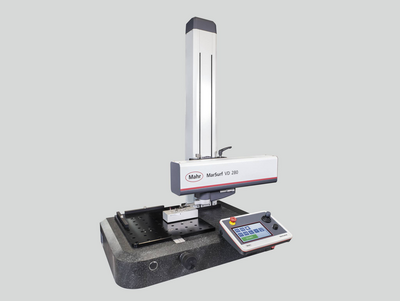
형상 및 거칠기 측정을 위한 접촉 측정 스테이션
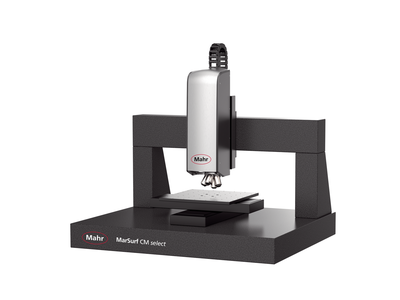
ISO 25178 / ISO 4287에 따른 2D/3D 형상 및 거칠기 측정
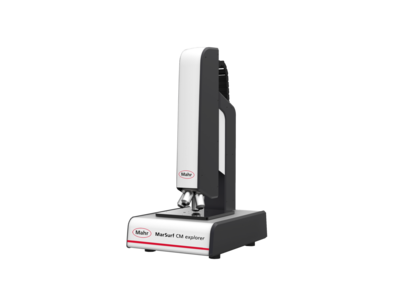
산업 및 연구를 위한 3D 표면 측정기
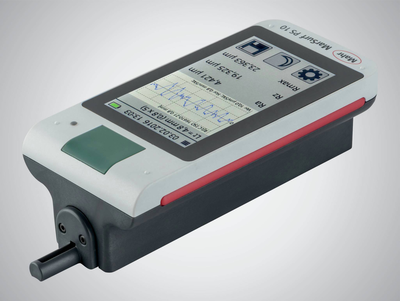
휴대용 측정 장치로 모든 분야를 측정합니다!
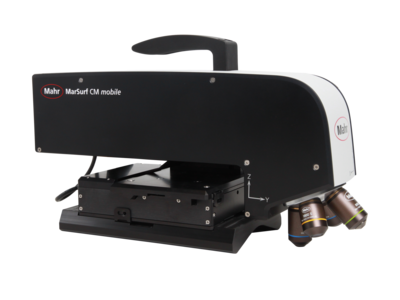
현장에서
사용하기 위한 모바일 3D 표면 측정기
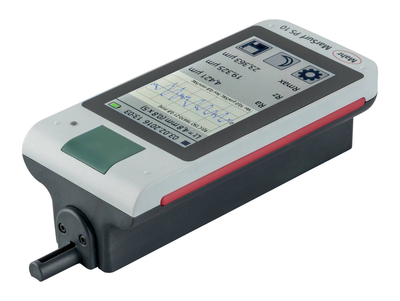
휴대용 측정 기를 이용하면 결과가 필요할 때 정확히 측정을 수행할 수 있습니다.
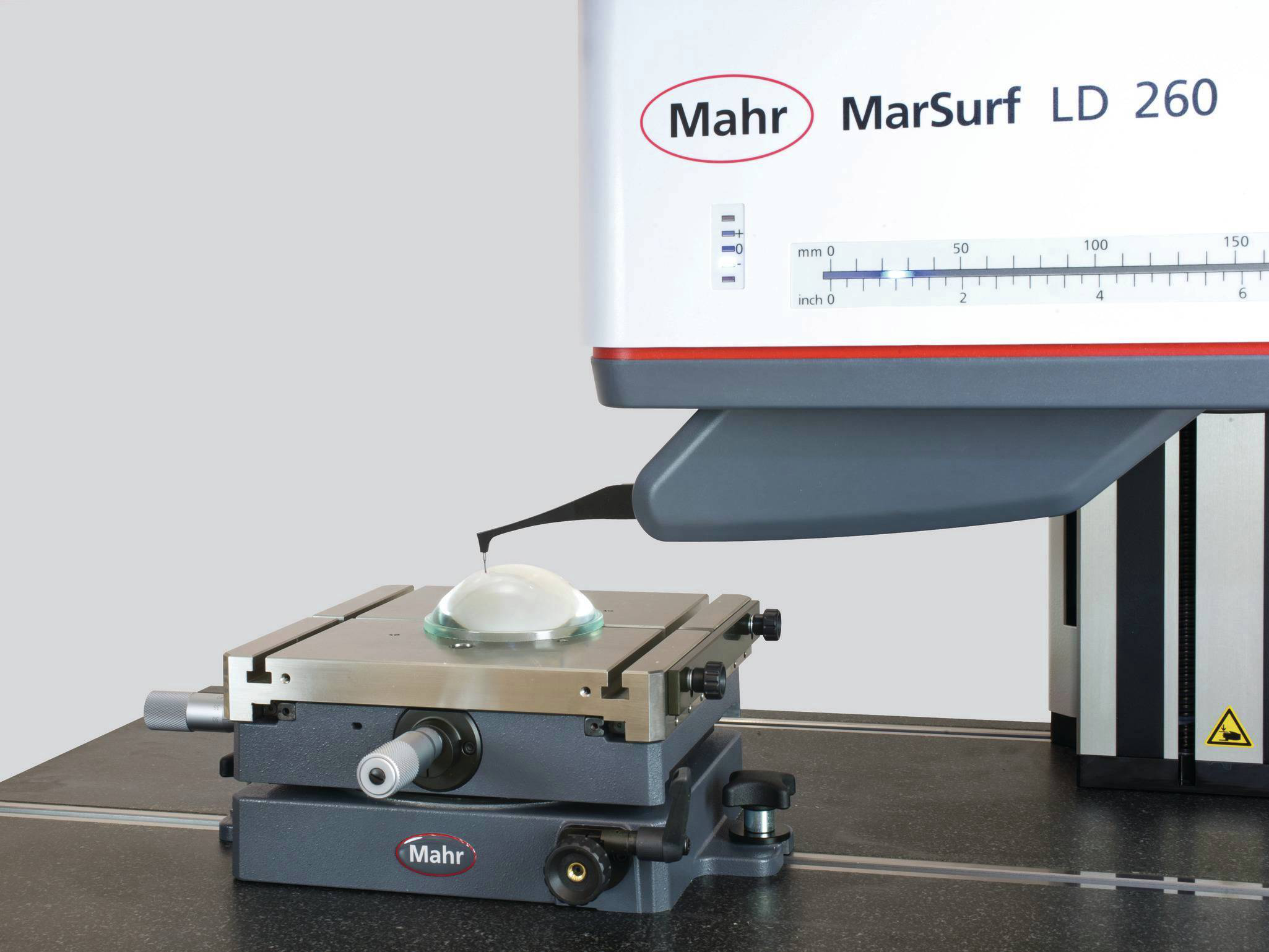
초고감도 렌즈 측정을 위한 측정 스테이션
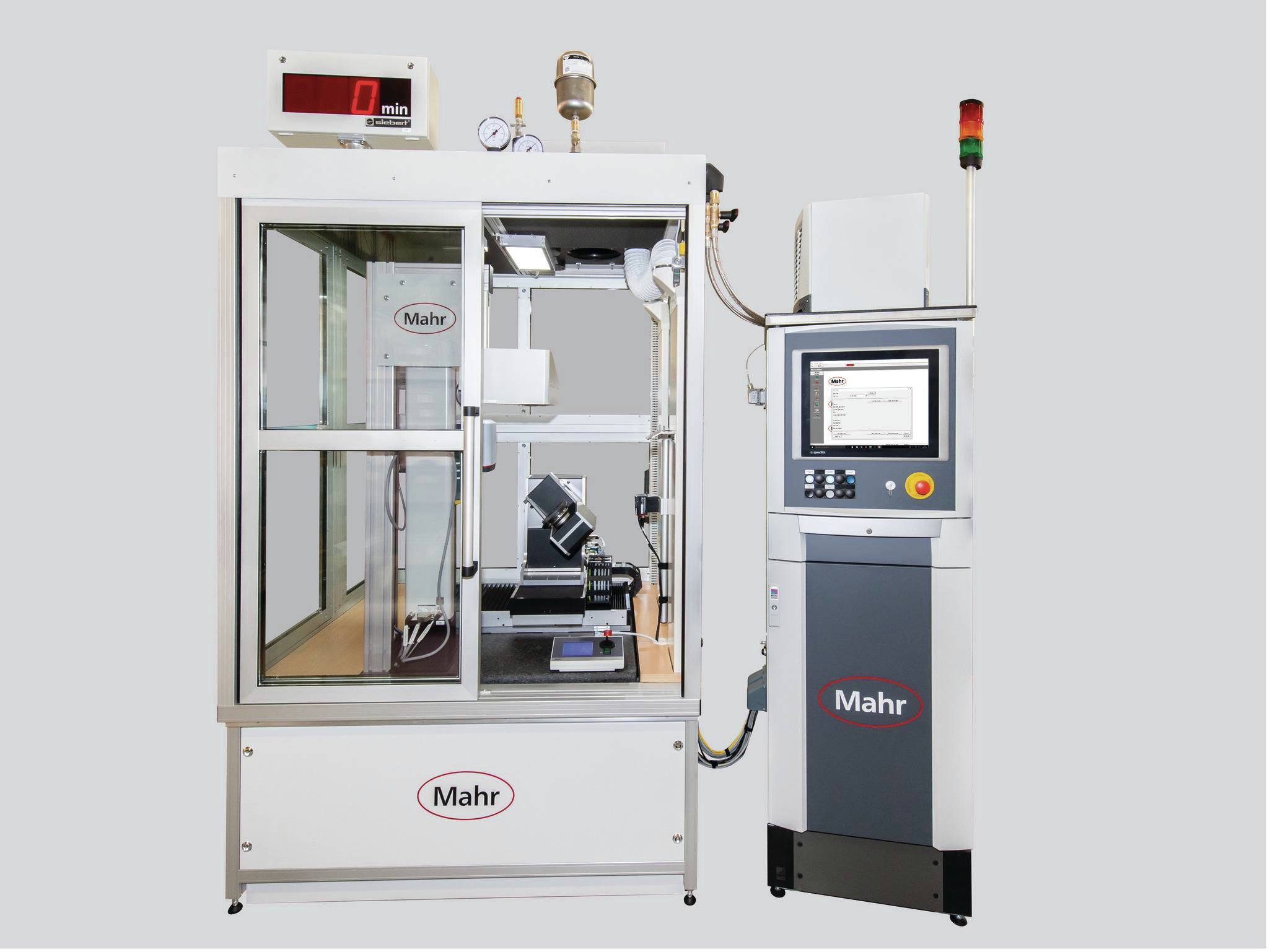
표준 솔루션으로 더 이상 충분하지 않을 경우: 개별 커스터마이즈 솔루션
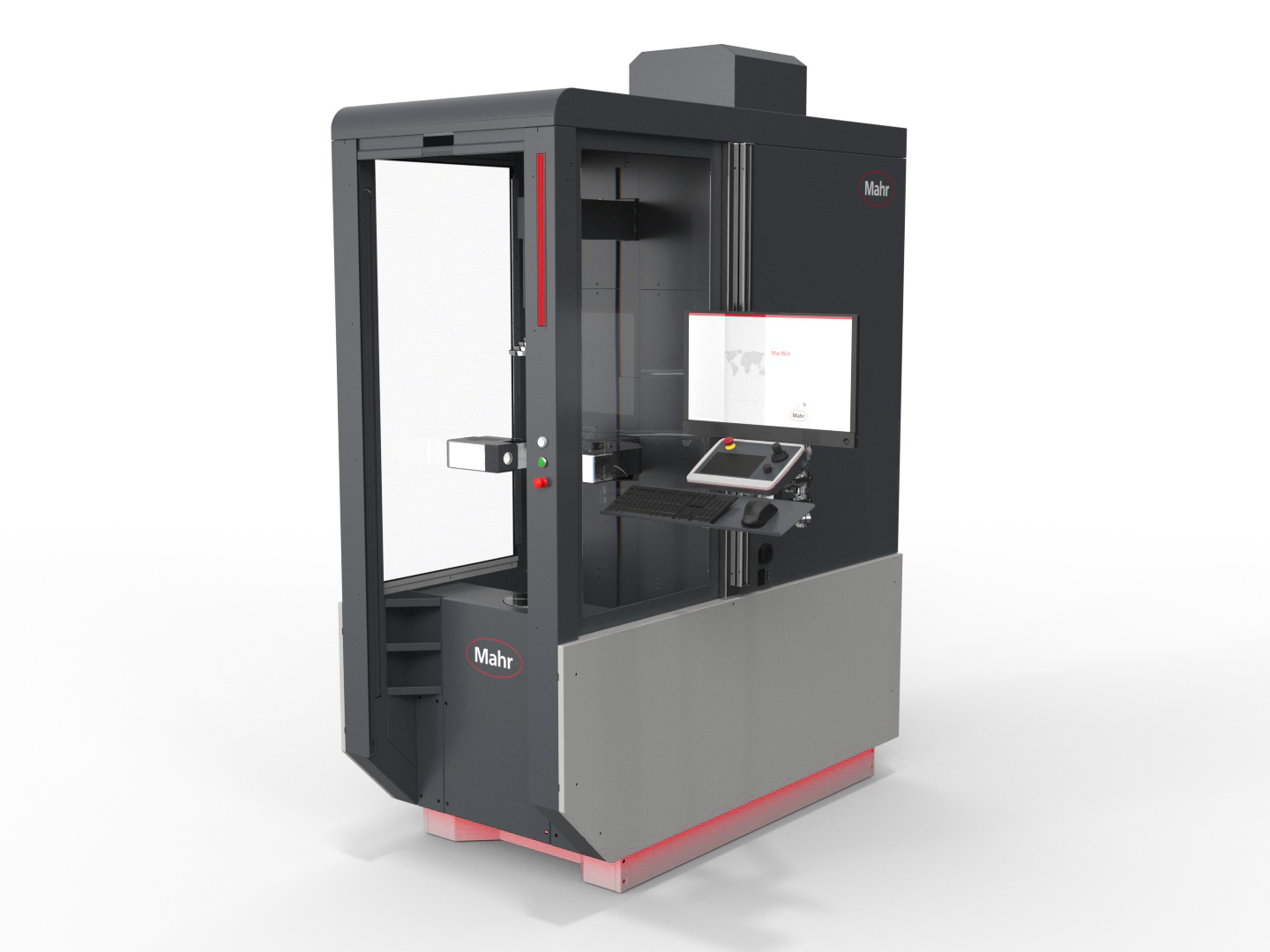
Metrology
Experience outstanding features combined with extreme flexibility in workpiece size and increase your productivity in the production environment.
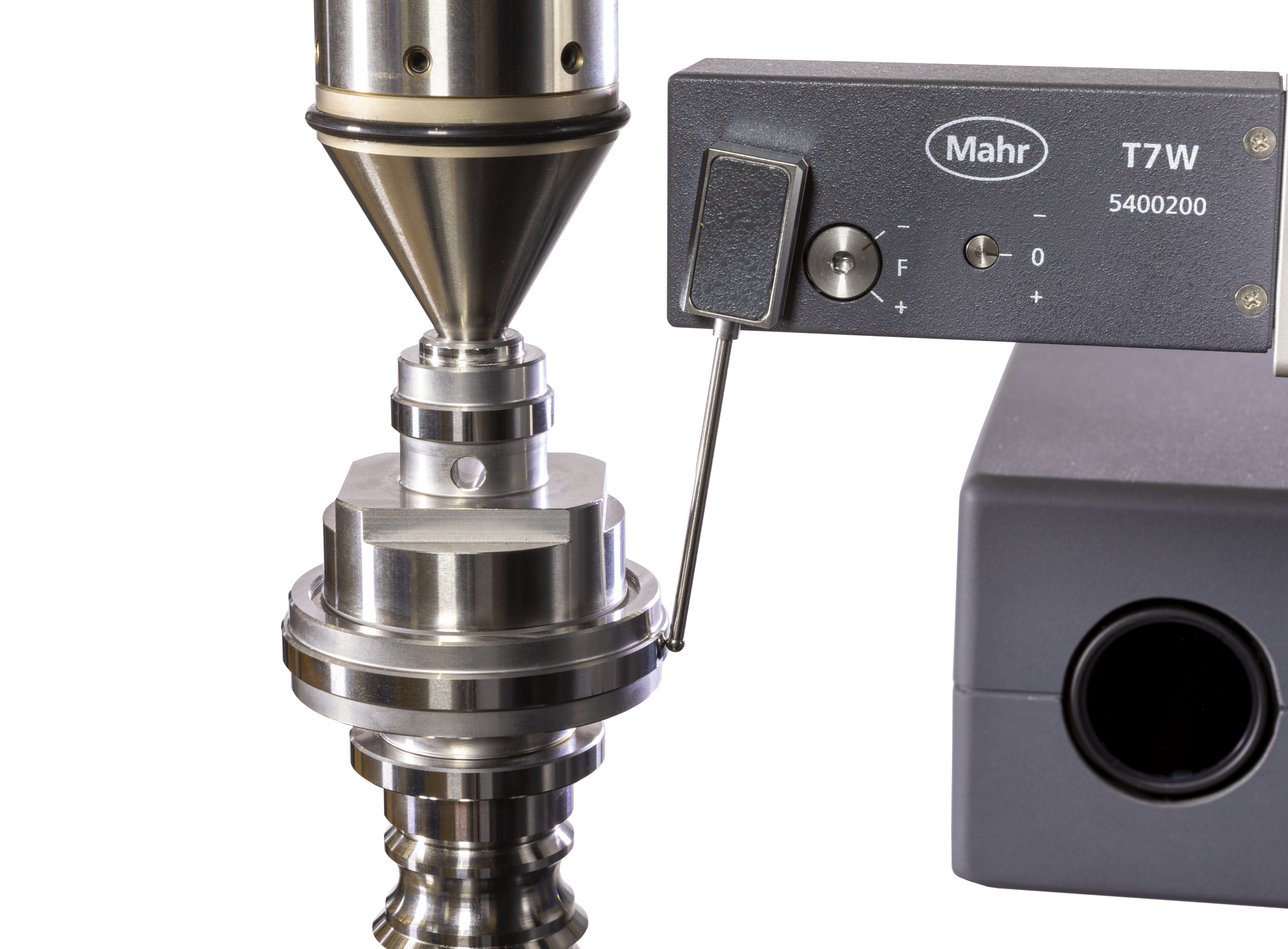
Fast optical matrix camera in combination with high-precision touch probes for measuring a large number of features on rotationally symmetrical workpieces.
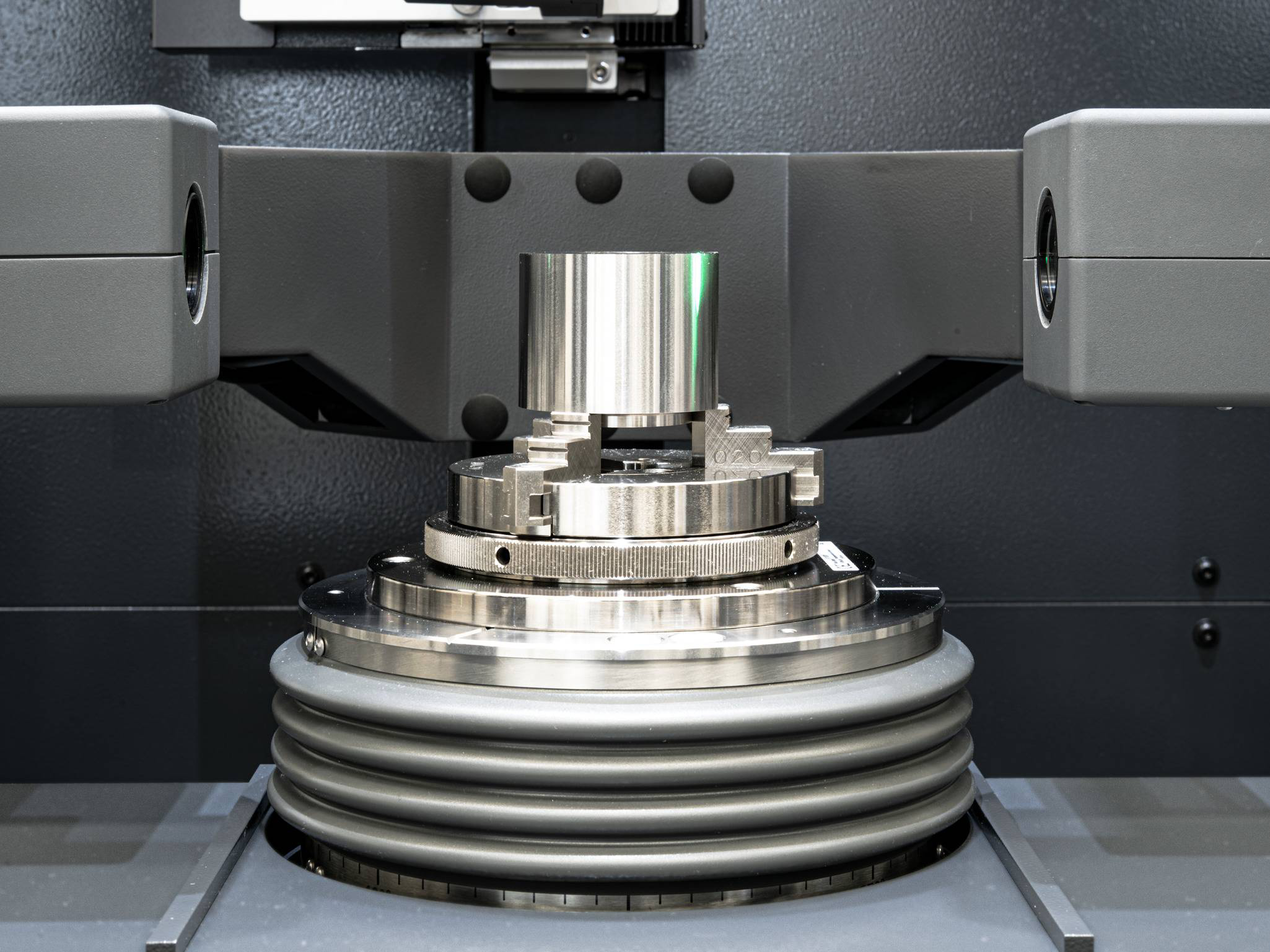
Fast optical matrix camera in combination with high-precision touch probes for measuring a large number of features on rotationally symmetrical workpieces. Addition of a fully automatic centering and tilting table for extremely fast, mechanical alignment, flexible clamping options and, for example, internal measurements.
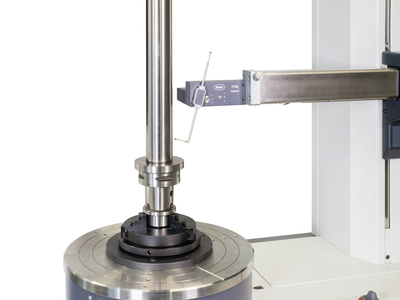
진원도, 평탄도, 평탄도, 진직도, 동축도 및 기타 측정 작업 등 형상 및 위치 공차를 테스트하기 위한 시스템. 수동에서부터 완전 자동식.

이 장치는 진원도, 진직도, 동심률 등과 같은 특성을 간단하고 비용 효율적이면서 매우 정확하게 측정합니다. 이 수동 형상 측정기기는 측정실에서의 작업을 비롯해서 생산 현장 가까이에서 측정을 수행하는 데 적합합니다.
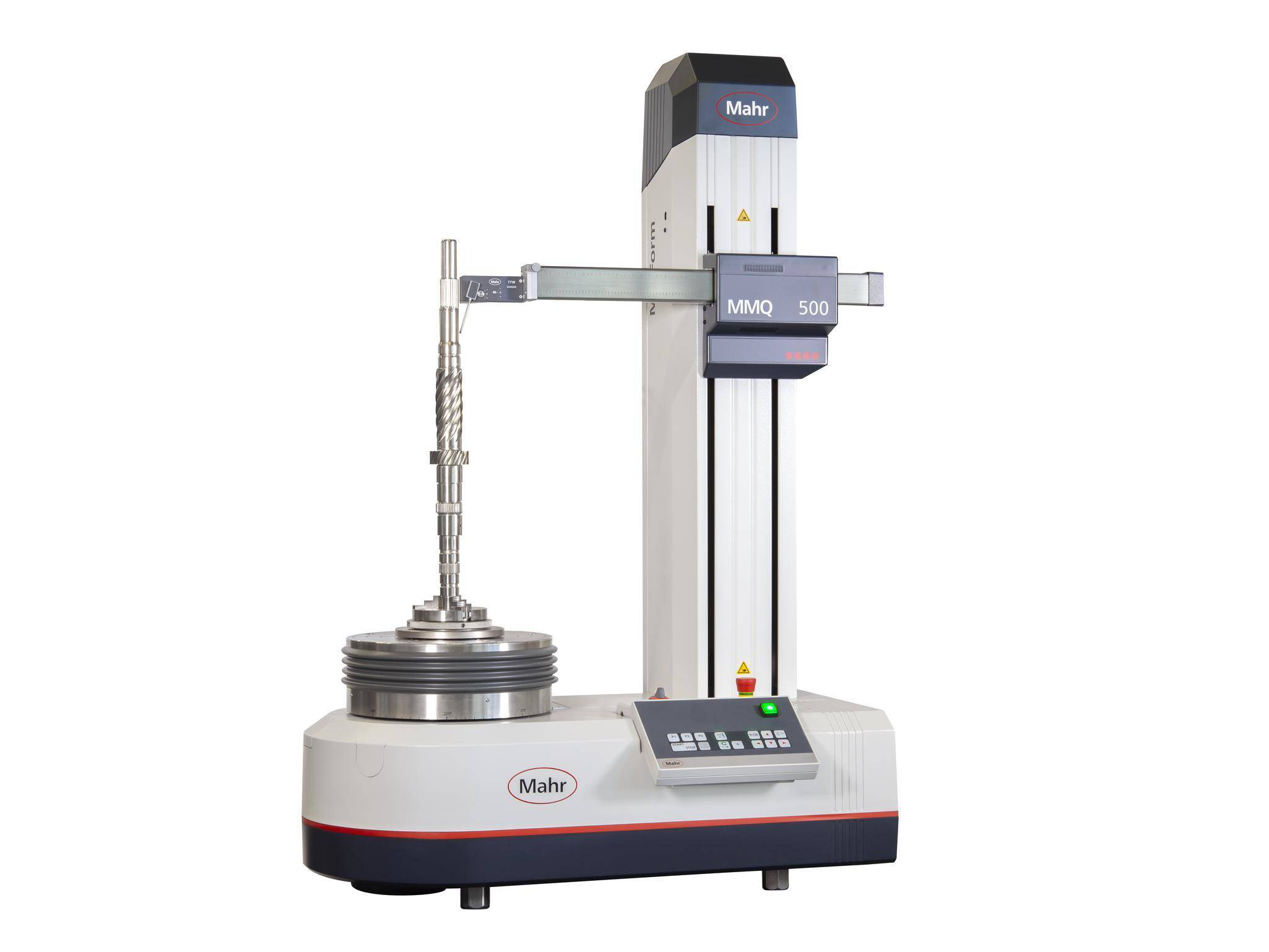
자동 진원도 측정 시스템을 이용하면 최고 수준의 자동화, 유연성 및 정확도를 갖춘 안정적이고 혁신적인 장치를 통해 검사 비용의 증가 없이 프로세스 비용을 줄일 수 있습니다.
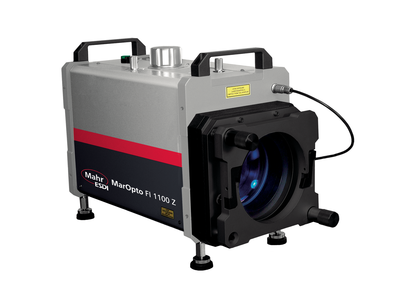
강력한 MarOpto Fizeau 간섭계는 평면 및 구형 표면에서 비접촉식 측정을 제공합니다.
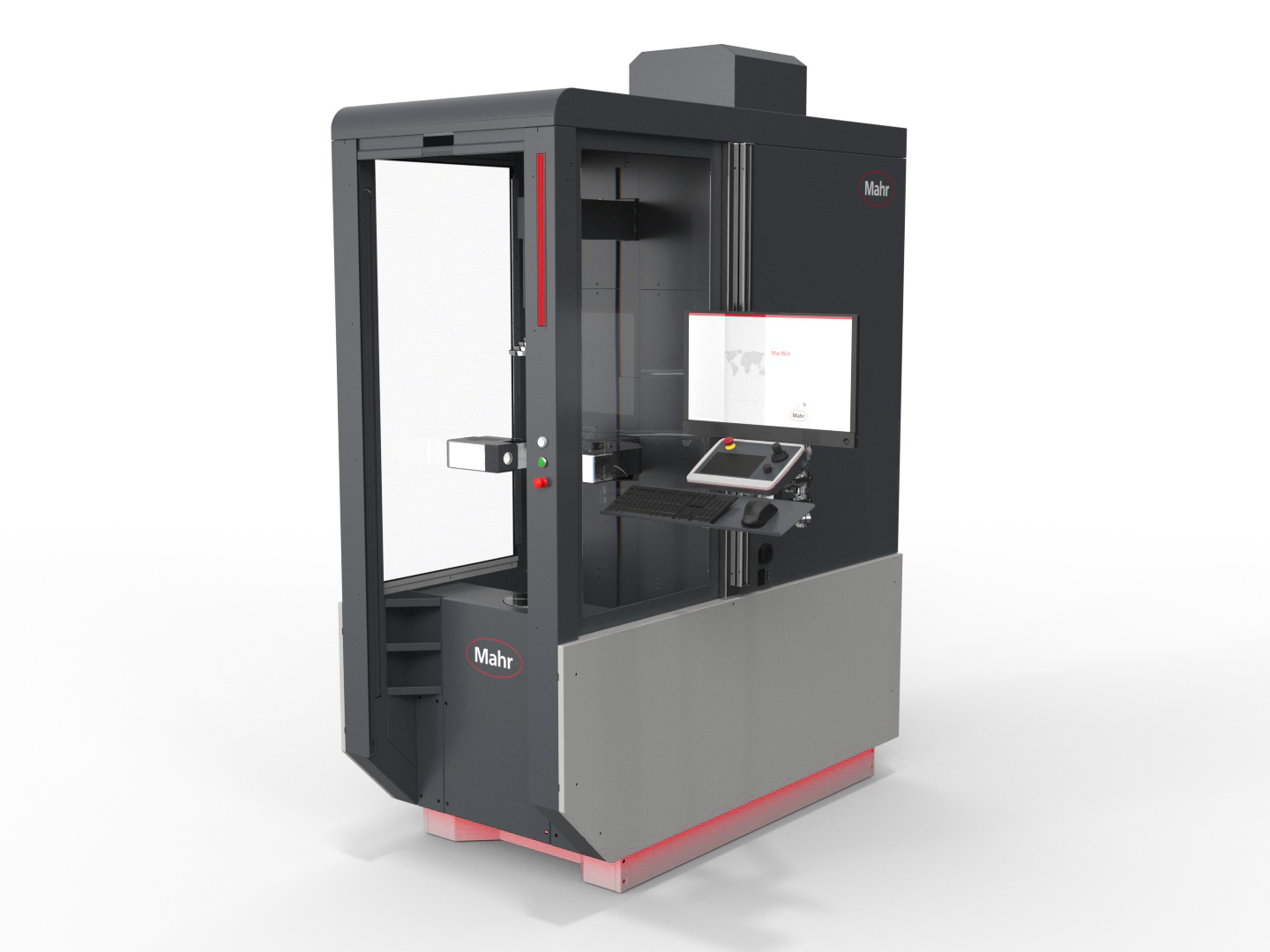
Metrology
Experience outstanding features combined with extreme flexibility in workpiece size and increase your productivity in the production environment.
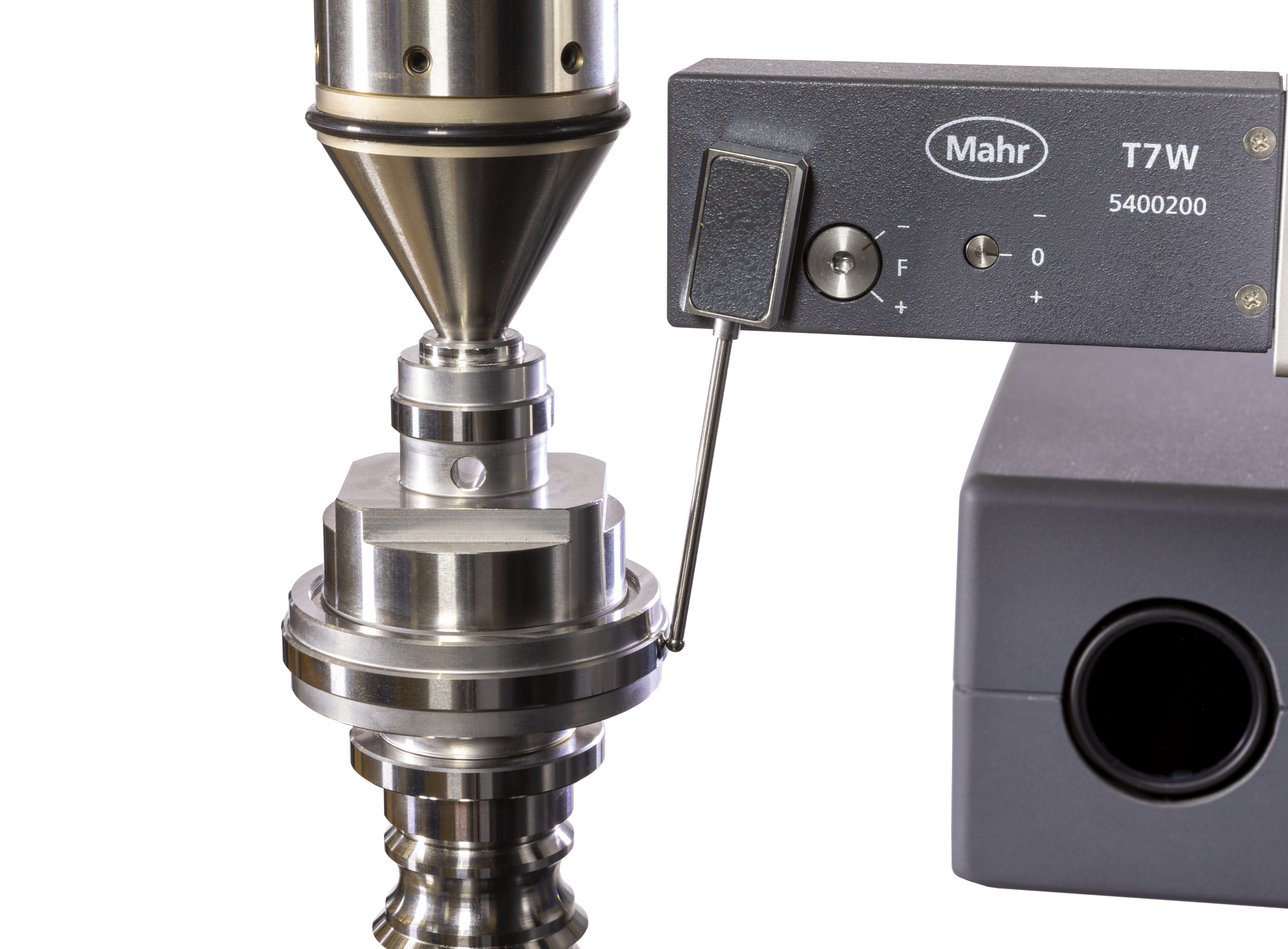
Fast optical matrix camera in combination with high-precision touch probes for measuring a large number of features on rotationally symmetrical workpieces.
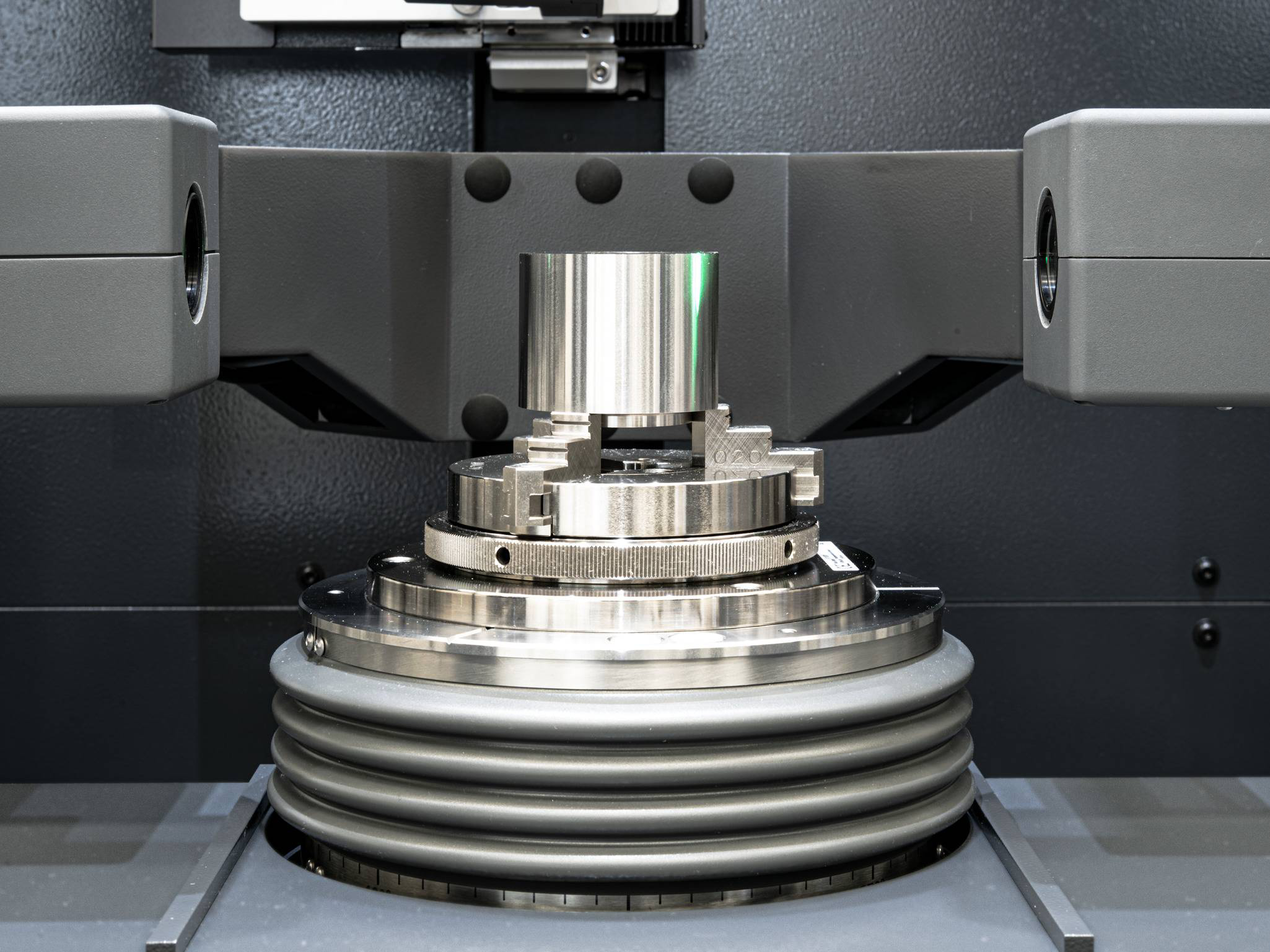
Fast optical matrix camera in combination with high-precision touch probes for measuring a large number of features on rotationally symmetrical workpieces. Addition of a fully automatic centering and tilting table for extremely fast, mechanical alignment, flexible clamping options and, for example, internal measurements.
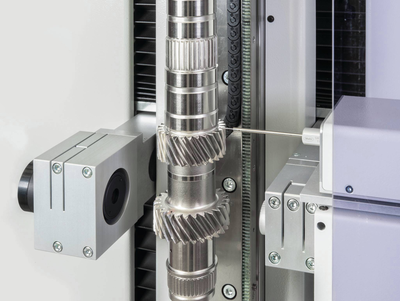
혹독한 제조 환경에서 사용 하기 위한 광학 및 접촉 샤프트 측정 시스템. 일반적인 모든 회전 대칭형 측정물을 완벽하게 측정.
.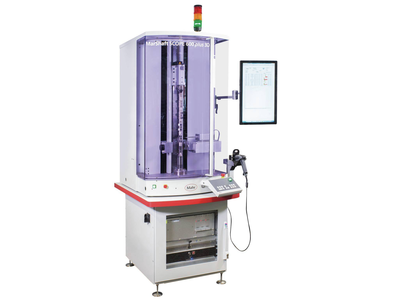
혹독한 제조 환경에서 사용 하기 위한 광학 및 접촉 샤프트 측정 시스템. 일반적인 모든 회전 대칭형 측정물을 완벽하게 측정.
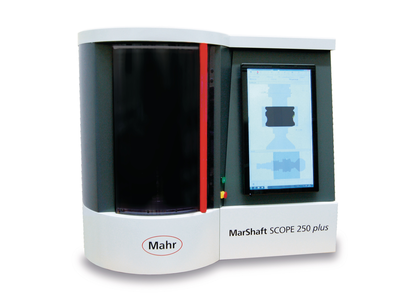
거친 워크샵 환경에서 사용하기 위한 완전 자동식의 강력한 범용 광학 샤프트 측정기기.
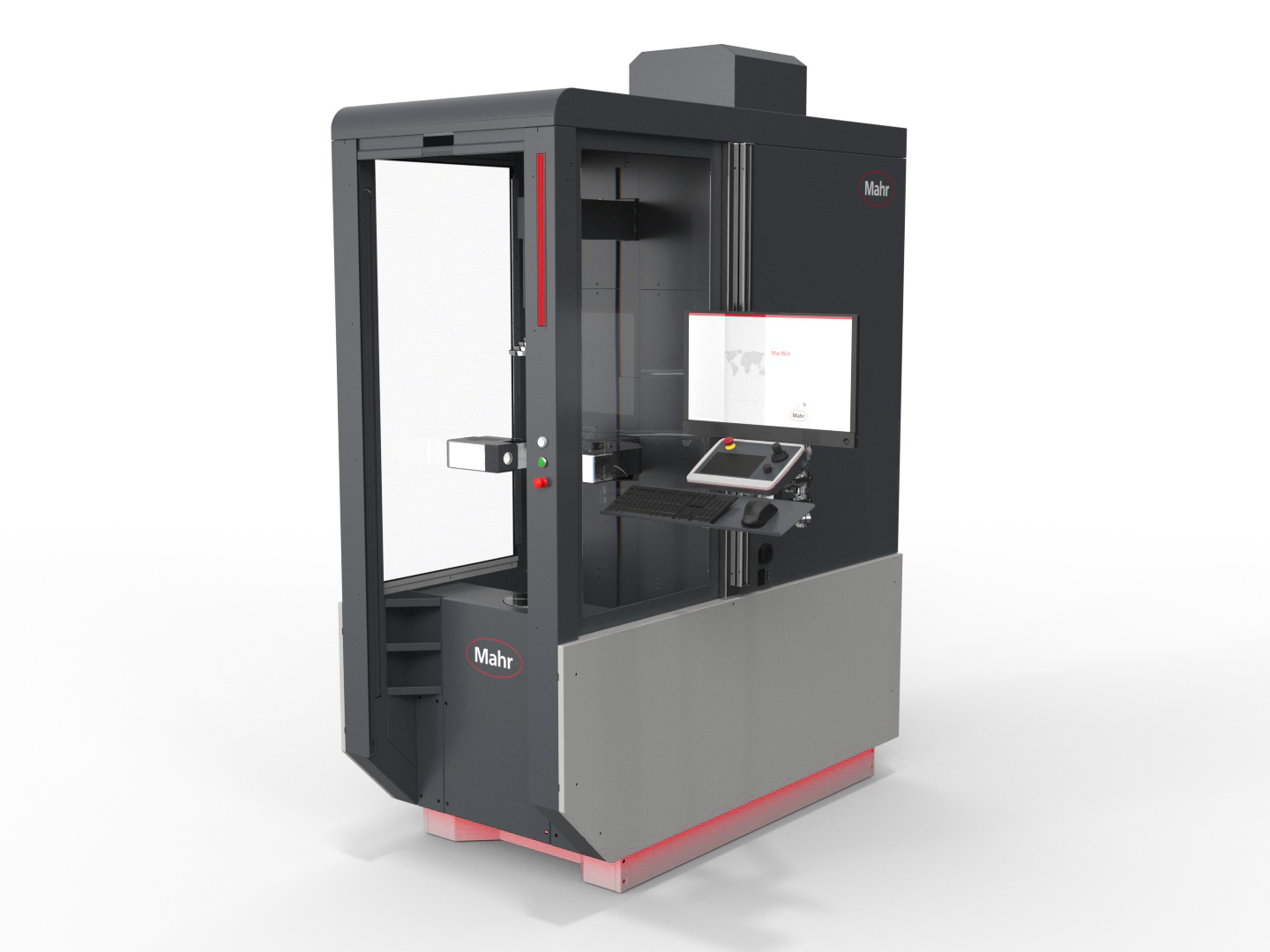
Metrology
Experience outstanding features combined with extreme flexibility in workpiece size and increase your productivity in the production environment.
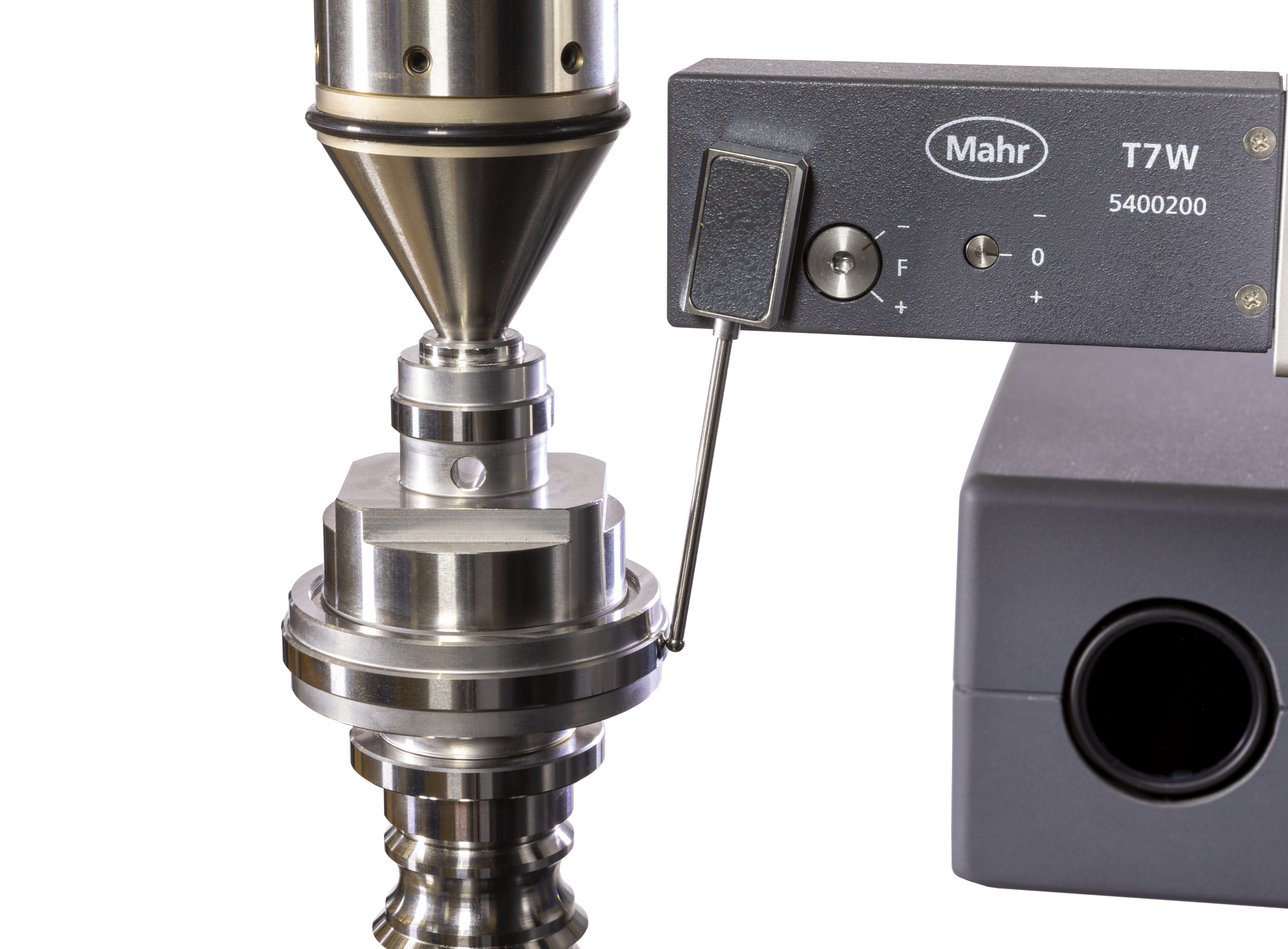
Fast optical matrix camera in combination with high-precision touch probes for measuring a large number of features on rotationally symmetrical workpieces.
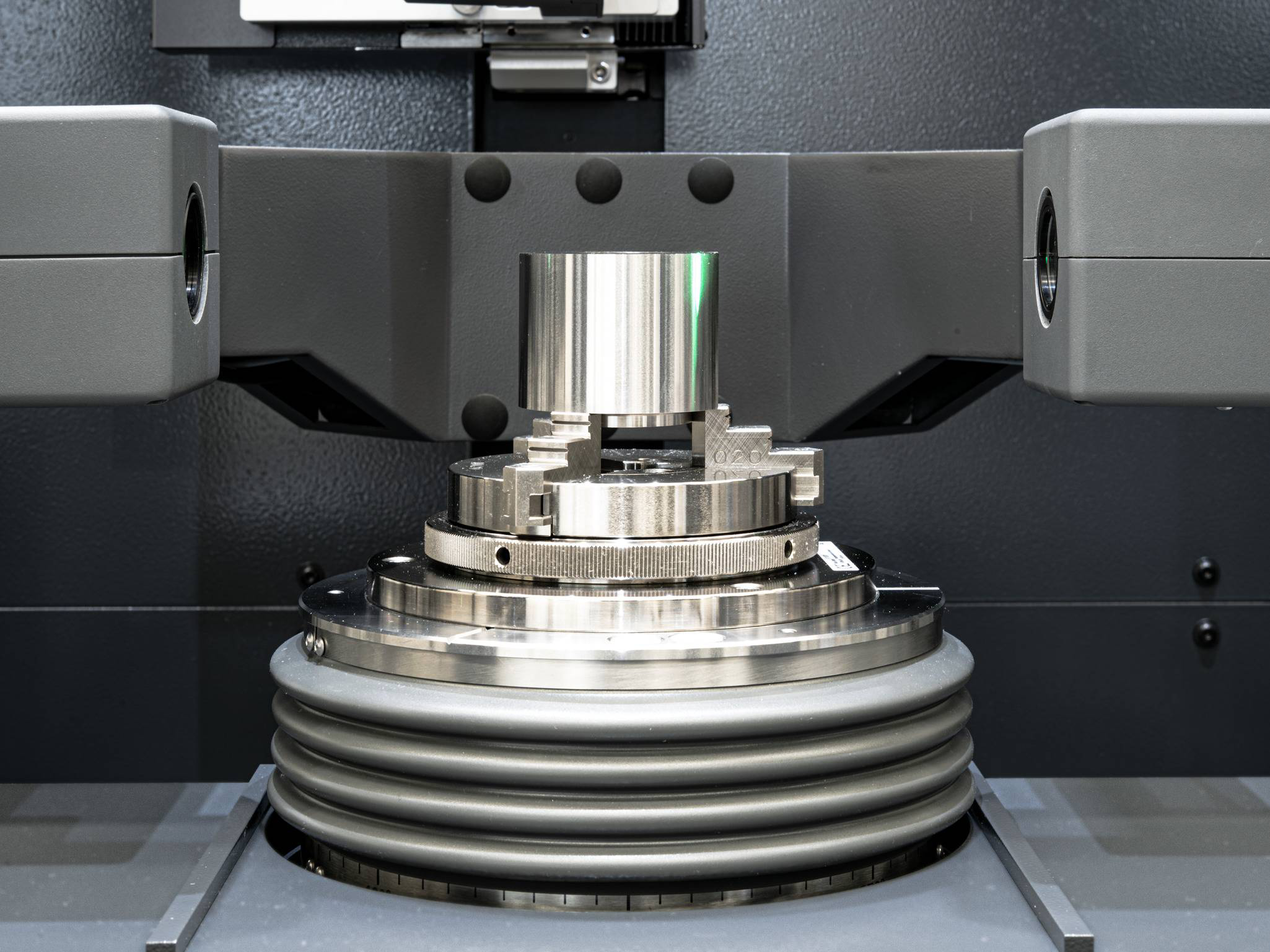
Fast optical matrix camera in combination with high-precision touch probes for measuring a large number of features on rotationally symmetrical workpieces. Addition of a fully automatic centering and tilting table for extremely fast, mechanical alignment, flexible clamping options and, for example, internal measurements.

고도의 전문적인 기어 분석부터 완전 통합형 연속 측정까지, Mahr는 모든 현대 기어 및 기어박스 제조에서 믿을 수 있는 파트너입니다.
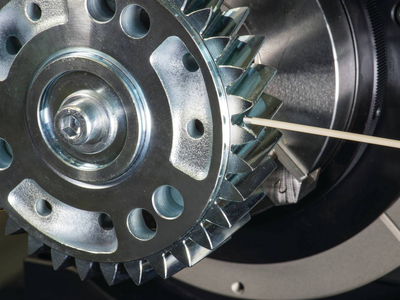
제품 제조 시점에 제품을 측정하여 제조 공정에서 신속하게 피드백을 보내면 불량 제품의 생산을 줄일 수 있습니다.
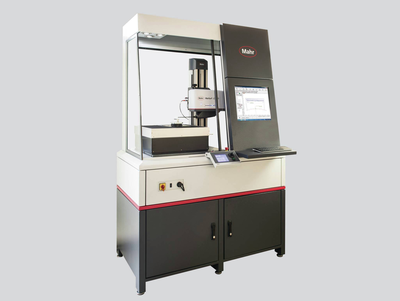
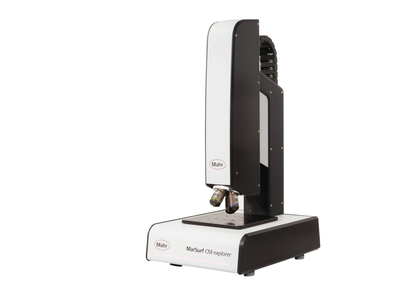
표면 및 기하구조의 빠른 비접촉식 기록을 위한 광범위한 기술과 제품.
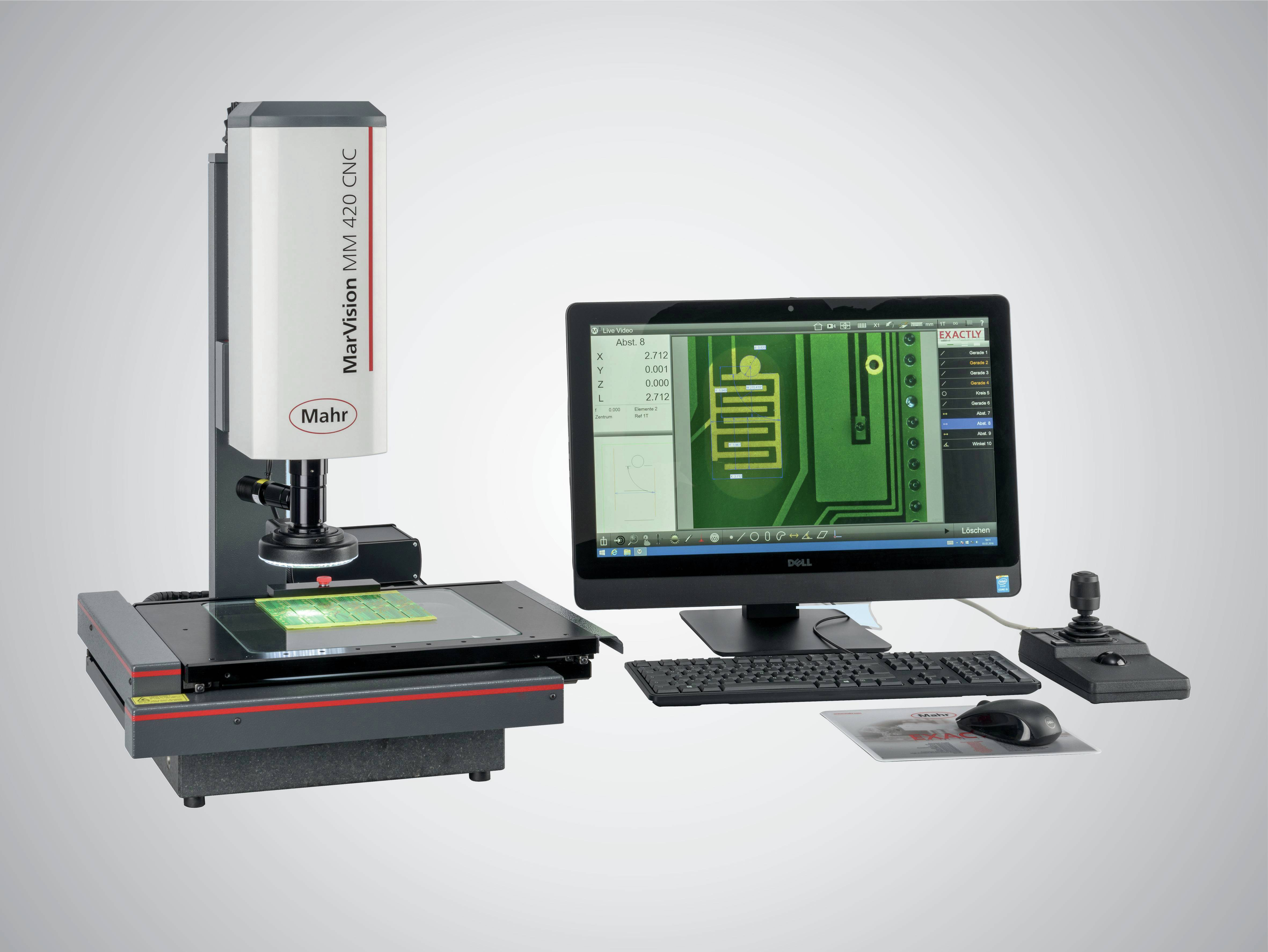
현미경은 거리, 반지름, 각도의 빠른 검사를 위해 거의 모든 산업에서 사용됩니다. 실험실 또는 생산 현장 가까이에서 사용됩니다.
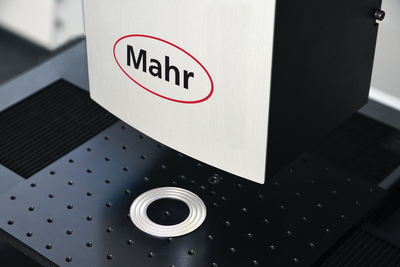
거칠기, 윤곽선 및 기타 여러 표면 파라미터를 결정.
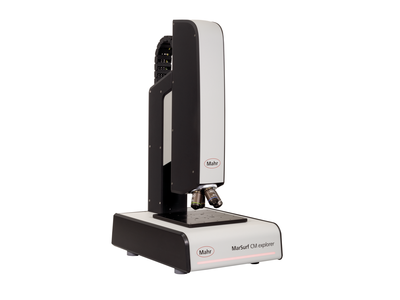
산업 및 연구를 위한 표면 측정기
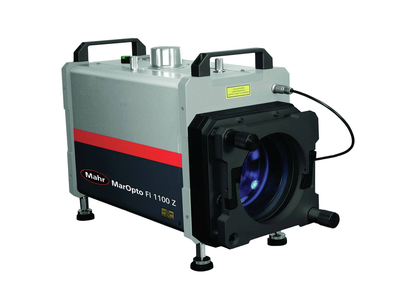
백색광 또는 레이저 간섭계든, 해당 분야에 가장 적합한 솔루션을 찾을 수 있습니다.
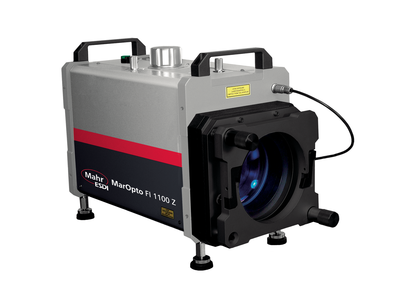
강력한 MarOpto Fizeau 간섭계는 평면 및 구형 표면에서 비접촉식 측정을 제공합니다.
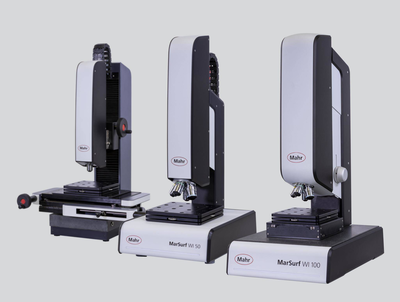
나노미터 수준의 최소 거칠기 정확도
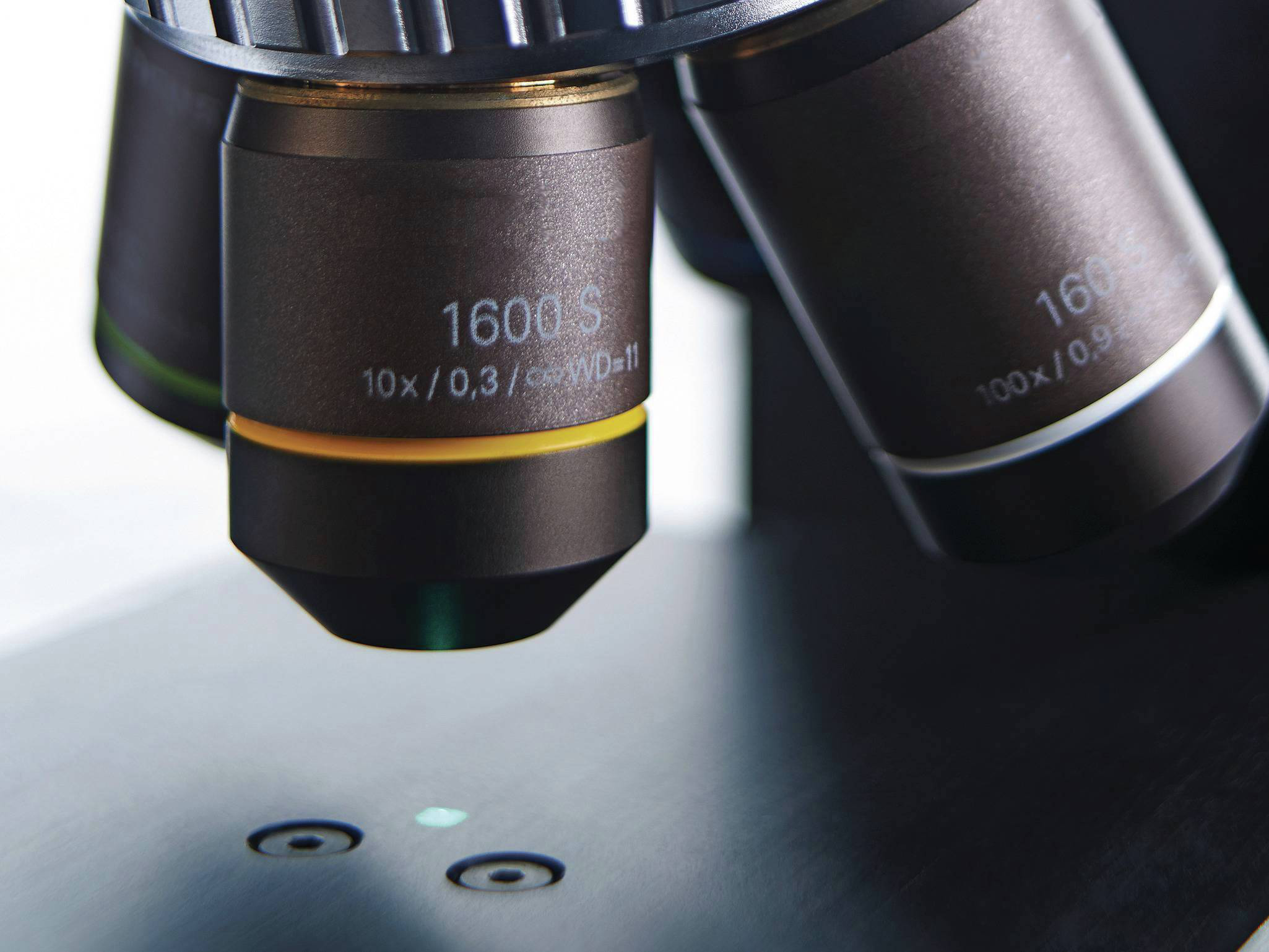
표면 토포그래피 및 기하구조의 광학 분석
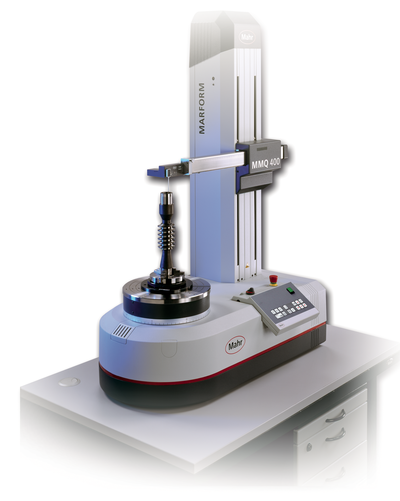
입증된 Mahr 품질의 리퍼비시 시스템
사례 연구: 측정 셀에서 선삭 부품 테스트
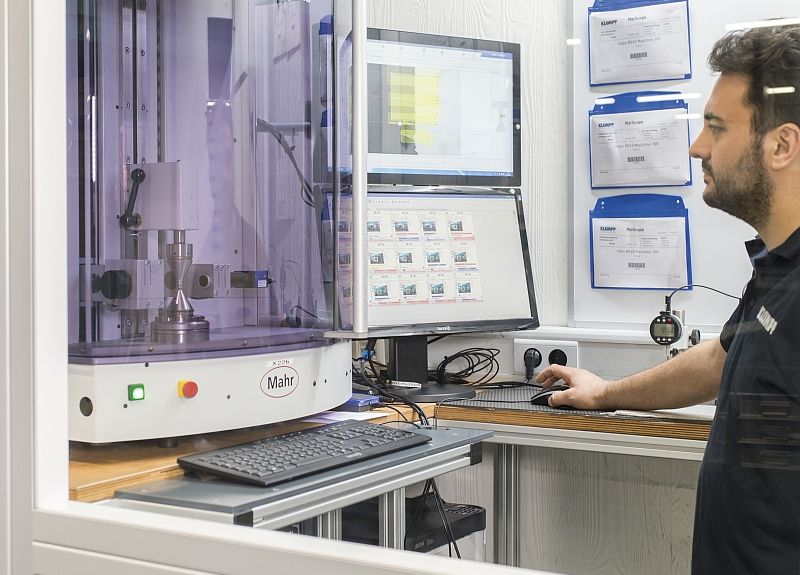
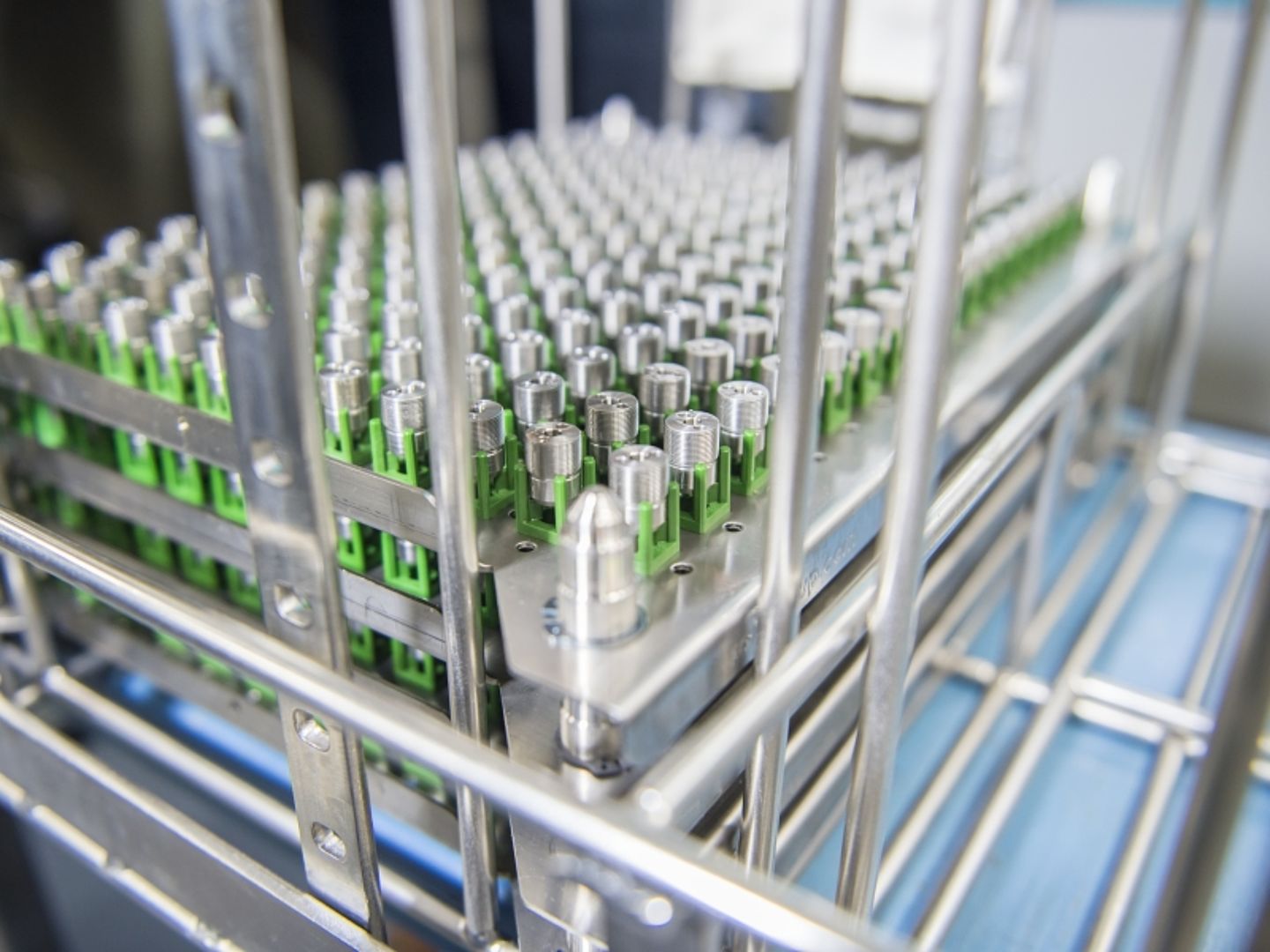
소형 선삭 부품은 다양한 산업의 많은 조립품에 사용됩니다. 공작물 요구 사양은 정확히 명시된 대로 1,000분의 1밀리미터로 생산됩니다. Karlsruhe 근처의 Bretten에 위치한 Klumpp는 세계 최고의 선삭 부품 제조 업체 중 하나이며, 고정밀 선삭 부품의 대량 생산을 전문적으로 합니다. 제품의 크기는 4 ~ 32 mm 사이입니다. Klumpp는 다양한 재질 및 매우 복잡한 기능의 제품을 제조합니다. Klumpp는 고객의 요구를 충족하기 위해 최신 제조 기술과 고품질 처리 방법을 이용합니다.
새로운 방향 필요
이러한 이유로 회사의 품질 관리를 시험해 보기로 결정했습니다. 실현: 이전 절차는 매우 복잡했고 작업자가 끼치는 영향에 따라 100% 신뢰할 수 없었습니다. 또한, 현재 표준규격에 따라 결과를 문서화할 수 없었습니다. 게다가, 제조 라인에서 멀리 떨어진 정밀 측정실에서 컨트롤을 해야 했으므로 시간이 많이 소모되었습니다.
Klumpp사 에게는 이러한 취약점이 품질 보증을 재정비해야 하는 충분한 사유가 되었습니다. Mahr와 함께, 측정기를 담당하는 부서 매니저 Evelin Kobiljar는 지속적인 양산의 품질을 모니터링 및 문서화 가능한 방식으로 하기 위해 제조 라인 가까이에서 새로운 컨셉을 개발하였습니다.
해결책: 제조 라인의 측정 셀
새로운 솔루션의 핵심은 냉난방 장치가 완비되고 측정 셀이 커버 되어 제조 라인에 직접 배치하는 것입니다. 이는 오염으로부터 방지하고 일관된 기후 조건을 보장합니다. 측정기 작업자가 여기서 직접 측정을 수행합니다.
Kobiljar는 측정 셀 내에 시험 장비 시스템의 좌표계를 셋업 하였습니다. 이 시스템은 프로세스에 대해 신뢰할 수 있고, 절대 측정값을 안정적으로 유지하며, 정밀 측정실에서 승인을 받았습니다. 정밀 측정실에서 사용된 측정 프로그램은 계속해서 작성되며, 여기에 품질 관리 책임이 적용됩니다. 모든 장치는 최신 측정 프로그램을 검색하며, 이는 안전하고 신뢰할 수 있는 측정값을 구현하는 데 있어 중요한 기초가 됩니다.
성공을 위한 4가지 단계
새로운 측정 개념에 따른 품질 보증은 4가지 단계로 이루어집니다.
1단계: 첫 단계는 담당 직원과 시편을 확인하는 것입니다. 나중에 QR 코드를 판독해서 인식할 수 있습니다. 이 단계는 문서화를 위해 중요하며, 동시에 또 다른 장점을 제공합니다. 즉, 측정은 항상 정확한 최신 측정 프로그램을 사용해서 이루어집니다.
2단계: 그런 다음, 4개의 Mahr 디지털 다이얼 게이지를 사용해 내경 치수가 자동으로 측정됩니다. 측정 결과가 케이블을 통해 샤프트 측정 시스템으로 전송되고, 그 다음의 테스트가 실행됩니다.
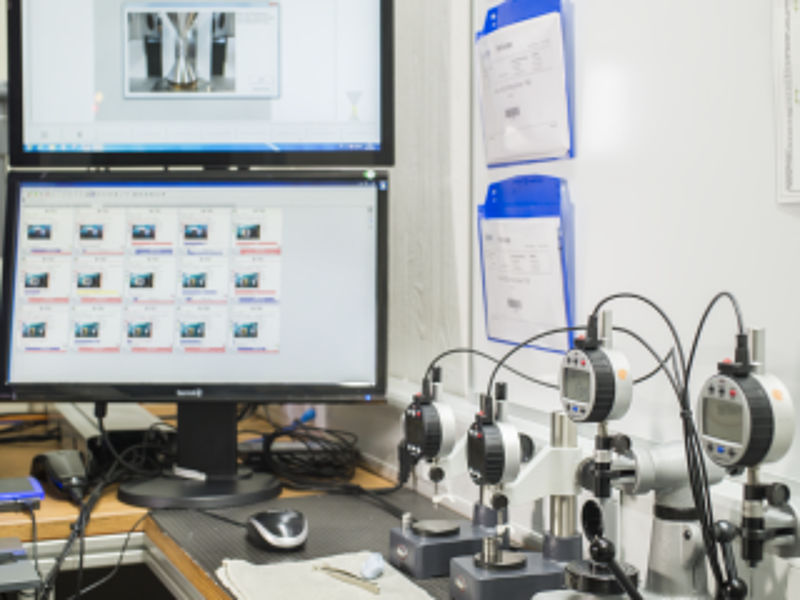
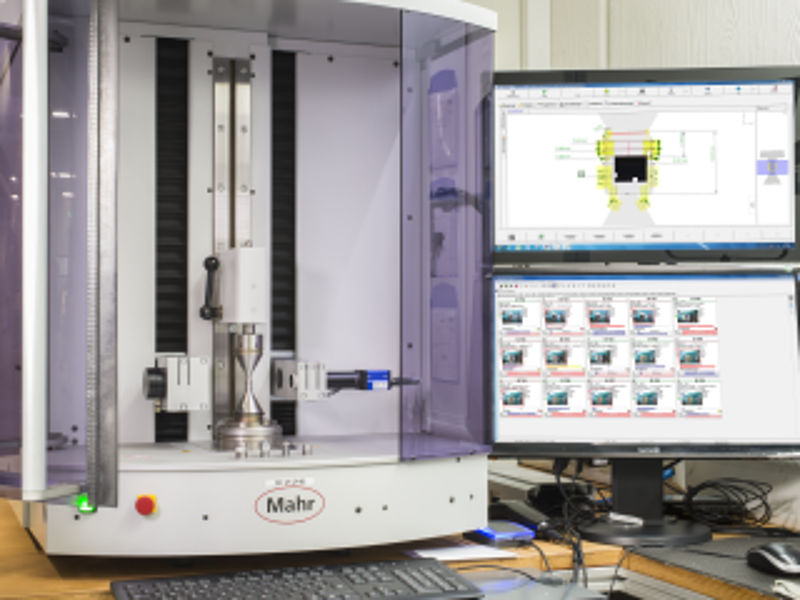
3단계: 내부 치수를 기록한 후, Klumpp 직원은 완전 자동식 광학 측정 시스템 MarShaft SCOPE 350 plus를 이용해 측정물의 외부 치수를 확인합니다. 작업자가 측정물을 측정 시스템에 체결한 다음, 측정을 시작합니다. 이 시스템은 단 15초 안에 지름, 길이, 반지름, 각도 등 외부 윤곽선에 대한 40가지의 특징을 측정합니다. 측정 순서는 작업자의 간섭 없이 완전 자동으로 수행됩니다.
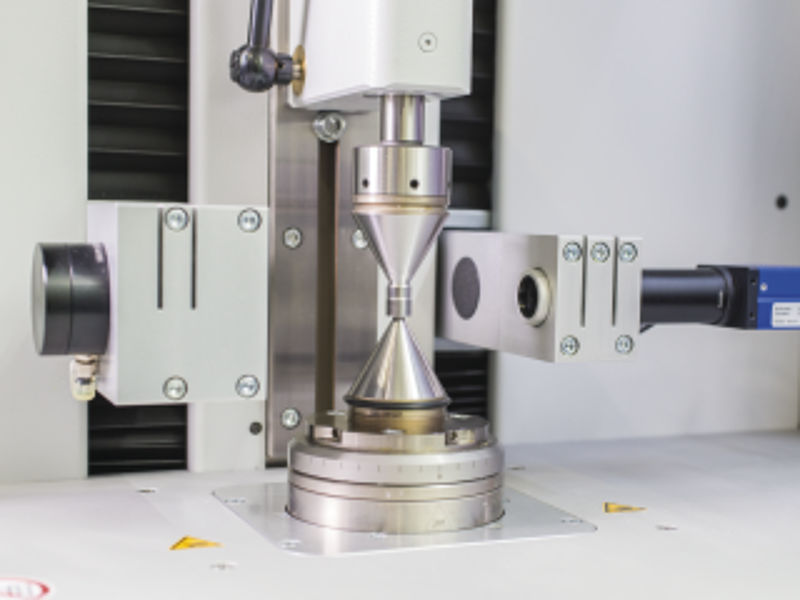
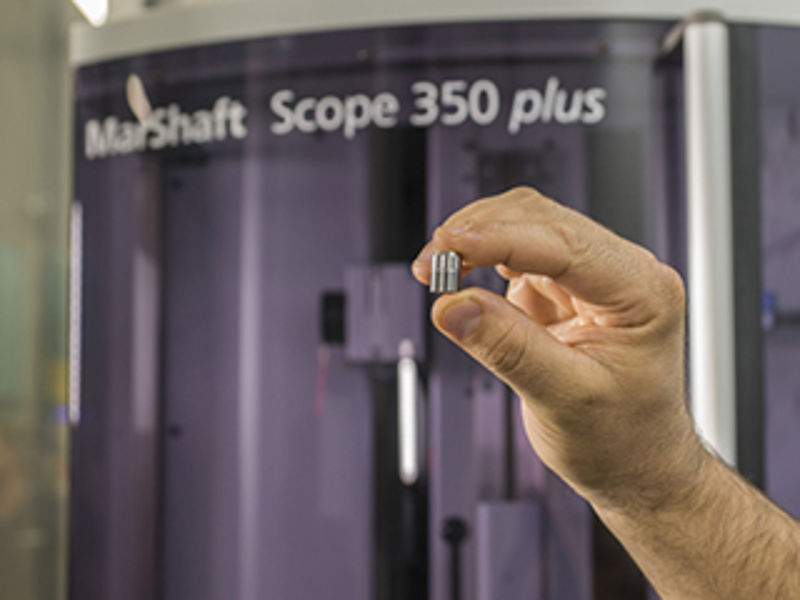
4단계: 모든 측정이 완료되면 내부 및 외부 측정을 위한 모든 측정 데이터가 품질 관리 시스템으로 전송되고, 여기서 측정값이 평가 및 문서화됩니다.
측정 개념의 이점
새로운 측정 솔루션은 Klumpp와 품질 보증 담당자에게 많은 이점을 가져다 줍니다:
- 휴대형 기기 수가 크게 줄어들어 품질 보증 비용이 감소하였습니다.
- 교정 및 기기 관리를 위한 비용과 노력이 줄어들었습니다. 측정기기 및 시스템의 투자 비용을 불과 몇 달 안에 회수하였습니다.
- 측정이 보다 효율적이고 믿을 수 있으며 항상 작업자의 개입 없이 진행되었습니다.
- 생산이 허용 공차 내에서 진행되는지에 대한 빠른 피드백을 확보하고 값비싼 제품 불량 또는 불만을 효과적으로 방지할 수 있게 되었습니다.
결론
전반적으로 Klumpp의 전체 제조 품질 보증이 보다 정확하고 효율적으로 개선되었습니다. 이제 새로운 측정 개념이 성공적으로 테스트되었으므로 Klumpp는 생산에서 다량의 수동 측정기 제조라인을 제거할 것입니다. 대신 총 7대의 표준화 측정 셀이 설치될 예정입니다. 그런 후, 회사는 생산 작업에서 정밀 선삭 부품의 생산 품질을 안정적으로 보장하는 목표를 달성하였습니다.