Ölçüm odasında, üretimde, gelen mallarda ve geliştirme alanında kalite kontrol için yüksek kaliteli metroloji.
Gear Metering Pumps & Meter Mix Dispense Machines with highest accuracy for processing liquids and pastes.
High-precision rotary stroke bearings for backlash-free linear and rotational movements for use in machine and device construction.
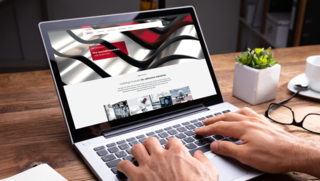
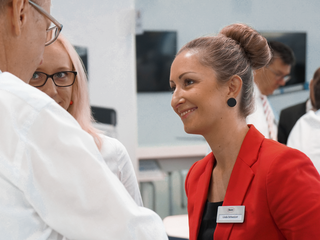
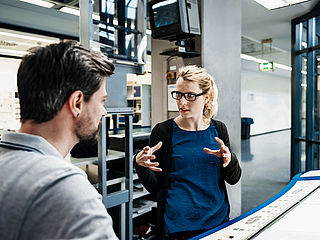
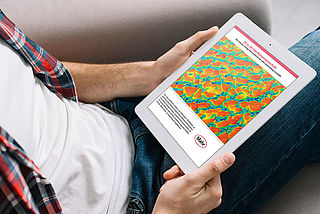
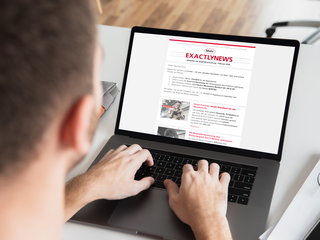
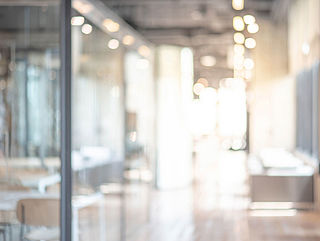
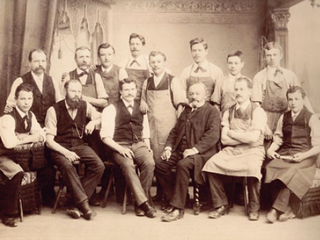
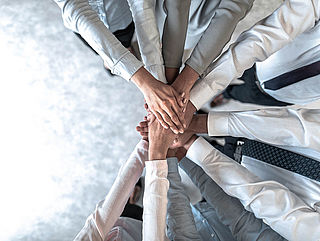
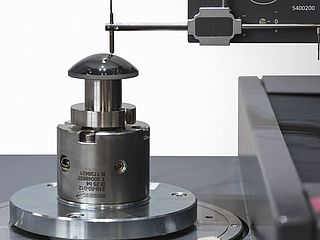
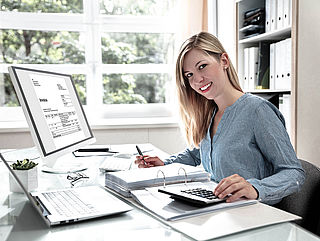
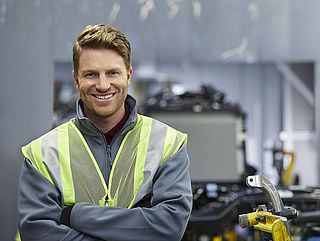
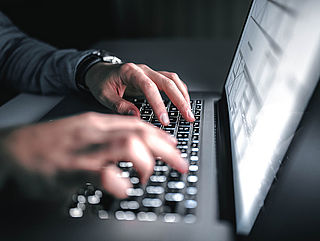
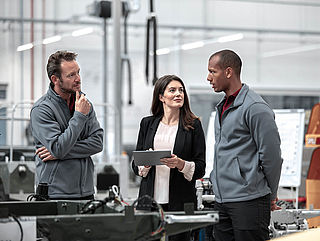
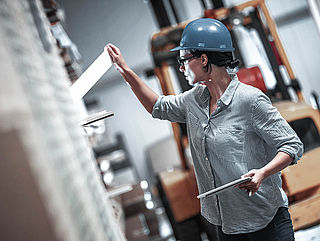
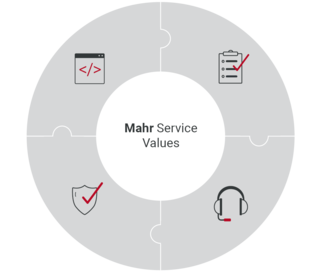
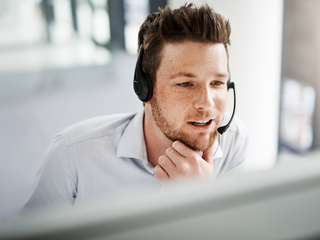
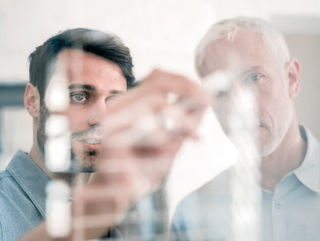
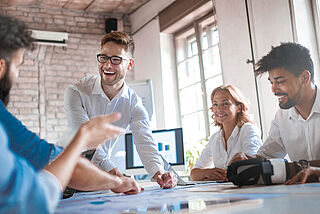
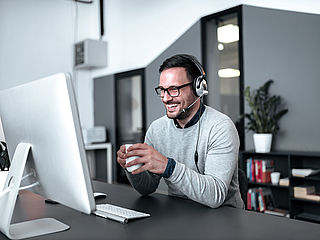
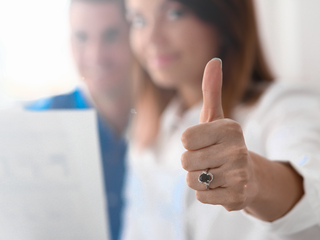
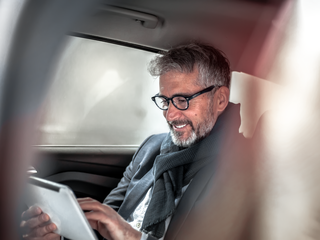
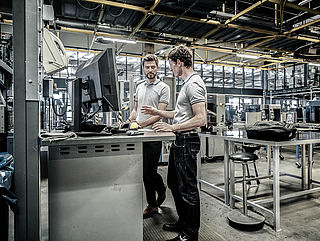
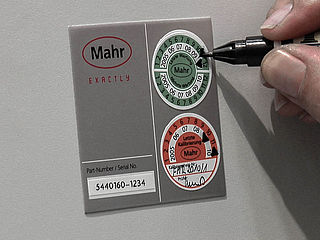
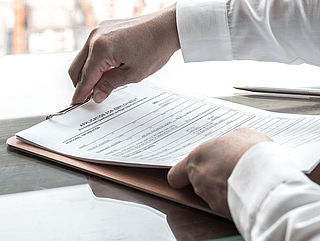
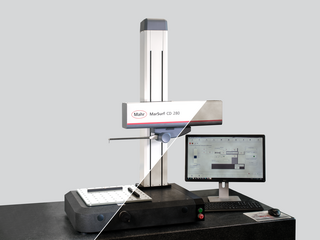
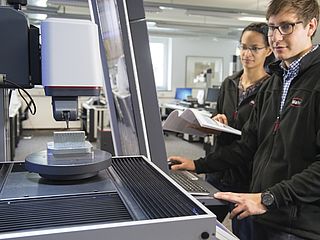
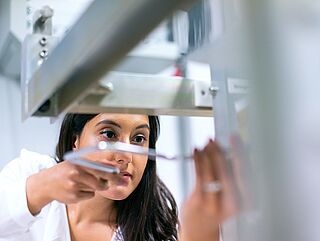
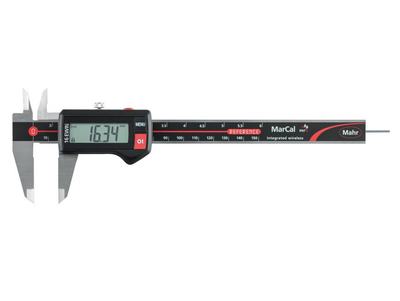
Mahr'dan yenilikçi el tipi ölçüm ekipmanları: Kumpaslar, mikrometre vidaları ve analog indikatörler #96, analogdan dijitale entegre kablosuz aktarımlı modellere. Mahr'ın karşılaştırmalı ölçüm aletleri ve referans standartları vazgeçilmezdir
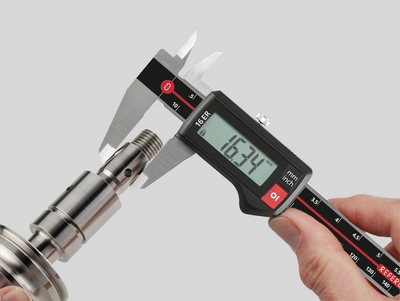
Analogdan dijitale, her çeşit kumpas yelpazesi. Kolay kullanım, kablosuz ve son derece hassas. Üretimde verimli kullanım için mükemmel.
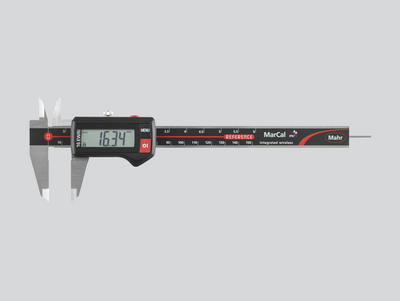
Güvenli, okunması kolay dijital ekran, modern tasarım ve her zamanki Mahr hassasiyeti dijital kumpaslarımızın ayırt edici özelliğidir. Ürün gamında, tüm uygulamalar için ölçüm aletleri bulunur. Veri aktarımı için çeşitli arabirimler ve IP 67'ye kadar koruma derecesi ile karşılanmadık talep kalmaz.
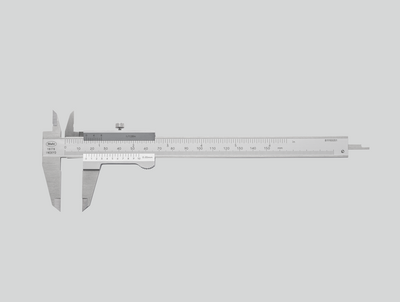
Skalayı korumak ve en yüksek hassasiyeti sağlamak için yansıma önleyici okuma ünitesi, sertleştirilmiş çelik, yükseltilmiş kılavuzlar. Klasik nonius kumpas ile Mahr'dan kaliteli kumpas özellikleri.
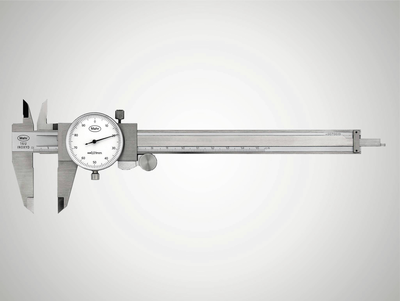
Uzun süreli hassasiyet için büyük, yüksek kontrastlı kadran ve darbeye karşı korumalı ölçüm aleti. Hızlı ve güvenli okuma için denenmiş ve test edilmiş mekanik tasarım.
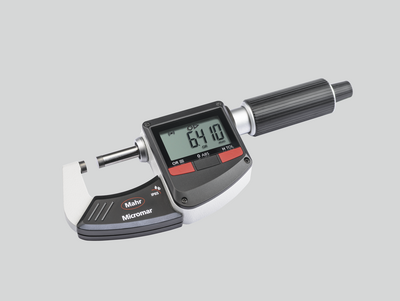
Çeşitli tasarımlarda maksimum hassasiyet. Mahr'ın mikrometre vidaları geleneksel mekanik, dijital ve kablosuz versiyonlarda mevcuttur.
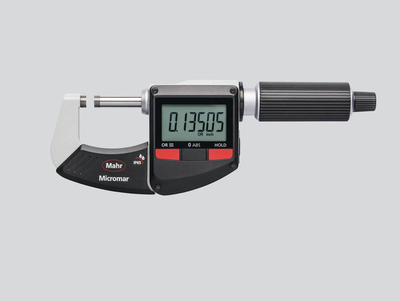
Net dijital ekran, modern tasarım ve her zamanki Mahr hassasiyeti dijital dış mikrometrelerimizin öne çıkan özellikleridir. Ürün gamında, tüm uygulamalar için ölçüm aletleri bulunur. Veri aktarımı için çeşitli arabirimler ve IP 65'e kadar yüksek koruma derecesi ile karşılanmadık talep kalmaz.
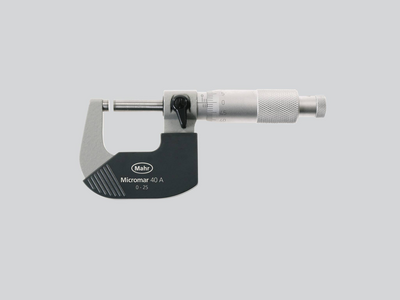
Yansıma önleyici okuma ünitesi, ısı yalıtım plakaları ve maksimum duyarlılık için hassas topraklanmış mil. Mahr'dan kaliteli mikrometre özellikleri.

Seri parçaların (mil, cıvata, şaft) güvenilir ve hızlı testi için özellikle uygundur. Boyutsal hassasiyet, analog komparatörde bir bakışta tanınır ve okunur.
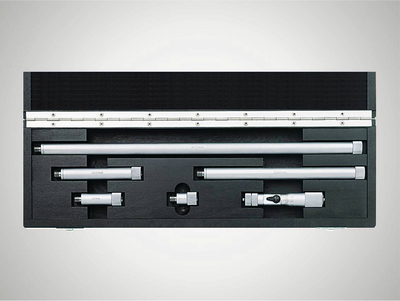
2.500 mm'ye kadar büyük çapları ve test mesafelerini ölçmek için uygundur
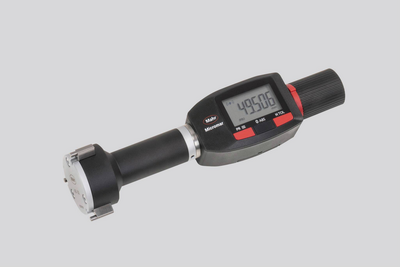
Skalalı veya dijital ekranlı veya tabanca tipi kabzalı hızlı ölçüm aleti olarak mevcuttur. Mahr 3 noktalı iç ölçüm cihazları, otomatik merkezleme sayesinde her zaman güvenilir ölçüm sonuçları sağlar.
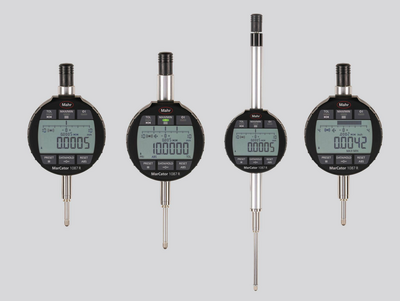
Analogdan dijitale, tüm kadranlı mastar, analog komparatör ve kadran testi indikatörleri yelpazesi. Kolay kullanım, kablosuz (isteğe bağlı), ve son derece hassas. Üretimde verimli kullanım için mükemmel.
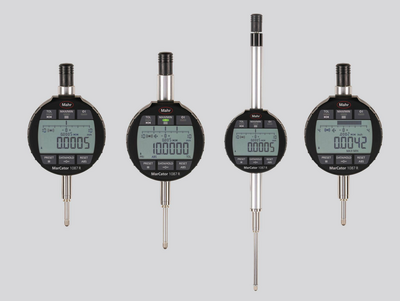
Net dijital ekran, sağlam yapı ve yüksek Mahr hassasiyeti, dijital kadranlı mastarlarımızı niteler. Ürün gamında, tüm uygulamalar için ölçüm aletleri bulunur. Veri aktarımı için çeşitli arabirimler ve IP 54'e kadar koruma derecesi ile karşılanmadık talep kalmaz.
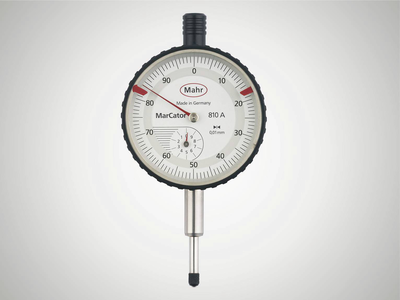
Aşağıdaki özellikler sayesinde yüksek duyarlılık ve hassasiyet: Ölçüm aleti eksenlerinin, hassas dişli çarkların ve pinyonların sağlam montaj bağlantısı, yüksek hassasiyette monte edilmiş ölçüm pimi
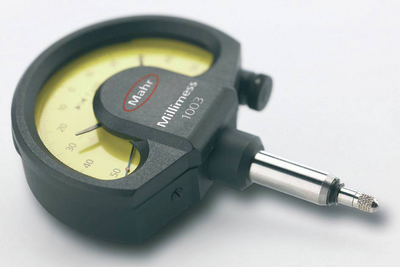
Analog kadranlı indikatörlerle karşılaştırıldığında, Millimess kadran komparatörleri daha da hassas bileşenlere sahiptir, bu da daha iyi ölçüm hassasiyeti ve çok daha iyi bir histerezis hatası sağlar. Bu avantajlar özellikle kaçıklık testlerinde, doğruluk ve düzlük ölçümlerinde ve karşılaştırmalı ölçümlerde belirgindir.
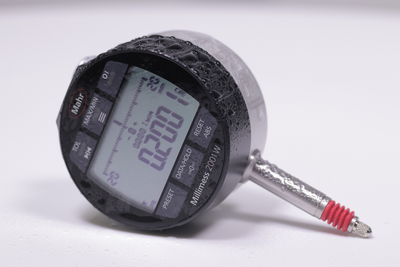
Yüksek hassasiyetli endüktif Millimess analog komparatörler 0,2 μm'ye kadar dijital artışlar yapabilir. Tolerans izleme, dinamik ölçümler için minimum veya maksimum kayıt, birleşik sayısal ve skala ekranı ve kolay veri aktarımı gibi kullanıcı dostu işletim işlevleri, cihazı vazgeçilmez bir hassas ölçüm aleti haline getirir.
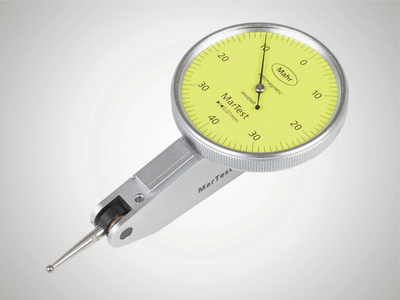
Bilgisayarla optimize edilmiş hassas ölçüm aracı, maksimum güvenilirlik ve hassasiyet sağlar. Zorlu atölye kullanımı için ekran, sertleştirilmiş bir mineral cam panel tarafından çizilmeye veya kırılmaya karşı mükemmel bir şekilde korunur ve ayrıca sızdırmaz, nüfuz eden sıvılara karşı güvenilir koruma sağlar.
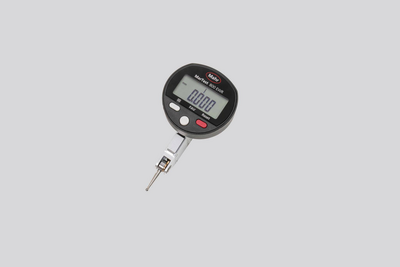
The sensitive computer-optimised measuring tool ensures maximum reliability and precision. For rough workshop use, the display is superbly protected. A seal also provides reliable protection against penetrating liquids.
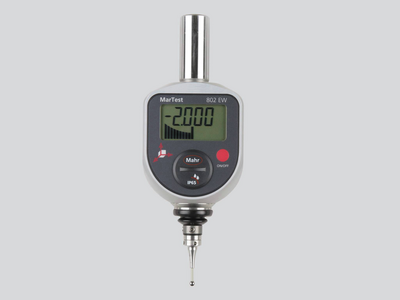
NC tezgahları, işleme merkezleri ve aşındırma tezgahları için Mahr 3D ölçüm probları, kurulum ve arıza sürelerini kısaltır. İş parçaları ve fikstürlerdeki referans kenarlarına hassas şekilde temas etmek için mükemmeldir.
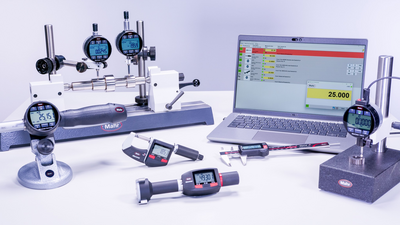
Entegre Kablosuz, harici kablosuz modüller, USB, Opto RS232 veya Digimatic olsun: Kullandığınız arabirim standardından bağımsız olarak MarConnect, her zaman en iyi bağlantıyı sağlar.
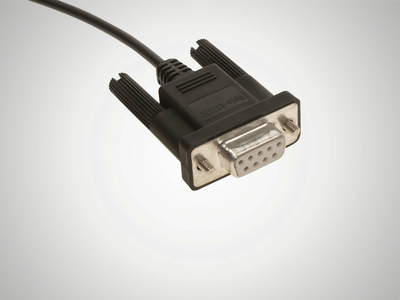
Birçok Mahr hassas mastarı, MarConnect arabirimi ile bir veri çıkışına sahiptir. USB, Opto RS232 veya Digimatic; kullandığınız arabirim standardından bağımsız olarak MarConnect, her zaman en iyi bağlantıyı sağlar.
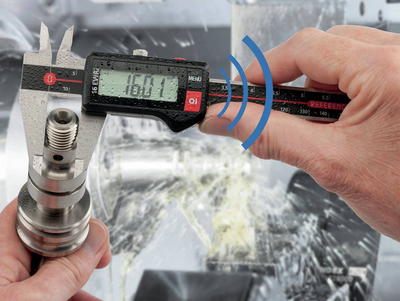
Mahr'ın Kablosuz serisi, tam mobilite ile hassas ölçüm sonuçları sağlar. Kablolu teknolojinin kısıtlamaları olmadan ölçmenin modern ve kolay yolu.
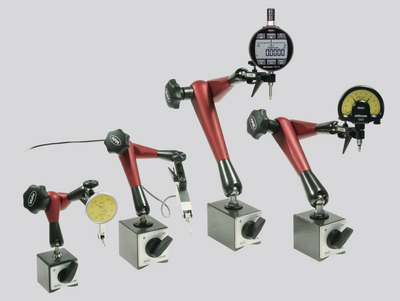
MarStand ölçüm tripodları, ölçüm tablaları ve radyal salgı mastarları, hassas ölçüm sonuçlarının dayanağı olan yüksek stabilite sunar. Analog indikatörleriniz, analog komparatörleriniz, analog test indikatörünüz, ölçüm cihazlarınız ve ölçüm problarınız için gerekli desteği sunarlar.
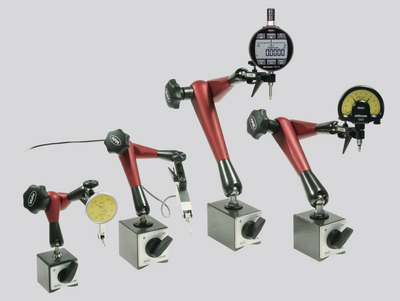
Ölçüm tripodları, kararlı tasarımları sayesinde hassas ölçüm sonuçları için dayanak sağlar. Analog indikatörleriniz, analog komparatörleriniz, analog test indikatörünüz, ölçüm cihazlarınız ve ölçüm problarınız için gerekli desteği sunarlar.
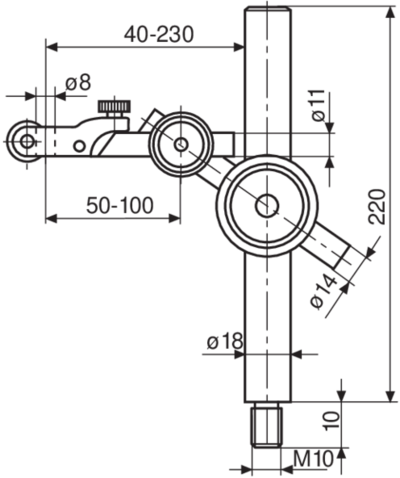
MarStand direk ve destek tertibatları, bağımsız çözümler için kullanılır ve hassas ölçüm sonuçları için gerekli olan yüksek stabilite sunar. Analog indikatör, analog komparatör, analog test indikatörü ölçüm cihazları ve ölçüm probları için gerekli desteği sunarlar.
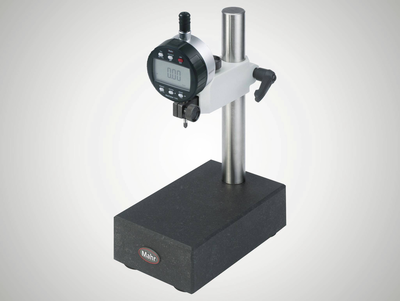
Ölçüm tablaları, hassas ve seviyeli bir ölçüm tablasını, sabit bir ölçüm sütununu ve güçlü kol parçalarını birleştirir. MarStand ölçüm tablaları, ekstra kararlı tasarımları sayesinde hassas ölçüm sonuçları için dayanak sağlar.
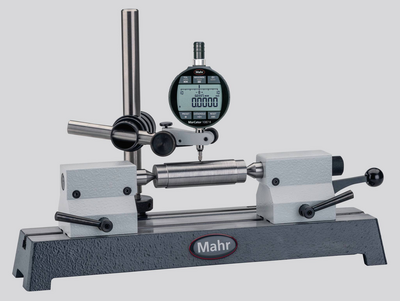
Radyal salgı mastarları, üretime yakın bir ortamda millerdeki konum ve biçim hatalarını tespit etmenin en basit yöntemidir. Model çeşitliliği nedeniyle, sağlam MarStand radyal salgı mastarları, çok çeşitli iş parçası gereksinimleri ve hassas ölçüm sonuçları için temel oluşturur.
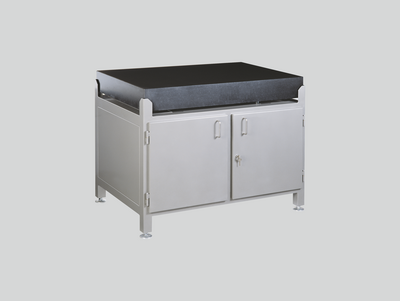
Sert granitten yapılmış test plakaları, plakaların yüksek mukavemeti ve boyutsal kararlılığı nedeniyle yükseklik ölçüm aletleriniz için mükemmel bir yüzeydir.
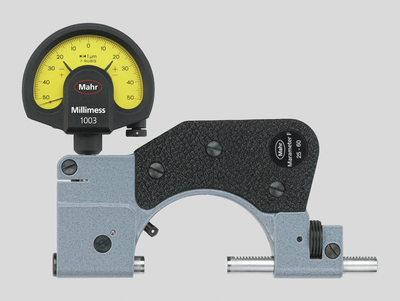
Gösterge mastarlarının karşılaştırmalı mastarlar olarak kullanılması, üretimde hassas ölçümler için mükemmel bir araçtır. Mastarı bir referans standardına ayarlamak sapma marjını azaltır ve sıcaklık dalgalanmalarının ölçüm sonucu üzerindeki etkisini en aza indirir.
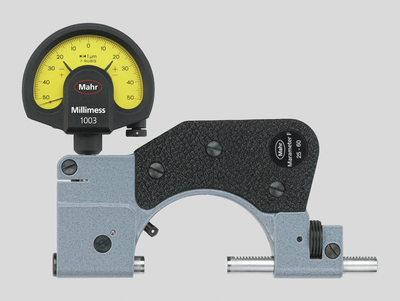
Hassas ibre tutma mastarları, özellikle seri parçalar üzerinde güvenli ve hızlı testler için mil, cıvata ve şaft gibi silindirik parçaların hassas ölçümleri için mükemmel ölçüm araçlarıdır. Boyutsal hassasiyet, komparatörde bir bakışta tanımlanır ve okunur.
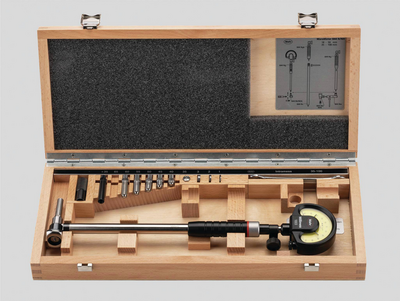
İç ölçüm cihazları, deliklerin çap, yuvarlaklık ve konikliğinin hassas bir şekilde ölçümü için mükemmel araçlardır.
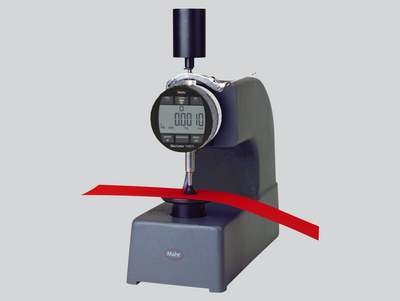
Kalınlık ölçerlerimiz, çeşitli film, sac ve levhaların özellikle hızlı ölçümü için sağlam ve basit bir aralık sunar.
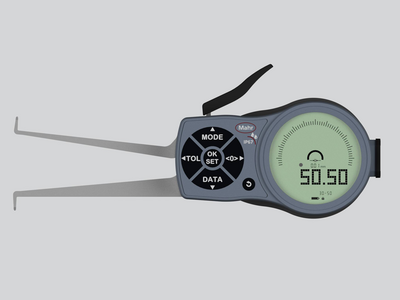
İş parçası geometrisi nedeniyle kumpas veya iç mikrometre vidaları gibi yaygın ölçüm aletleri kullanılamıyorsa kumpas mastarları mükemmel çözümdür!
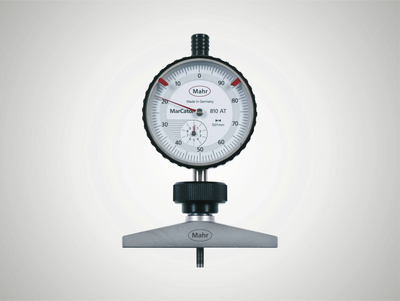
Derinlik mastarlarımız, özellikle hızlı derinlik ölçümleri için sağlam ve basit bir aralık sunar. 8 mm'lik montaj mili, ölçüm görevine göre analog indikatör, komparatör ve probların kullanımına uygundur.
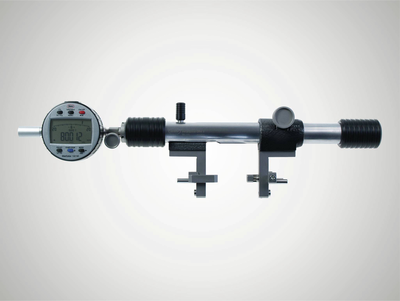
Çok amaçlı ölçüm aletleri, üretimde hassas ölçümler için mükemmel ortaklardır, çünkü bir referans standartla karşılaştırmalı ölçüm, sıcaklık dalgalanmalarının ölçüm sonucu üzerindeki etkisini en aza indirir.
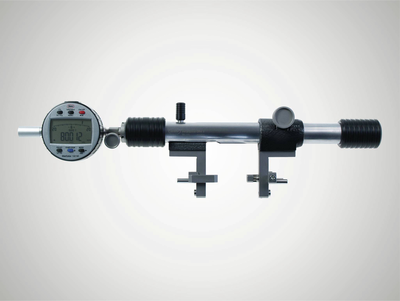
Dişli, diş, konik veya girinti fark etmez. Multimar çok amaçlı ölçüm aletleri, standart ölçüm aletlerinin uygun olmadığı hemen hemen tüm iç ve dış ölçümler için ideal bir çözümdür. Temel ünite seçenekleri ve geniş bir aksesuar yelpazesi mevcuttur.
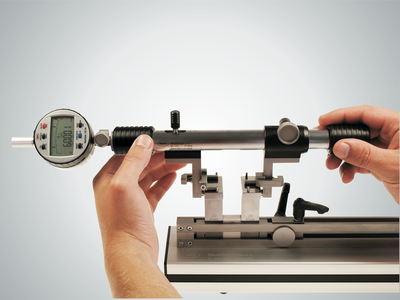
İç ve dış çap ölçüm aletlerinizi doğru şekilde ayarlayın. 844 S ayar aletlerini kullanırken daha büyük boyutlar için bile her ölçüm görevi amacıyla mükemmel bir donanıma sahipsiniz.
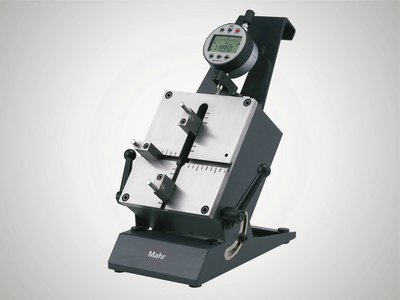
Merkezleme omuzları, dar bilezikler, veya girintiler fark etmez: Multimar 36B çok amaçlı ölçüm aletleri, neredeyse tüm iç ve dış ölçümler için ideal bir çözümdür. Temel ünite seçenekleri ve geniş bir aksesuar yelpazesi mevcuttur.
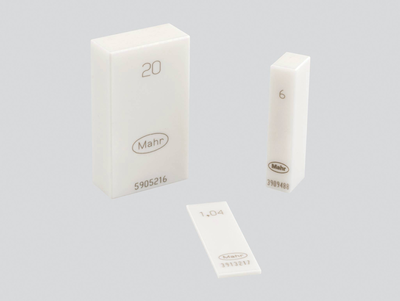
Mahr'ın ayar standartlarına ve mastarlarına güvenin – çünkü bunlar hassas ölçüm sonuçlarının dayanağıdır.
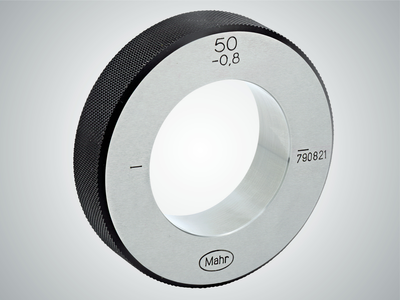
Mahr'ın ayar standartlarına güvenin, çünkü bunlar hassas ölçüm sonuçlarında referans olarak kullanılır
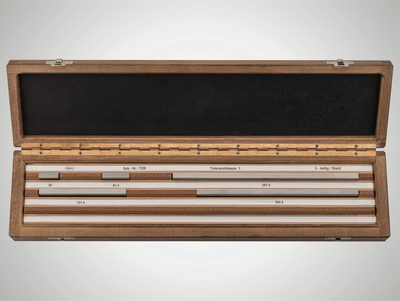
Mahr mastar blokları, yüksek kaliteli referans ve çalışma standartlarına sahip olmanızı sağlar. Atölyenizin, üretiminizin veya kalite güvencenizin gereksinimlerine uygun dört tolerans sınıfı ve iki malzeme arasından seçim yapın.
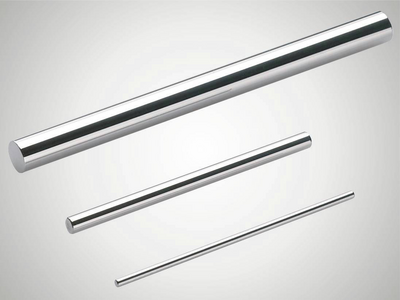
Mahr pim mastarları üç tolerans sınıfında ve çeşitli tasarımlarda mevcuttur. Atölyenizin, üretiminizin veya kalite güvencenizin gereksinimlerine uygun cihazı seçin.
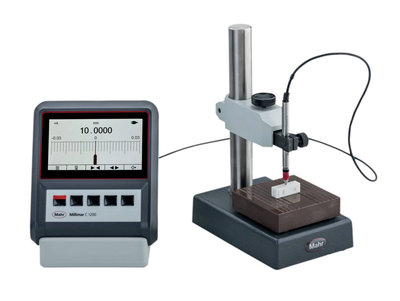
Elektriksel uzunluk ölçüm aletlerinin gereksinimleri, uygulamaları kadar çeşitlidir. Mükemmel güvenilirlik, hassasiyet ve kolay kullanım aranır.
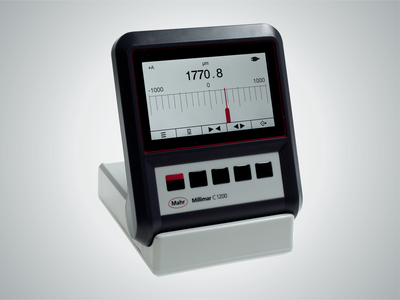
Elektriksel uzunluk ölçüm aletlerinin gereksinimleri, uygulamaları kadar çeşitlidir. Mükemmel güvenilirlik, hassasiyet ve kolay kullanım aranır. Millimar kompakt ve sütun ölçüm aletleri, bu gereksinimleri karşılamaktadır.
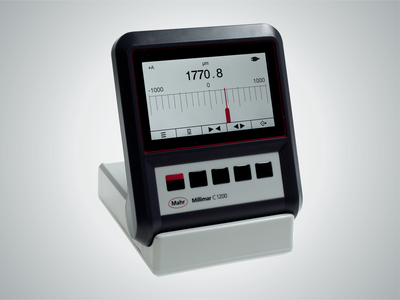
Millimar uzunluk ölçüm aletleri kompakt, sağlam ve kullanımı kolaydır. Üretim alanında ve ölçüm odasında yönetilebilir karmaşıklıktaki görevleri ölçmek için çok yönlü değerlendirme ve görüntüleme aletleridir.
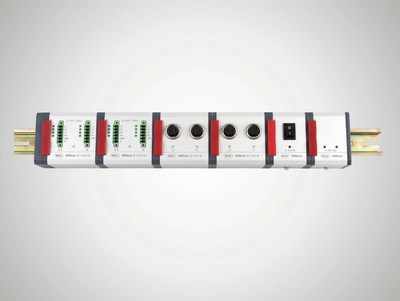
Modüllerin ve yazılımın farklı kombinasyon seçenekleri, çalışma ortamını ve araçları her zamankinden daha farklı olarak tasarlama fırsatı sunar.
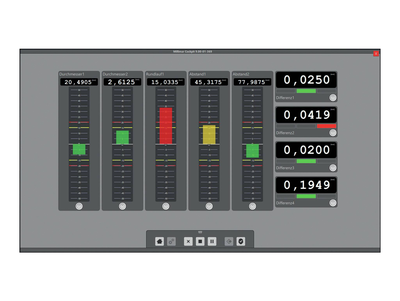
Smart and universally applicable software for complex measurement tasks in the manufacturing sector
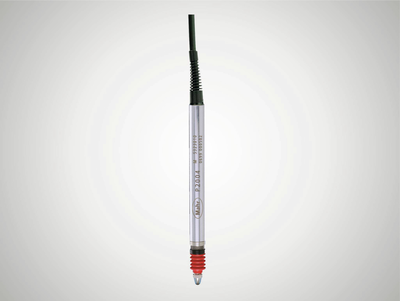
Millimar dönüştürücüler, bir ölçüm zincirinin en önemli bileşenleridir. Özellikleri, tüm ölçümün kalitesini belirler. Uygulamaya bağlı olarak bu amaç için çeşitli teknolojiler mevcuttur. Örneğin Millimar endüktif ölçüm probları: Bu ürünler dayanıklı, çok yönlü ve cazip fiyatlıdır.
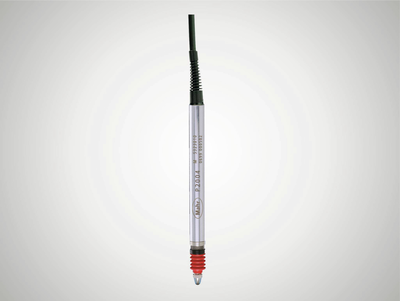
Kalınlık ölçümü, radyal kaçıklık veya eş merkezlilik fark etmez: Endüktif problarla, şekil, destek veya radyal kaçıklık sapmalarından bağımsız olarak ölçülen değerleri ve sapmaları kaydedebilirsiniz. Büyük avantajları, geniş doğrusallık aralığı ve parazite karşı göreceli duyarsızlıktır. Problar esas olarak üretimde karşılaştırmalı ölçümler için kullanılır, ancak sensörün belirli görevleri değişebilir.
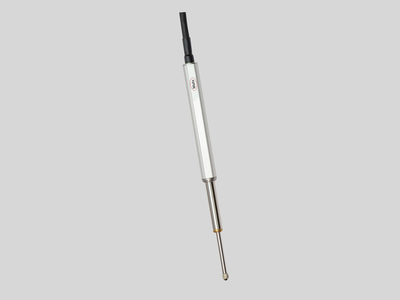
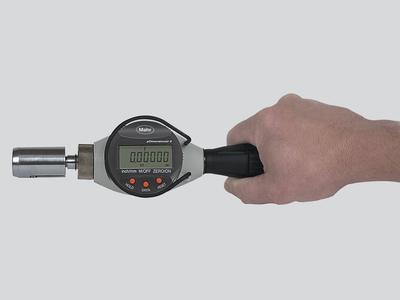
Pnömatik uzunluk ölçüm aletleri, yüksek hassaslıkları ve uzun vadeli kararlılıkları ile bilinir. Ölçüm nozulları ile temassız ölçüm, iş parçalarına zarar vermez. Temizlenmemiş, üzerinde madde bulunan, yağlanmış veya kaplanmış iş parçaları bile
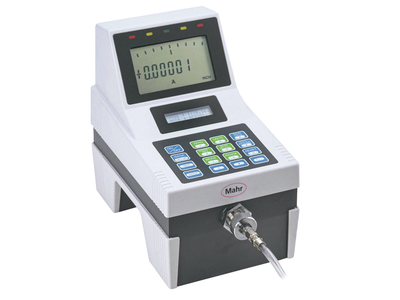
Millimar uzunluk ölçüm aletleri kompakt, sağlam ve kullanımı kolaydır. Üretim alanında yönetilebilir karmaşıklıktaki görevleri ölçmek için çok yönlü görüntüleme ve değerlendirme cihazlarıdır.
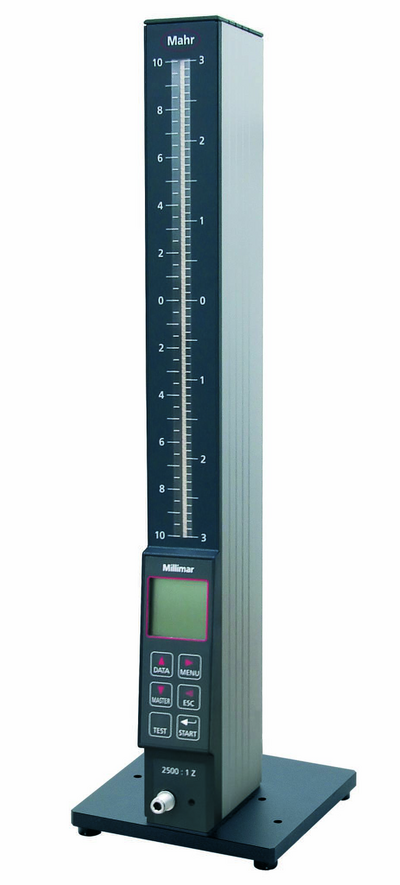
Ölçüm sonuçları 101 adet üç renkli LED üzerinde görüntülenir ve uzaktan kolayca okunabilir. Programlanabilir uyarı ve tolerans sınırları aşıldığında, segmentlerin renkleri yeşilden sarıya veya kırmızıya değişir.
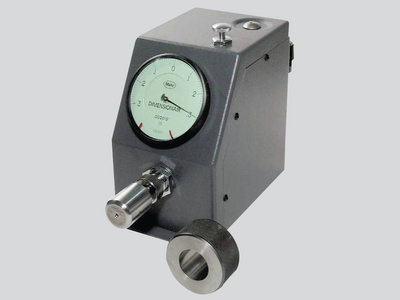
Millimar pnömatik ölçüm cihazları, boyutsal sapmaları hızlı ve doğru bir şekilde kaydeder. Endüstriyel üretim ve ölçüm odaları konusunda uzun yıllardır kendini kanıtlamıştır.
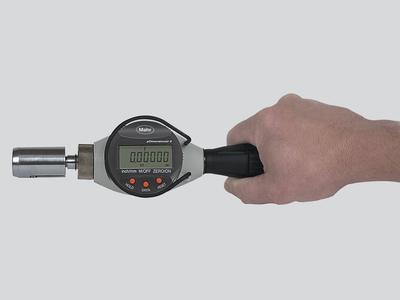
Hareket halindeyken ölçüm ve değerlendirme için.
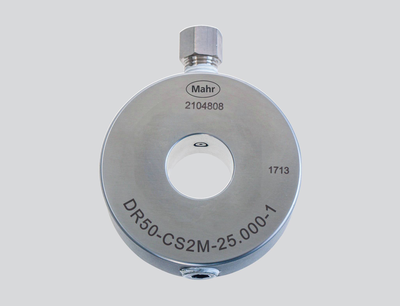
Pnömatik ölçüm halkaları kullanarak temassız ölçüm, iş parçalarına zarar vermez.
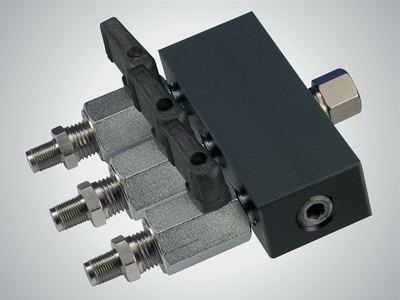
Hava ölçüm teknolojisi için aksesuarlarla ölçüm istasyonunu ölçümünüze uyarlayın.
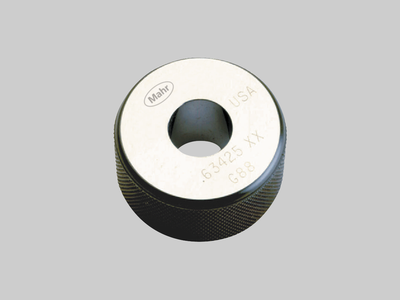
Mahr'ın ayar standartlarına güvenin, çünkü bunlar hassas ölçüm sonuçlarında referans olarak kullanılır
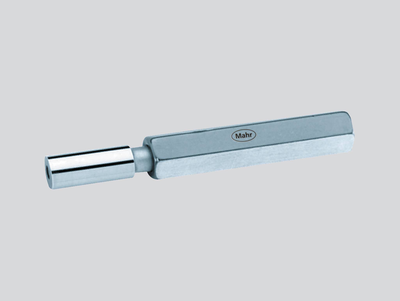
Pnömatik ölçüm aletleri ayarı (nozul halka mastarlar) Titizlikle sertleştirilmiş, eskitilmiş, tornalanmış ve bindirilmiş.
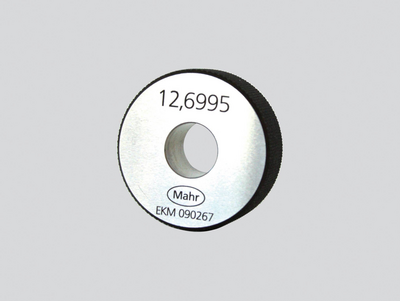
Pnömatik ölçüm aletleri ayarı (nozul delik mastarları) Titizlikle sertleştirilmiş, eskitilmiş, tornalanmış ve bindirilmiş.
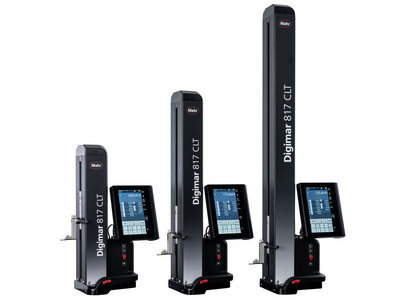
Ölçümlerinizle yüksekleri hedeflemek ister misiniz? Digimar tam size göre!
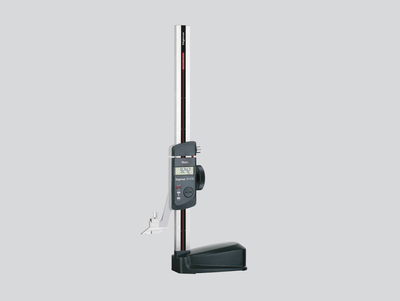
Atölyede iş parçalarını çizmek ve işaretlemek için. Yükseklik ve mesafelerin kolay ölçümü.
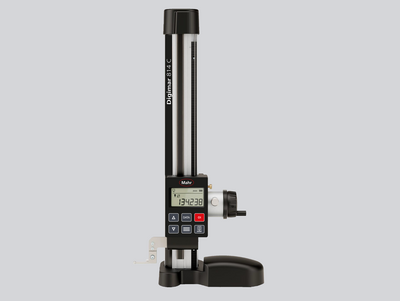
Practical measurement modes and options: The Digimar 814 C makes typical measurement tasks easy
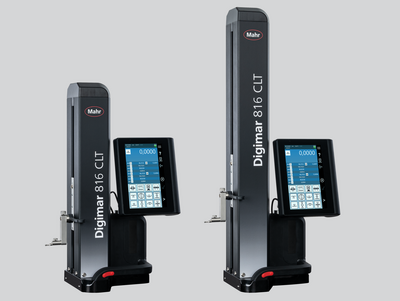
Touch operation, ergonomic handling and a wide range of evaluation options: This is what the Digimar 816 CLT height measuring device stands for.
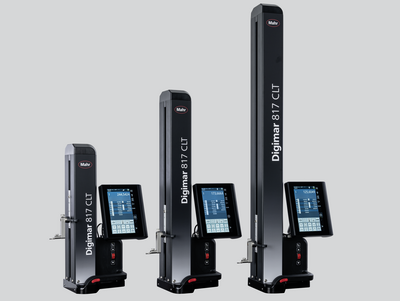
Touch operation, ergonomic handling and a wide range of evaluation options: This is what the Digimar 817 CLT height measuring device stands for.
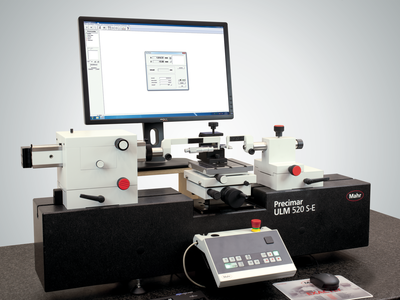
Hassas uzunluk metrolojisi, hem mutlak hem de bağıl ölçümler için yüksek hassasiyetli boyut metrolojisi anlamına gelir.
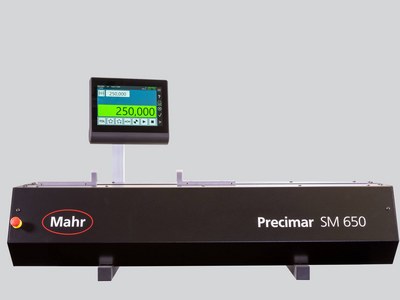
Atölye için çok amaçlı, kullanımı kolay uzunluk ölçüm ve ayar cihazları
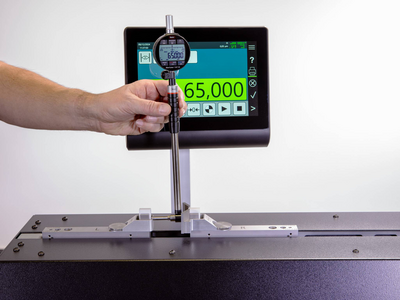
Atölye için çok amaçlı, kullanımı kolay uzunluk ölçüm ve ayar cihazları
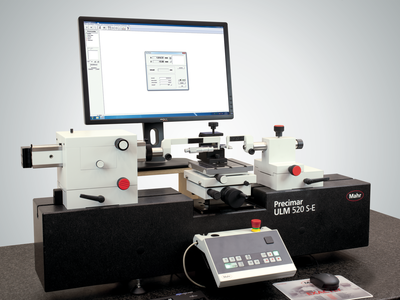
Basit mastar blok test standı, tam otomatik komparatör test standı ve ULM cihazlarından ultra hassas ve kısmen otomatikleştirilmiş CiM çok amaçlı ölçüm makinesine kadar geniş ürün yelpazesi sayesinde Mahr, üretim, ölçüm odaları ve kalibrasyon laboratuvarları için her zaman pratik çözüm sunar. Diğer bir ifadeyle: Maksimum hassaslık ve son derece verimli ölçüm süreçleri bir arada.
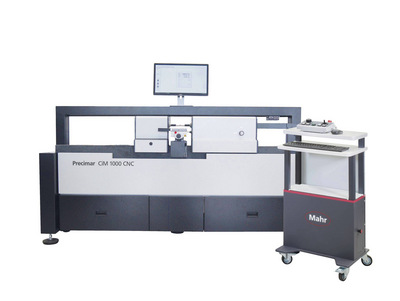
İster klasik ULM ister motorlu PLM ve CiM aletleri. Mahr çok amaçlı uzunluk ölçüm makineleri, minimum belirsizlikle kullanıcı dostu, hızlı ve güvenilir ölçüm sağlar.
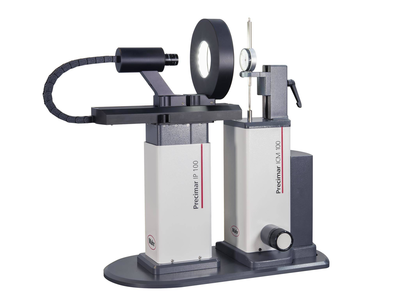
Analog indikatörlerin, analog test indikatörlerin ölçüm cihazlarının, analog komparatörlerin ve probların yarı otomatik ve tam otomatik testi verimli ve hassas bir şekilde yapılır.
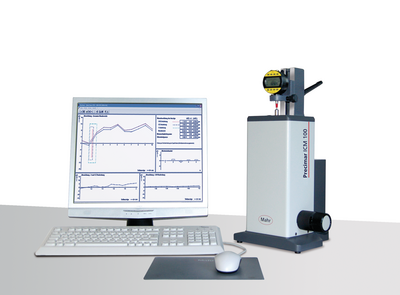
Analog indikatörlerin, analog test indikatörlerin ölçüm cihazlarının, analog komparatörlerin ve probların yarı otomatik ve tam otomatik testi verimli ve hassas bir şekilde yapılır.
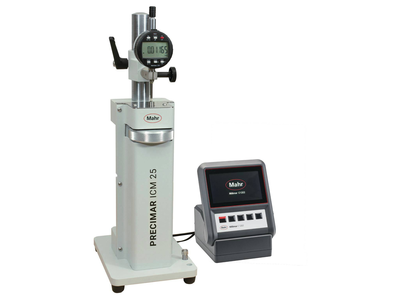
Manual testing of dial gages, dial test indicators and comparators - easy and precise
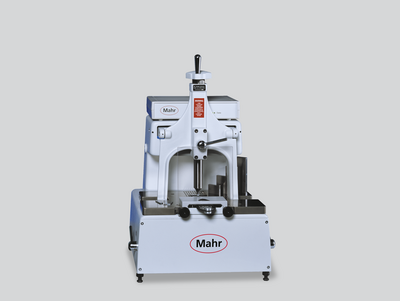
Mahr mastar blok karşılaştırıcılarına güvenin, çünkü bunlar, standartlarınızın hassas şekilde test edilmesinin dayanağıdır
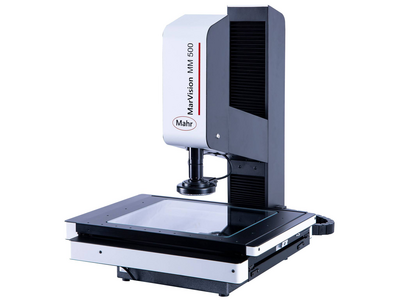
Mikroskoplar, hemen hemen tüm sektörlerde mesafe, yarıçap ve açıların hızlı bir şekilde incelenmesi için kullanılır. Laboratuvarda veya üretim alanına yakın metroloji.
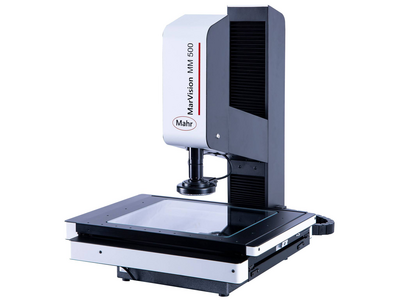
Mikroskoplar, hemen hemen tüm sektörlerde mesafe, yarıçap ve açıların hızlı bir şekilde incelenmesi için kullanılır. Laboratuvarda veya üretim alanına yakın metroloji.
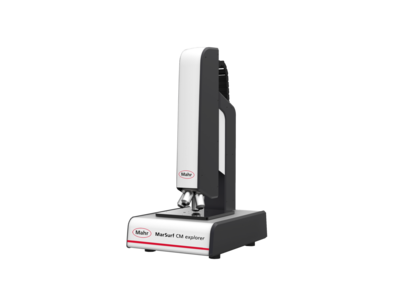
Endüstri ve araştırma için yüzey metrolojisi
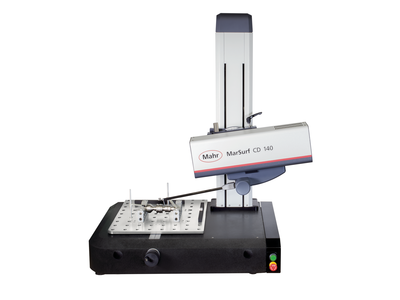
Sıkı toleranslara sahip yapılandırılmış işlevsel yüzeylerde, bir iş parçasının veya nesnenin topografisini kısa bir alanda minimum sürede kaydeden yüksek hassasiyetli ölçüm sistemleri gerekir.

Kaba şekil sapmalarını belirlemek için kontur ölçüm teknolojisi kullanılır.

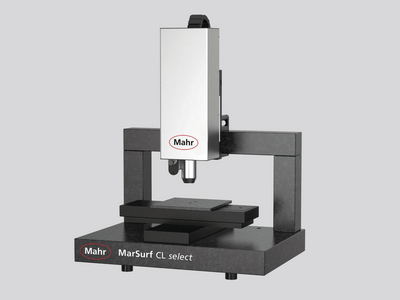
Optik ölçüm aletleriyle konturları hassas bir şekilde ölçün
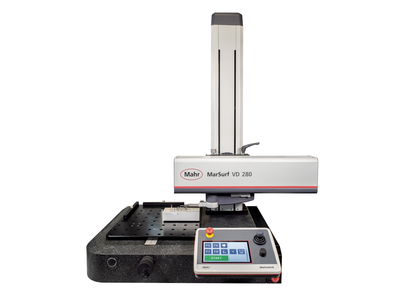
Kontur ve pürüzlülük ölçümü bir arada: Profesyonel çok yönlü
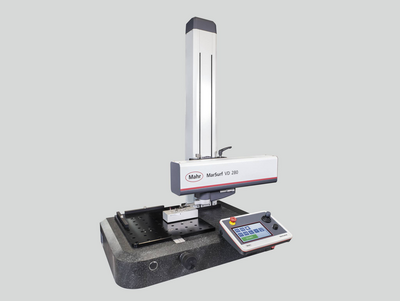
Kontur ve pürüzlülük ölçümü bir arada: Profesyonel çok yönlü
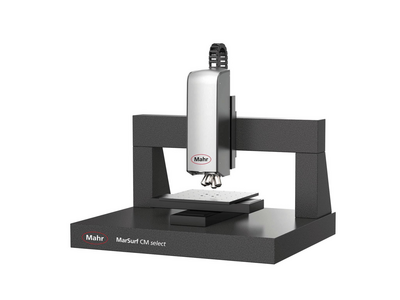
2D/3D Kontur ölçümü ve ayrıca ISO 25178 / ISO 4287'ye göre pürüzlülük ölçüm aksesuarları
Endüstri ve araştırma için 3D yüzey metrolojisi
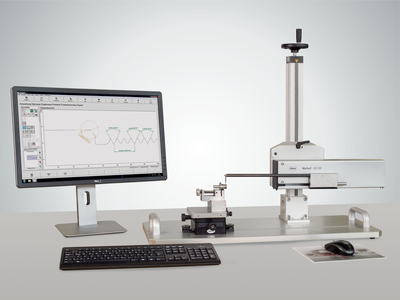
Mobil ölçüm cihazları ile her yerde ölçüm yapın!
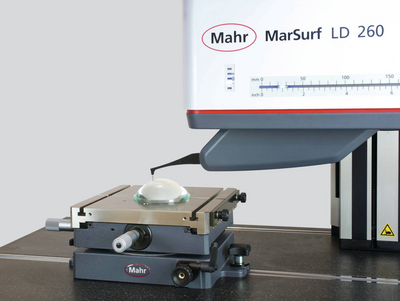
Yüksek hassasiyetli objektiflerin ölçümü için ölçüm istasyonları
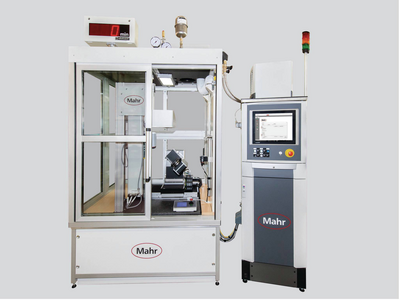
Standart çözümler artık yeterli olmadığında: Bağımsız özelleştirilmiş çözümler
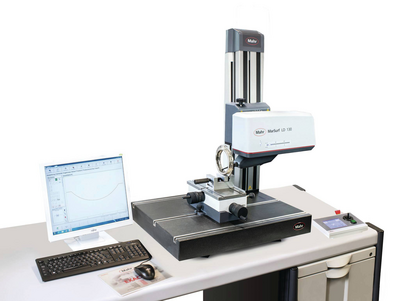
Sıkı toleranslara sahip yapılandırılmış işlevsel yüzeylerde, bir iş parçasının veya nesnenin topografisini kısa bir alanda minimum sürede kaydeden yüksek hassasiyetli ölçüm sistemleri gerekir.
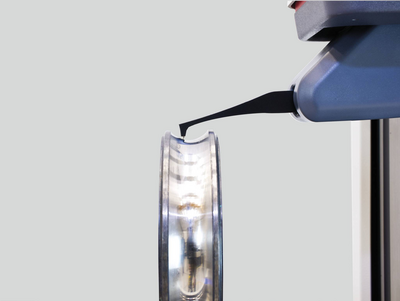
Ölçüm odalarında ve laboratuvarlarda çok yönlü ve güçlü kullanım
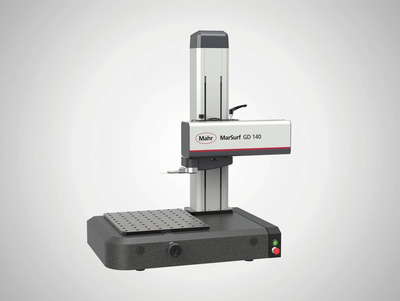
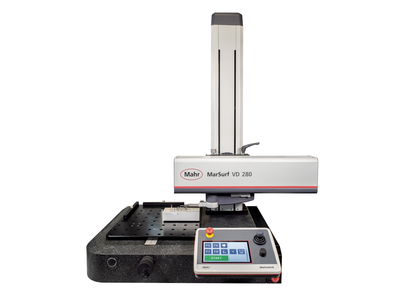
Kontur ve pürüzlülük ölçümü bir arada: Profesyonel çok yönlü
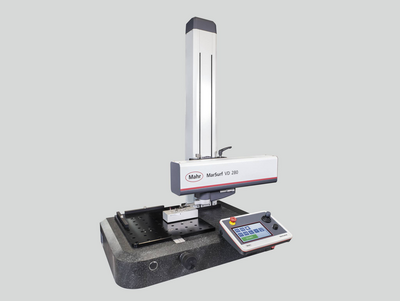
Kontur ve pürüzlülük ölçümleri için temaslı ölçüm istasyonları
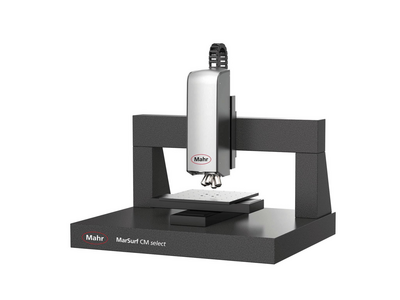
ISO 25178 / ISO 4287'ye göre 2D/3D kontur ve pürüzlülük ölçüm aksesuarları
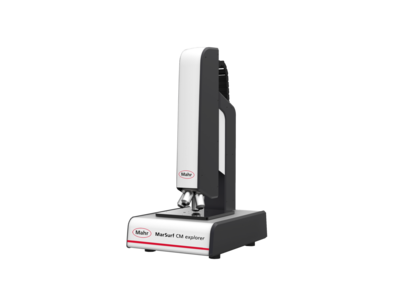
Endüstri ve araştırma için 3D yüzey metrolojisi
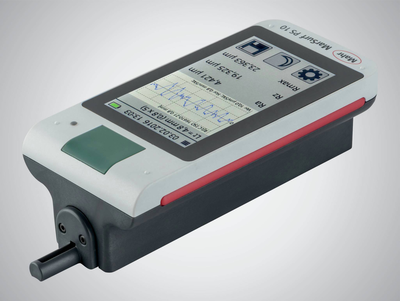
Mobil ölçüm cihazları ile her yerde ölçüm yapın!
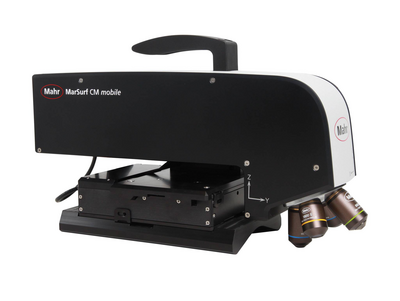
Kullanım için çok yönlü
mobil 3D yüzey metrolojisi
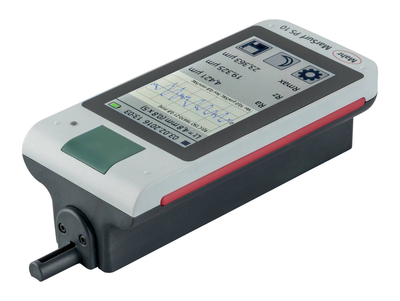
Mobil ölçüm aletleri, sonuçlara tam olarak ihtiyaç duyduğunuz yerde ölçüm yapmanızı sağlar.
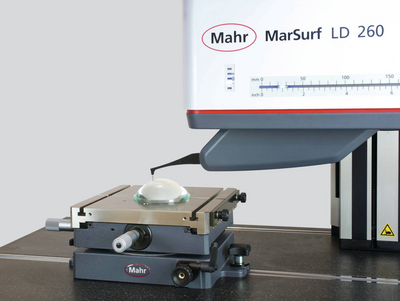
Ultra yüksek hassasiyetli objektiflerin ölçümü için ölçüm istasyonları
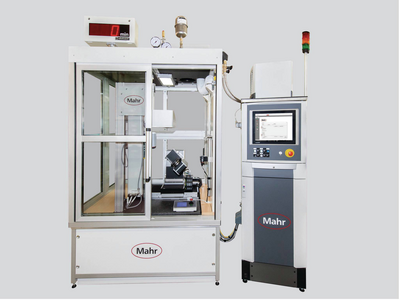
Standart çözümler artık yeterli olmadığında: Bağımsız özelleştirilmiş çözümler
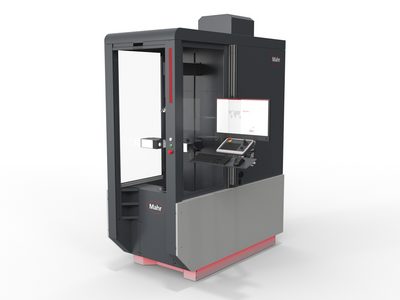
Metrology
Experience outstanding features combined with extreme flexibility in workpiece size and increase your productivity in the production environment.
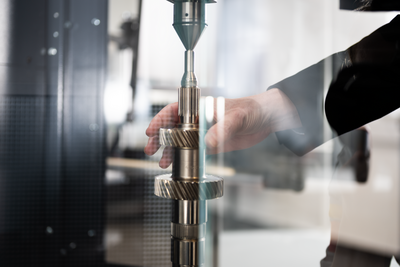
Flexible measurement of workpieces that can be clamped between centers
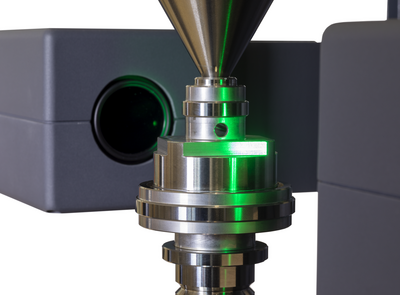
High resolution and very fast matrix camera for measuring a large number of features on rotationally symmetrical workpieces.
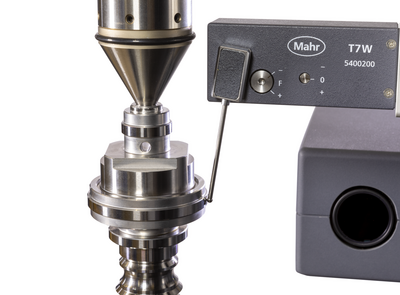
Fast optical matrix camera in combination with high-precision touch probes for measuring a large number of features on rotationally symmetrical workpieces.
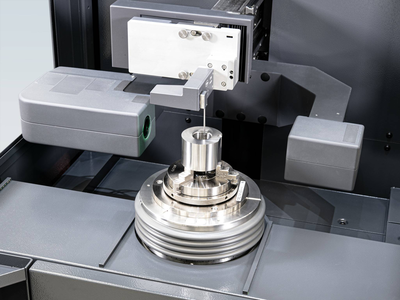
Flexible clamping options and high-precision alignment using a fully automatic centering and tilting table
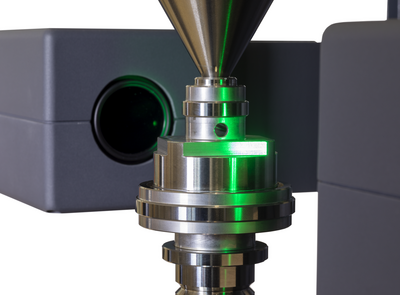
High resolution and very fast optical matrix camera for measuring a wide range of rotationally symmetrical workpieces. Addition of a fully automatic centering and tilting table for extremely fast, mechanical alignment and flexible clamping options.
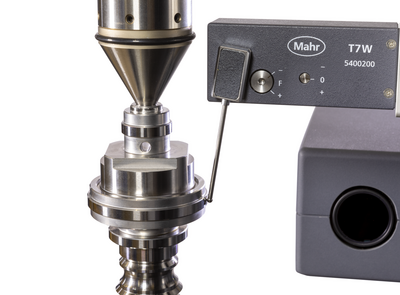
Fast optical matrix camera in combination with high-precision touch probes for measuring a large number of features on rotationally symmetrical workpieces. Addition of a fully automatic centering and tilting table for extremely fast, mechanical alignment, flexible clamping options and, for example, internal measurements.
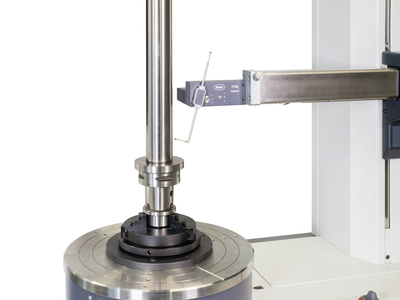
Yuvarlaklık, düzlük, doğrusallık, eş eksenlilik ve diğer ölçüm görevleri gibi form ve konum toleranslarını test etmek için sistemler. Manuelden tam otomatiğe.
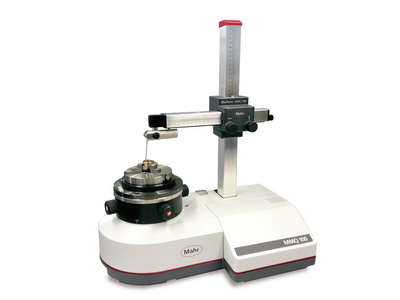
Cihaz yuvarlaklık, düzlük ve eş merkezlilik gibi özellikleri kolay, uygun maliyetli ve yüksek hassasiyetle ölçer. Manuel form ölçüm aletlerimiz hem ölçüm odası hem de üretime yakın ölçümler için uygundur.
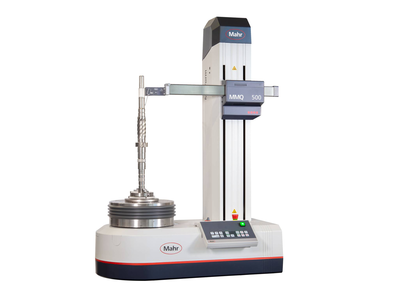
Otomatik form ölçüm sistemlerimizle, en yüksek otomasyon, esneklik ve hassasiyet seviyesine sahip kararlı, yenilikçi cihazlar aracılığıyla denetim maliyetlerinizi artırmadan süreç maliyetlerinizi düşürürsünüz.
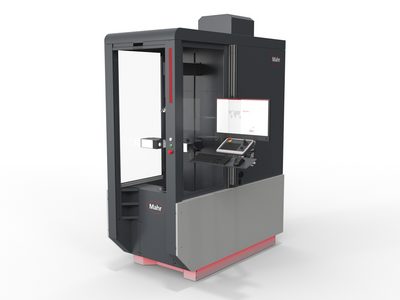
metrology
Experience outstanding features combined with extreme flexibility in workpiece size and increase your productivity in the production environment.
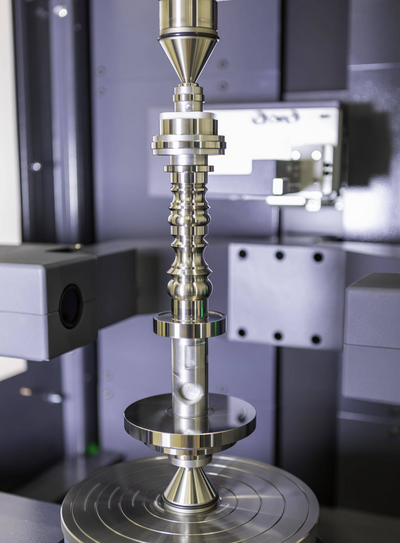
Flexible measurement of workpieces that can be clamped between centers
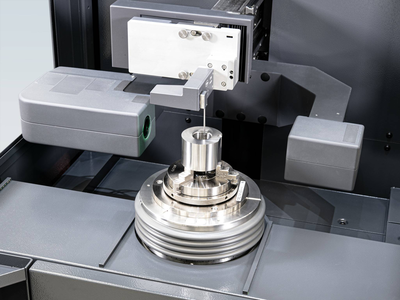
Flexible clamping options and high-precision alignment using a fully automatic centering and tilting table
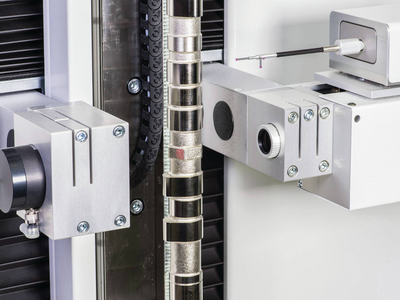
Zorlu üretim ortamlarında kullanım için optik ve temaslı mil ölçüm sistemleri. Tüm yaygın döner simetrik iş parçalarının eksiksiz ölçümü.
.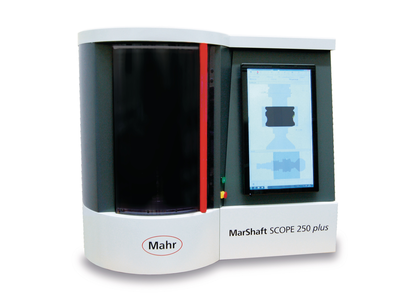
Zorlu atölye ortamlarında kullanım için çok amaçlı, tam otomatik ve sağlam optik mil ölçüm makineleri.
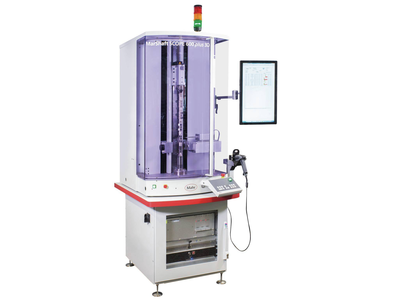
Zorlu üretim ortamlarında kullanım için optik ve temaslı mil ölçüm sistemleri. Tüm yaygın döner simetrik iş parçalarının eksiksiz ölçümü.
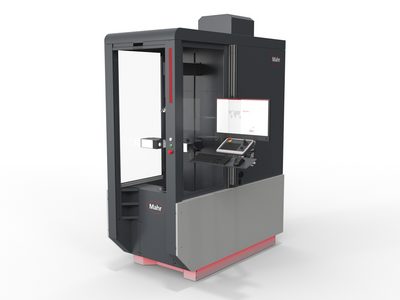
Metrology
Experience outstanding features combined with extreme flexibility in workpiece size and increase your productivity in the production environment.
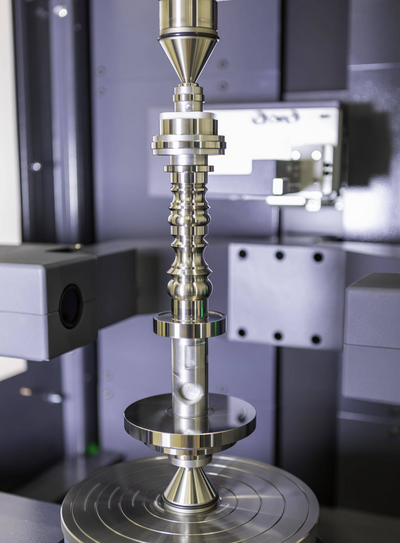
Flexible measurement of workpieces that can be clamped between centers
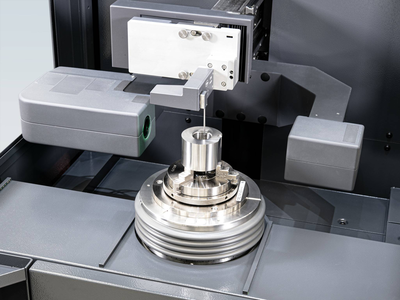
Flexible clamping options and high-precision alignment using a fully automatic centering and tilting table
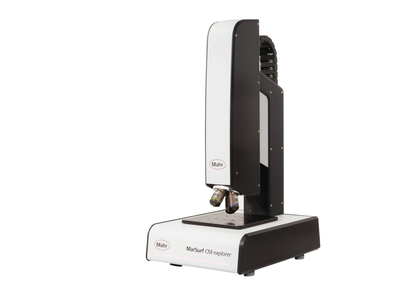
Yüzeylerin ve geometrilerin hızlı ve temassız kaydı için geniş teknoloji ve ürün yelpazesi.
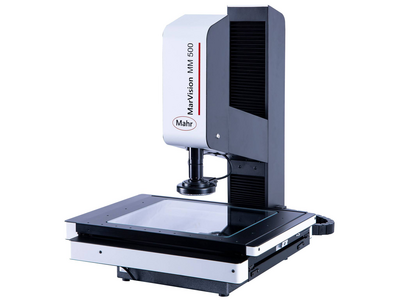
Mikroskoplar, hemen hemen tüm sektörlerde mesafe, yarıçap ve açıların hızlı bir şekilde incelenmesi için kullanılır. Laboratuvarda veya üretim alanına yakın metroloji.
Pürüzlülük, kontur ve diğer birçok yüzey parametrelerinin belirlenmesi.
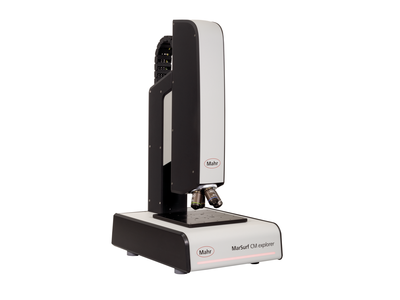
Endüstri ve araştırma için yüzey metrolojisi
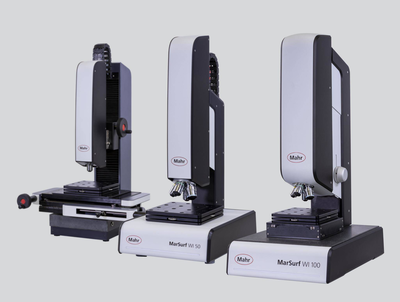
Nanometreye kadar hassas minimum pürüzlülük
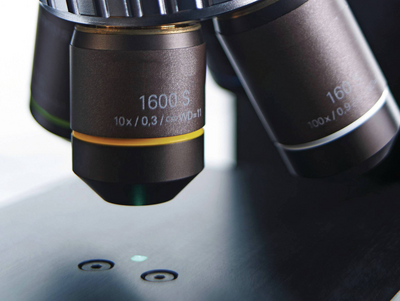
Yüzey topografyalarının ve geometrilerinin optik analizi
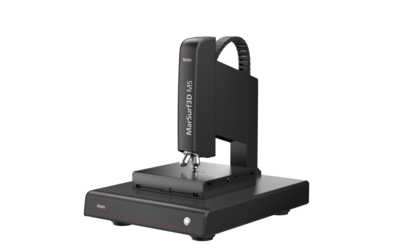
Surface metrology for industry and research
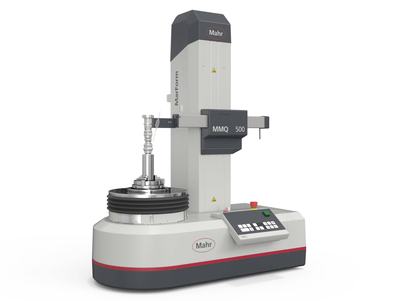
Kanıtlanmış Mahr kalitesinde yenilenmiş sistemler
Solution in a box
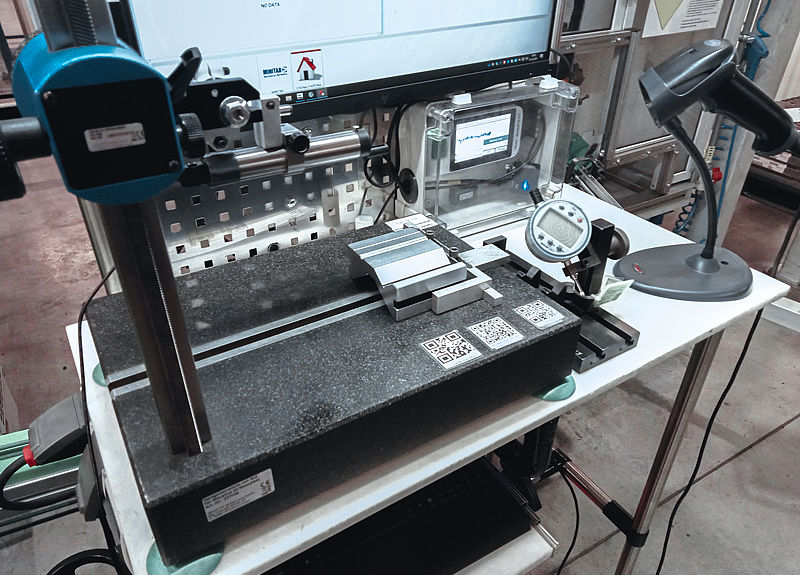
Valves are among the most important components of an internal combustion engine: they ensure the intake of the air-fuel mixture into the combustion chamber and at the same time provide a controlled exhaust of the gas. This requires the valves to be hermetically sealed and reliably close the openings of the combustion chamber. This is achieved by elaborate polishing of the valve seat in particular, so that it achieves a precise smoothness.
Testing critical surfaces
Eaton Automotive Systems Sp. z o.o. in Bielsko-Biała / Poland therefore regularly checks the quality of the valve seats before, during and after production. "These surfaces are essential for the functioning of a valve in the engine and are classified as highly critical by our customers," explains Wojciech Liro, Measurement Systems Specialist at Eaton. In addition to vehicle and aircraft components, the global engineering company also develops and sells systems for mobile and industrial hydraulics, power distribution and electrical systems.
Intuitive measurement with the MarSurf M 310
Eaton's valves are made of special valve steels such as EMS-1 or EMS-296, and in order to accurately measure the roughness of their valve seats, Wojciech Liro's 2020 team was looking for the right measurement technology. "Our focus was clearly on precision, a long service life for the device, and saving as much time as possible," explains Liro. Since they already use many Mahr devices at the plant and are very satisfied with them, the request to Sales Engineer Jacek Bartoszek from Mahr Poland was obvious. "He has already provided us with excellent advice on metrological problems many times," Liro emphasizes. Bartoszek suggested the new MarSurf M 310 mobile roughness measuring device to the Eaton team. It features easy operation and a highly robust design. A large, high-resolution and backlit 4.3-inch TFT display ensures that all measurement results are accurately displayed. "The MarSurf M 310 is operated intuitively via the touch-enabled screen - just as we are used to from smartphones today. Another benefit is that users can reliably determine roughness parameters with the MarSurf M 310 even without specialist knowledge or training," Bartoszek explains the flexible measuring device.
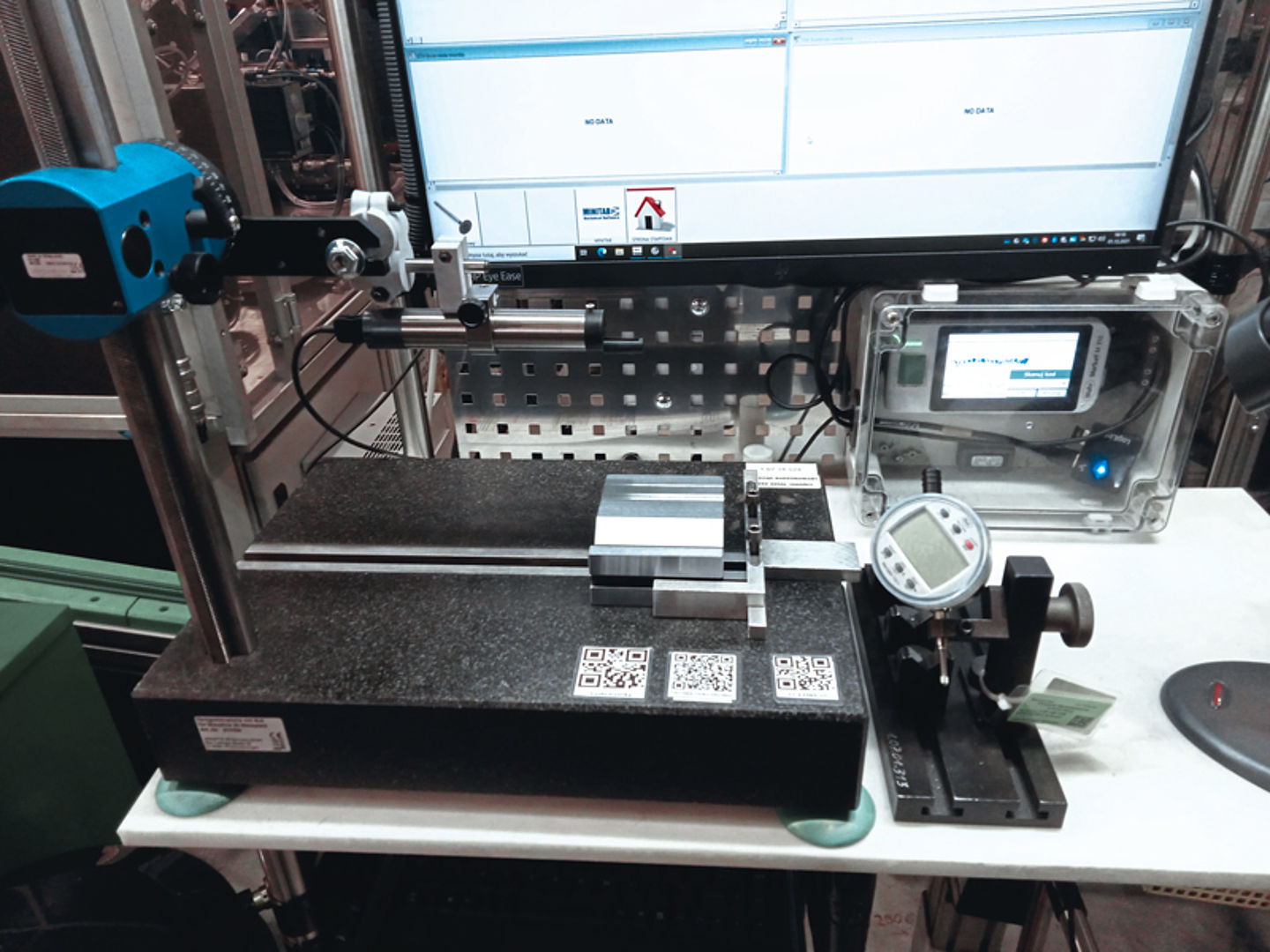
Enclosure and scanner make errors impossible
Since July 2021, the MarSurf M 310 has now been used at Eaton to measure the roughness on the stem surface as well as the valve seat. The measurements are performed by the production line operator. "The plan is to extend the roughness measurements to valve tip, valve head and other geometric features of the valve in the future," reports the Eaton measurement engineer. Initially, quality inspectors at the Bielsko-Biała plant in southern Silesia had to manually select the respective program from the control unit menu for the measurements. This was time-consuming and entailed the risk of unintentionally changing the parameters. However, Bartoszek came up with the idea of placing the control unit in a separate box that separates it from the harsh production environment – and thus from the oil and oil mist on the factory floor, which can penetrate the device and slowly destroy its electronics. With this box, the operator is now separated from the control unit and no longer has to touch it. Instead, he simply scans a QR code with the barcode scanner connected to the MarSurf M 310, which triggers the corresponding measuring program. "So the operator no longer has to spend a long time searching for a program in the menu, but now has very easy access to it," explains quality manager Liro with satisfaction.
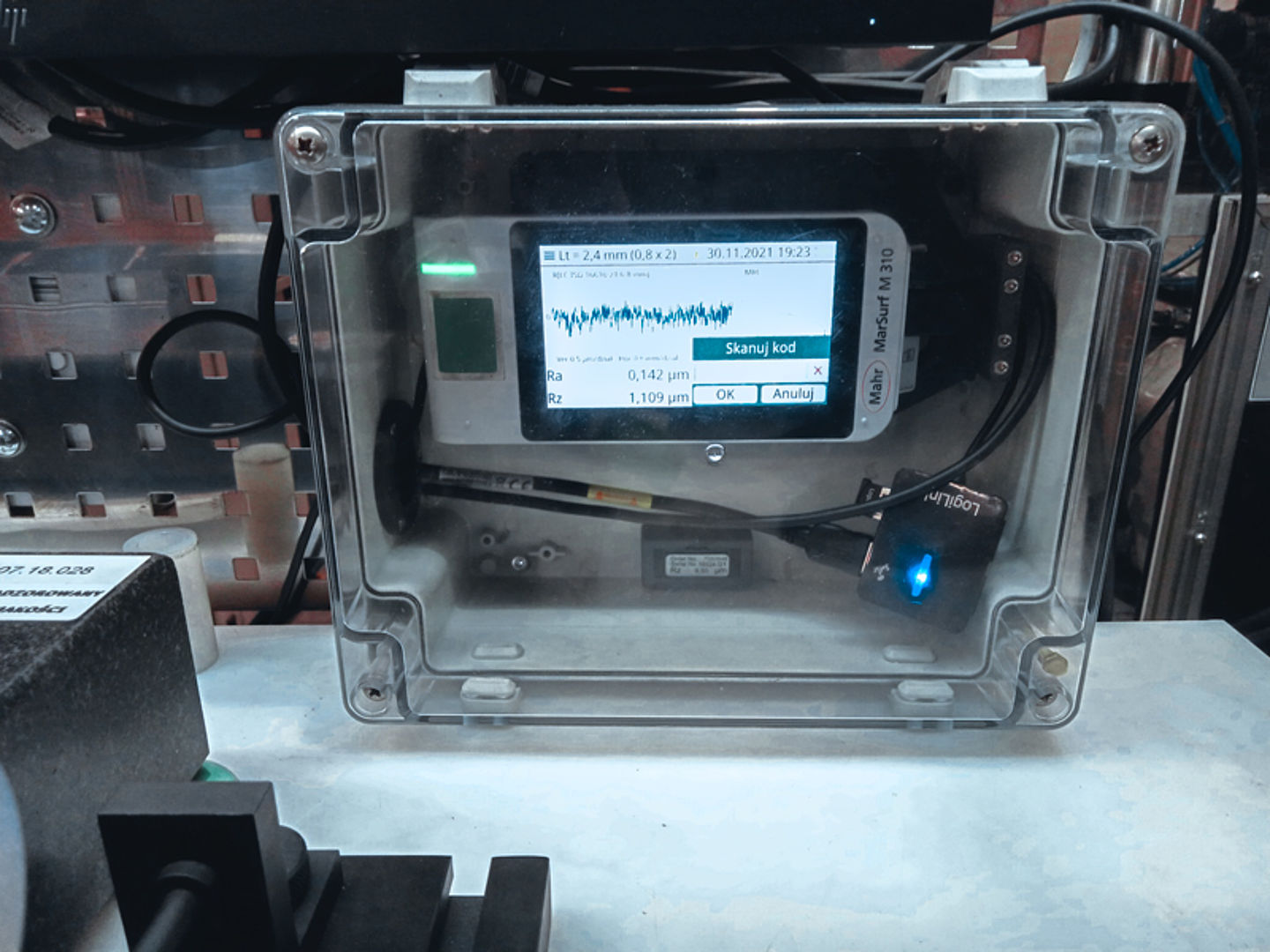
Conclusion: The MarSurf M 310 now puts the valve seats through their paces. The measurements deliver precise results with amazingly simple handling, and sources of error are largely eliminated. Only if the surface finish is within the permissible tolerances does the component pass the strict quality controls at Eaton Automotive Systems. And in the future, it will bring combustion engines up to full speed.
Questions about the device? Martin Adler, Product Manager MarSurf, will be happy to answer your questions and provide further information by phone at +49 551 / 7073-99321 or by email: Martin.Adler@mahr.de.
Info: MarComProf supports internal controlling
With the MarSurf M 310, Eaton is also able to send measurement results data from the M 310 to the internal SPC analysis program via MarComProf software without touching the computer keyboard or manually rewriting the results – "this was not possible with our previous instruments," Liro says. This process eliminates the possibility of errors, saves a lot of time and allows operators to focus on their work, he said. His team also uses MarComProf to collect wireless data from Mahr's digital indicators attached to the M 310's measuring station and send it to the SPC program as well – unifying the measuring station.