Magas színvonalú méréstechnika a minőségellenőrzéshez a mérőszobában, a termelésben, az árubeérkezésnél vagy fejlesztésnél.
Gear Metering Pumps & Meter Mix Dispense Machines with highest accuracy for processing liquids and pastes.
High-precision rotary stroke bearings for backlash-free linear and rotational movements for use in machine and device construction.
Metrology Alak- és helyzet méréstechnika Tengelymérés-technika Fogazatmérés-technika Optikai méréstechnika Használt gép portál
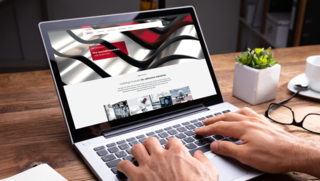
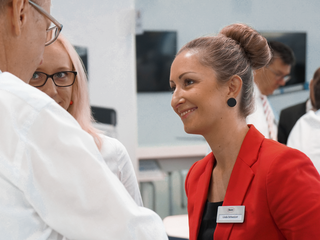
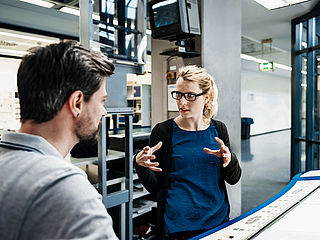
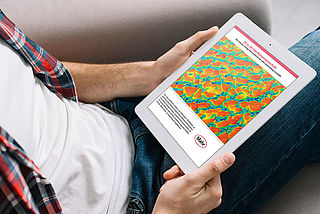
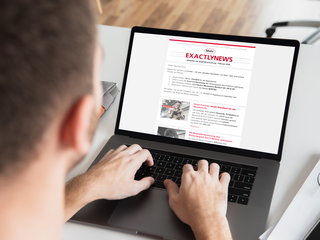
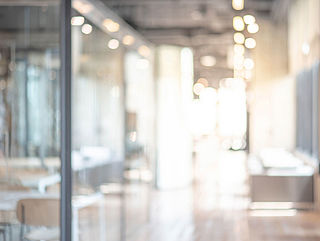
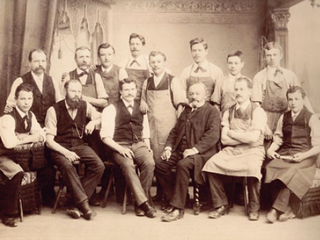
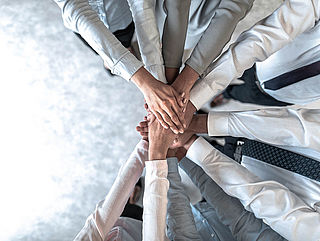
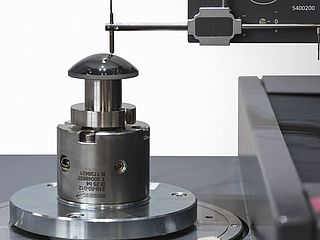
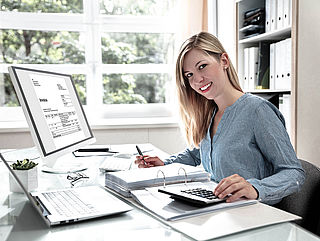
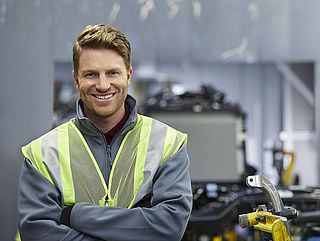
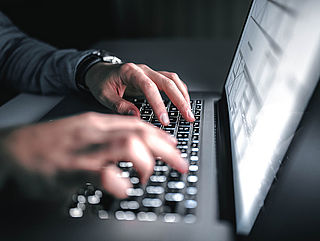
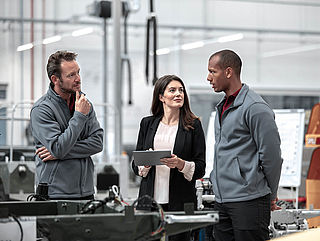
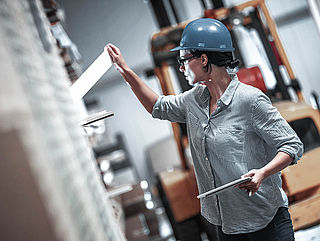
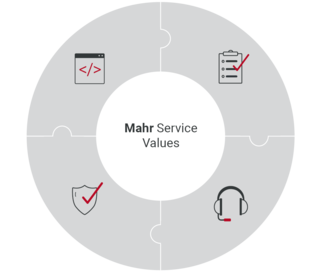
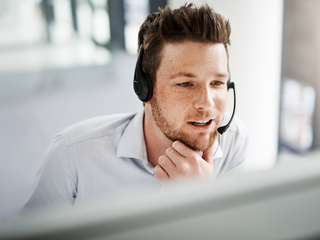
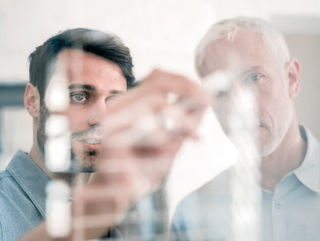
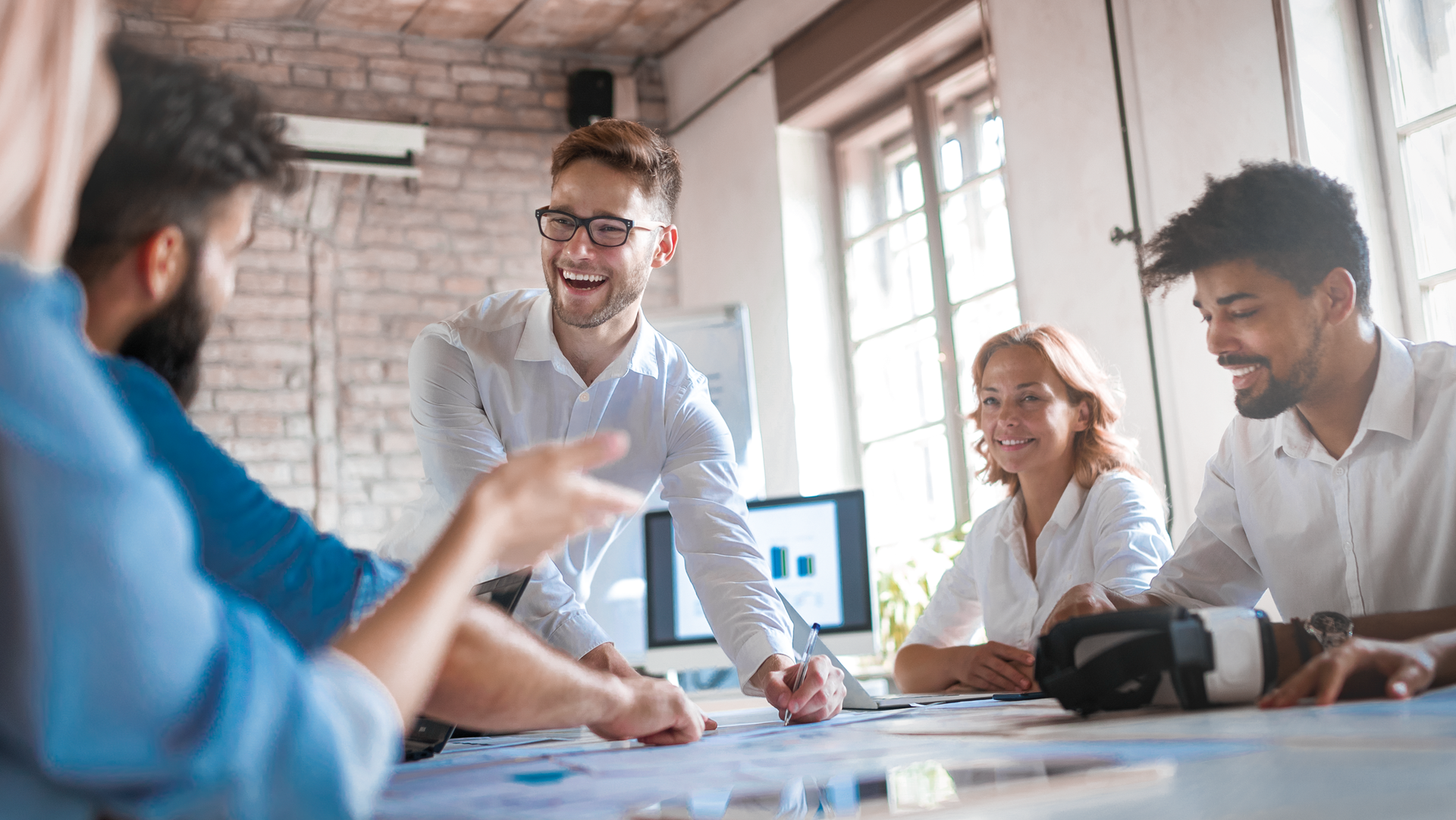
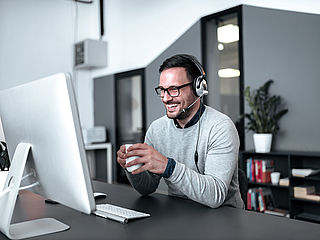
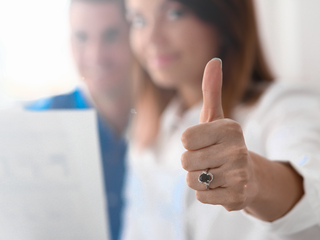
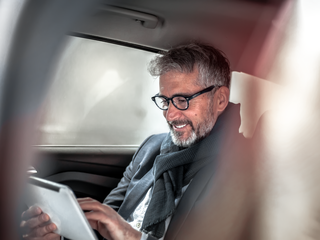
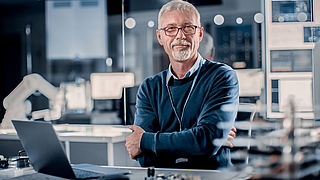
Nemzetközi szinten működő vállalatként a Mahrnak vannak szabadalmai nemcsak Németországban, hanem az egész világon is.
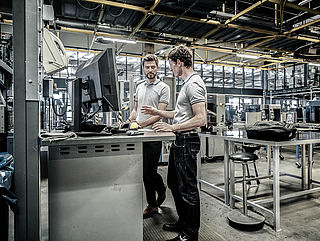
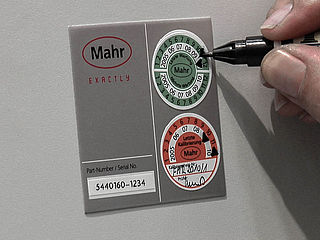
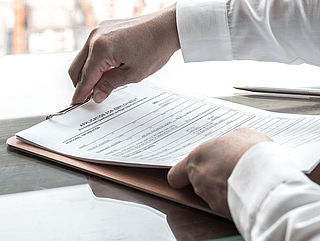
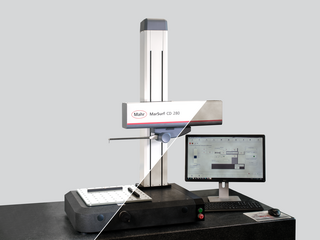
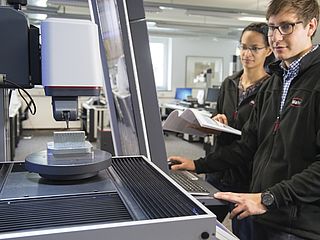
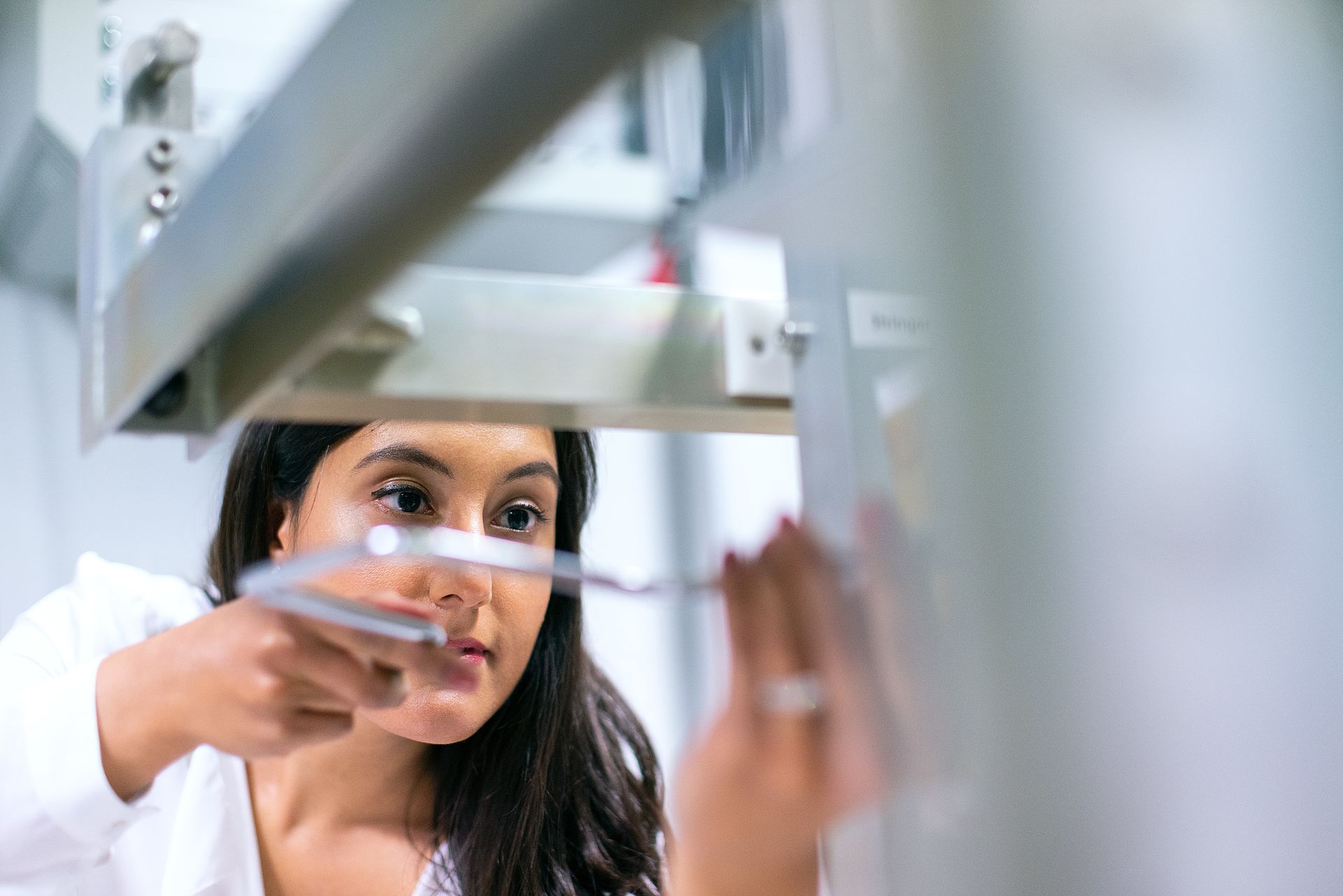
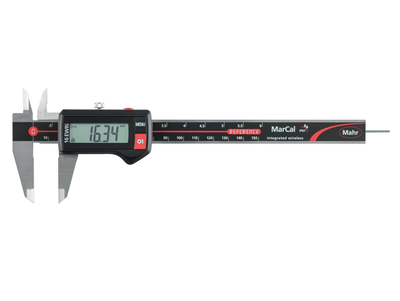
A Mahr innovatív kézi méréstechnikája: Tolómérők, mikrométerek és mérőórák analóg és digitális kivitelben beépített rádiós átvitellel. A Mahr összehasonlító mérőkészülékek és referencia etalonok nélkülözhetetlenek az Ön pontos gyártásközeli méréstechnikájához.
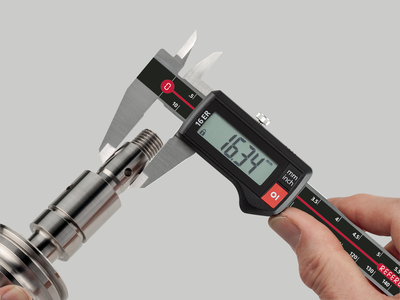
Analóg és digitális tolómérők széles választéka. Egyszerű kezelés, vezeték nélküli kivitel és nagy pontosság. Pontos mérésekhez tökéletes megoldás a gyártásban.
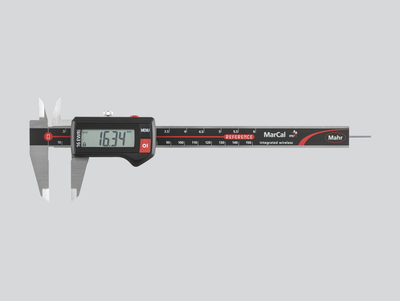
Biztonságosan leolvasható digitális kijelző, a modern kivitel és a szokásos Mahr pontosság jellemzi a digitális tolómérőinket. A termékválasztékban megtalálható bármely alkalmazáshoz szükséges mérőkészülék. A különböző adatátviteli portok és a max. IP67 védelmi fokozat minden igényt kielégít.
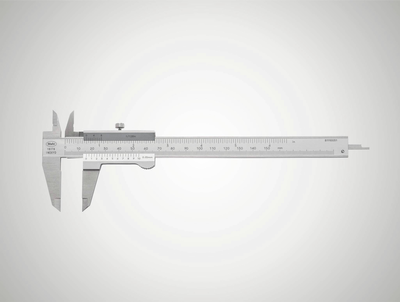
Tükröződésmentes leolvasás, edzett acél, megemelt vezetőpályák a mérőskála védelme és a legnagyobb pontosság érdekében. A Mahr klasszikus nóniuszos minőségi tolómérőjének jellemzői.
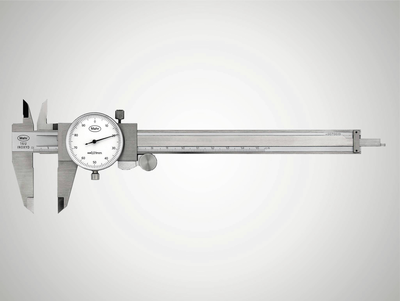
Nagy kontrasztos számlap és ütésálló mérőegység a tartós pontosságért. A mechanikus Klasszikus a gyors és biztonságos leolvasásért.
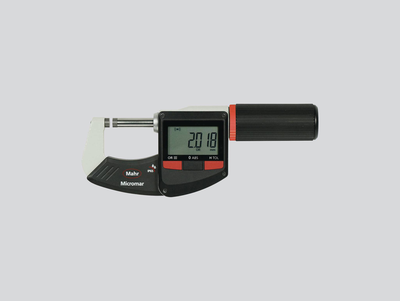
Legmagasabb pontosság a legkülönbözőbb kivitelekben. A Mahr mikrométerei klasszikus mechanikus, digitális és vezeték nélküli változatban érhetők el.
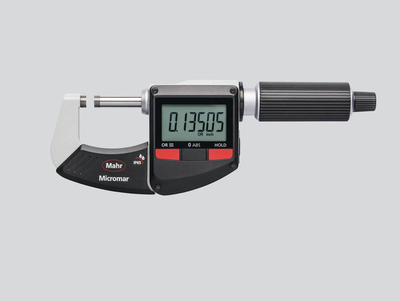
Jól leolvasható digitális kijelző, a modern kivitel és a szokásos Mahr pontosság jellemzi a digitális kengyeles mikrométereinket. Termékválasztékban megtalálható bármely alkalmazáshoz szükséges mérőkészülék. A különböző adatátviteli interfészek és az akár IP65 védelmi fokozat minden igényt kielégít.
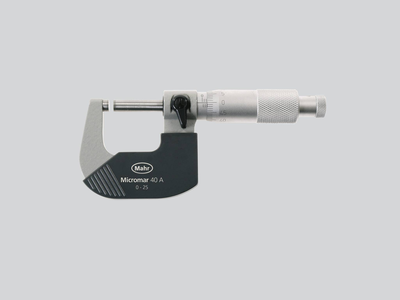
tükröződésmentes leolvasás, hőszigetelő lapok és precíziós csiszolású orsók a maximális pontosságért. A Mahr egyik minőségi mikrométerének jellemzői.
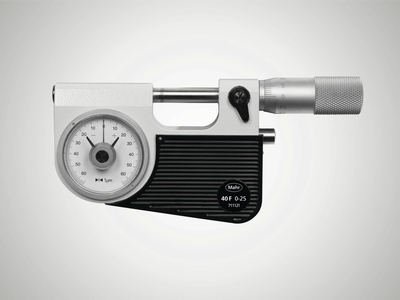
Különösen alkalmas a szériaalkatrészek (tengelyek, csapok, szárak) biztonságos és gyors vizsgálatára. Egy szempillantás alatt felismerhető és leolvasható a méretpontosság.
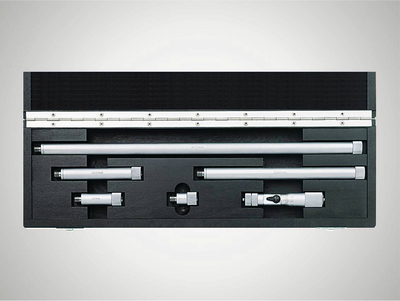
Nagy átmérők mérésére és távolságok vizsgálatára 2500 mm-ig
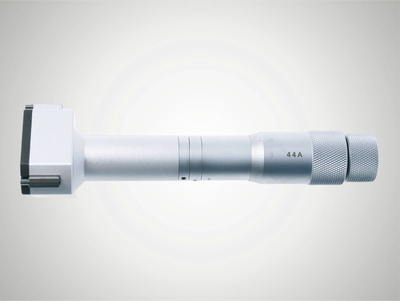
Választhatóan skálás vagy digitális kijelzővel vagy gyors mérőkészülék pisztolymarkolattal. A Mahr hárompontos furatmérő készülékei az automatikus önbeállásnak köszönhetően mindig megbízható mérési eredményeket adnak.
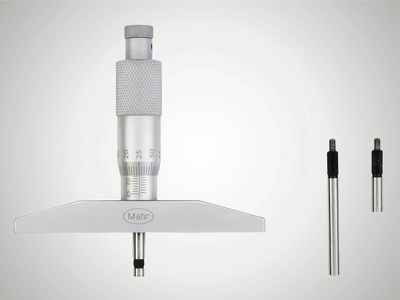
Tükröződésmentes leolvasás és precíziós csiszolású orsók a maximális pontosságért. A Mahr egyik minőségi mikrométerének jellemzői.
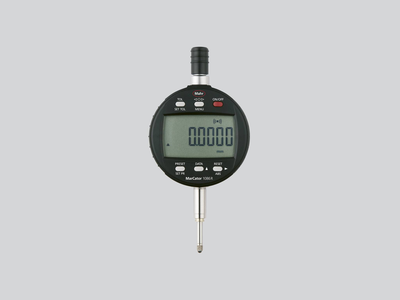
Analóg és digitális mérőórák, finomkijelzők és szögtapintós mérőórák széles választéka. Egyszerű kezelés, opcionálisan rendelhető vezeték nélküli kivitel és nagy pontosság. Pontos mérésekhez tökéletes megoldás a gyártásban.
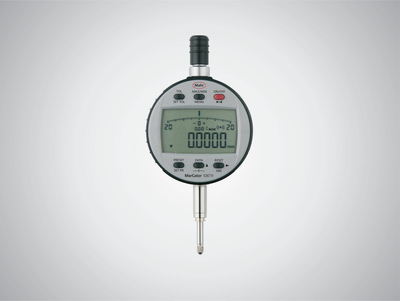
Jól olvasható digitális kijelző, robusztus szerkezet és a Mahr-tól megszokott nagy pontosság jellemzi a digitális mérőórákat. Termékválasztékban megtalálható bármely alkalmazáshoz szükséges mérőkészülék. A különböző adatátviteli interfészek és az akár IP54 védelmi fokozat minden igényt kielégít.
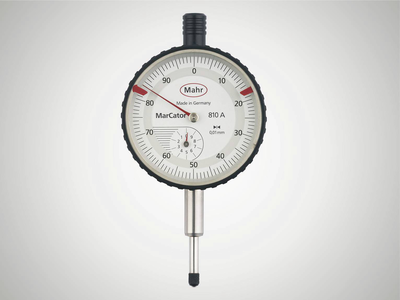
Nagyfokú érzékenység és nagy pontosság az alábbiaknak köszönhetően: Mérőegység tengelyeinek robusztus csapágyazása, precíziós fogazású kerekek és fogaskerekek, nagyon pontosan csapágyazott mérőcsap.
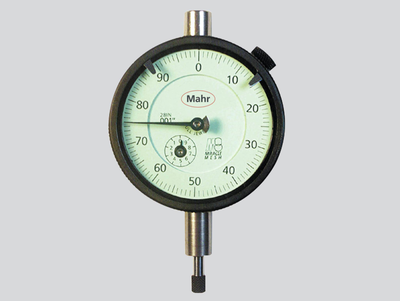
Nagyfokú érzékenység és nagy pontosság az alábbiaknak köszönhetően: Mérőegység tengelyek robusztus csapágyazása, precíziós fogazású kerekek és fogaskerekek, nagyon pontosan csapágyazott mérőcsap
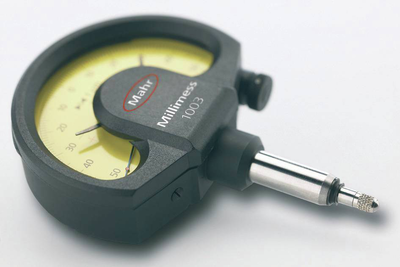
A Millimess finomkijelzők az analóg mérőórákhoz képest még pontosabb egységek, jobb mérési pontosság és sokszorosan jobb irányváltási különbség. Ezek az előnyök különösen a radiális ütés vizsgálatoknál, egyenesség- és síklapúság mérésnél és összehasonlító méréseknél mutatkoznak meg.
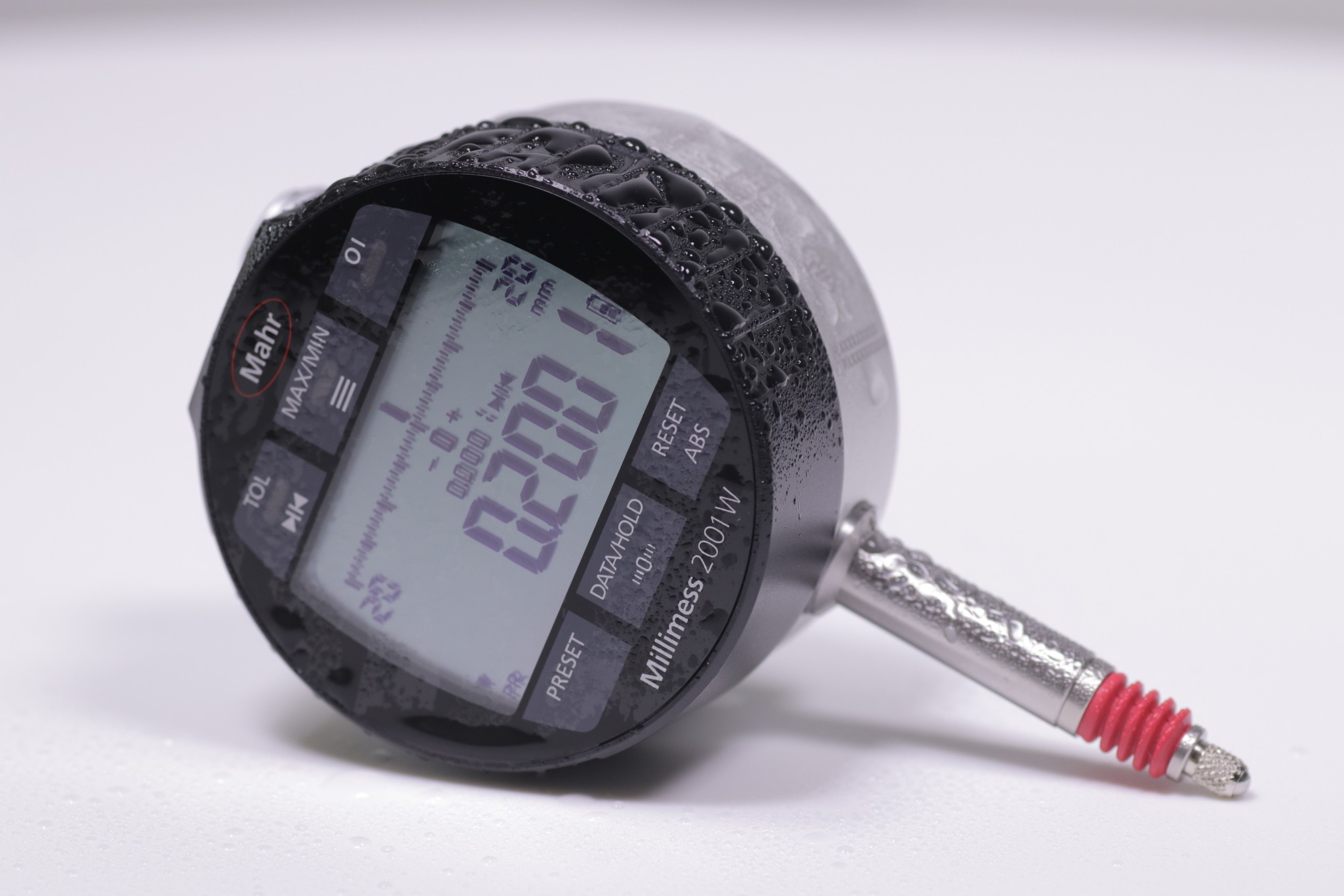
A nagy pontosságú induktív Millimess finomkijelzők 0,2 μm digitális felbontást is elérnek. A gyakorlatias kezelési funkcióknak, pl. a tűrésfelügyeletnek, dinamikus méréseknél a minimum vagy maximum meghatározásnak, a kombinált számjegyes és skálás kijelzőnek, az egyszerű adatátvitelnek köszönhetően nélkülözhetetlen precíziós mérőkészülék.
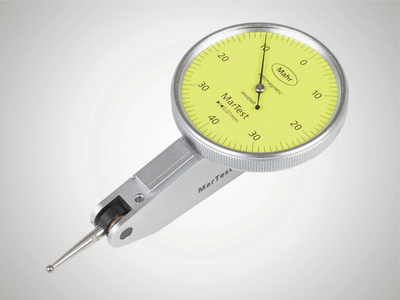
A finoman működő, számítógéppel optimalizált mérőmű a biztonság és a precizitás maximumát nyújtja. A durva műhelykörülmények közötti használathoz a kijelzőt az edzett ásványi üveg kiválóan védi a karcolástól és a töréstől, ráadásul tömítés akadályozza meg a folyadék behatolását.
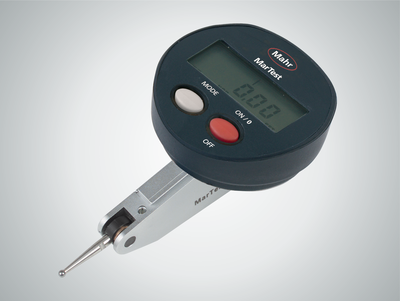
Jól olvasható digitális kijelző, robusztus szerkezet és a Mahr-tól megszokott nagy pontosság jellemzi a digitális szögtapintós mérőórákat.
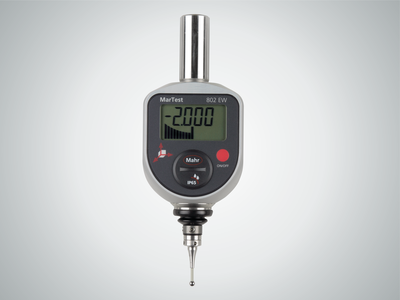
Az NC gépekhez, megmunkáló központokhoz és szikraforgácsoló gépekhez tervezett Mahr 3D mérőtapintók megrövidítik azok beállítási idejét és élettartamát. Tökéletes megoldás a munkadarabok és berendezések referencia éleinek pontos tapintásához.
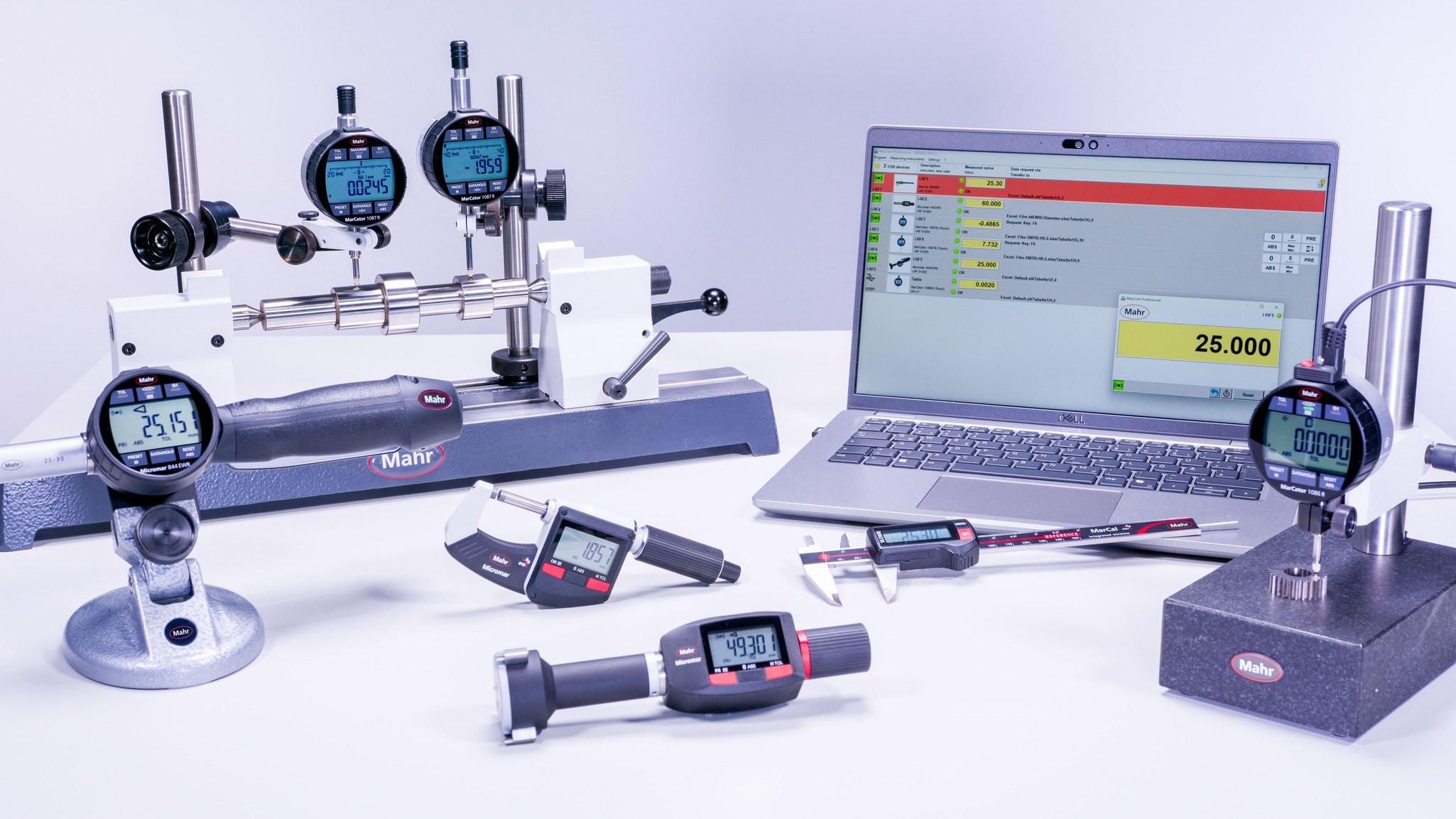
Mindegy hogy beépített vezeték nélküli kapcsolat, külső rádiómodulok, USB, Opto RS232 vagy Digimatic: Mindegy, hogy melyik adatátviteli szabványt használja, a MarConnect mindig gondoskodik az optimális összeköttetésről.
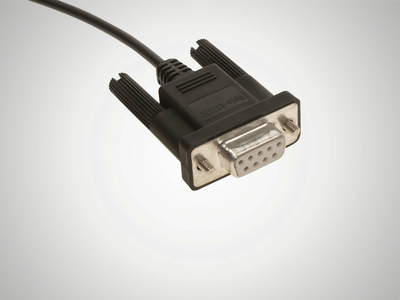
Sok Mahr kézi mérőeszköz rendelkezik MarConnect adatkimenettel. Mindegy, melyik adatcsatlakozási szabványt használja (USB, Opto RS232 vagy Digimatic), a MarConnect mindig gondoskodik az optimális összeköttetésről.
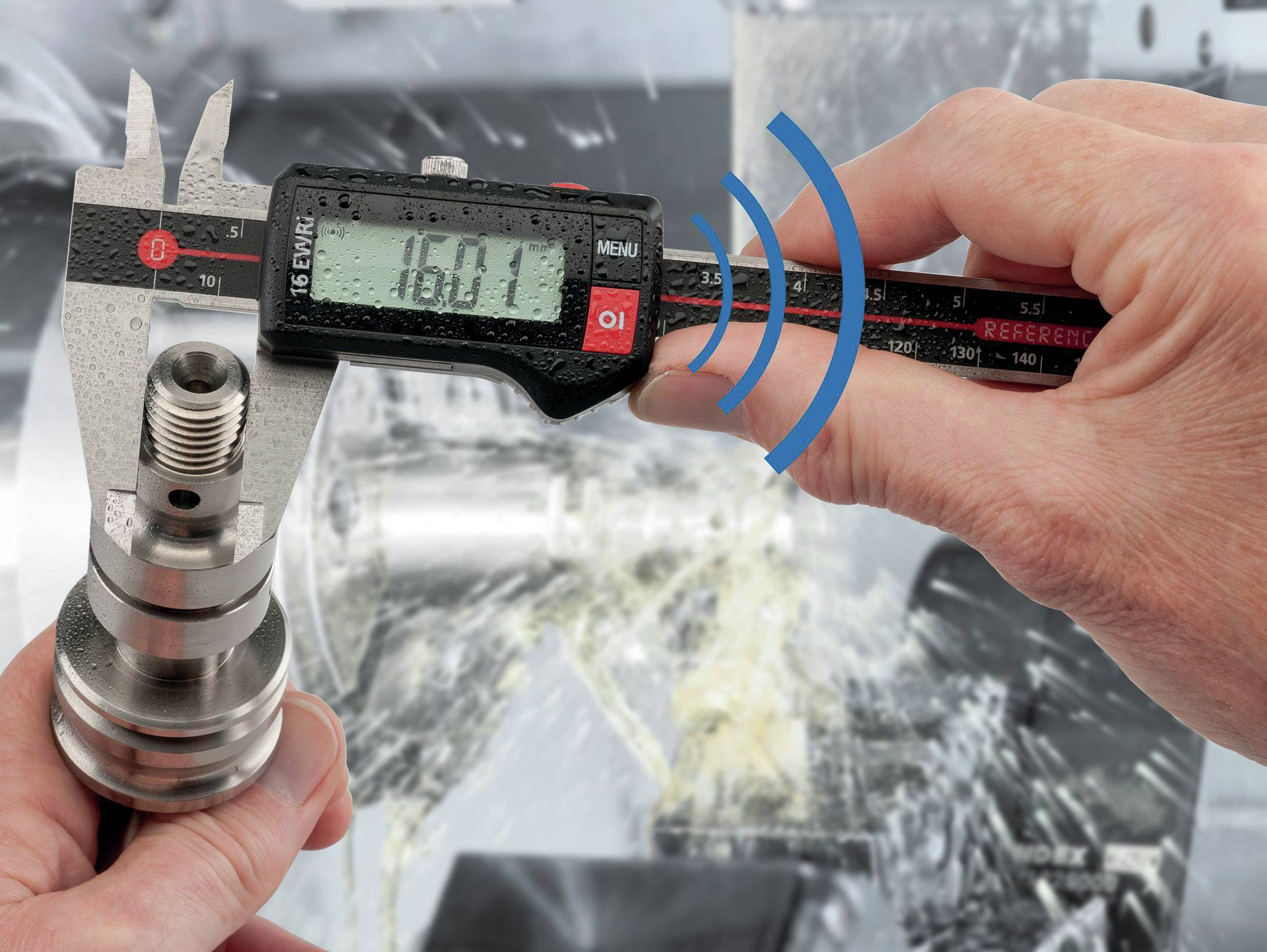
A Mahr vezeték nélküli termékválasztékával biztosítja a pontos mérési eredményeket, a teljes mozgási szabadság mellett Mérjen korszerűen és egyszerűen úgy, hogy ne korlátozza a kábelhez kötött technika
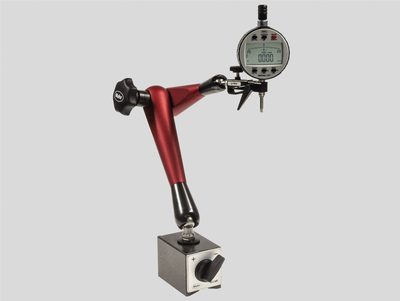
A MarStand mérőállványok, mérőasztalok és radiális ütésvizsgáló készülékek stabil felépítésüknek köszönhetően a precíz mérési eredmények előfeltételét képezik. Mérőóráinak, finomkijelzőinek, szögtapintóinak és mérőtapintóinak biztos támaszt nyújtanak.
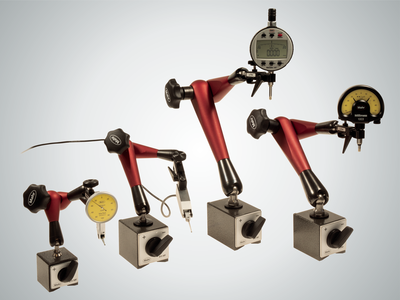
A mérőállványok stabil felépítésükkel a precíz mérési eredmények alapját képezik. Mérőóráinak, finomkijelzőinek, szögtapintóinak és mérőtapintóinak biztos támaszt nyújtanak.
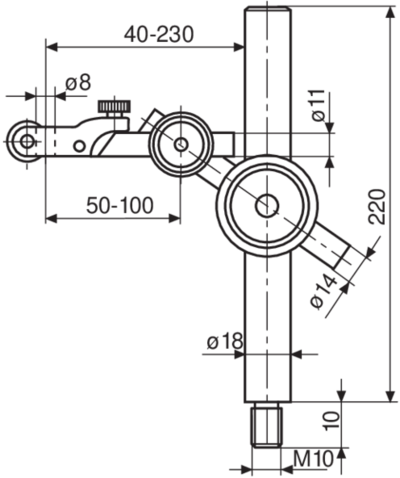
A MarStand mérőrudak egyedi megoldásokhoz használatosak és stabil felépítésükkel a precíz mérési eredmények alapját képezik. Mérőóráinak, finomkijelzőinek, szögtapintó mérőóráink és mérőtapintóinak biztos támaszt nyújtanak.
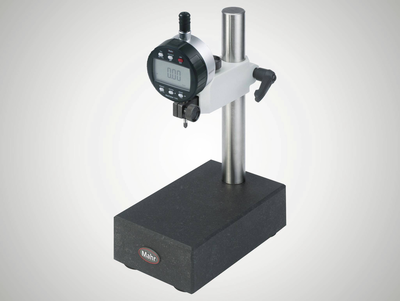
A pontos és sima mérőasztal, a stabil mérőoszlop és az erős karok kombinációja jellemzi a mérőasztalokat. A MarStand mérőasztalok különlegesen stabil felépítésüknek köszönhetően a precíz mérési eredmények alapvető feltételét képezik.
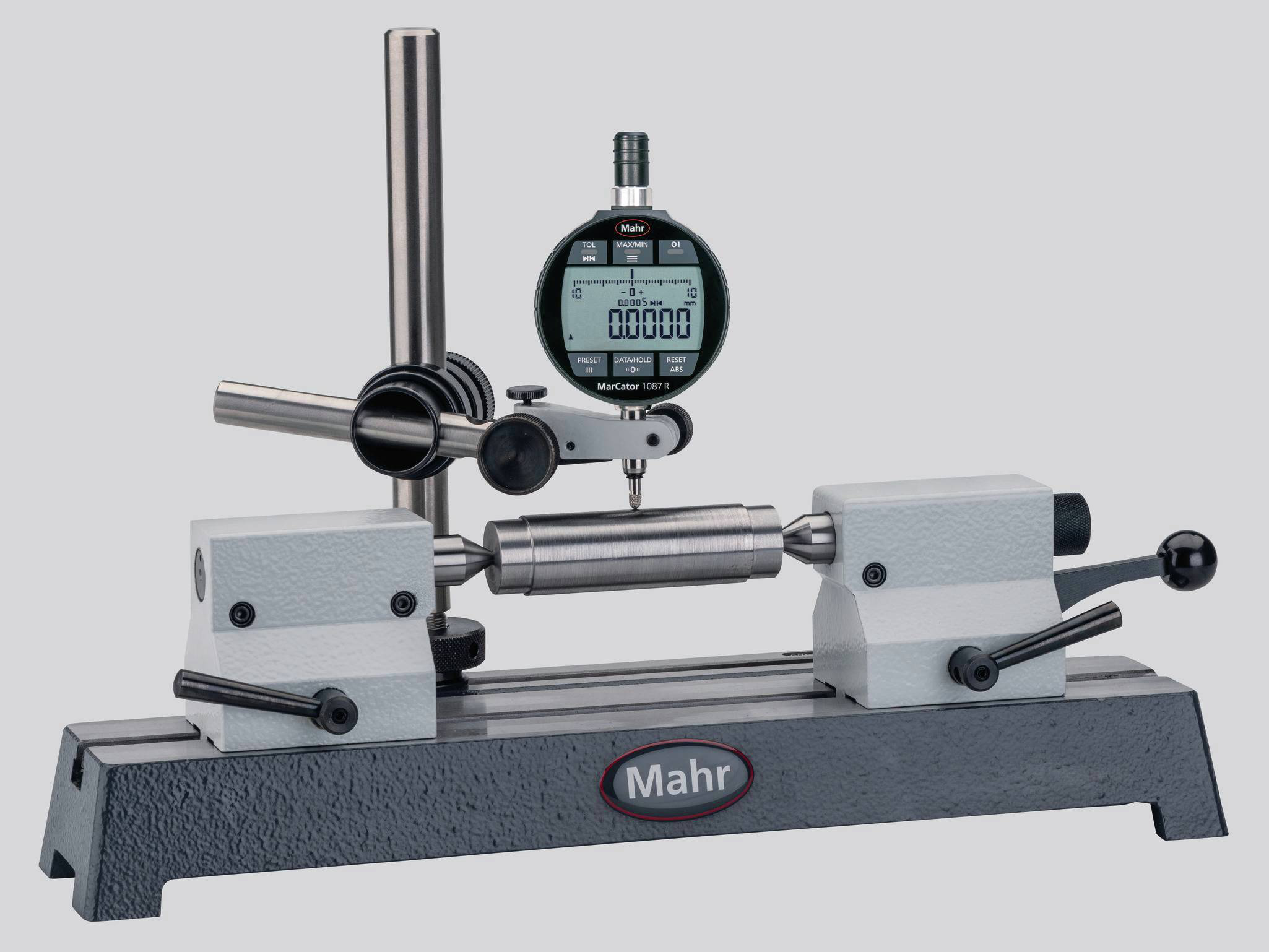
Az ütésvizsgáló készülékek a legegyszerűbb módszert biztosítják a tengelyek helyzet- és alakhibáinak gyártásközi környezetben történő meghatározásához. A sokszínű modelleknek köszönhetően a robusztus MarStand ütésvizsgáló készülékek, a munkadarabbal szemben támasztott legkülönbözőbb követelmények és pontos mérési eredmények alapját képezik.
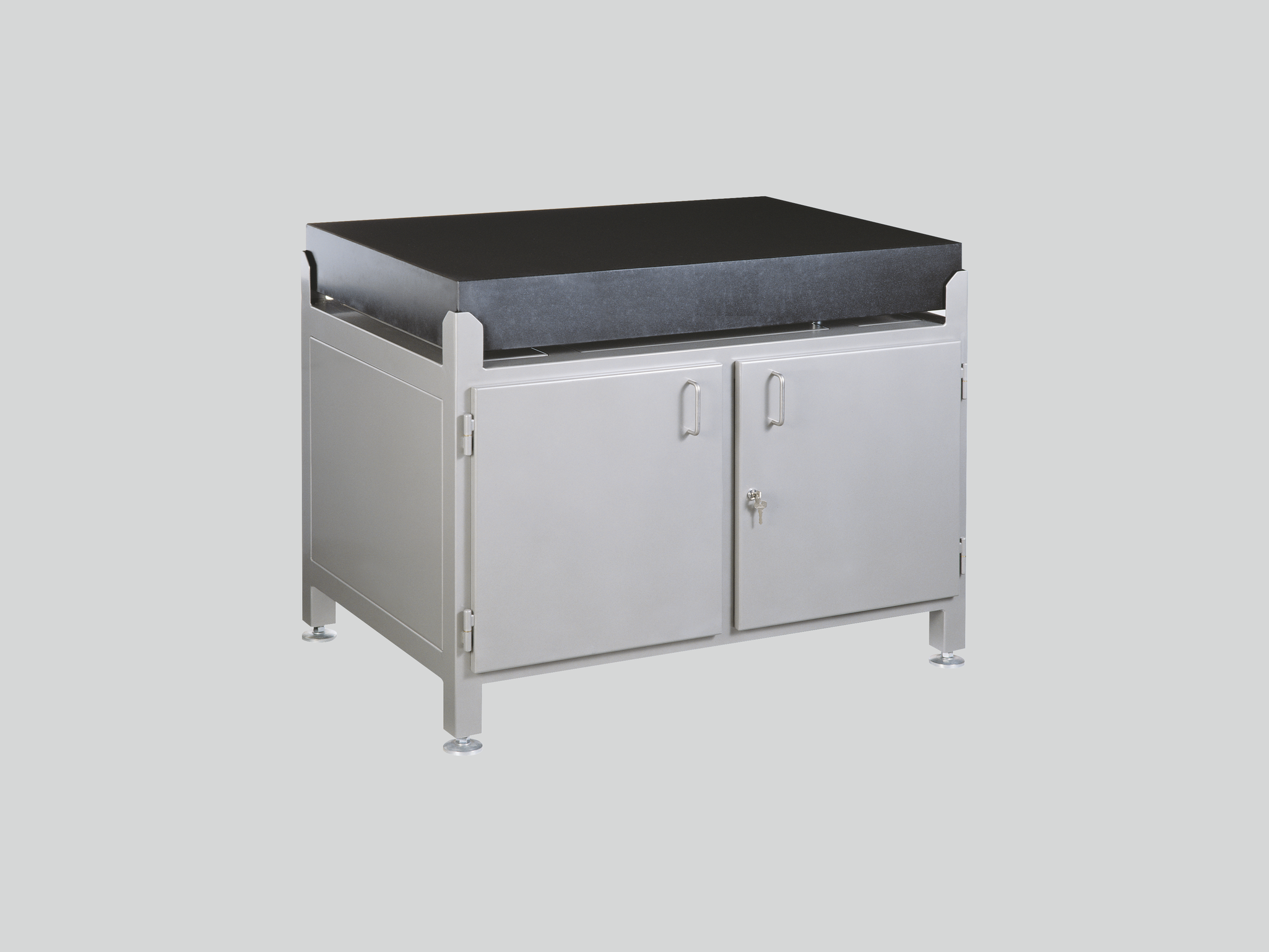
A kemény gránit vizsgálólapok magas kopásállóságuknak és mérettartóságuknak köszönhetően a magasságmérő készülékek tökéletes alapját képezik.
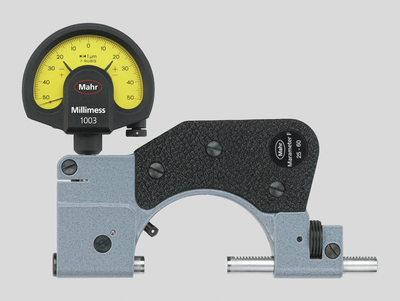
A kijelzős összehasonlító mérőkészülék a tökéletes szerszám a gyártásközi precíziós mérésekhez. Egy referencia etalonhoz beállítás csökkenti az eltérés tartományt és a lehető legkisebbre csökkenti a hőmérséklet-ingadozások mérési eredményre gyakorolt hatását.
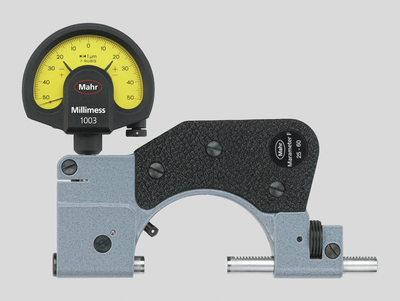
A finomkijelzős villás idomszerek a hengeres részek, pl. tengelyek, csapok és szárak precíziós méréséhez, különösen a szériaalkatrészek biztonságos és gyors vizsgálatához. A finomkijelzőn egy szempillantás alatt felismerhető és leolvasható a méretpontosság.
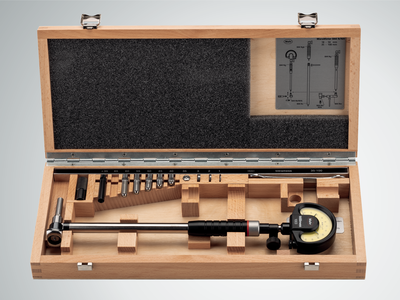
A belső mérőkészülékek a furatok átmérőjének, körkörösségének és kúposságának precíziós mérésének tökéletes eszközei.
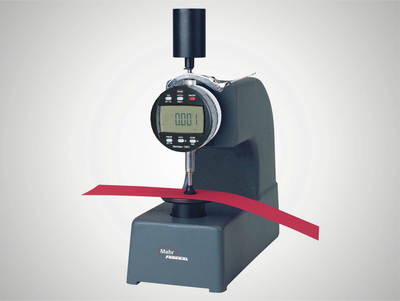
Vastagságmérő készülékeinkkel bármely fólia, lemez és lap különösen gyors méréséhez kínálunk stabil és egyszerű megoldásokat.
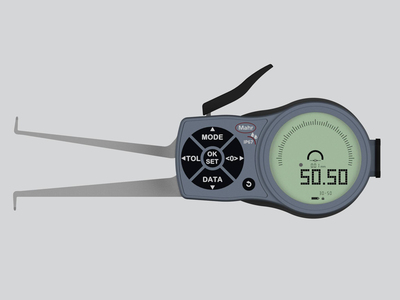
Ha a szokásos mérőkészülék, pl. a tolómérő vagy a furatmikrométerek a munkadarab geometriája miatt nem használhatók, a tapintókaros mérőkészülék a tökéletes megoldás!
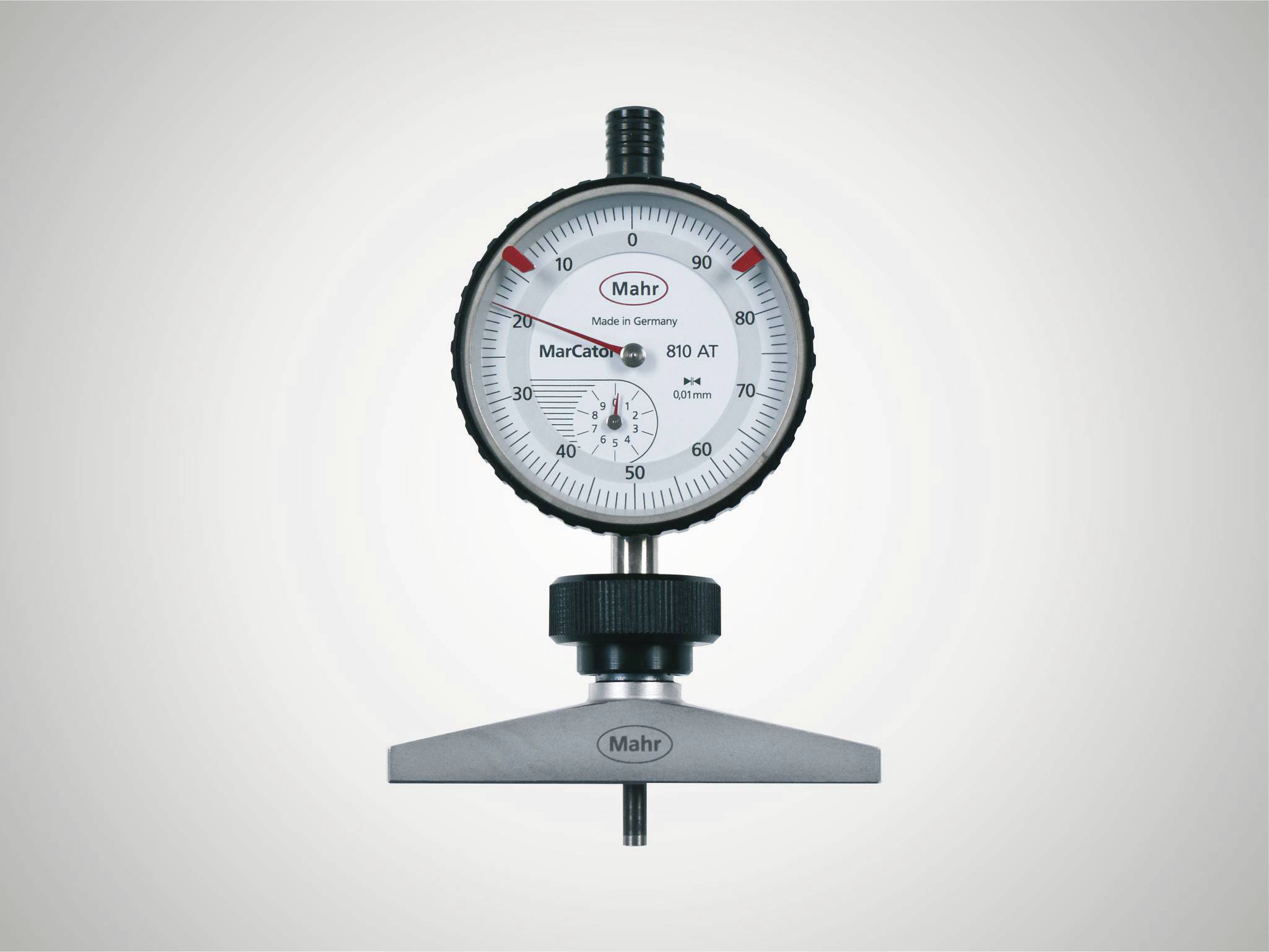
Mélységmérő hídjainkkal robusztus és egyszerű megoldásokat kínálunk a különösen gyors mélységmérésekhez. A 8 mm-es befogószárnak köszönhetően a mérési feladatnak megfelelő mérőórák, finomkijelzők és tapintók használhatók.
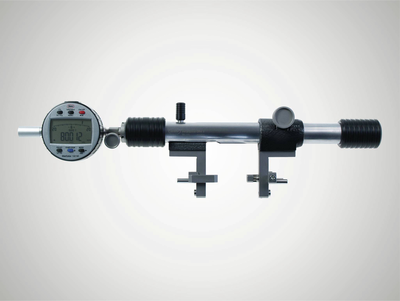
Az univerzális mérőkészülékek összehasonlító mérőkészülékek, a gyártásközi precíziós mérések tökéletes partnerei, mivel a referencia etalonnal összehasonlító mérés a minimálisra csökkenti a hőmérséklet-ingadozások mérési eredményre gyakorolt hatását.
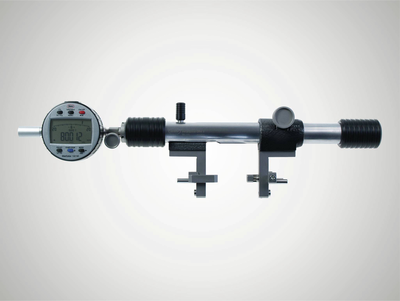
Legyen szó fogazásról, menetről, kúpról vagy beszúrásról: A Multimar univerzális mérőkészülékek szinte minden olyan belső és külső mérésre optimális megoldást nyújtanak, amelyekhez a standard mérőeszközök nem alkalmasak. Ehhez különböző alapkészülékek és a tartozékok széles választéka áll rendelkezésére.
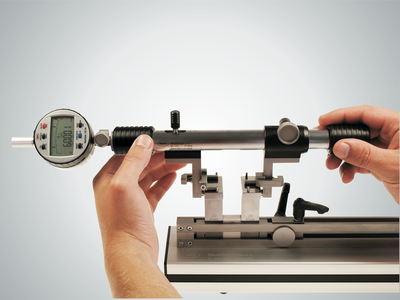
Állítsa be pontosan belső és külső méréshez készülékeit. A 844 S beállító-készülékekkel bármely mérési feladathoz a legjobb eszközzel rendelkezik, még a nagyobb dimenziókhoz is.
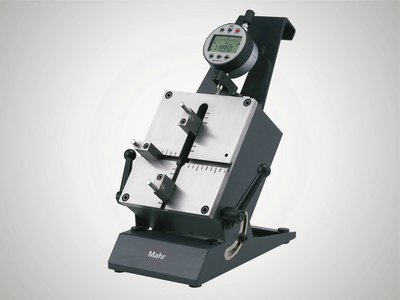
Mindegy, hogy központosító élek, keskeny vállak vagy beszúrások: A Multimar 36B univerzális mérőkészülékek szinte minden belső és külső méréshez optimális megoldást kínálnak. Ehhez különböző alapkészülékek és a tartozékok széles választéka áll rendelkezésére.
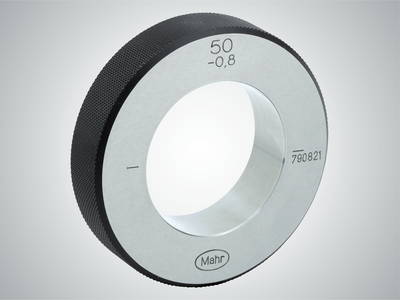
Bízzon a Mahr etalonokban és idomszerekben, mert ezek jelentik a pontos mérési eredmények alapjait.
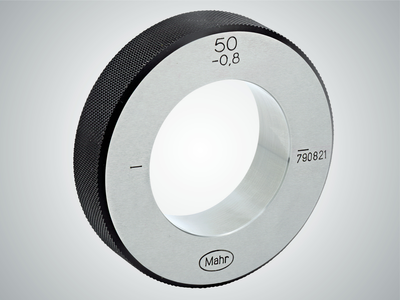
Bízzon a Mahr beállító etalonjaiban, mert azok a pontos mérési eredmények alapjai.
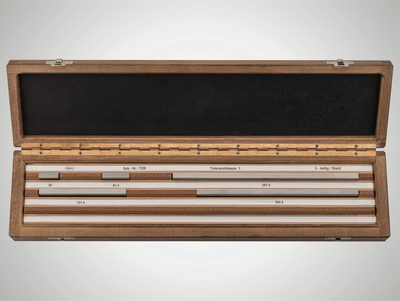
A Mahr mérőhasábok birtokában csúcsminőségű referencia és használati etalonokkal rendelkezik. Válasszon a 4 tűrésosztályból és 2 anyagból a műhelyéhez, termelési folyamatához vagy minőségbiztosításához megfelelően.
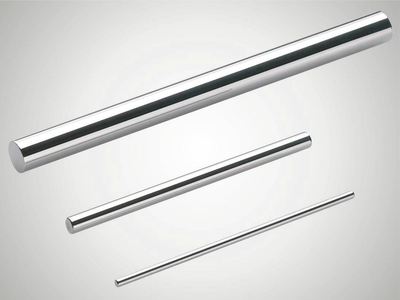
A Mahr mérőcsapok 3 tűrésosztályban és különböző kivitelben állnak rendelkezésre. Válasszon a műhelyéhez, termelési folyamatához vagy minőségbiztosításához megfelelően.
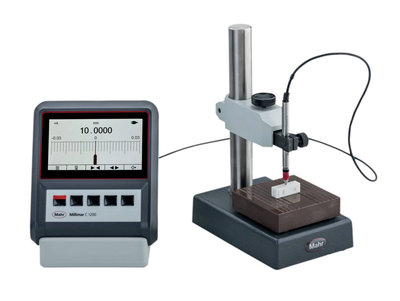
Amilyen sokrétűek az elektromos hosszmérő készülékekkel szemben támasztott követelmények, ugyanolyan változatosak alkalmazási lehetőségeik is. Elvárás a maximális fokú megbízhatóság és precizitás, valamint a könnyű kezelhetőség.
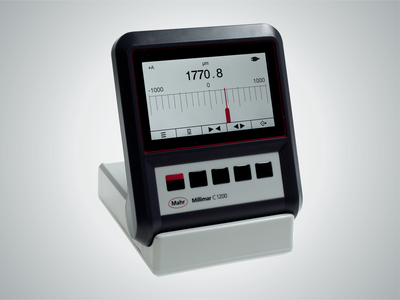
Amilyen sokrétűek az elektromos hosszmérő készülékekkel szemben támasztott követelmények, ugyanolyan változatosak alkalmazási lehetőségeik is. Elvárás a maximális fokú megbízhatóság és precizitás, valamint a könnyű kezelhetőség. A Millimar kompakt- és oszlopos mérőkészülékek teljesítik ezeket a követelményeket.
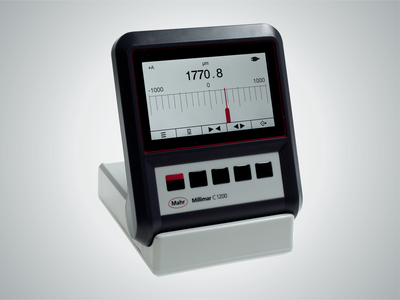
A Millimar hosszmérő készülék kompaktak, erősek és egyszerűen kezelhetők. Univerzálisan használható kiértékelő és kiértékelő készülékek az áttekinthető komplexitású gyártásközi és mérőszobai mérési feladatokhoz.
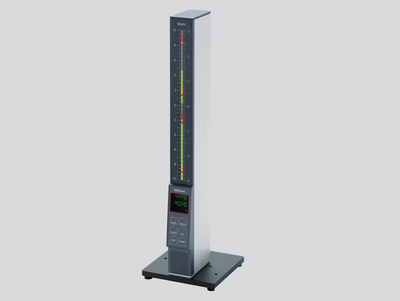
A mérési eredményeket 101 db, három színű fénydióda jeleníti meg, amelyek távolról is jól leolvashatók. A programozható figyelmeztetési és tűréshatárok túllépése esetén a szegmensek színe zöldről sárgára ill. pirosra változik
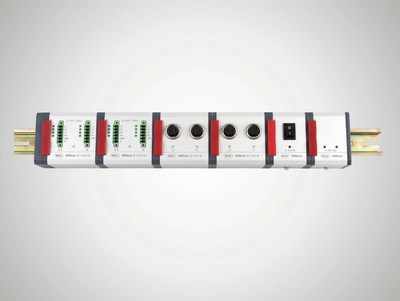
A modulok és szoftverek kombinációinak széles skálájának köszönhetően lehetősége nyílik arra, hogy munkakörnyezetét és eszközeit minden eddiginél egyedibben tervezze meg.
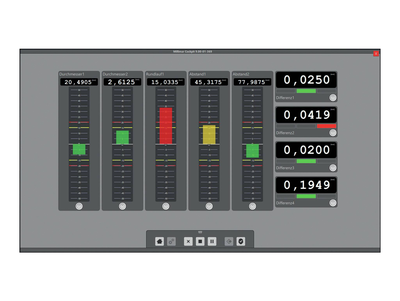
Smart and universally applicable software for complex measurement tasks in the manufacturing sector
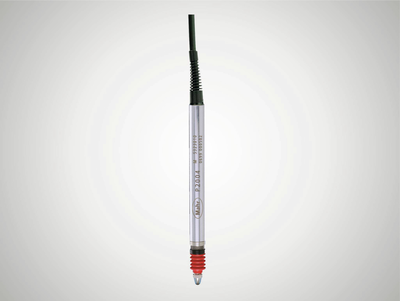
A Millimar jelátalakítók a mérőláncot legnagyobb mértékben befolyásoló komponensek. Tulajdonságaik határozzák meg a mérés minőségét. Ezért alkalmazástól függően többféle technológiát kínálunk. Például a Millimar induktív mérőtapintókat: Robusztus felépítés, flexibilis alkalmazás és vonzó ár.
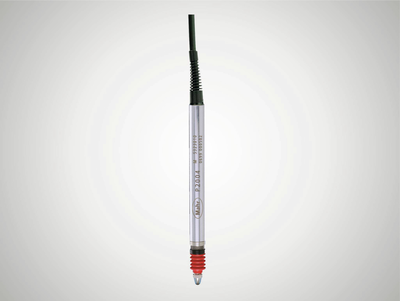
Mindegy, hogy vastagságmérés, radiális ütés vagy központosság: az induktív tapintókkal alaktól, felülettől vagy radiális ütéseltéréstől függetlenül rögzítheti a mért értékeket és eltéréseket. Nagy előnyük a nagy linearitási tartomány és a zavaró hatások elleni relatív érzéketlenség. A tapintókat főként termelésben használják összehasonlító mérésekhez, közben a szenzor specifikus feladatai változhatnak.
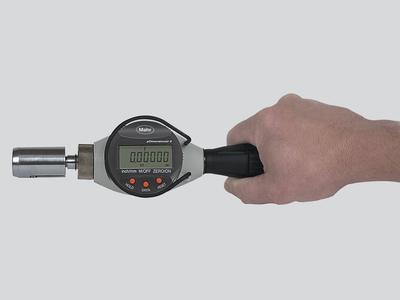
A pneumatikus hosszmérő készülékeket a nagy pontosság és a hosszú ideig tartó stabilitás jellemzi. A pneumatikus mérőfúvókákkal végzett érintésmentes méréssel a munkadarabok nem károsodnak. A szennyezett, olajos, zsíros vagy leppelő pasztával kezelt munkadarabok biztonságos mérése probléma mentesen lehetséges, mivel a mérési helyeket a mérőlevegő megtisztítja.
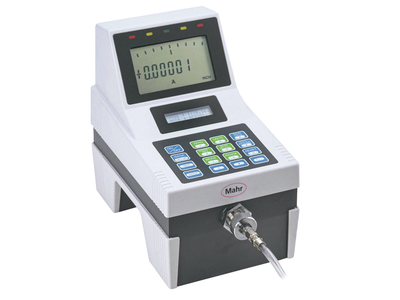
A Millimar hosszmérő készülék kompaktak, erősek és egyszerűen kezelhetők. Univerzálisan használható kijelzős és kiértékelő készülékek a kezelhető összetettségű gyártásközi mérési feladatokhoz.
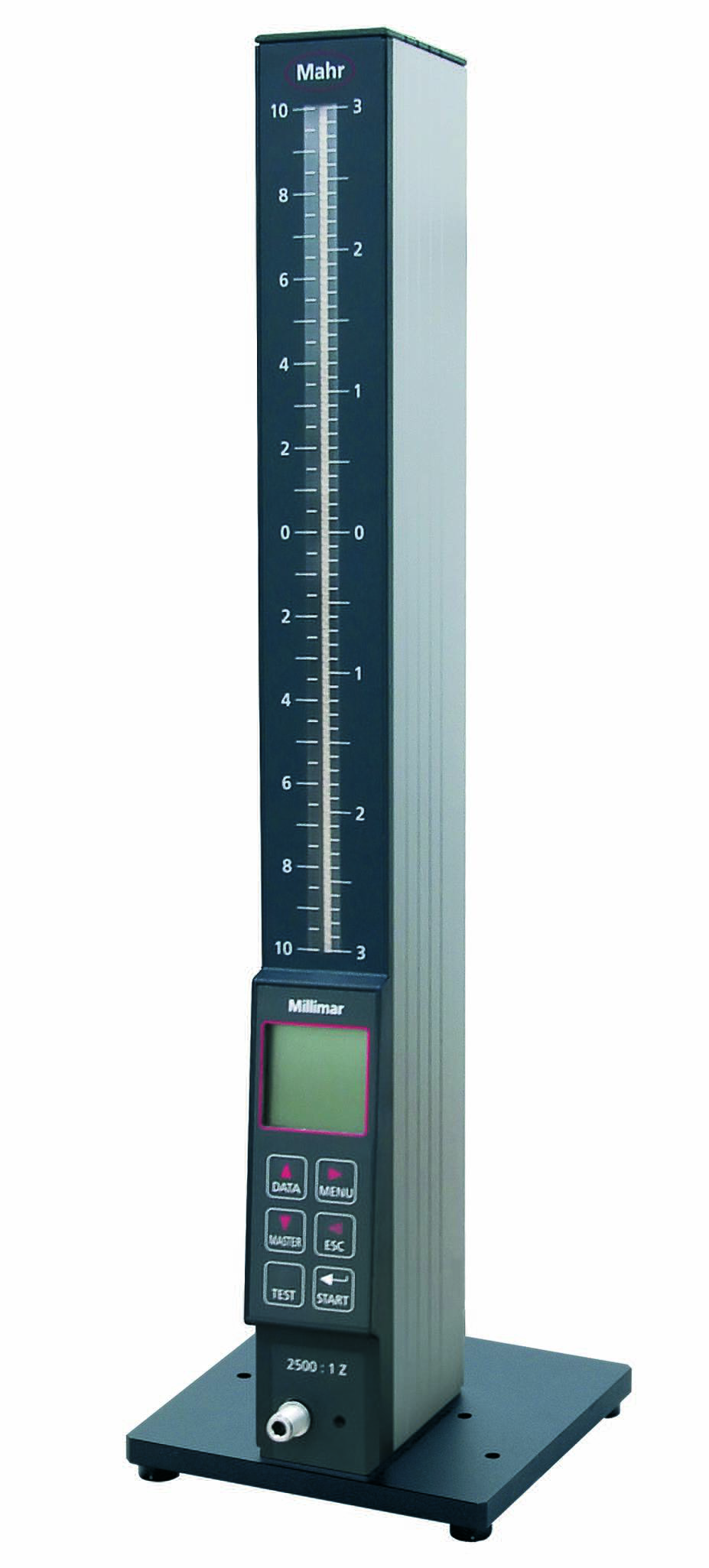
A mérési eredményeket 101 db, három színű fénydióda jeleníti meg, amelyek távolról is jól leolvashatók. A programozható figyelmeztetési és tűréshatárok túllépése esetén a szegmensek színe zöldről sárgára ill. pirosra változik.
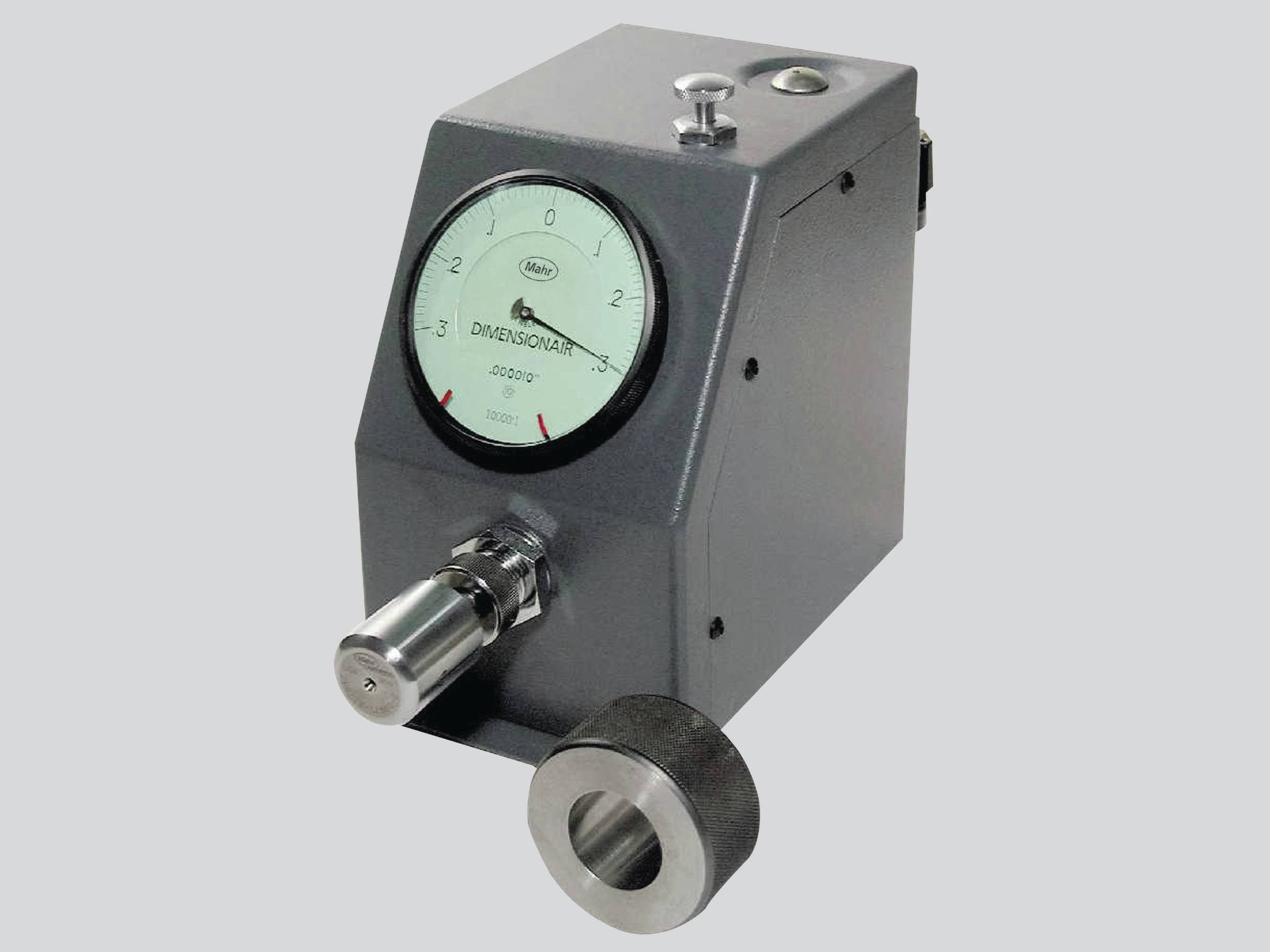
A Millimar levegős mérőkészülékek gyorsan és pontosan rögzítik a mérési eltéréseket. Csúcspontosságú pneumatikus hosszmérő készülékként már évek óta bizonyítottak mind az ipari gyártás terén, mind a mérőszobában.
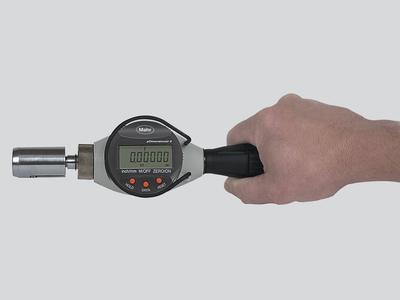
Ha a mérésnek és a kiértékelésnek mobilnak kell lenni.
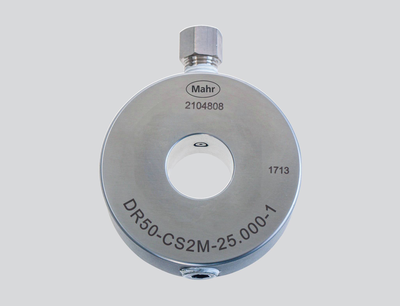
Érintésmentes mérés pneumatikus mérőgyűrűkkel, a munkadarabok károsodása nélkül.
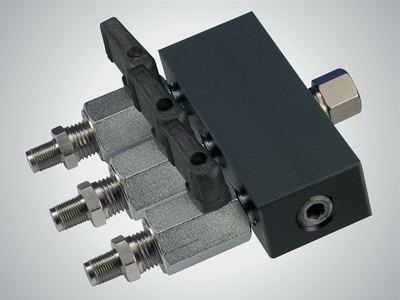
Alakítsa ki a mérőállomást az Ön mérési feladatainak megfelelően a levegős mérési technológia tartozékaival.
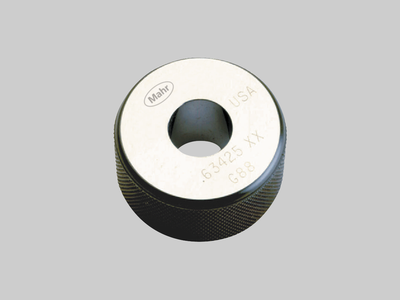
Bízzon a Mahr beállító etalonjaiban, mert azok a pontos mérési eredmények alapjai
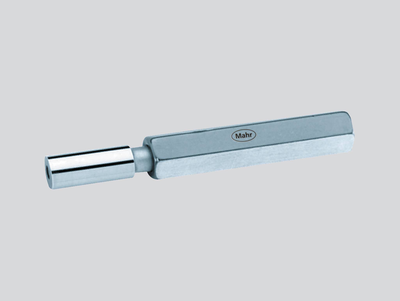
Pneumatikus mérőkészülékek (fúvókás mérőgyűrűk) beállítása. Gondosan edzett, öregített, csiszolt és leppelt.
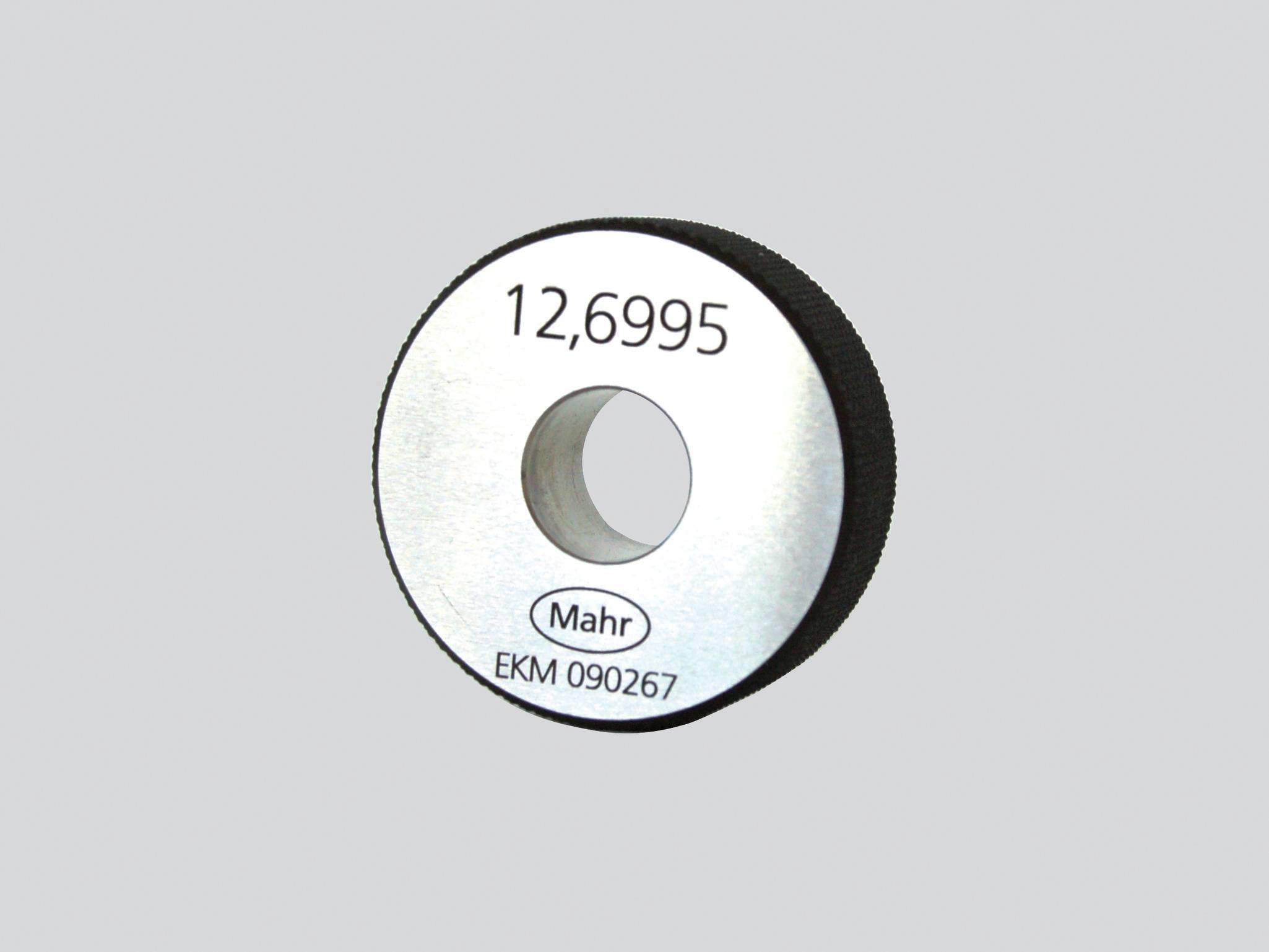
Pneumatikus mérőkészülékek (fúvókás mérőcsapok) beállítása. Gondosan edzett, öregített, csiszolt és leppelt.
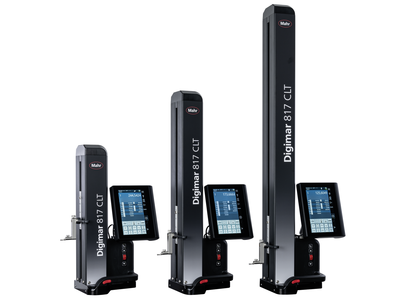
Nagyon magasan szeretne mérni? Ehhez itt a Digimar!
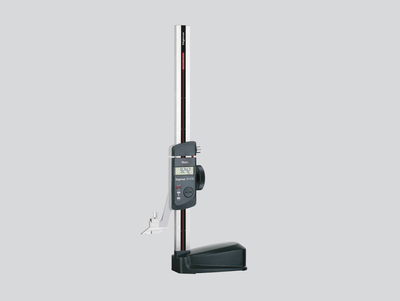
Munkadarabok előrajzolásához és jelöléséhez a műhelyben. Magasságok és távolságok egyszerű mérése.
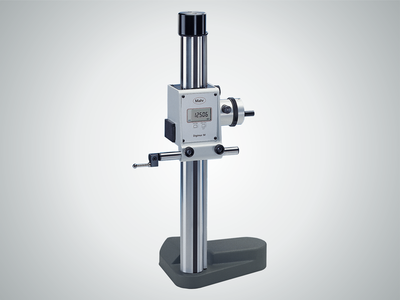
Magasságok és távolságok méréséhez furatok, felületek és élek között. Alkalmas munkadarabok előrajzolására és jelölésére további tartozékokkal.

Érintéses használat, ergonomikus kezelés és számos kiértékelési lehetőség: Ehhez a Digimar 817 CLT magasságmérő készülék áll rendelkezésre.
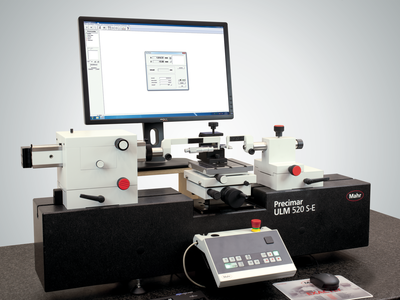
Maximális pontosság precíziós hosszméréstechnika - abszolút és relatív méréseknél.
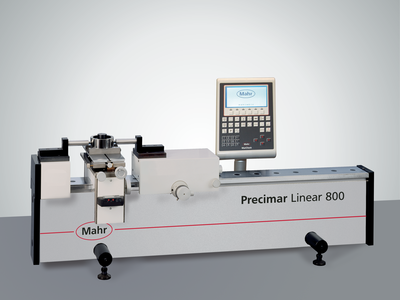
Univerzális, egyszerűen kezelhető hosszmérő és beállító készülékek a gyártáshoz

Univerzális, egyszerűen kezelhető hosszmérő és Beállító készülékek a gyártáshoz
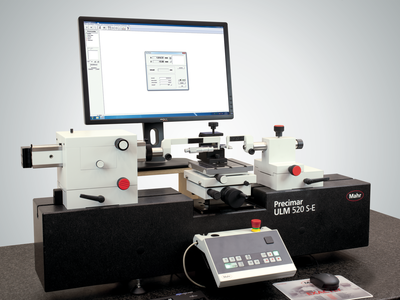
A Mahr az egyszerű mérőhasáb-vizsgáló állomást, a teljesen automatikus mérőóra-vizsgáló állomást, az ULM készülékeket és szuperpontosságú és részlegesen automatizált CiM univerzális mérőgépet magában foglaló széles termékválasztékot kínál a gyártáshoz, a mérőszobához és a kalibráló laboratóriumokhoz. Másképp fogalmazva: Maximális pontosságú méréstechnika rendkívül hatékony mérési folyamatokhoz.
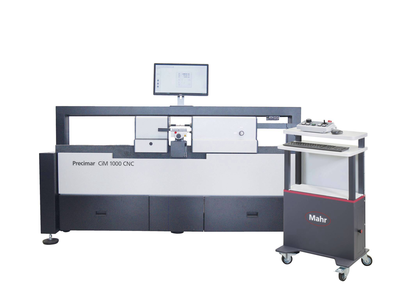
Mindegy, hogy klasszikus ULM vagy motorikus PLM CiM készülék. A Mahr univerzális hosszmérő gépek felhasználóbarát, gyors és biztonságos mérést tesznek lehetővé a lehető legkisebb bizonytalanság mellett.
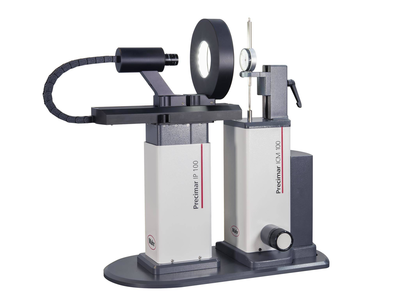
Mérőórák, szögtapintós mérőórák, finomkijelzők és tapintók részben automatikus és teljesen automatikus hatékony és pontos vizsgálata.
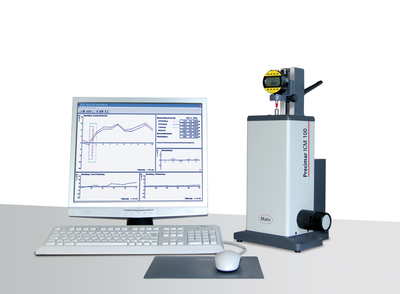
Mérőórák, szögtapintós mérőórák, finomkijelzők és tapintók részben automatikus és teljesen automatikus hatékony és pontos vizsgálata.
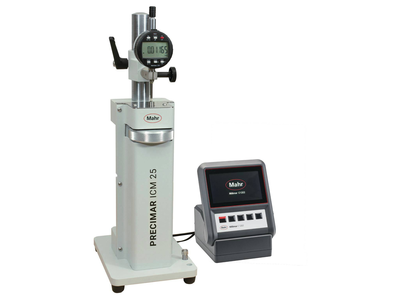
Mérőórák, szögtapintós mérőórák és finomkijelzők manuális vizsgálata - egyszerűen és pontosan
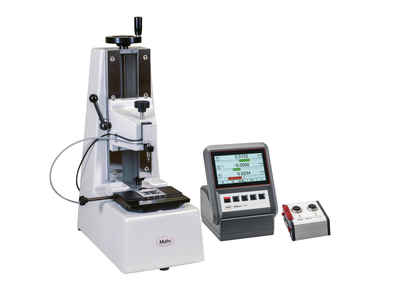
Bízzon a Mahr mérőhasáb-vizsgáló állomásaiban, mert azok képezik az etalonok pontos vizsgálatának alapját
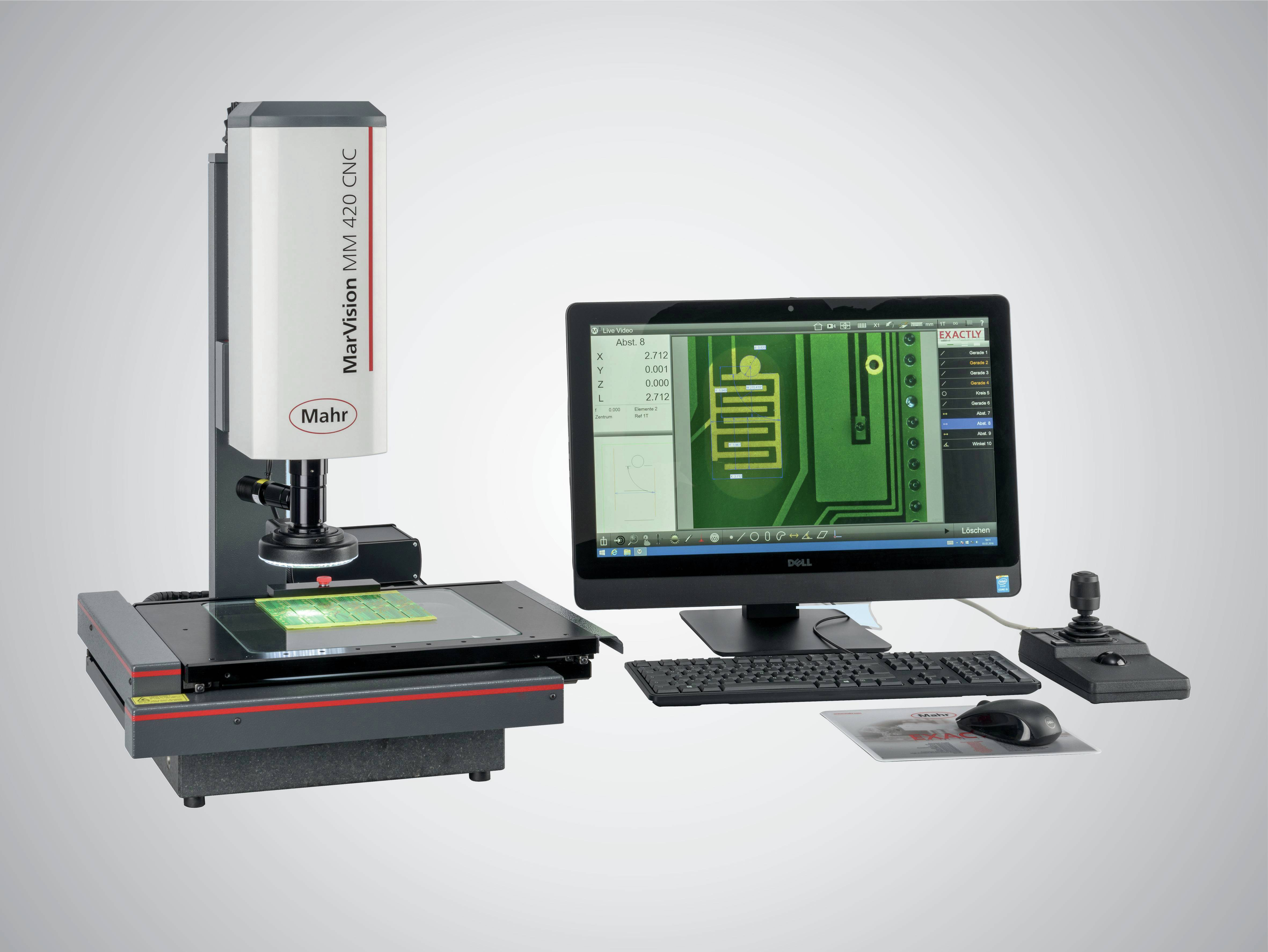
A mikroszkópokat szinte minden iparágban használják a távolságok, sugarak és szögek gyors vizsgálatára. Mindegy, hogy a laborban vagy gyártás közben.
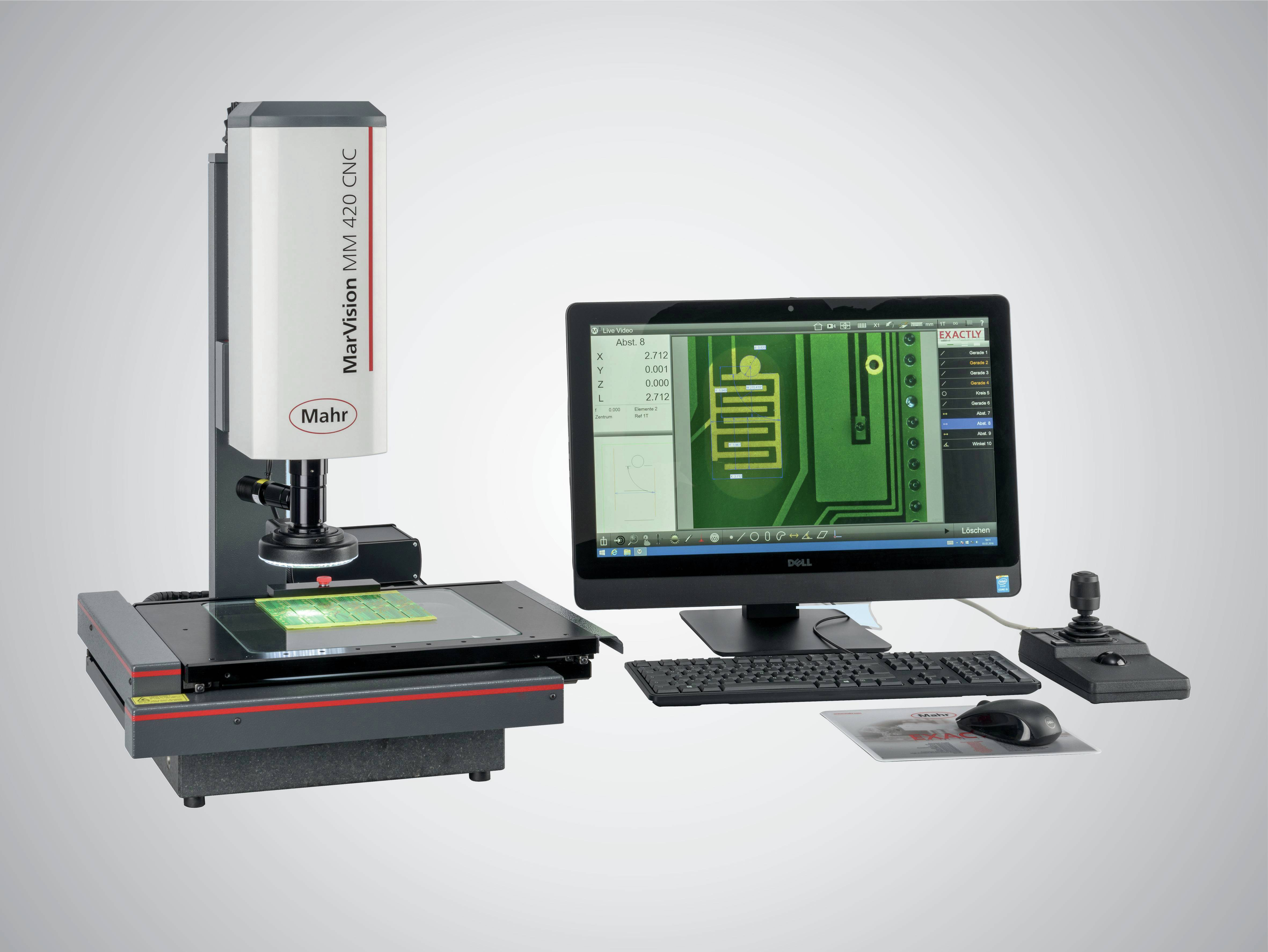
A mikroszkópokat szinte minden iparágban használják a távolságok, sugarak és szögek gyors vizsgálatára. Mindegy, hogy a laborban vagy gyártás közben.
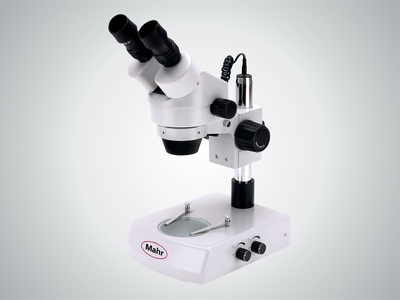
Kiváló optikával felszerelt sztereo zoom mikroszkóp fényes, éles, háromdimenziós képek készítéséhez. Két lencsés vagy három lencsés digitális kamerák kiegészítő használatával.
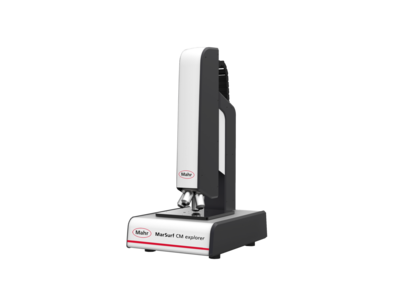
Felületmérés-technika az ipar és a kutatás számára
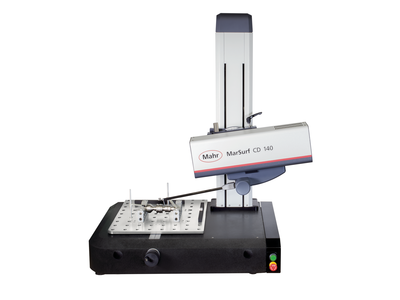
A szűk tűrésű strukturált funkcionális felületekhez nagy pontosságú mérőrendszerek szükségesek, amelyek rövid idő alatt felveszik egy munkadarab vagy objektum felületi topográfiáját.
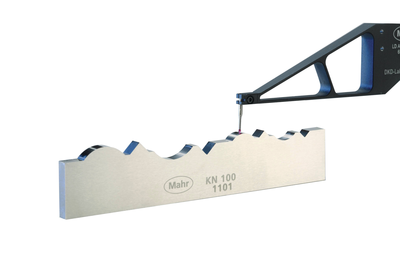
Kontúrmérés-technika a durva alaki eltérések meghatározásához.
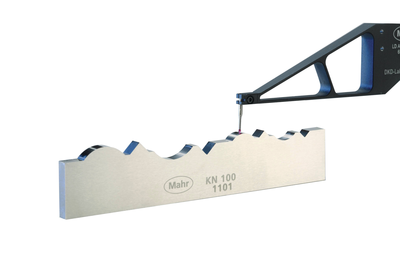
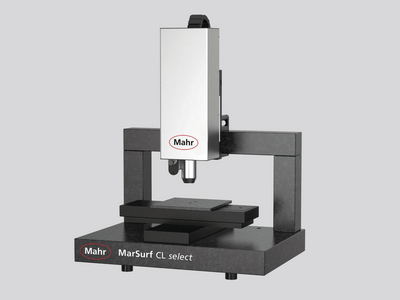
Optikai mérőkészülékekkel pontos kontúrok mérése
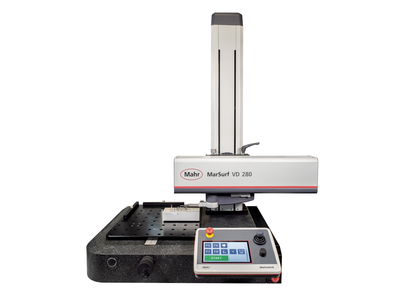
Kombinált kontúr- és érdességmérés: Profi minden esetre
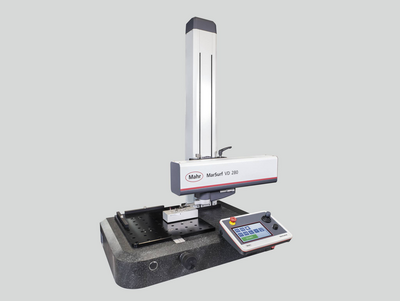
Kombinált kontúr- és érdességmérés: Profi minden esetre
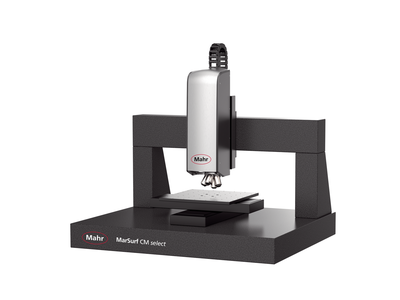
2D/3D kontúrmérés ISO 25178 / ISO 4287 szerinti érdességmérésként is
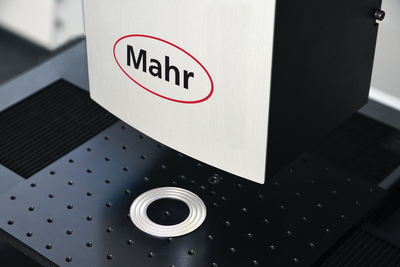
3D felületmérés-technika az ipar és a kutatás számára
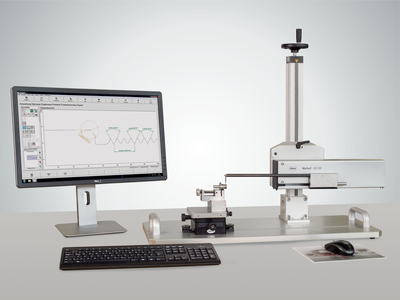
A mobil mérőkészülékekkel mindenhol mérhet!
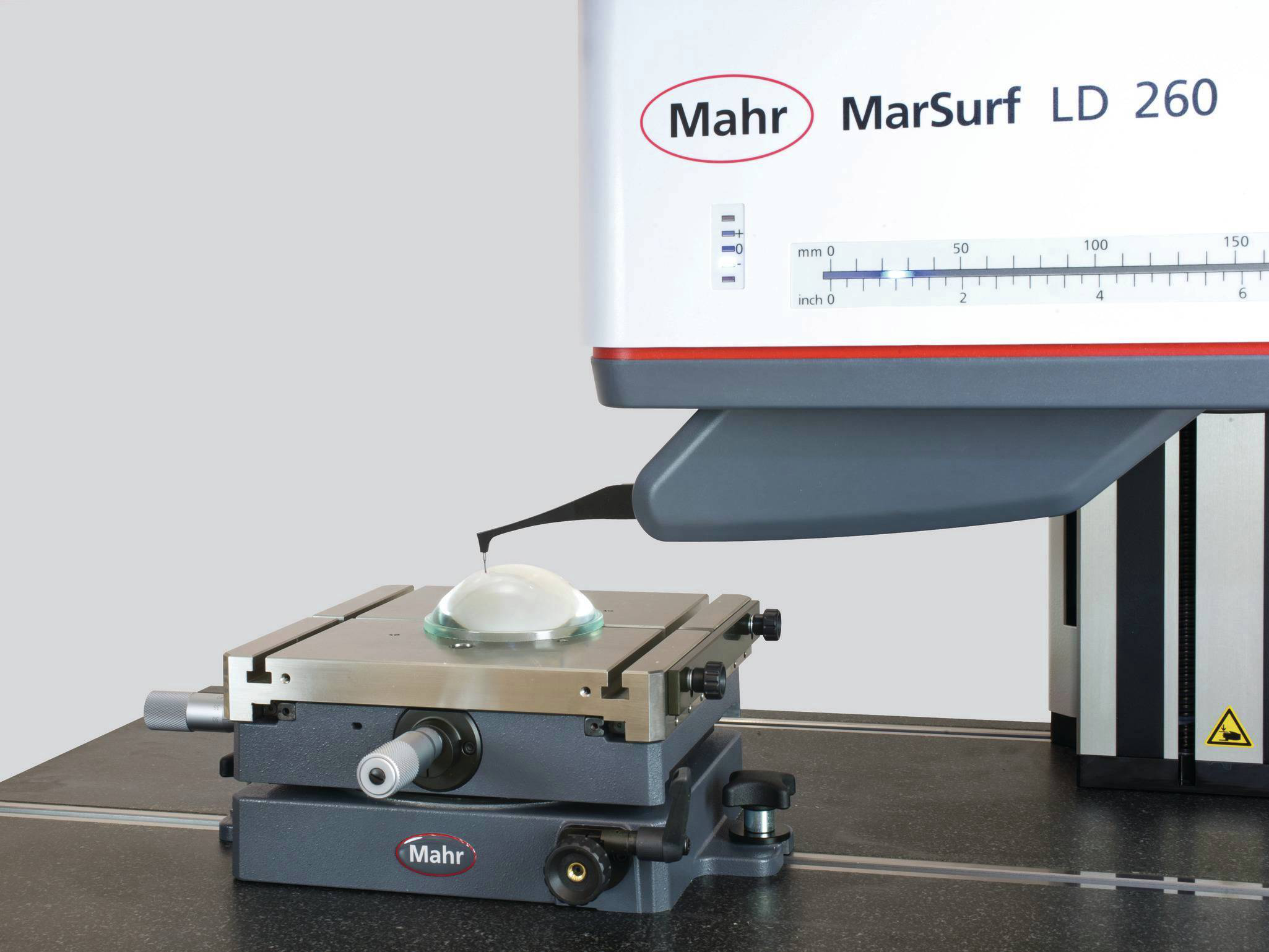
Mérőállomások nagypontosságú optikák mérésére
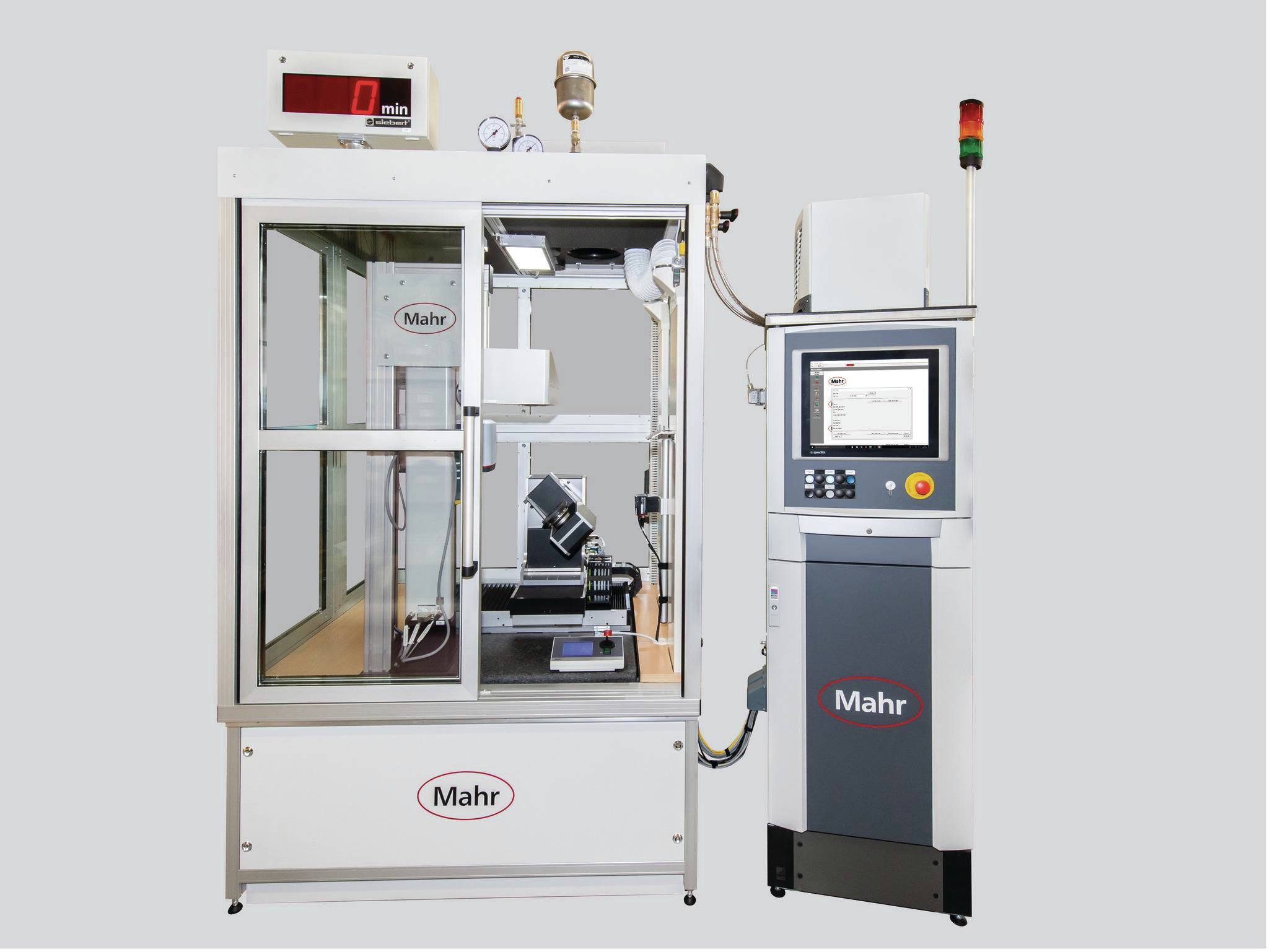
Ma már nem elég az alapfelszereltség: Egyedi megoldások az ügyfél kívánságának megfelelően
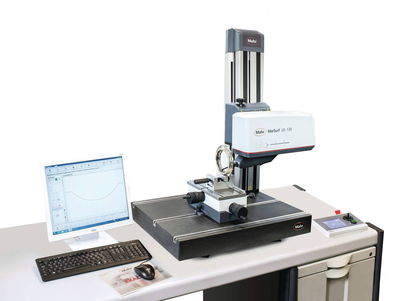
A szűk tűrésű strukturált funkcionális felületekhez nagy pontosságú mérőrendszerek szükségesek, amelyek rövid idő alatt felveszik egy munkadarab vagy objektum felületi topográfiáját.
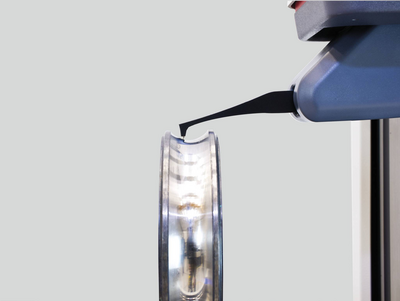
Sokoldalúság és kiváló teljesítmény a mérőszobában és a laborban
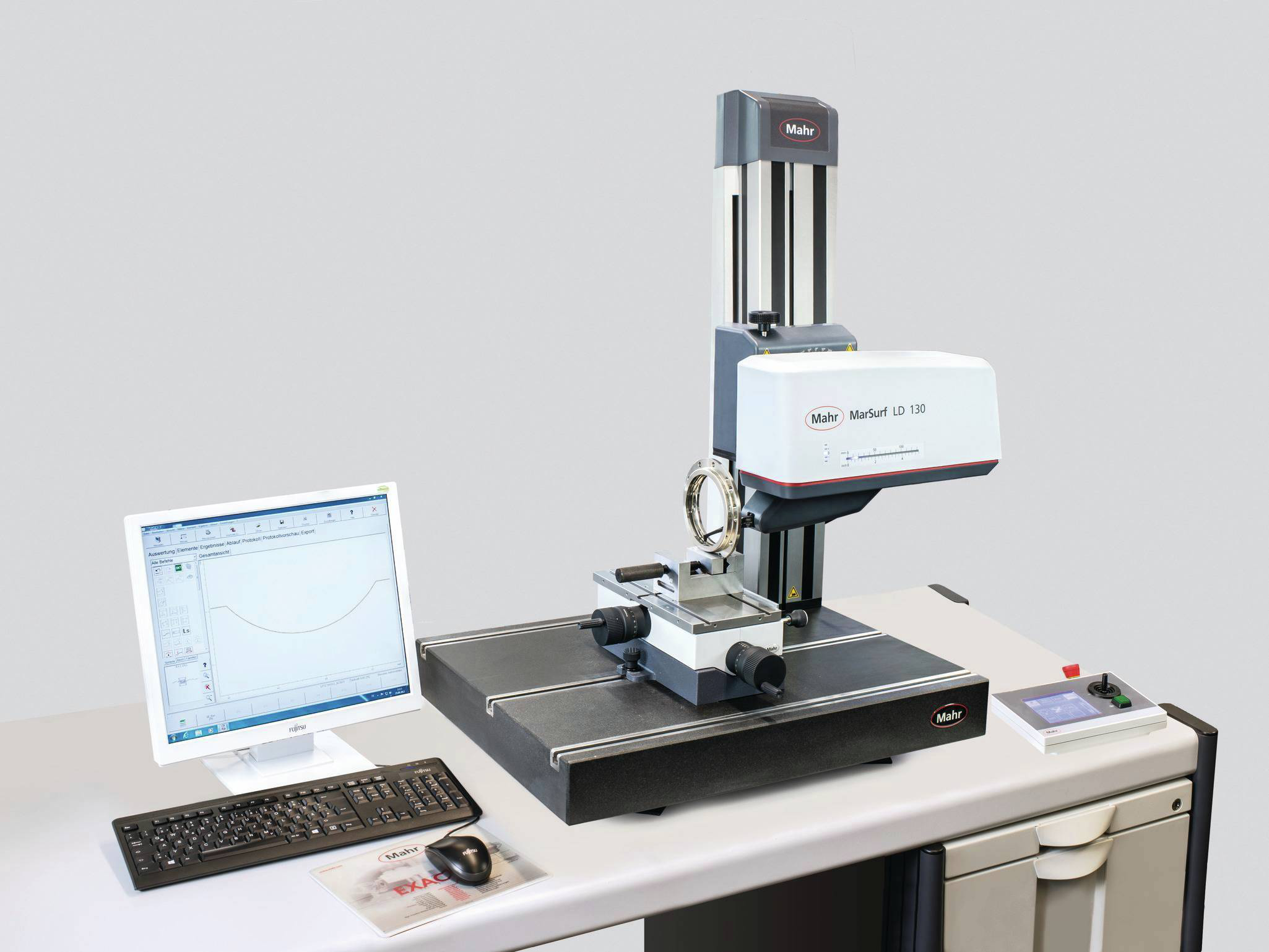
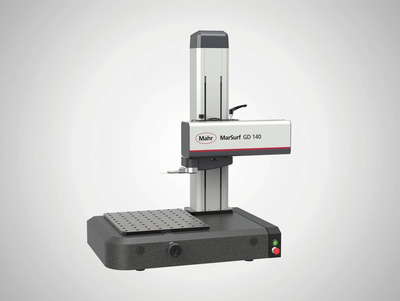
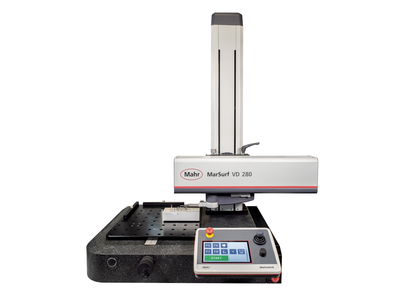
Kombinált kontúr- és érdességmérés: Profi minden esetre
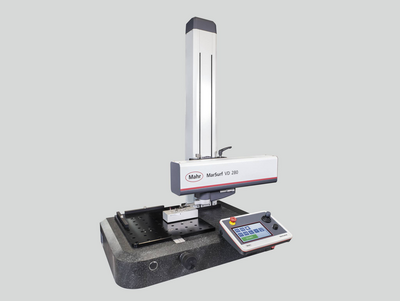
Tapintásos mérőállomások kontúr- és érdességméréshez
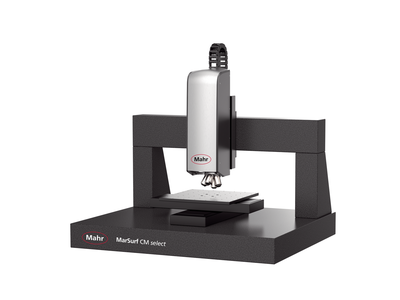
2D/3D ISO 25178 / ISO 4287 szerinti kontúr- és érdességmérés
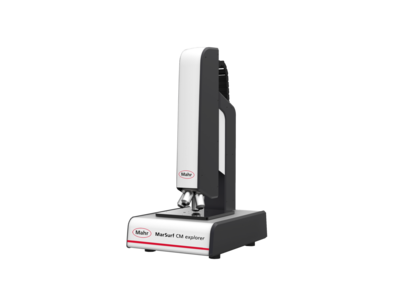
3D felületmérés-technika az ipar és a kutatás számára
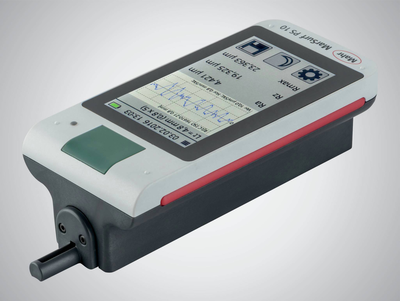
A mobil mérőkészülékekkel mindenhol mérhet!
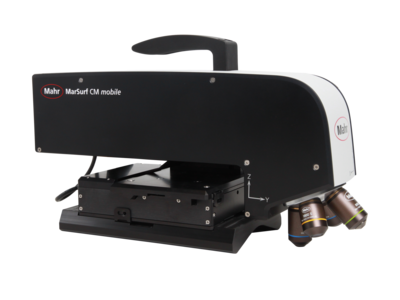
Mobil 3D felületmérés-technika
helyszíni használatra
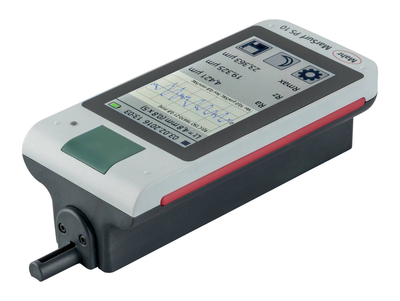
A mobil mérőkészülékekkel mindig éppen ott mérhet, ahol az eredményekre szükség van.
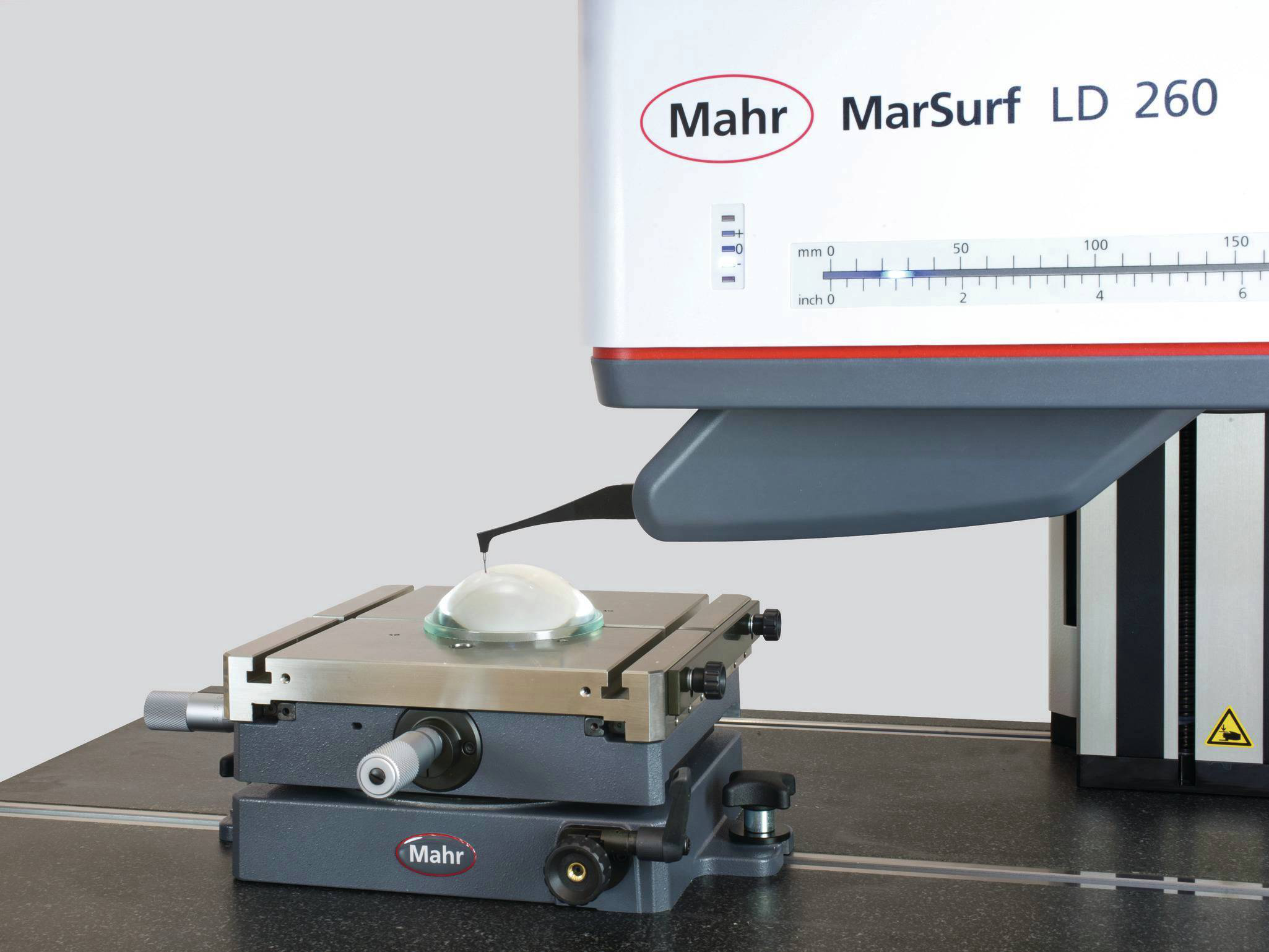
Mérőállomások nagyon érzékeny optikák mérésére
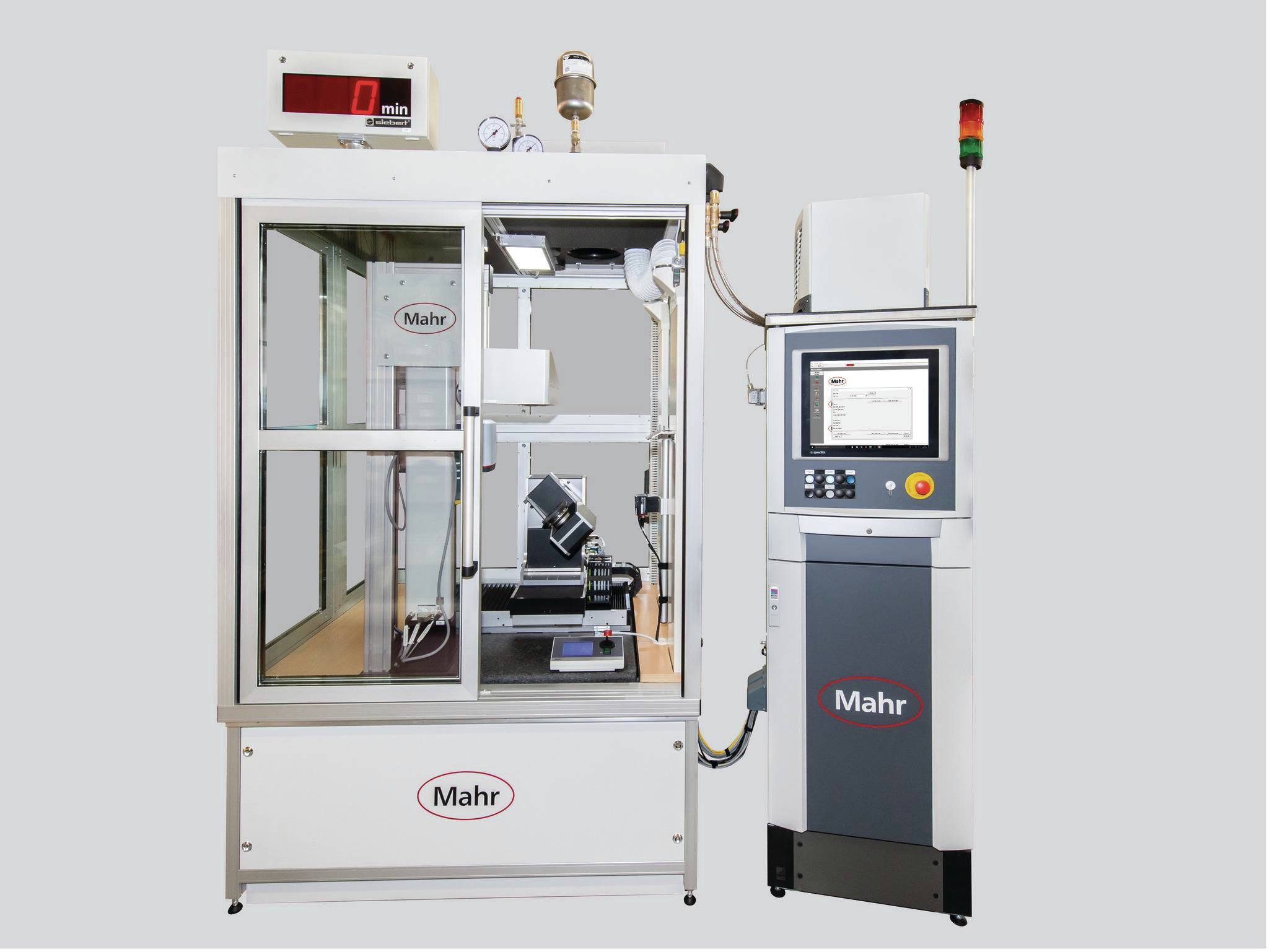
Ma már nem elég az alapfelszereltség: Egyedi megoldások az ügyfél kívánságának megfelelően
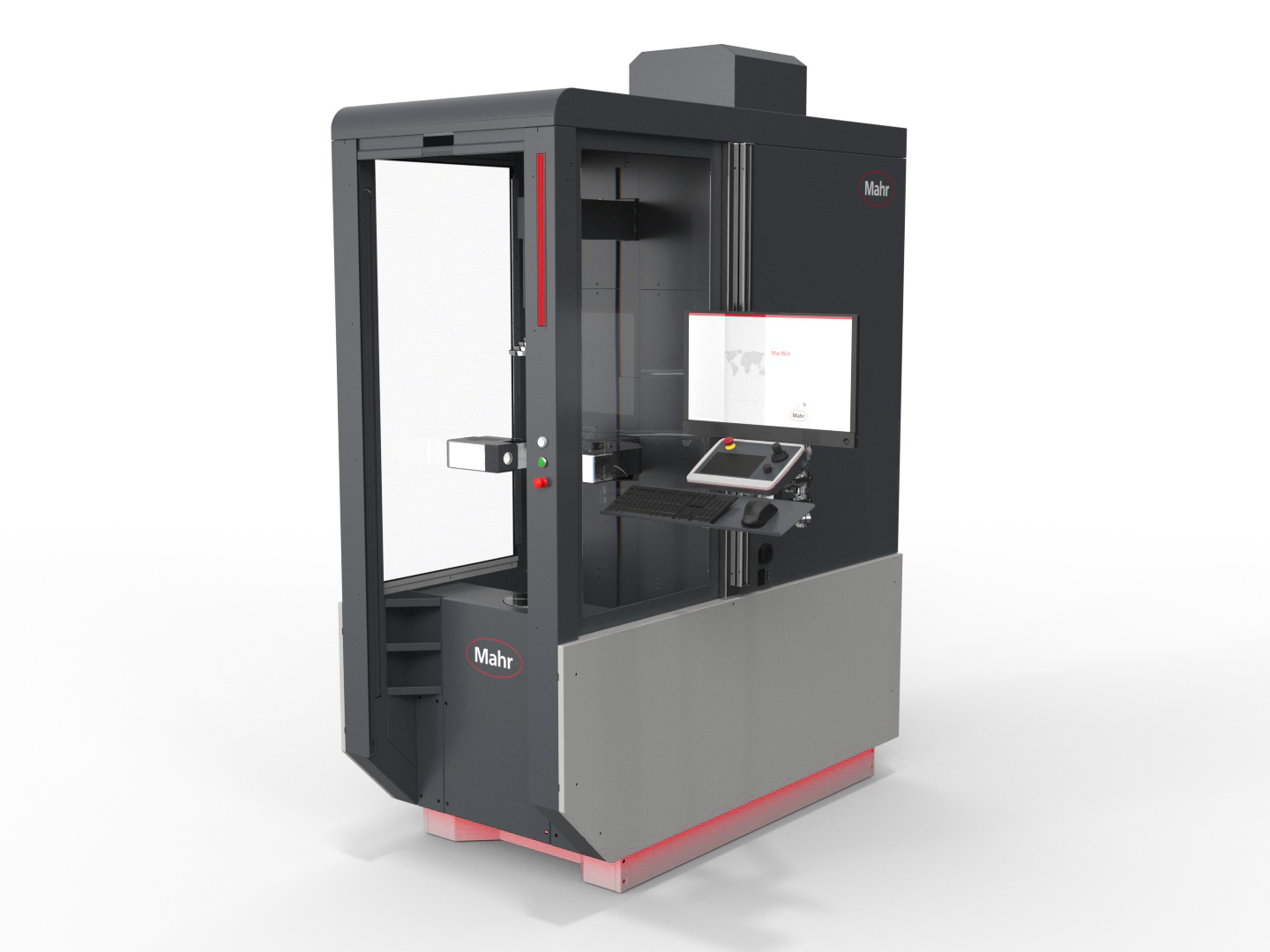
Metrology
Experience outstanding features combined with extreme flexibility in workpiece size and increase your productivity in the production environment.
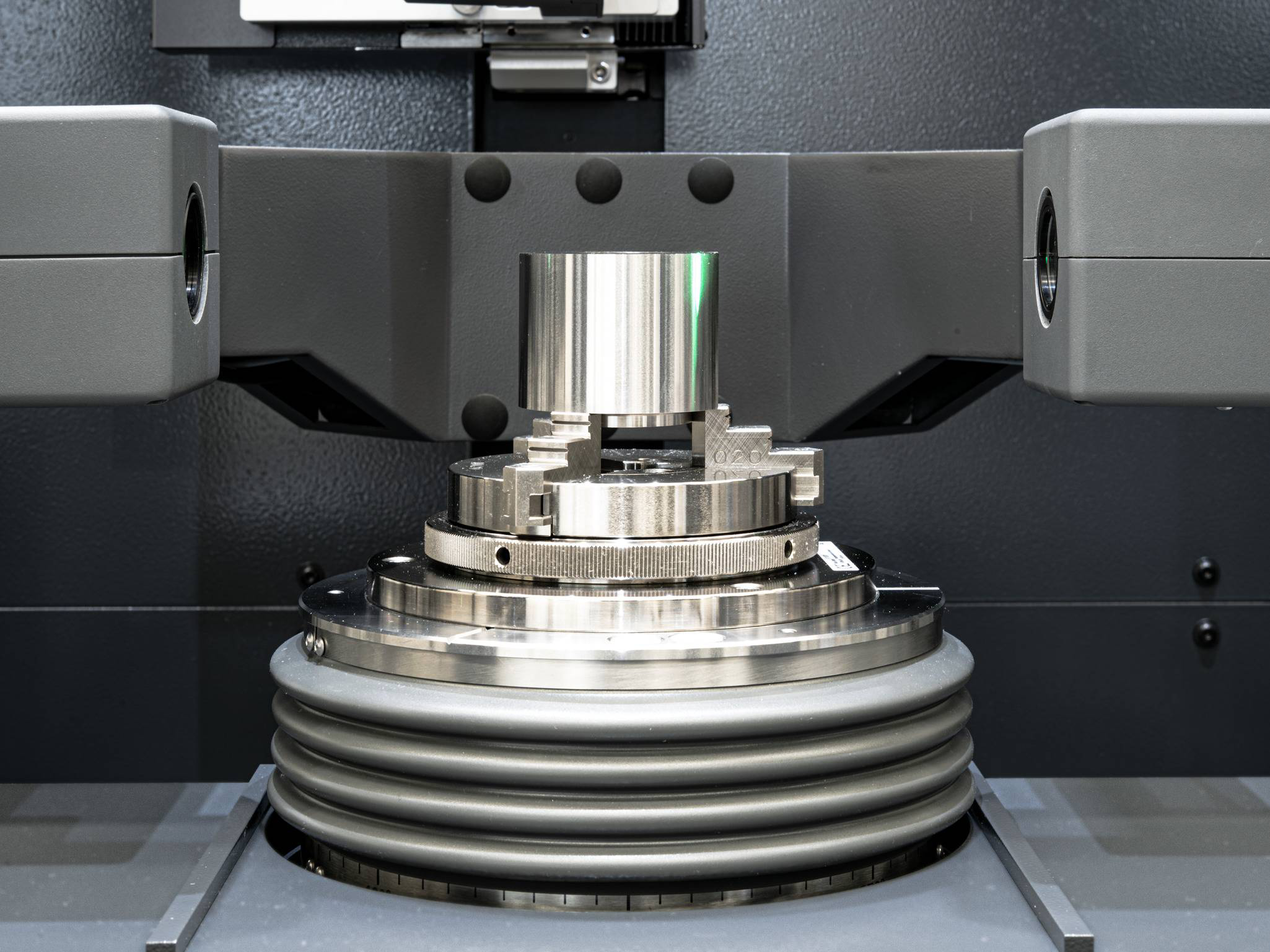
Fast optical matrix camera in combination with high-precision touch probes for measuring a large number of features on rotationally symmetrical workpieces. Addition of a fully automatic centering and tilting table for extremely fast, mechanical alignment, flexible clamping options and, for example, internal measurements.
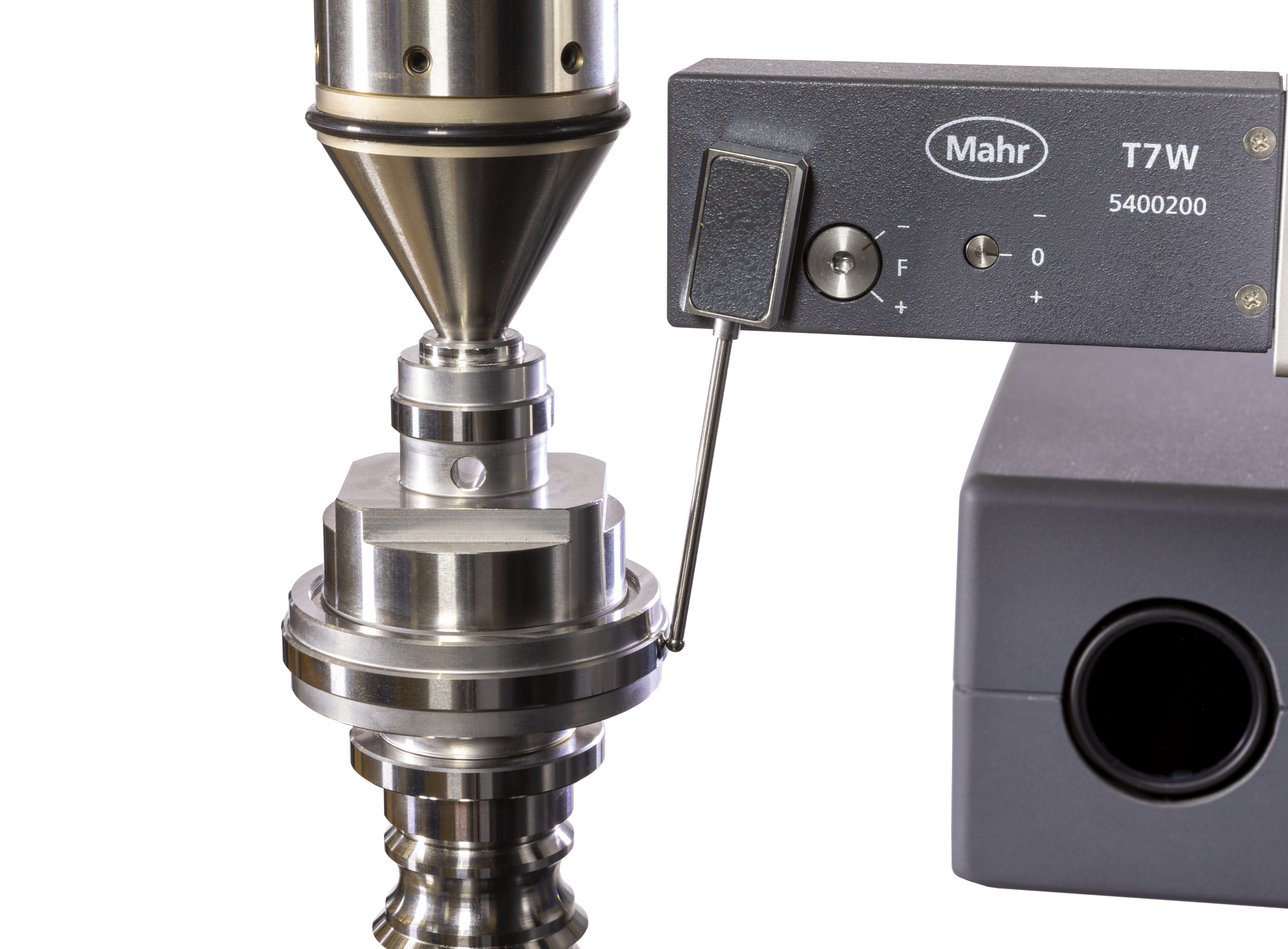
Fast optical matrix camera in combination with high-precision touch probes for measuring a large number of features on rotationally symmetrical workpieces.
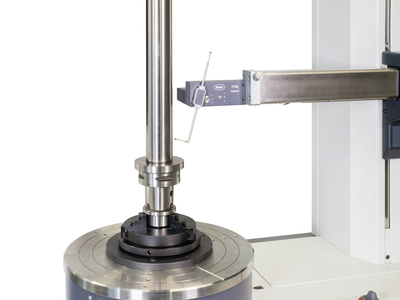
Rendszerek alak- és helyzettűrés, pl. körkörösség, síklapúság, egyenesség, egytengelyűség vizsgálatához és egyéb mérési feladatokhoz. Manuálistól a teljesen automatikusig.

Mérje költséghatékonyan, egyszerűen és mégis nagy pontossággal az olyan jellemzőket mint körkörösség, egyenesség és radiális ütés. Manuális alakmérő készülékeink alkalmasak mind a mérőszobában, mind a gyártásközi méréshez.
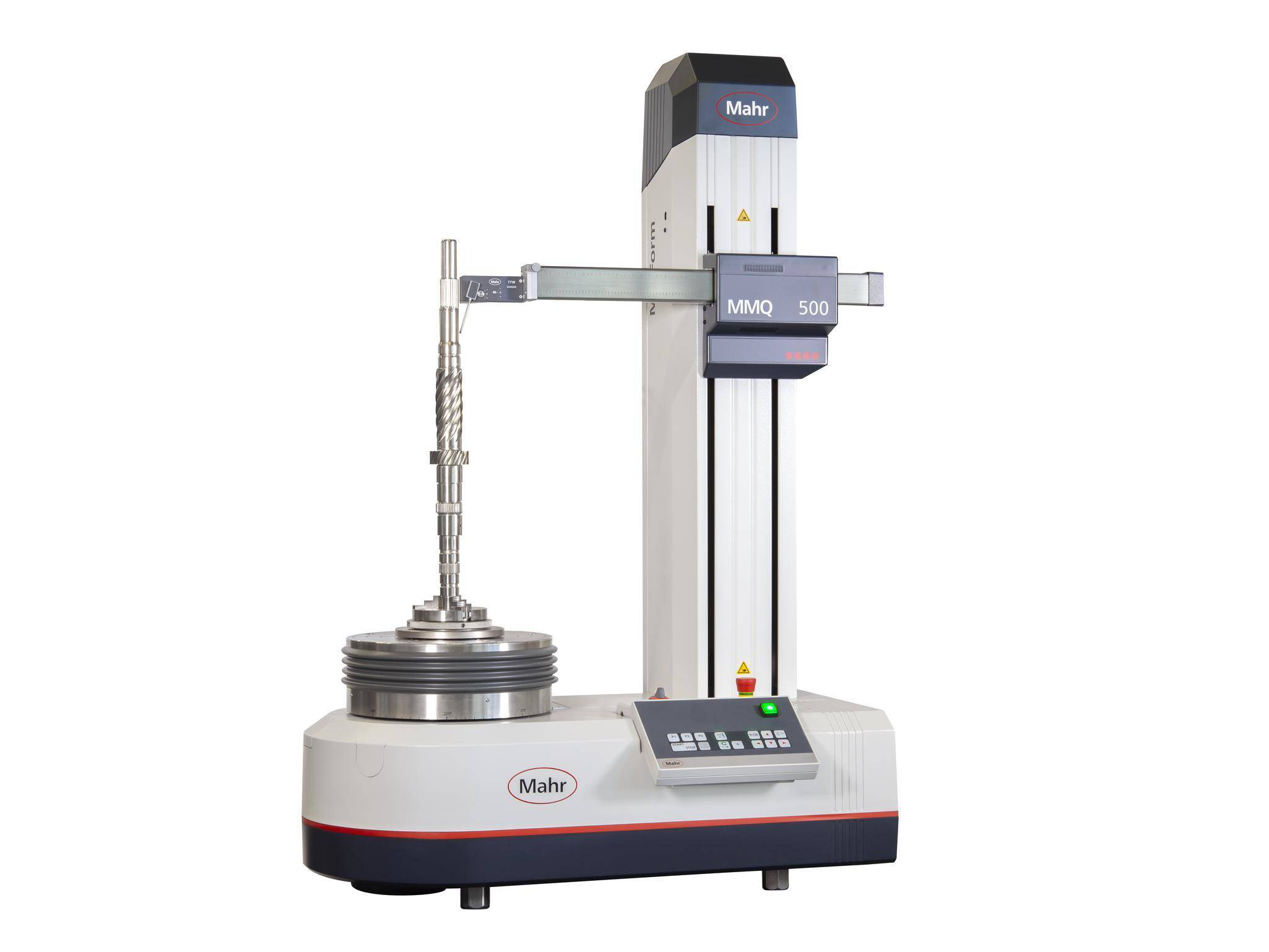
Automatikus formamérő rendszereinkkel a tesztelési költségek növelése nélkül csökkentheti a folyamat költségeit – stabil, innovatív, nagyfokú automatizálással, rugalmassággal és pontossággal rendelkező eszközökkel.
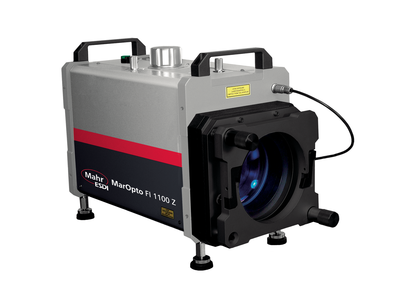
A nagy teljesítményű MarOpto Fizeau interferométerek lehetővé teszik a síkoptikák és szférikus felületek érintés nélküli mérését.
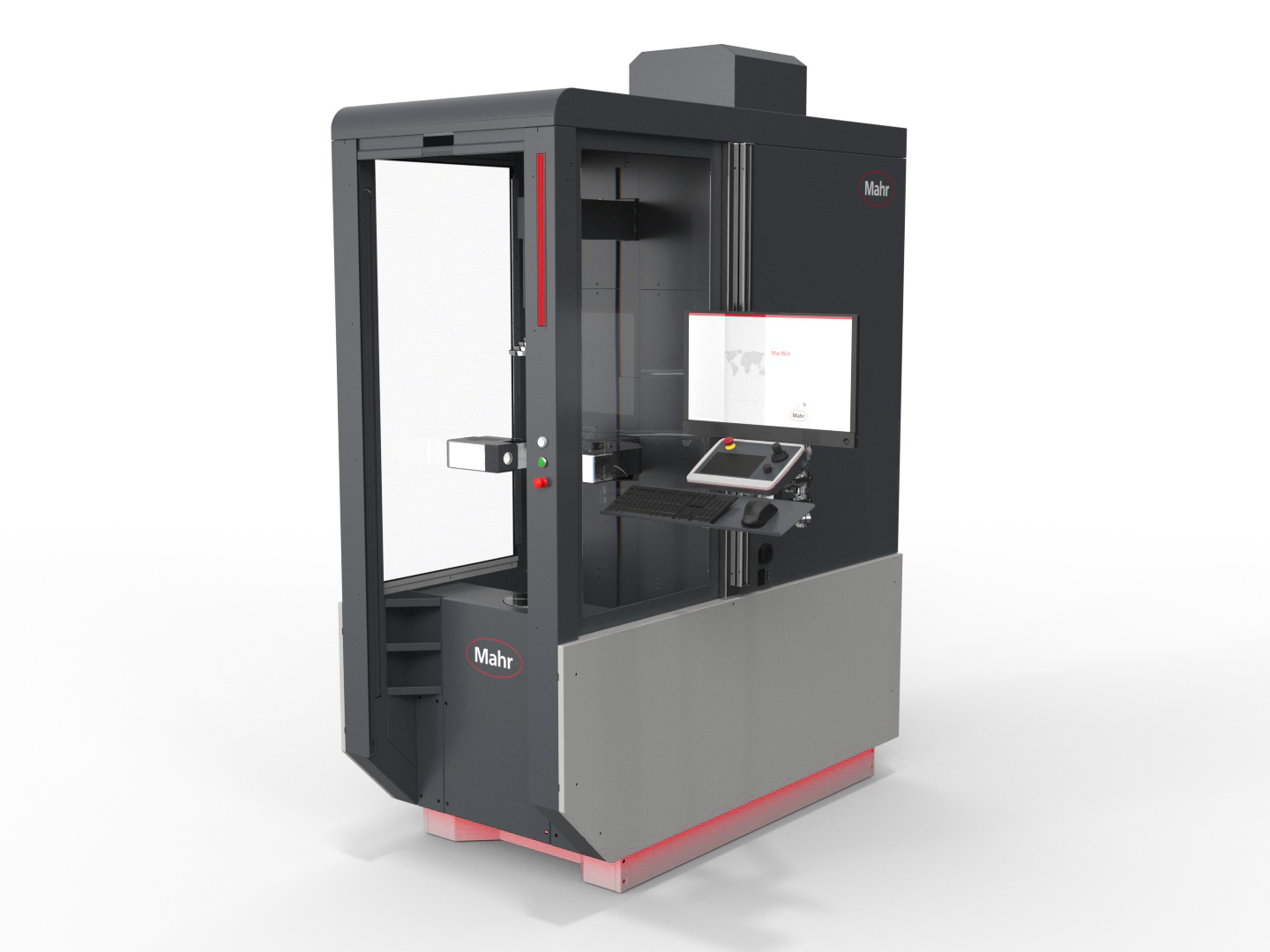
Metrology
Experience outstanding features combined with extreme flexibility in workpiece size and increase your productivity in the production environment.
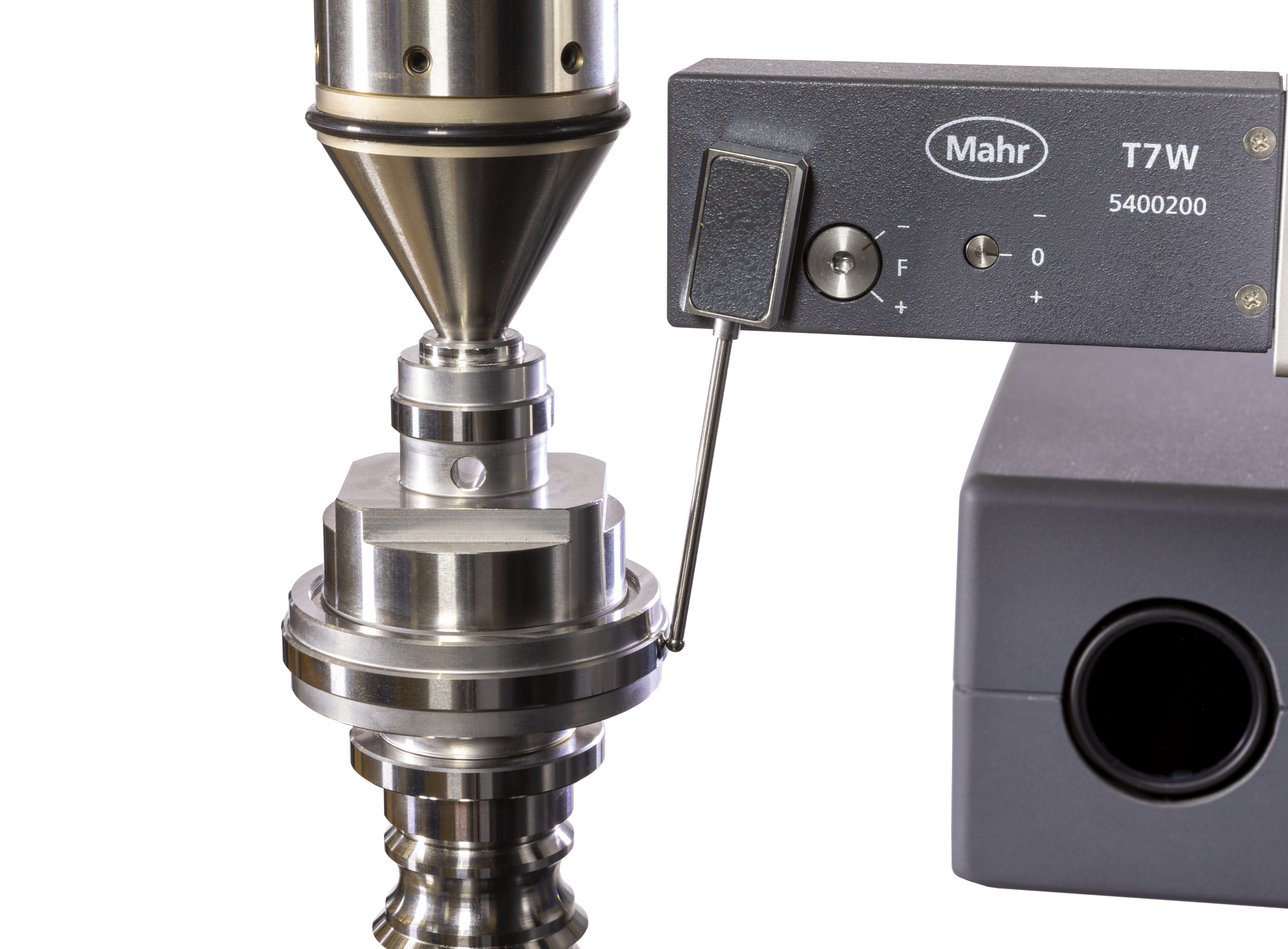
Fast optical matrix camera in combination with high-precision touch probes for measuring a large number of features on rotationally symmetrical workpieces.
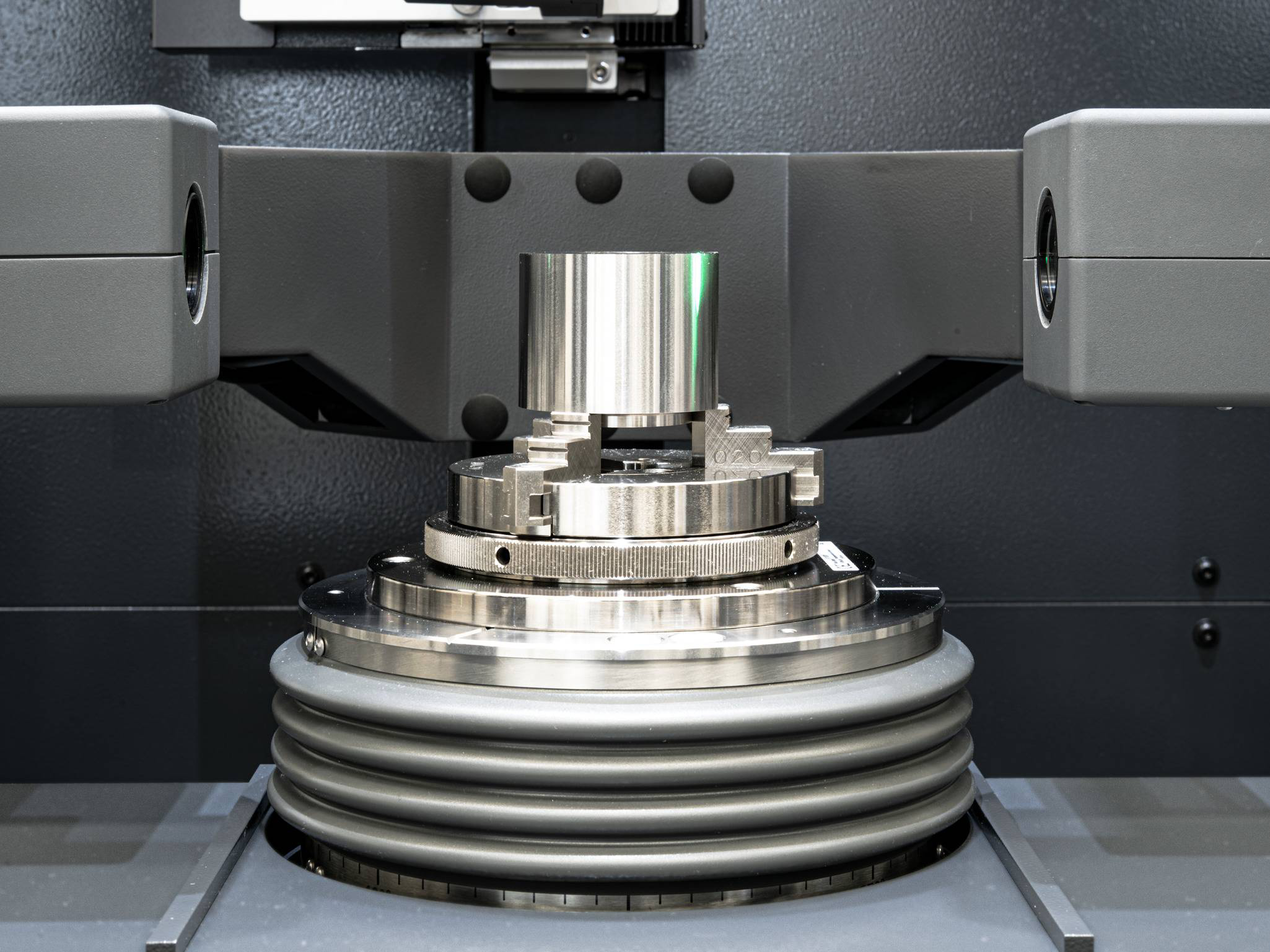
Fast optical matrix camera in combination with high-precision touch probes for measuring a large number of features on rotationally symmetrical workpieces. Addition of a fully automatic centering and tilting table for extremely fast, mechanical alignment, flexible clamping options and, for example, internal measurements.
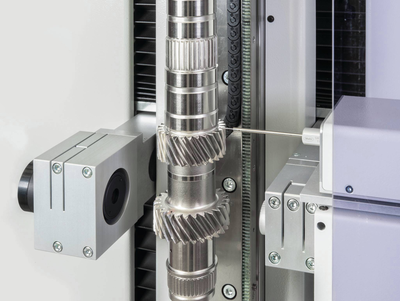
Optikai és tapintásos tengelymérő rendszerek a durva gyártási környezetben történő használatra. Minden szokásos forgásszimmetrikus munkadarab komplett mérése.
.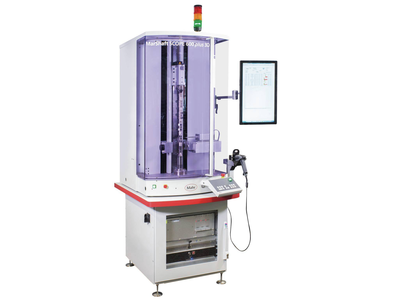
Optikai és tapintásos tengelymérő rendszerek a durva gyártási környezetben történő használatra. Minden szokásos forgásszimmetrikus munkadarab komplett mérése.
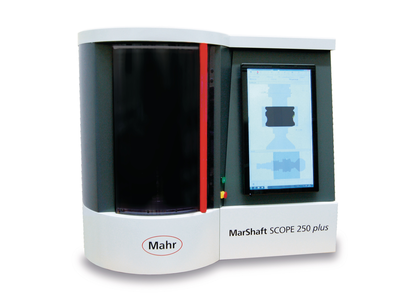
Univerzális, teljesen automatikus és robusztus optikai tengelymérő gépek durva műhelykörnyezetben történő használathoz.
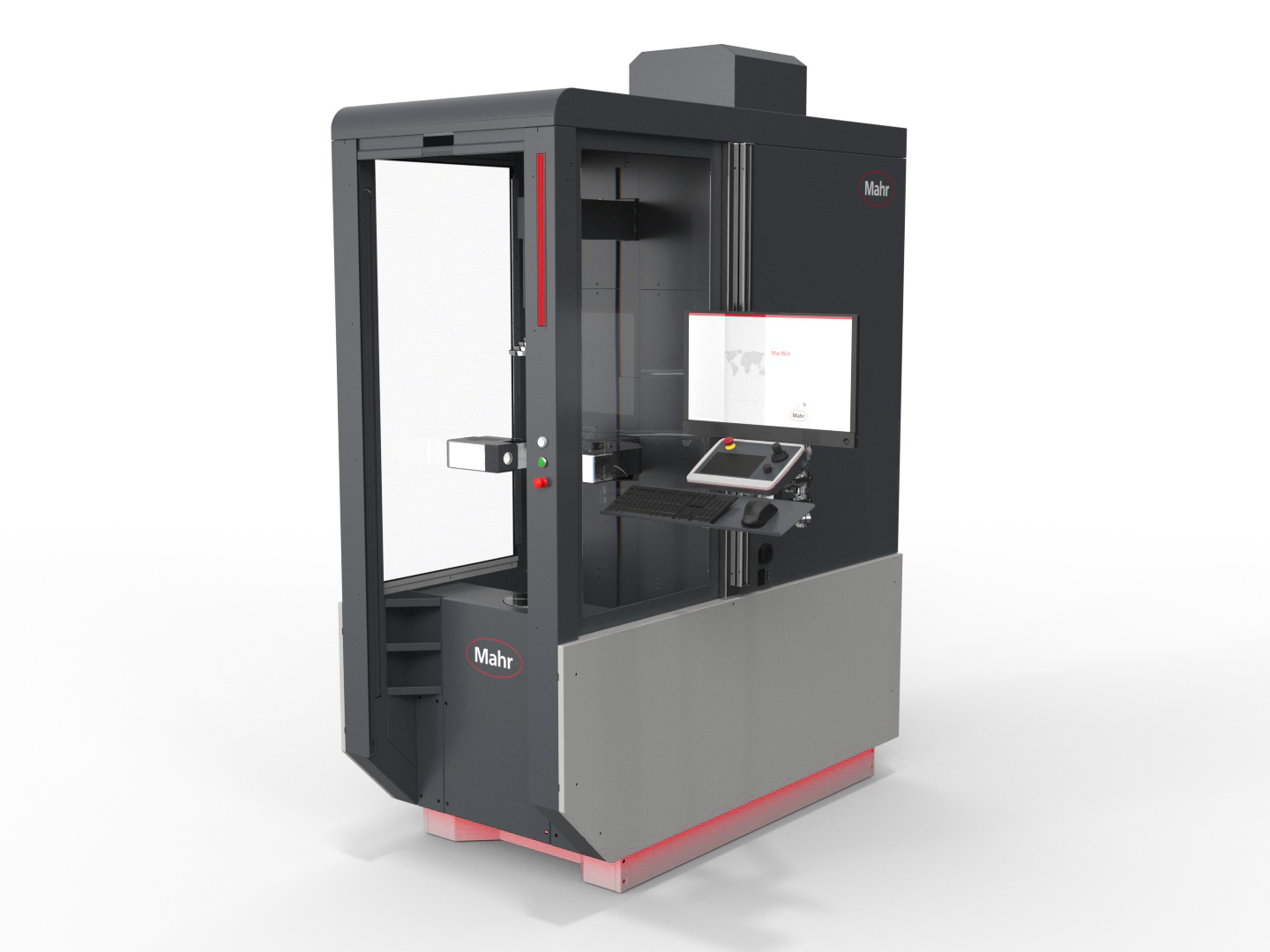
Metrology
Experience outstanding features combined with extreme flexibility in workpiece size and increase your productivity in the production environment.
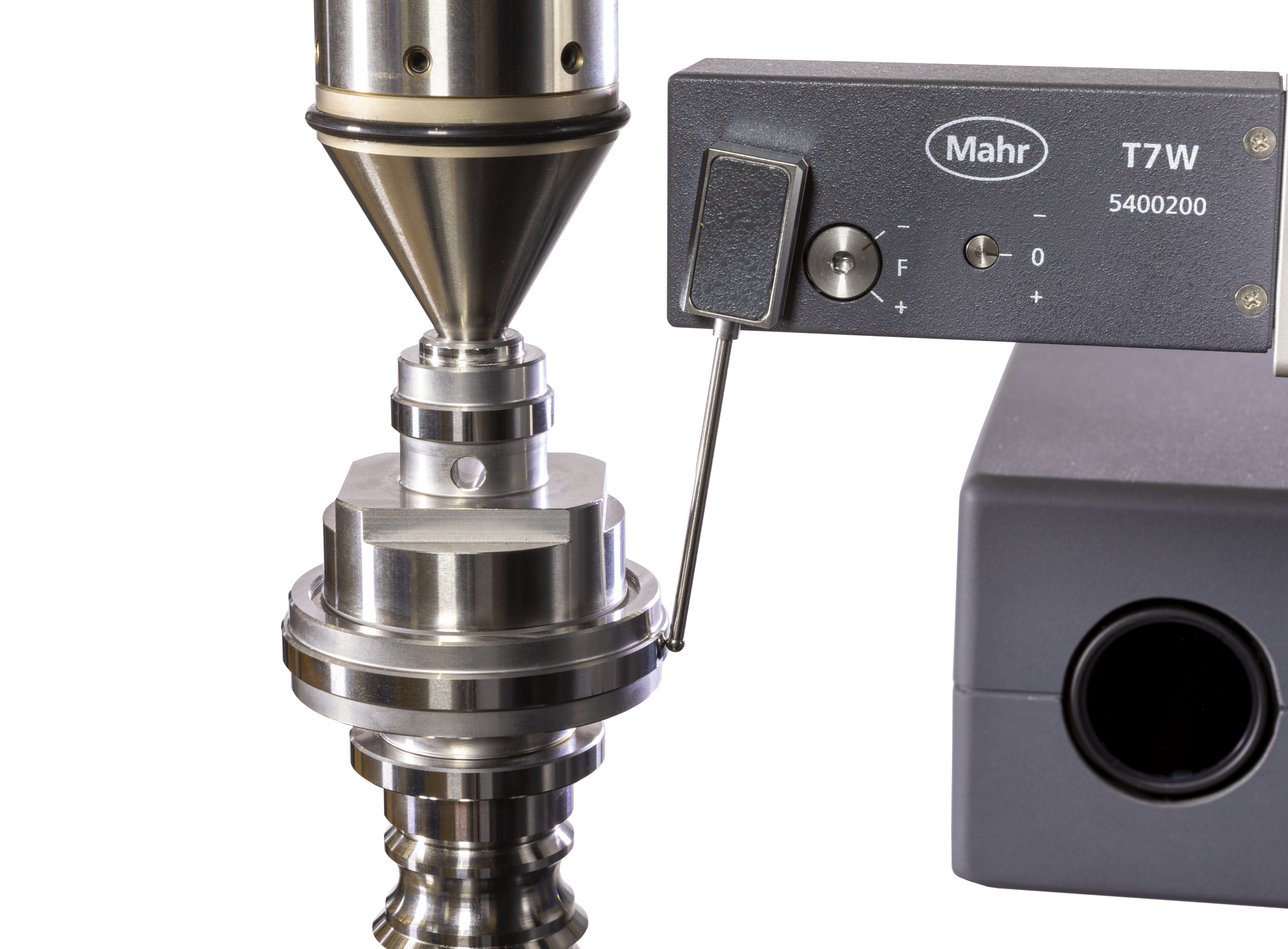
Fast optical matrix camera in combination with high-precision touch probes for measuring a large number of features on rotationally symmetrical workpieces.
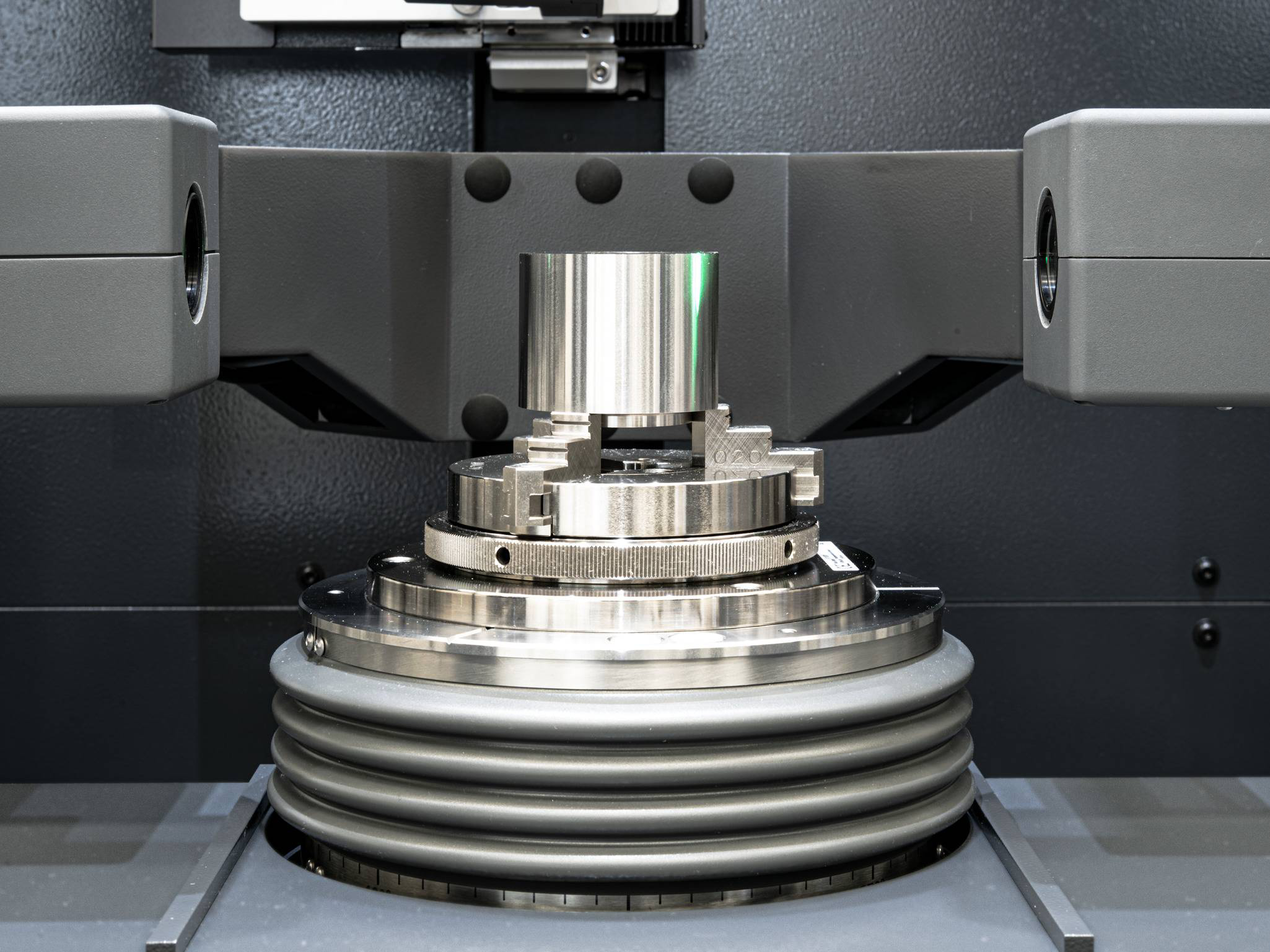
Fast optical matrix camera in combination with high-precision touch probes for measuring a large number of features on rotationally symmetrical workpieces. Addition of a fully automatic centering and tilting table for extremely fast, mechanical alignment, flexible clamping options and, for example, internal measurements.
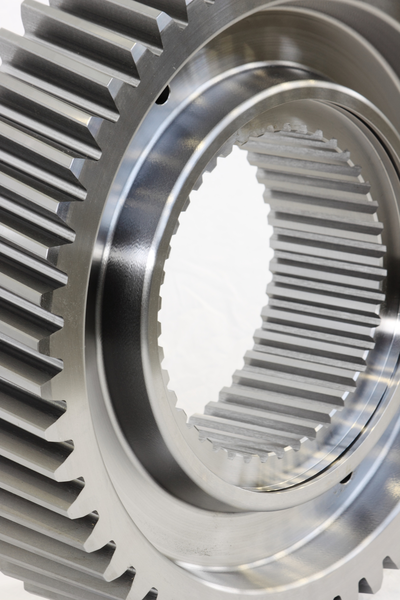
A nagyon speciális fogazáselemzésektől a teljesen integrált sorozatmérésig a Mahr a modern fogaskerék- és hajtóműgyártás minden szintjén az Ön partnere.
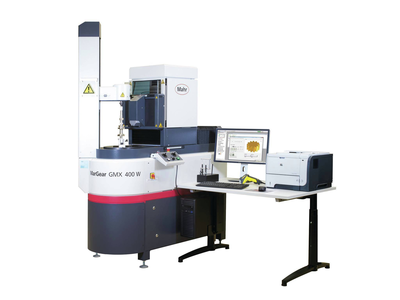
A MarGear készülékek flexibilis fogazat- és hengerkoordináta-mérőkészülékek. A MarGear a megfelelő választás, ha gyártás közben több különböző jellemző gyors visszajelzésére van szükség. A fogazások alakjának, helyzetének, dimenziójának nagy pontosságú és teljesen automatikus vizsgálata: A MarGear megoldja a mérési feladatot.
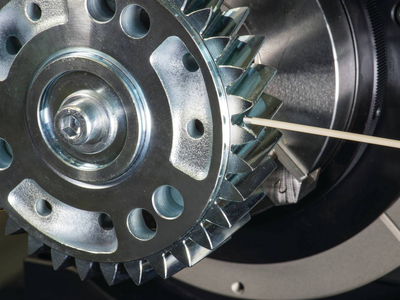
Selejt keletkezésének elkerülése érdekében pontosan ott mérjen, ahol a termék keletkezik és biztosítsa a gyártási folyamatra vonatkozó gyorsabb visszajelzést.
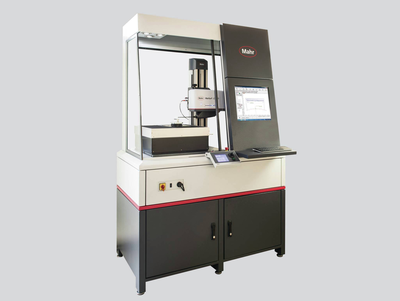
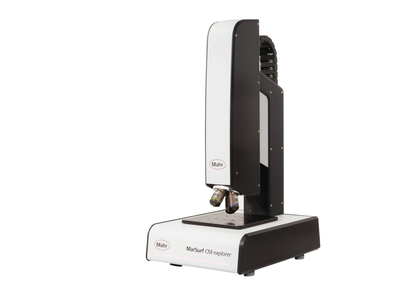
Technológiák és termékek széles választéka a felületek és geometriák gyors és érintés nélküli rögzítéséhez.
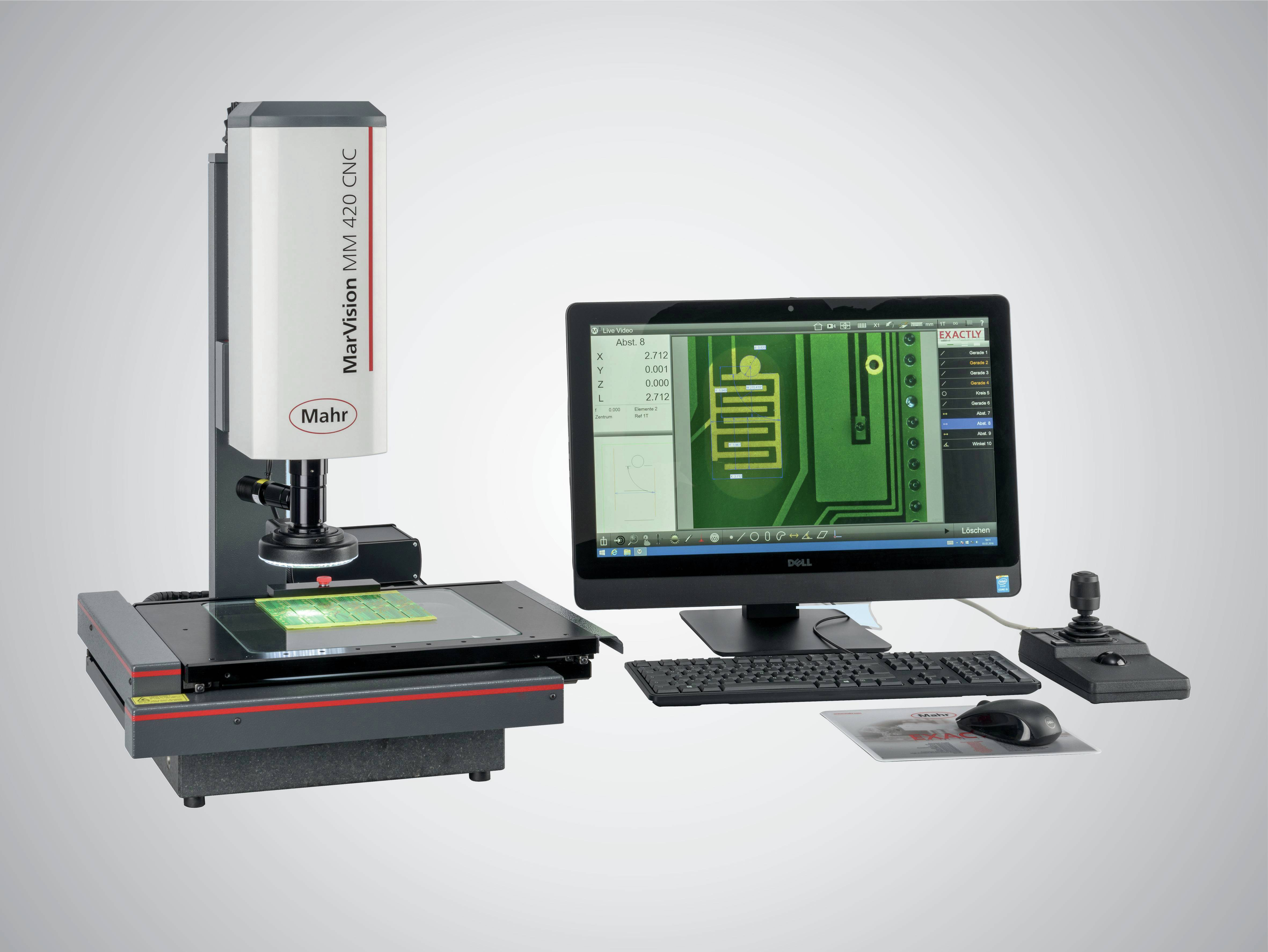
A mikroszkópokat szinte minden iparágban használják a távolságok, sugarak és szögek gyors vizsgálatára. Mindegy, hogy a laborban vagy gyártás közben.
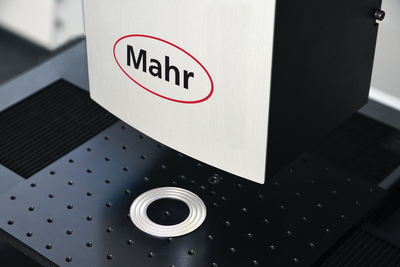
Érdesség, kontúr és sok más felületi paraméter meghatározása.
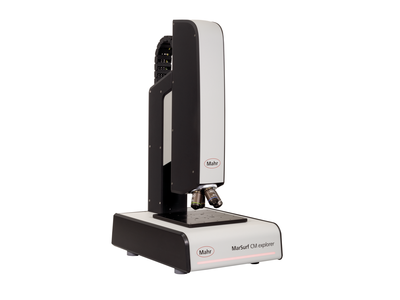
Felületmérés-technika az ipar és a kutatás számára
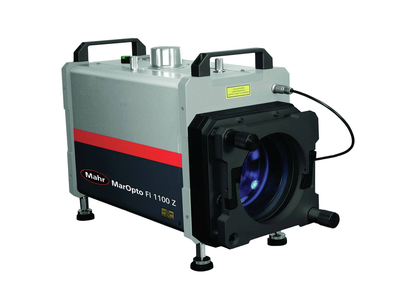
Mindegy, hogy fehér fény vagy lézer interferométer, mindig megtalálja a megfelelő megoldást az alkalmazáshoz.
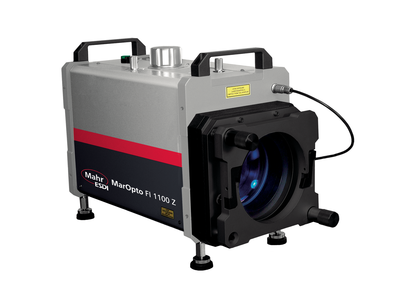
A nagy teljesítményű MarOpto Fizeau interferométerek lehetővé teszik a síkoptikák és szférikus felületek érintés nélküli mérését.
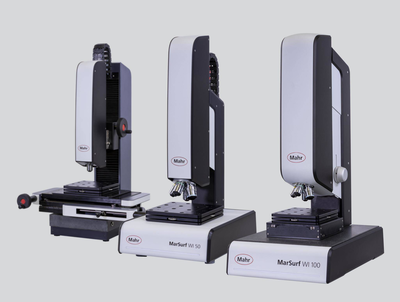
Minimális érdességek - nanométeres pontossággal
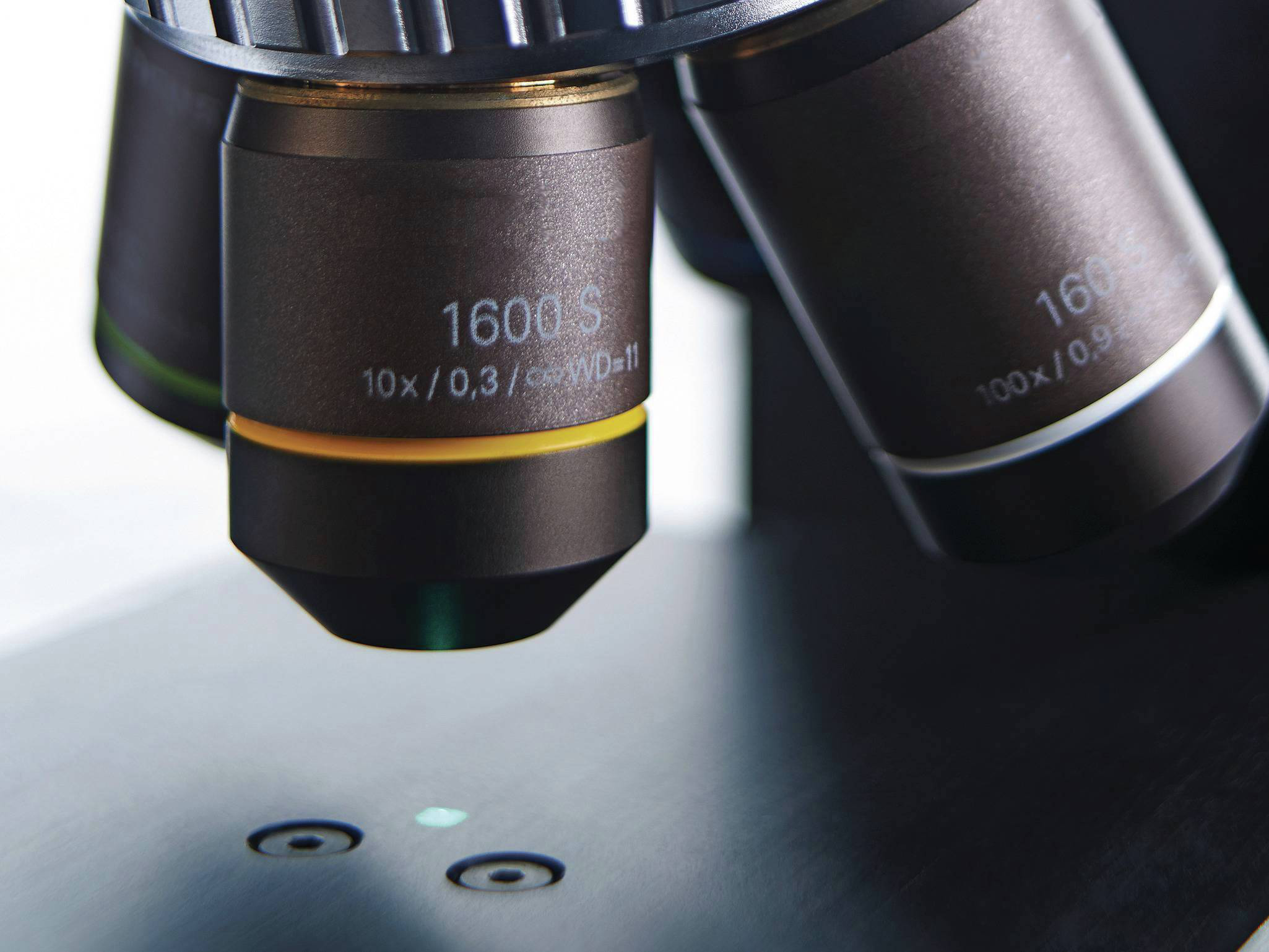
Felületi topográfiák és geometriák optikai elemzése
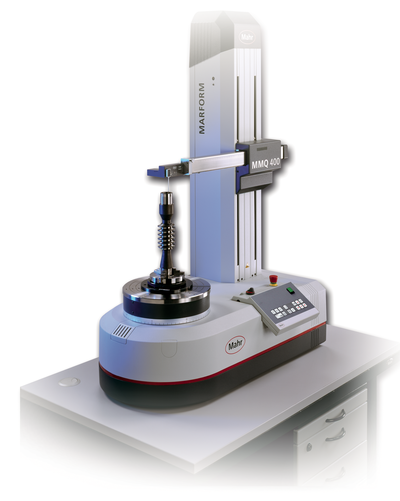
Megújult rendszerek a bevált Mahr minőségben
Pneumatikus méréstechnika alkalmazása ortopédiai berendezéseknél
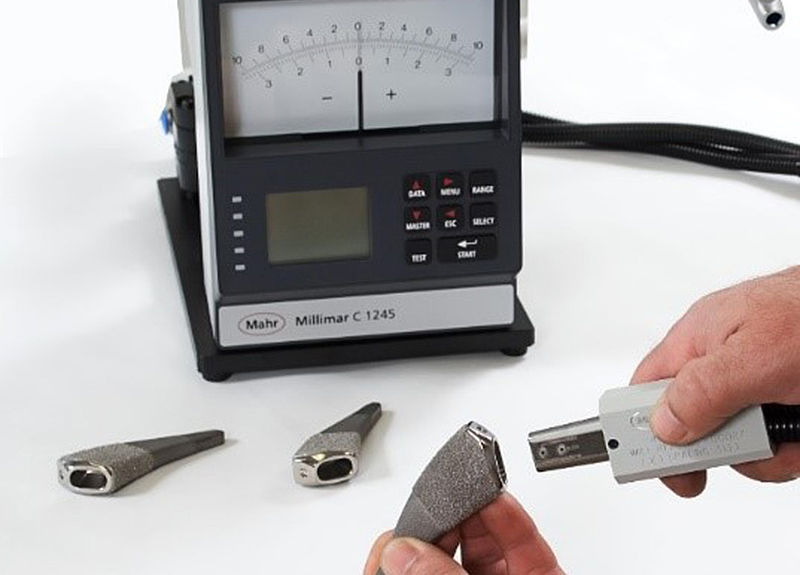
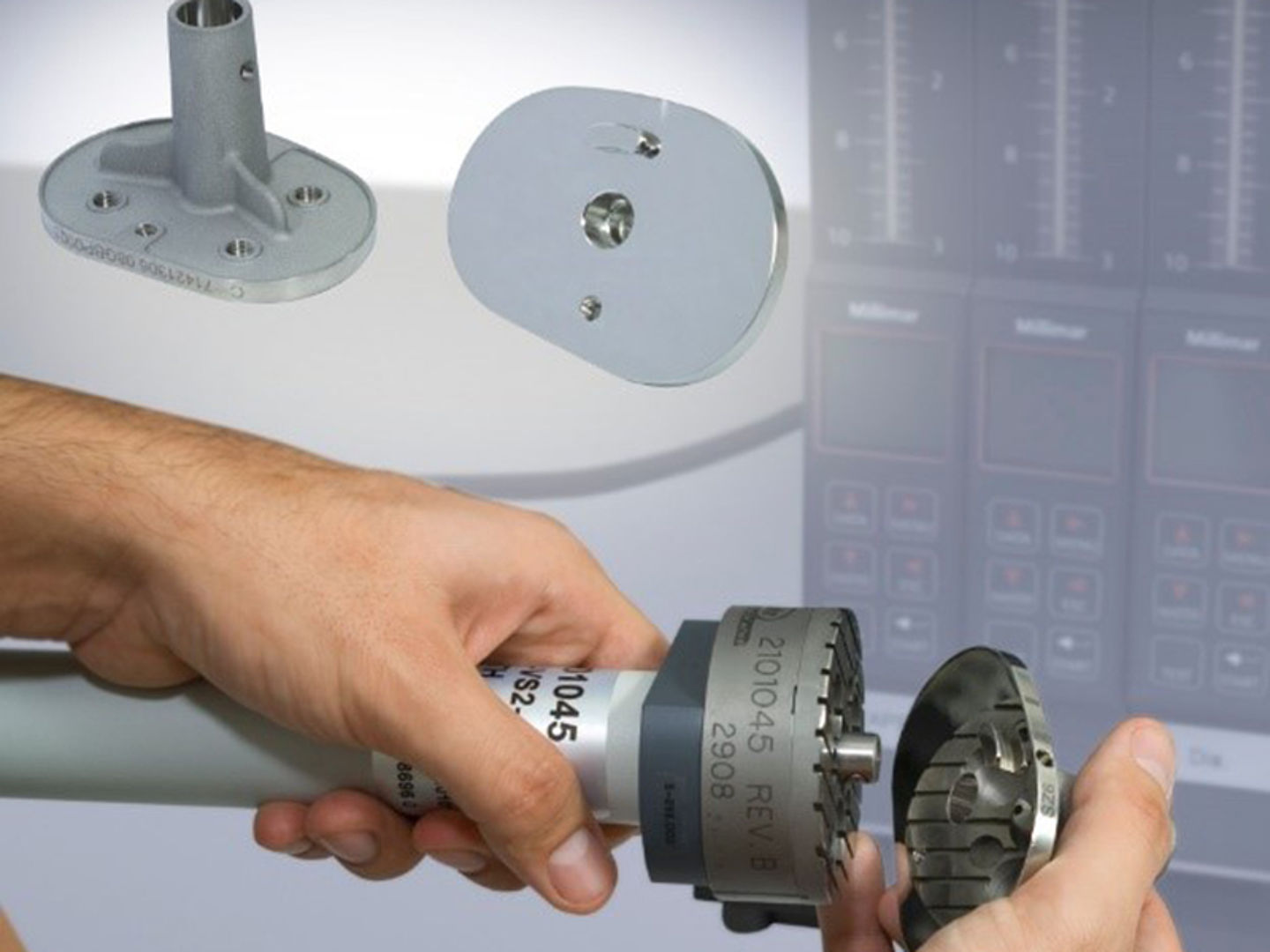
Az ortopédiai precíziós alkatrészek csak akkor tudnak megfelelni a magas minőségi szabványok követelményeinek, ha minden egyes gyártási lépés (az első vágástól a végső feldolgozásig) következetesen stabil. Ehhez a jellemzők folyamatorientált ellenőrzése, a tűrések túllépésekor küldött azonnali visszajelzés és az összes folyamatadat dokumentálása szükséges.
Jellemzően, ahogy a munkadarabok a nyersanyagtól a végtermékig végighaladnak a gyártási folyamaton, a mérettűrés, a felületminőség és a geometriai jellemzők egyre kritikusabbak - egyre kritikusabb ezeknek a tűréseknek a betartása vagy felismerése a tűrés átlépése esetén. Az ortopédiai berendezések gyártási folyamatának végén mért egyik méretjellemző a kúpos felületeken az egyes alkatrészek illeszkedésének szűk tűrése. Például a csípő- és térdimplantátumok többségénél kúpos felületeket használnak az optimális beállításához és a komponensek megfelelő pozícióban történő biztonságos „rögzítéséhez”. Fenti alkatrészek gyártása során már a kúp alakjának és méretének ellenőrzése meghatározza, hogy milyen lesz az ortopédiai implantátumok teljesítménye élettartamuk során.
Miért a pneumatikus méréstechnika a leghatékonyabb módszer?
Tekintettel az egyre szűkebb tűrésekre, a mérőkészülékeknek egyre stabilabbnak kell lenniük, és megfelelő tervezési jellemzőkkel kell rendelkezniük, hogy az alkatrészeket megfelelően fogják be. A szükséges tűrések méréséhez megfelelő felbontással és pontossággal is kell rendelkezniük. A pneumatikus méréstechnika itt egyre inkább a kritikus paraméterek ellenőrzésének előnyben részesített vizsgálati eszközzé vált. A pneumatikus mérőkészülékek különösen pontosak és nagyon nagy felbontást nyújtanak. Általában olyan alkalmazásokhoz használják, ahol a tűrések szűkek - általában ±25 µm alattiak, és a felületi érdesség kisebb Rz=6,3 µm-nél. Ilyen körülmények fennállása esetén, pl. orvosi alkalmazásokhoz használt precíziós kúpoknál, a pneumatikus méréstechnika gyakran a legjobb megoldásnak bizonyul.
A pneumatikus mérés különösen alkalmas a méretviszonyok vizsgálatára is; a pneumatikus mérőkészülékek gyorsan, könnyen használhatóak és hosszú élettartamúak, még a legkeményebb használati feltételek között is, annak érdekében, hogy több millió alkatrész mérését lehessen végrehajtani. Bizonyos esetekben a pneumatikus méréstechnika akár az alkatrész meghatározott alakjellemzőinek vizsgálatára és értékelésére is használható.
A mérőfúvóka, vagyis minden olyan kis nyílás, amelyből levegő távozik, az oka annak, hogy a pneumatikus méréstechnika ennyire hasznos az ortopédiai kúpos felületek méréséhez. Egyetlen más mérőszenzor sem ilyen kicsi, vagy nem helyezhető el olyan közel a mérési helyhez, ha több átmérőt vagy geometriai alakot kell mérni. Bár a kisméretű elektronikus szenzorok vagy örvényáram-érzékelők mérete megközelítheti a mérőfúvóka méretét, de nem tudnak lépést tartani gazdaságosságukkal vagy a termelési területen történő közvetlen használatra való alkalmasságukkal.
Lehetséges az átmérő és a kúp mérése akár elektronikus szenzorok kombinációjával, akár éltapintós koordináta-mérőgép (CMM) segítségével. A mérőfúvóka közvetlenül precíziós készülékbe szerelhető, így az alkatrész közvetlenül a gyártásban történő mérésére használható. Ily módon a mérés egyetlen gyors mérési folyamatban, minimális kezelői erőfeszítéssel végezhető el. Sem a CMM, sem az optikai méréstechnika nem biztosítja a szükséges sebességet és pontosságot a munkadarabok 100%-os gyártásközi ellenőrzésének végrehajtásához és a folyamatteljesítmény azonnali visszajelzésének biztosításához.
Vizsgálóeszköz megfelelő kivitelének kiválasztása
Gyakorlatilag annyi módszer létezik a kúpos alakra vonatkozó követelmények meghatározására, mint ahány kúpos alkatrészgyártó létezik. A referenciafelület gyártótól függően változhat, a tűrések különböző módon adhatók meg.
Attól függően, hogy az egyes alkatrészeket hogyan kell egy egységgé összeállítani, a kúp tűrései szűkebbek lehetnek, mint az átmérőké, vagy fordítva. Alternatív megoldásként kúpok tűréseinek kombinációja is megadható csak egy átmérőn. Így a rajzon található adat a legjobb iránymutatás a pneumatikus mérőeszköz legmegfelelőbb változatának kiválasztásához. A pneumatikus méréstechnikánál a vizsgálóeszközöket kifejezetten minden egyes kúpos alkalmazáshoz készítették, így döntő jelentőségű a követelmények munkadarab-specifikus vizsgálata. Ennek a mérési módszernek a rugalmassága és előnyei mégis szinte felülmúlhatatlanok: nagyon nagy felbontást kínál, a mérőszenzorok változatosan kombinálhatók annak érdekében, hogy tetszőleges számú dimenzionális és geometriai mérési adat közvetlenül a gyártásban történő fogadása lehetséges legyen.
Különböző típusú pneumatikus kúpmérő eszközök
Az orvosi implantátumoknak rendkívül tartósnak és ellenállónak kell lenniük, hogy a kúpos illeszkedés a két rész között nagyon pontos legyen. A két résznek biztonságosan kell összekapcsolódniuk egymással, és megfelelő magasságban kell lenniük. A gyártásban szokásos gyakorlat az, hogy az alkatrészek 100%-át megvizsgálják a két alkatrész gyártási pontosságának biztosítása érdekében. Ez általában differenciális pneumatikus méréstechnológia segítségével történik, amely egyesíti a szükséges nagy felbontást és pontosságot a gyártási területen megkövetelt gyorsasággal, egyszerű működéssel és robusztus kivitellel.
A pneumatikus kúpmérő eszközök leggyakoribb típusában két pár fúvóka van két mérési síkban elhelyezve, és a munkadarab és a mérőeszköz közötti köpenyes rendszerre van méretezve (lásd ábrák). Ha a kúpszög túl nagy, a kisebb kúpvégen nagyobb holtjáték van a két felület között. Ha a kúpszög túl kicsi, a nagyobb végen van nagyobb holtjáték. Mindkét esetben ez csökkentheti az alakzáró kapcsolatot, aminek következtében a „biztonságos kapcsolat” idővel megszűnhet, ha meglazul vagy túlforog. Ha a kúpszög helyes, de a méret nem megfelelő, akkor ez az ortopédiai egység teljes hossza nem megfelelő, ami a beültetés után nemkívánatos eredményeket okozhat.
A köpenyes rendszerű kúpos fúvókás mérőcsapokhoz nem részleges átmérőt mérnek, inkább a munkadarab két mérési helyén mért átmérőkülönbségét mutatják, amelyet aztán összehasonlítanak az etalon, ill. a mester megfelelő mérési helyeivel. Ha a kúp nagy végén az átmérőkülönbség nagyobb, mint a kis végén lévő átmérőkülönbség, a felső fúvókák nagyobb ellennyomást érzékelnek, mint az alsó fúvókák. Ebben az esetben negatív kúpot, ill. nagyobb kúpszöget ír le. Ha a kis végén nagyobb az átmérőkülönbség, akkor az ellenkezője a helyzet, és a mérőkészüléken pozitív kúp olvasható le. Mivel azonban a köpenyes rendszerű pneumatikus kúpmérő eszköz csak az átmérőkülönbségeket jeleníti meg, a két helyen nem jeleníti meg a részleges átmérőt. Bár ez a típusú pneumatikus mérőeszköz a mérőkúp kopására vonatkozóan jó adatokat szolgáltat, és lehetővé teszi a kapcsolat alakzárásának előrejelzését, de azonban nem tud semmit mondani a kúpkomponensek pozicionáló pontosságáról.
Ehhez egy homlokrendszerű (néha karimás kivitelnek is nevezik) pneumatikus mérőeszközt használnak, amelynél a gyűrű alakú befogó a pneumatikus kúpméréshez úgy van méretezve, hogy a teljes kúpot be tudja fogni. Attól függően, hogy hol van az alkatrész referenciafelülete, az alkatrész referenciapontra állása a kúp végén, az egyik karimán (vállon) a felső rész felületével szemben lehetséges. Ez lehetővé teszi az átmérők ismert magasságokban történő mérését (a holtjáték eltérése mellett, mint a köpenyes rendszerű kivitel esetében). A mérőfúvókák további szintje kiegészíthető a konkáv, ill. konvex hengeralak vizsgálatához, v agyis két további feltétellel, amelyek a két illeszkedő komponens (belső és külső kónusz) közötti érintkezési felületet csökkentik.
A pneumatikus kúpmérő eszköz harmadik típusa az előzőleg említett típusok keveréke. Ez lényegében egy köpenyes rendszerű és hosszmérő szenzorral felszerelt pneumatikus mérőeszköz, amelynek referenciapontra állása a referenciafelület felületéhez történik. Ezzel bizonyítható, hogy milyen mélyre merül a pneumatikus mérőeszköz a mérendő részbe. Tehát amíg a kúpszög leolvasható a pneumatikus kiértékelő készüléken, a hosszmérő szenzor kijelzőjén az egyes átmérő mélységadata jelenik meg. Belső kúpos munkadarab mérésekor, ha a kúposság túl nagy, a mérőkészülék tovább merül az alkatrészbe. Ha a kúpemelkedés túl kicsi, az elvártnál kevésbe merül az alkatrészbe. Ha a merülési mélységet mérőtapintóval határozzák meg, ez az érték bármely mérési mélységnél figyelembe vehető az átmérők számításakor.
A felület figyelembe vétele
A pneumatikus méréstechnika nagy pontossága és felbontása miatt ezt a darab felületminősége befolyásolhatja. Ez bonyodalmakat okoz a pneumatikus méréstechnika alkalmazásakor, mivel a használathoz jó felület szükséges. Normál használatnál a mérőfúvókák légárama befedi a darab felületének egy területét. A légáram visszaverődik a felületről a méréshez szükséges ellennyomás létrehozásához. Sima felületen lényegtelen az átlagos felület és az érdességi csúcsok közötti különbség, amely a belső átmérőjű munkadarab esetében szintén minimális játékot jelent. Ha azonban a felület nagyon durva, a terület, ill. a hely, ahol az ellennyomás fellép, jelentős mértékben eltérhet. Ez regisztrálható a pneumatikus mérőkészülék kijelzőjén, és befolyásolhatja a megjelenített átmérőt.
A felület problémái esetén speciális lépések hajthatók végre azok figyelembe vételéhez. Amíg a felületi érdesség Rz 6,3 µm alatt van, az eltolás általában figyelmen kívül hagyható. De még ha a folyamatfejlesztés során felfedett hiba nem is kompenzálható és a tényleges átmérő meg is jelenik a gépkezelő számára. Tekintettel a felület jellegére és reakciójára szabadon lefújó mérőfúvókánál elektronikus erősítők és mérőszámítógépek is bocsáthatnak rendelkezésre megbízható számításokat a közepes vagy maximális átmérőkről.
Végkövetkeztetés
Az ortopédiai precíziós komponenseknek rendkívül magas minőségi szabványoknak kell megfelelni. Az ortopédiai berendezések gyártási folyamata közben mért egyik kritikus méretjellemző a kúpos felületeken az egyes alkatrészek illeszkedésének szűk tűrése. Tekintettel az egyre szűkebb tűrésekre, a mérőkészülékeknek stabilabbnak kell lenniük, és megfelelő tervezési jellemzőkkel kell rendelkezniük, hogy az alkatrészeket megfelelően fogják be. Ezenkívül a szükséges tűrések méréséhez megfelelő felbontással és pontossággal is kell rendelkezniük. A pneumatikus méréstechnika itt egyre inkább a kritikus paraméterek ellenőrzésének elsődleges vizsgálati eszközzé vált.
A cikk szerzője George Schuetz, a Mahr Inc. Precision Gages igazgatója.