Pregiati strumenti di misura per il controllo di qualità nella sala metrologica e nei reparti di produzione, accettazione merci o sviluppo.
Gear Metering Pumps & Meter Mix Dispense Machines with highest accuracy for processing liquids and pastes.
High-precision rotary stroke bearings for backlash-free linear and rotational movements for use in machine and device construction.
per cilindri Tecnologia di misura di forma e posizione Tecnologia di misura alberi Metrologia ottica Portale delle macchine usate
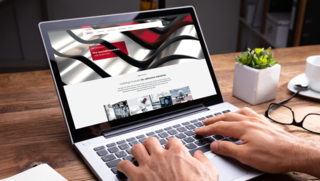
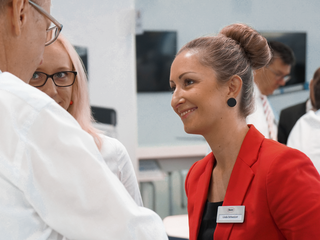
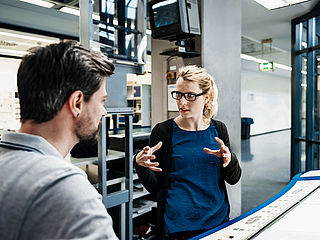
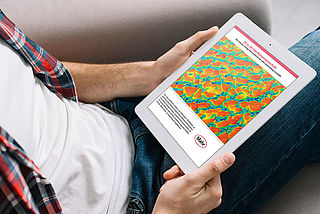
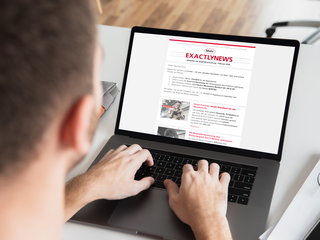
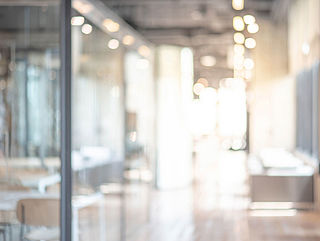
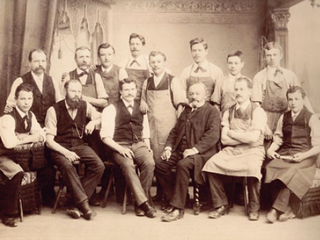
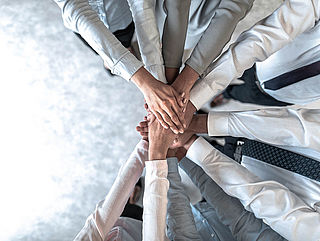
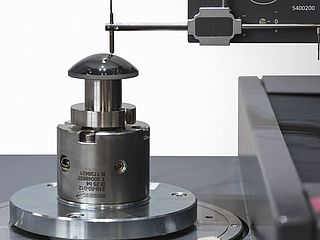
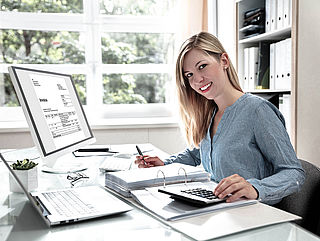
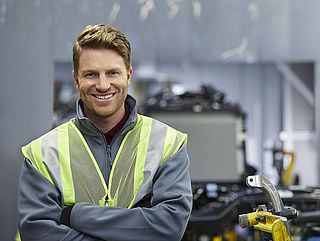
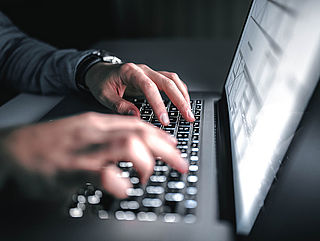
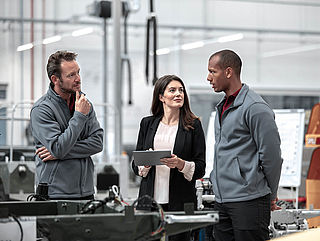
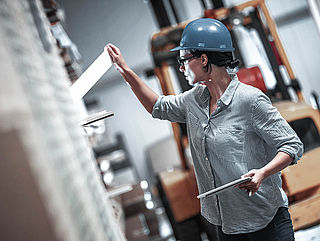
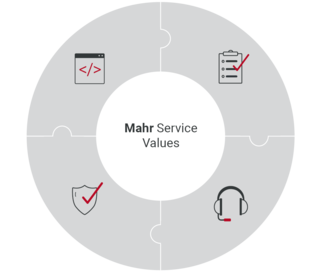
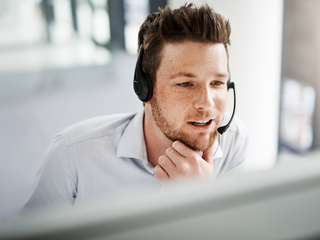
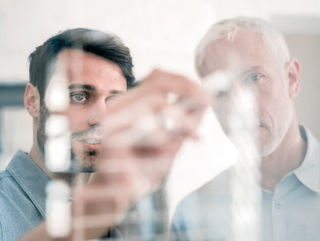
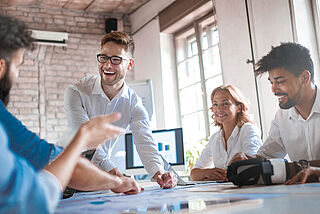
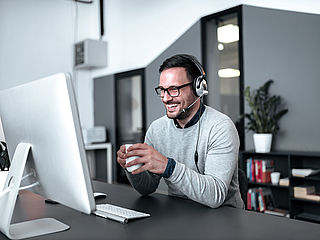
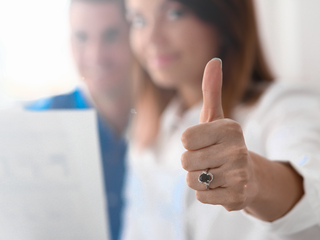
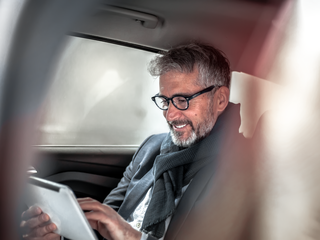
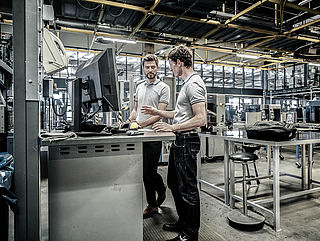
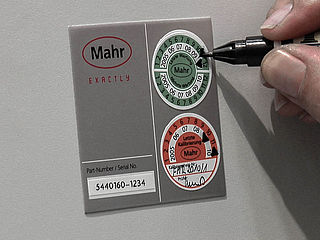
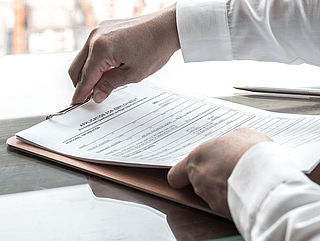
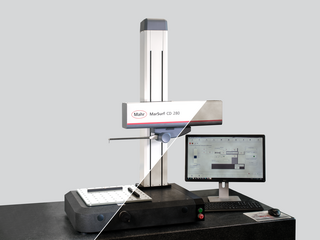
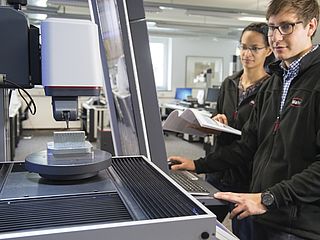
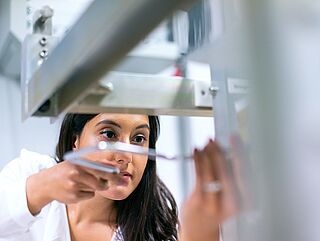
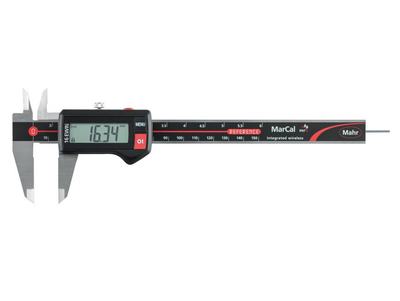
Innovativi strumenti di misura portatili Mahr: Calibri a corsoio, micrometri e comparatori in versione analogica o digitale con trasmissione radio integrata. I comparatori e i campioni di riferimento Mahr sono indispensabili per la metrologia industriale di precisione.
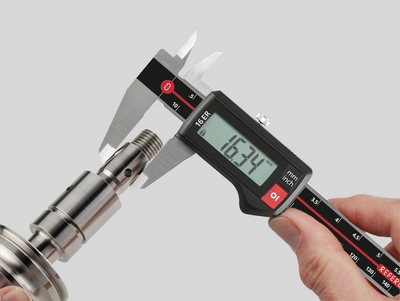
Dall'analogico al digitale, tutta la gamma di calibri a corsoio. Facili da usare, ad alta precisione e senza cavi. Perfetti per un uso efficiente in ambiente produttivo.
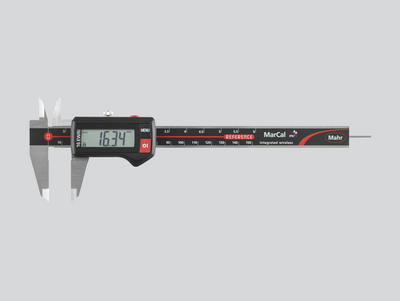
I nostri calibri a corsoio digitali si distinguono per il display digitale di facile lettura, il design moderno e l'abituale precisione Mahr. L'assortimento comprende strumenti di misura per tutte le applicazioni. Le varie interfacce di trasmissione dati e il grado di protezione fino a IP 67 soddisfano tutte le esigenze.
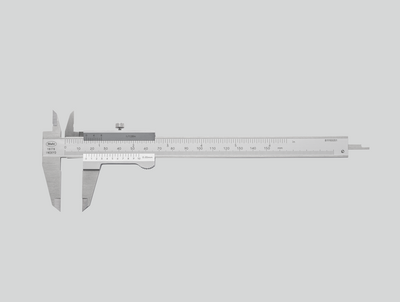
Lettura antiriflesso, acciaio temprato, guide di scorrimento rialzate a protezione della scala e massima precisione. Le caratteristiche di un calibro a corsoio di qualità Mahr con il classico nonio.
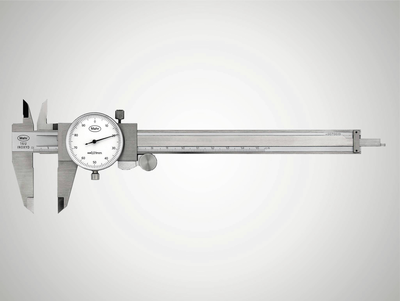
Grande quadrante a forte contrasto e sistema di misura antiurto per una precisione duratura. Il classico meccanico per una lettura veloce e sicura.
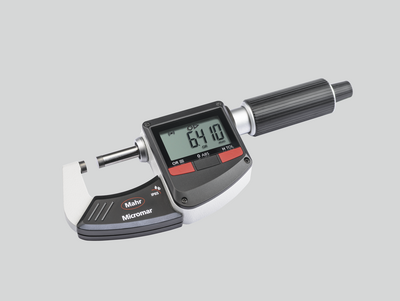
Massima precisione e ampia varietà di modelli. I micrometri Mahr sono disponibili nella classica variante meccanica o in versione digitale e wireless.
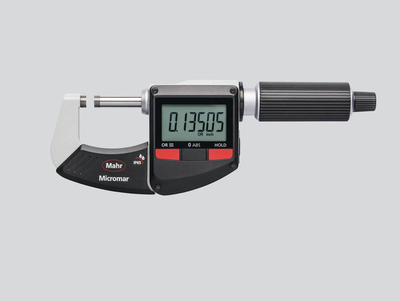
I nostri micrometri digitali per esterni si distinguono per il display digitale di facile lettura, il design moderno e l'abituale precisione Mahr. L'assortimento comprende strumenti di misura per tutte le applicazioni. Le varie interfacce di trasmissione dati e l'elevato grado di protezione fino a IP 65 soddisfano tutte le esigenze.
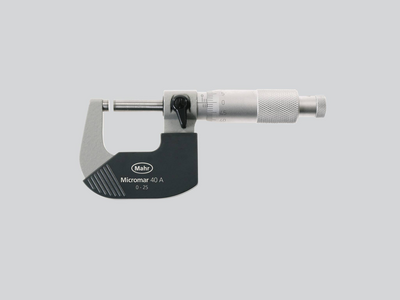
Lettura antiriflesso, pannelli termoisolanti e un mandrino rettificato di precisione per la massima accuratezza. Le caratteristiche di un micrometro di qualità Mahr.

Particolarmente indicato per un test rapido e sicuro di parti di serie (alberi, bulloni, perni). La precisione dimensionale può essere letta a colpo d'occhio utilizzando il misuratore millesimale.
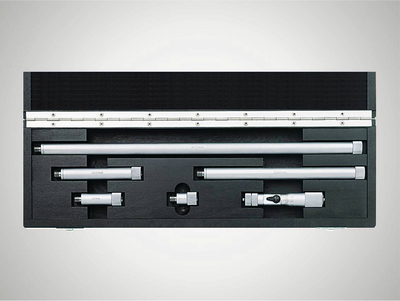
Per misurare diametri grandi e controllare distanze fino a 2500 mm
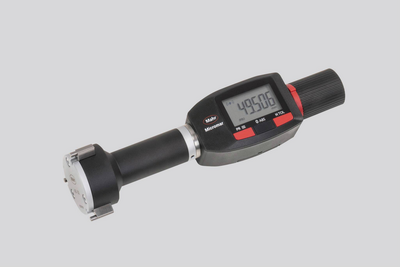
Con indicazione analogica o digitale, a scelta, o come strumento di misura rapido con impugnatura a pistola. Gli alesametri Mahr a 3 punti di contatto forniscono sempre risultati di misura affidabili grazie all'autocentraggio automatico.
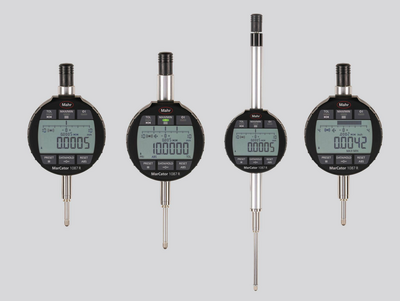
Dall'analogico al digitale, tutta la gamma di comparatori, misuratori millesimali e comparatori a leva. Facili da usare, ad alta precisione e con wireless opzionale. Perfetti per un uso efficiente in ambiente produttivo.
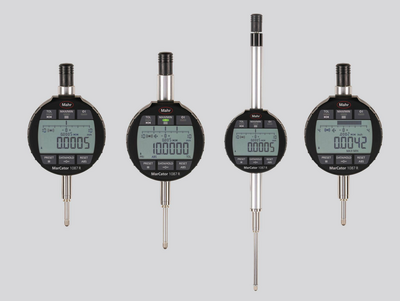
I nostri comparatori digitali si distinguono per il display digitale di facile lettura, la struttura robusta e l'alta precisione Mahr. L'assortimento comprende strumenti di misura per tutte le applicazioni. Le varie interfacce di trasmissione dati e l'elevato grado di protezione fino a IP 54 soddisfano tutte le esigenze.
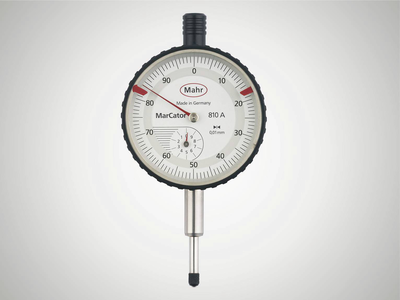
Alta sensibilità e precisione garantite da: solido supporto degli assi del sistema di misura, pignone e ruota dentata di precisione, perno montato in modo ultrapreciso.
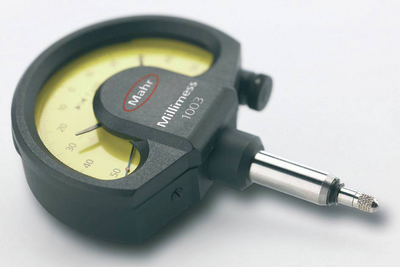
Rispetto ai comparatori analogici, i misuratori millesimali Millimess sono caratterizzati da componenti ancora più precisi, da una maggiore accuratezza e da un errore di inversione molto inferiore. Questi vantaggi emergono particolarmente nei controlli di oscillazione radiale, nelle misure di rettilineità e planarità e nelle misure comparative.
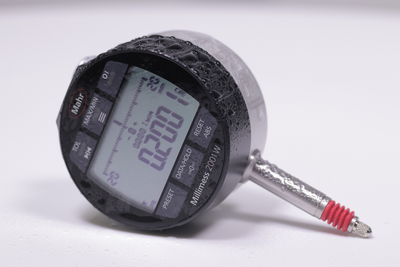
I misuratori millesimali induttivi ad alta precisione Millimess raggiungono risoluzioni fino a 0,2 μm. Le pratiche funzioni di comando, come il controllo delle tolleranze, il rilevamento del minimo o del massimo nelle misure dinamiche, l'indicazione numerica e analogica combinate e la facile trasmissione dei dati, ne fanno uno strumento di misura di precisione indispensabile.
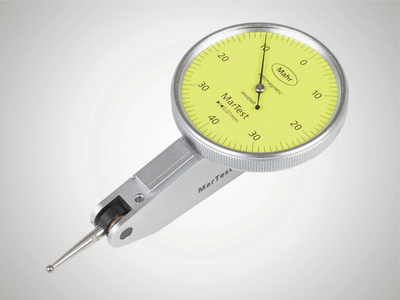
Lo strumento di misura, ottimizzato al computer, garantisce la massima sicurezza e precisione. Per l'uso in officina il display è perfettamente protetto contro graffi o rotture da un quadrante di vetro minerale temperato e contro l'infiltrazione di liquidi da una guarnizione.
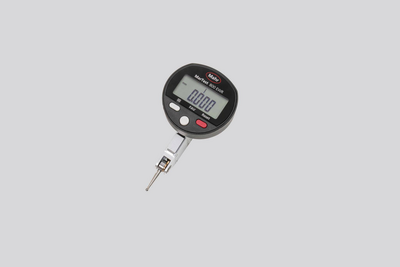
The sensitive computer-optimised measuring tool ensures maximum reliability and precision. For rough workshop use, the display is superbly protected. A seal also provides reliable protection against penetrating liquids.
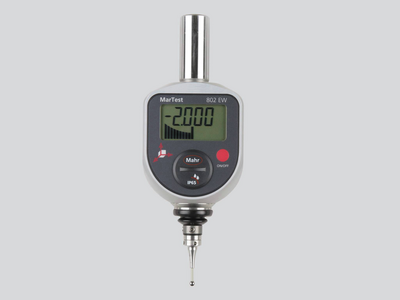
I tastatori di misura 3D Mahr per macchine a CN, centri di lavoro e macchine a elettroerosione riducono i tempi di preparazione e di fermo macchina. Perfetti per la tastatura precisa dei bordi di riferimento su pezzi e dispositivi.
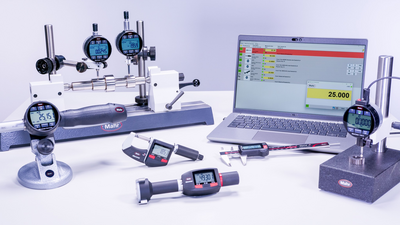
Indipendentemente dallo standard di interfaccia utilizzato (Integrated Wireless, moduli radio esterni, USB, Opto RS232 o Digimatic), MarConnect stabilisce sempre la connessione ideale.
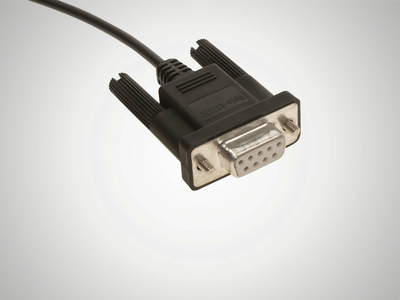
Numerosi strumenti di misura portatili Mahr dispongono di un'uscita dati con interfaccia MarConnect. Indipendentemente da quale standard di interfaccia utilizziate (USB, Opto RS232 o Digimatic), MarConnect stabilisce sempre la connessione ideale.
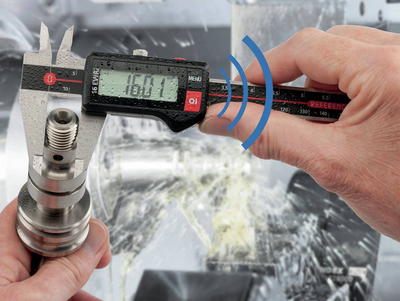
L'assortimento wireless di Mahr assicura risultati di misura accurati con la massima libertà di movimento. Misurate in modo semplice e moderno senza essere limitati dai cavi
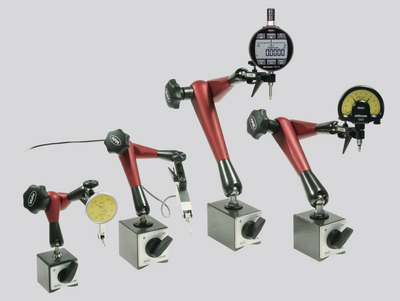
Gli stativi, le tavole di misura e gli strumenti per controlli di eccentricità MarStand garantiscono risultati di misura precisi grazie alla loro stabilità. I vostri comparatori, misuratori millesimali, comparatori a leva e tastatori di misura troveranno qui il supporto necessario.
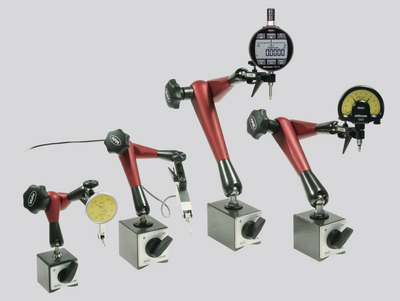
Gli stativi garantiscono risultati di misura precisi grazie alla loro stabilità. I vostri comparatori, misuratori millesimali, comparatori a leva e tastatori di misura troveranno qui il supporto necessario.
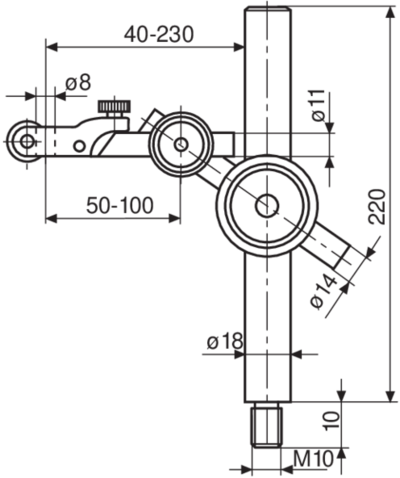
Le aste di misurazione MarStand si utilizzano per soluzioni personalizzate e garantiscono risultati di misura precisi grazie alla loro stabilità. Comparatori, misuratori millesimali, comparatori a leva e tastatori di misura troveranno qui il supporto necessario.
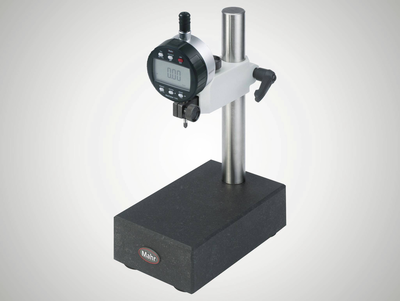
Le tavole di misura sono perfettamente piane e comprendono una colonna di misura stabile e bracci robusti. Le tavole di misura MarStand garantiscono risultati di misurazione precisi grazie alla loro grande stabilità.
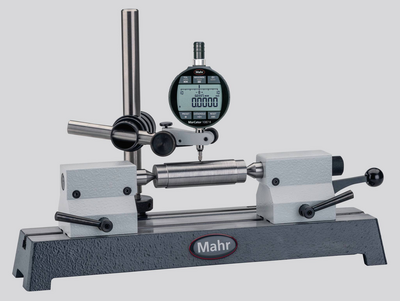
Gli strumenti per controlli di eccentricità rappresentano il metodo più semplice per rilevare gli errori di forma e posizione sugli alberi nell'ambiente di produzione. Grazie alla varietà di modelli, i robusti strumenti per controlli di eccentricità MarStand costituiscono la base per soddisfare gli svariati requisiti dei pezzi e ottenere risultati di misura precisi.
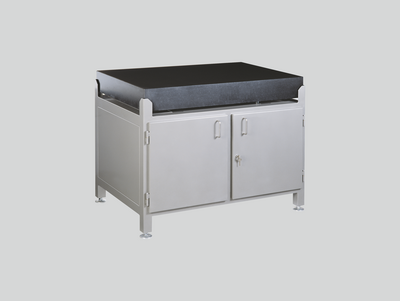
I piani di riscontro in granito costituiscono la base perfetta per i vostri altimetri grazie all'elevata resistenza e stabilità dimensionale.
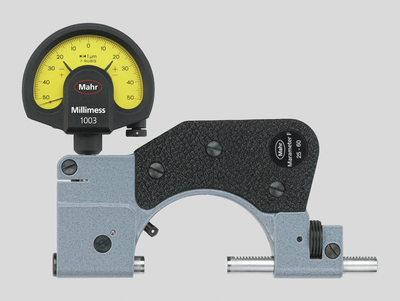
Gli strumenti di misura con visualizzatore, utilizzati come comparatori, sono perfetti per le misure di precisione in fase di produzione. La regolazione in base a un campione di riferimento diminuisce le deviazioni e riduce al minimo l'influenza delle oscillazioni di temperatura sul risultato di misura.
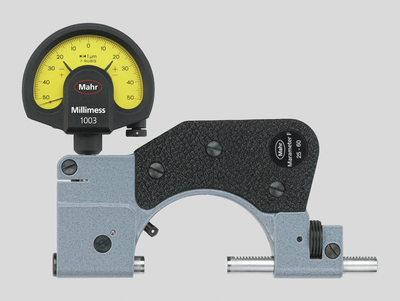
Le forcelle a comparazione sono strumenti di misura perfetti per misurazioni di precisione di pezzi cilindrici quali alberi, bulloni e perni e in particolare per controlli sicuri e veloci su pezzi di serie. La precisione dimensionale può essere letta con sicurezza a colpo d'occhio utilizzando il misuratore millesimale.
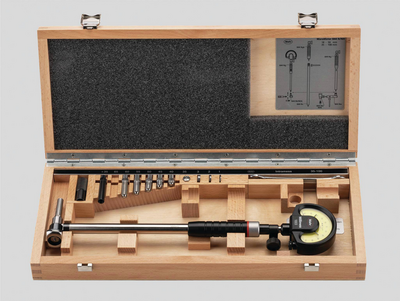
Gli alesametri sono gli strumenti perfetti per le misure di precisione di diametro, rotondità e conicità nei fori.
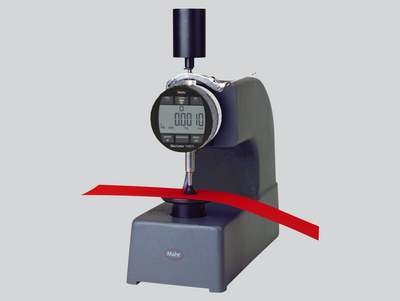
La nostra gamma di misuratori di spessore comprende strumenti robusti e semplici per misurare molto velocemente lamine, lamiere e piastre di qualsiasi tipo.
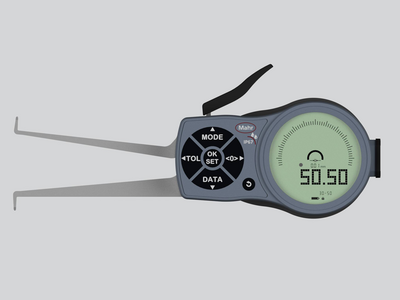
Quando i comuni strumenti, come per es. i calibri a corsoio o i micrometri per interni, non possono essere utilizzati a causa della geometria del pezzo, gli strumenti di misura portatili rappresentano la soluzione perfetta!
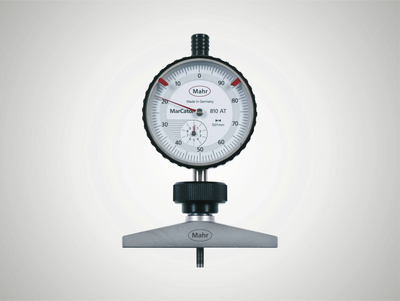
La nostra gamma di ponti per misure di profondità comprende strumenti robusti e semplici per misurare molto velocemente la profondità. Il codolo di serraggio di 8 mm permette l'uso di comparatori, misuratori millesimali e tastatori a seconda dell'operazione di misura da eseguire.
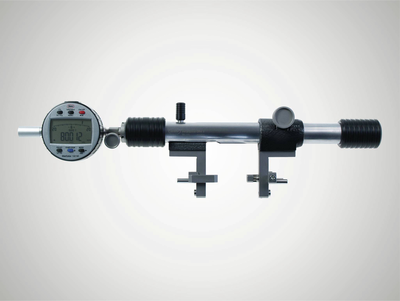
Gli strumenti universali sono i partner perfetti per le misure di precisione in fase di produzione poiché la misura comparativa rispetto a un campione di riferimento riduce al minimo l'influenza delle oscillazioni di temperatura sul risultato di misurazione.
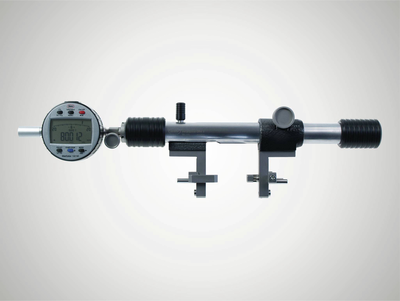
Ingranaggi, filettature, coni o scanalature: gli strumenti di misura universali Multimar offrono una soluzione ottimale per quasi tutte le misurazioni interne ed esterne che non possono essere eseguite con apparecchi standard. Sono quindi a vostra disposizione diversi strumenti base e una vasta gamma di accessori.
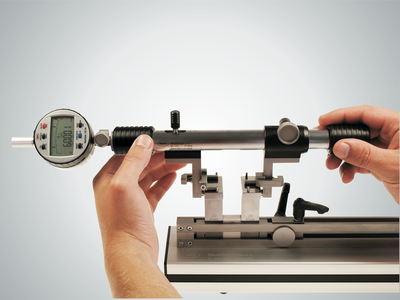
Regolate con precisione i vostri strumenti di misura per interni ed esterni. Con gli apparecchi di preset 844 S sarete ben attrezzati per qualsiasi operazione di misura – anche per maggiori dimensioni.
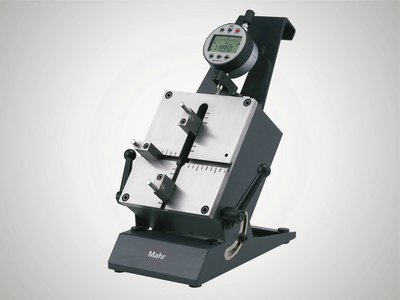
Spallamenti di centraggio, spallamenti stretti o scanalature: gli strumenti di misura universali Multimar 36B offrono una soluzione ottimale per quasi tutte le misure interne ed esterne. Sono quindi a vostra disposizione diversi strumenti base e una vasta gamma di accessori.
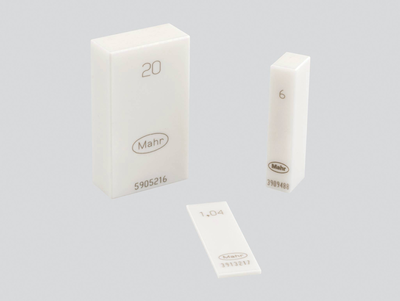
Affidatevi ai campioni e ai calibri Mahr – la base per ottenere risultati di misura precisi.
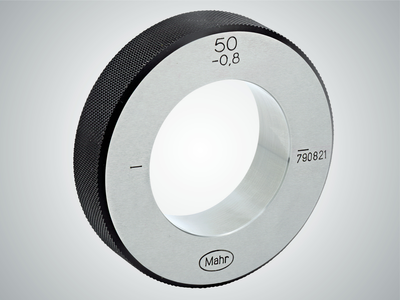
Affidatevi ai campioni di calibrazione Mahr - la base per ottenere risultati di misura precisi.
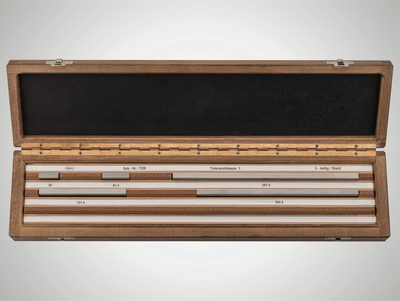
I blocchetti piano paralleli di Mahr sono campioni di riferimento e di lavoro di alta qualità. Scegliete tra 4 classi di tolleranza e 2 materiali per adattarli alla vostra officina e al vostro reparto di produzione o di controllo qualità.
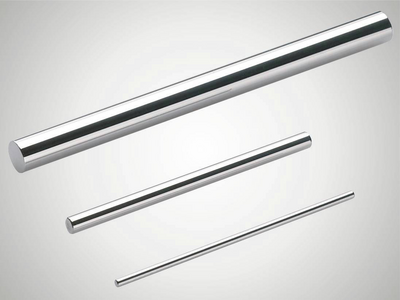
Le spine calibrate di Mahr sono disponibili in 3 classi di tolleranza e in varie versioni. Sceglietele in base alla vostra officina e al vostro reparto di produzione o di controllo qualità.
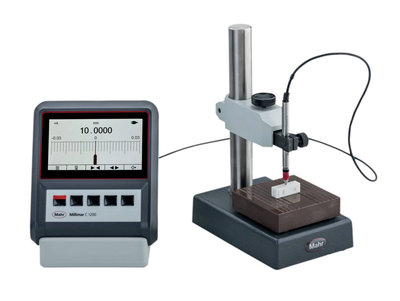
I requisiti dei misuratori elettrici di lunghezza sono molteplici così come le loro applicazioni. massima affidabilità e precisione e un uso semplicissimo.
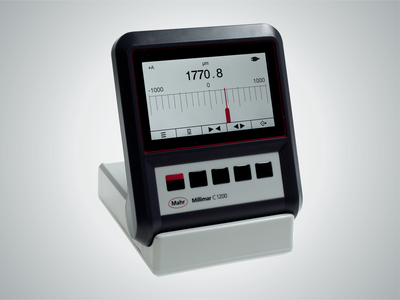
I requisiti dei misuratori elettrici di lunghezza sono molteplici così come le loro applicazioni. massima affidabilità e precisione e un uso semplicissimo. Gli strumenti di misura Millimar, compatti e a colonna, soddisfano proprio questi requisiti.
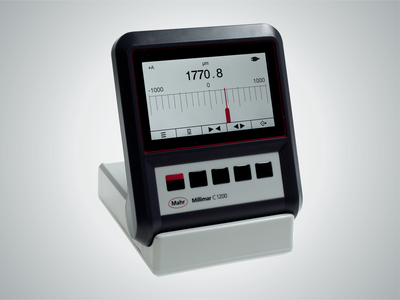
I misuratori di lunghezza Millimar sono compatti, robusti e facili da usare. Sono apparecchi di analisi e visualizzazione di impiego versatile per operazioni di misura di complessità gestibile nell'ambiente di produzione e nella sala metrologica.
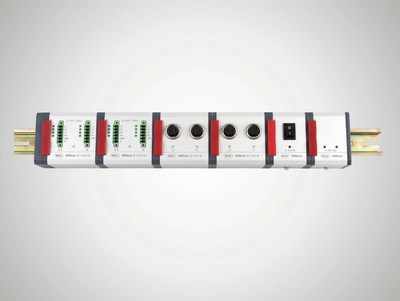
Grazie alle molteplici possibilità di combinazione di moduli e software, avrete l'opportunità di personalizzare più che mai l'ambiente di lavoro e gli utensili.
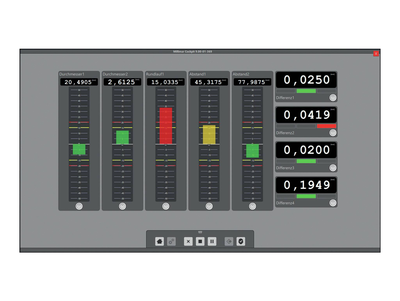
Software universale e intelligente per operazioni di misura complesse in ambienti di produzione
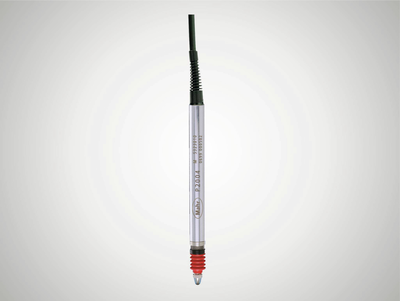
I trasduttori Millimar sono i componenti più importanti della catena di misura. Le loro caratteristiche determinano la qualità dell'intera misurazione. A seconda dell'applicazione sono disponibili tecnologie diverse. Per esempio, i tastatori di misura induttivi Millimar: costruzione solida, impiego flessibile e prezzo interessante.
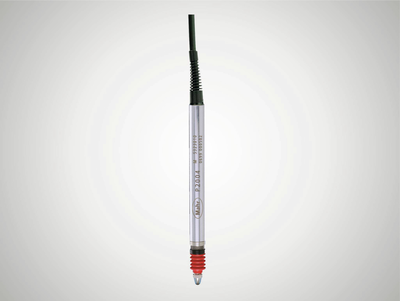
Misure di spessore, oscillazione radiale o concentricità: i tastatori induttivi permettono di rilevare i valori di misura e gli scostamenti indipendentemente dalla forma, dall'appoggio o dagli errori di oscillazione radiale. Il loro grande vantaggio è rappresentato dall'ampio campo di linearità e dalla relativa insensibilità ai fattori di disturbo. I tastatori sono principalmente utilizzati per misure comparative in fase di produzione, ma le funzioni specifiche del sensore possono variare.
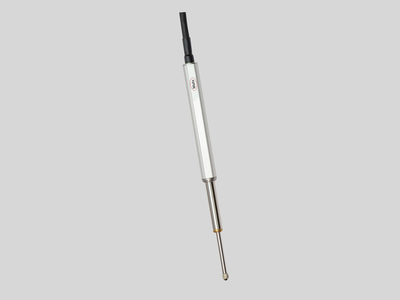
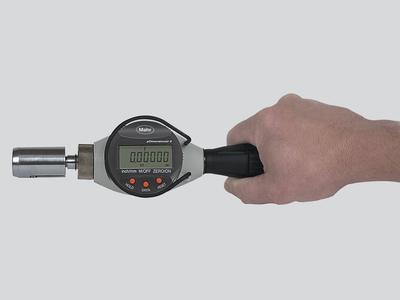
I misuratori di lunghezza pneumatici si distinguono per l'elevata precisione e la stabilità a lungo termine. La misura senza contatto tramite ugelli non danneggia i pezzi. Inoltre è possibile misurare pezzi sporchi, oliati, lubrificati o lappati con sicurezza e senza problemi, poiché le zone da misurare vengono pulite dal getto d’aria.
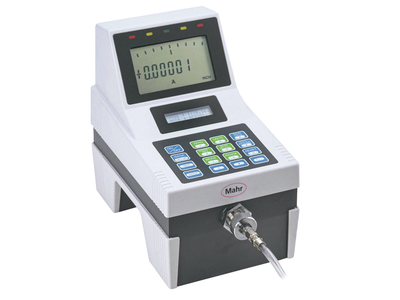
I misuratori di lunghezza Millimar sono compatti, robusti e facili da usare. Sono apparecchi di visualizzazione e analisi di impiego versatile per operazioni di misura di complessità gestibile nell'ambiente di produzione.
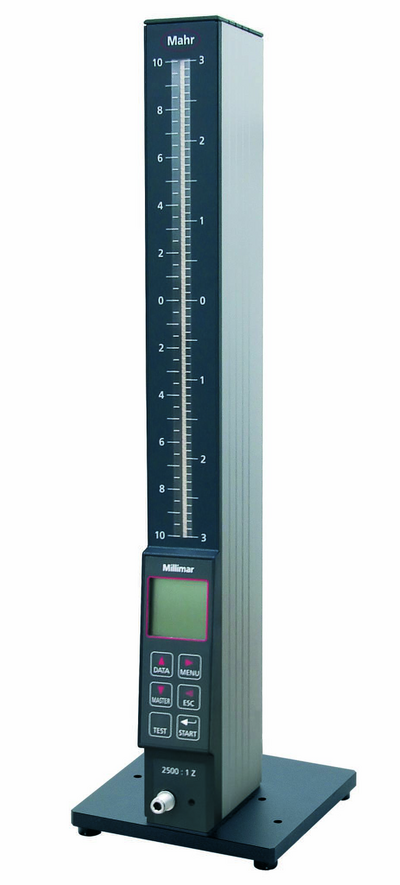
I risultati di misura sono visualizzati su 101 diodi luminosi a tre colori – facilissimi da leggere anche a distanza. Il superamento dei limiti di attenzione e tolleranza programmabili è segnalato con un cambio di colore dei segmenti dal verde al giallo o al rosso.
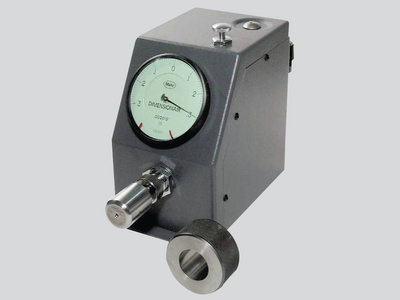
Gli strumenti di misura pneumatici Millimar rilevano gli errori dimensionali in modo rapido e preciso. Da anni si sono affermati come misuratori pneumatici di lunghezza di alta qualità nella produzione industriale e nella sala metrologica.
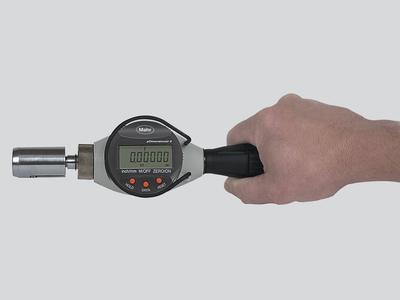
Quando la misura e l'analisi devono essere eseguite in mobilità.
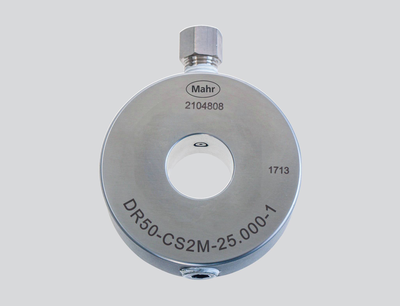
Misura senza contatto con anelli pneumatici, nessun danno ai pezzi.
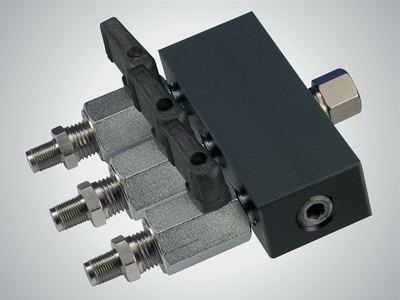
Adattate la stazione di misura all'operazione da eseguire utilizzando gli accessori per strumenti pneumatici.
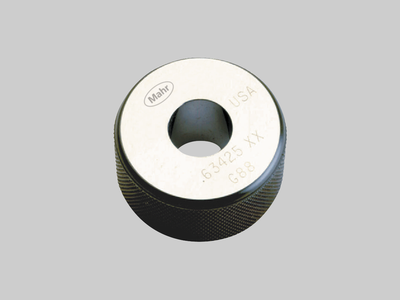
Affidatevi ai campioni di calibrazione Mahr - la base per ottenere risultati di misura precisi
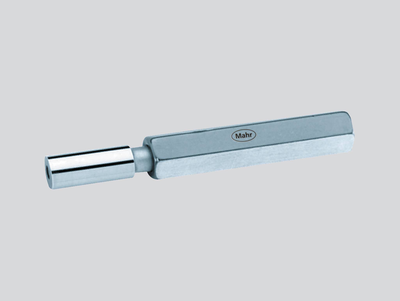
Regolazione di strumenti di misura pneumatici (anelli pneumatici). Accuratamente temprati, invecchiati, rettificati e lappati.
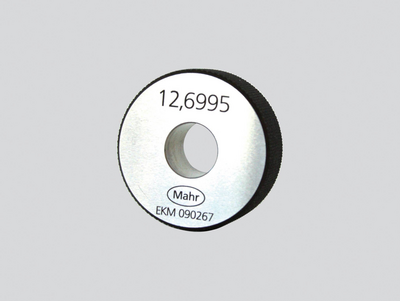
Regolazione di strumenti di misura pneumatici (tamponi pneumatici). Accuratamente temprati, invecchiati, rettificati e lappati.
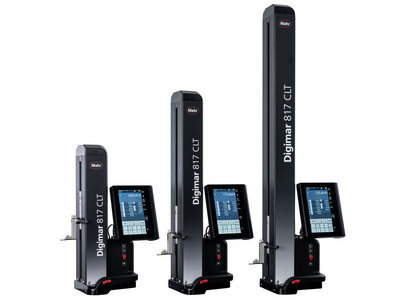
Con le vostre misurazioni mirate in alto? Per questo esiste Digimar!
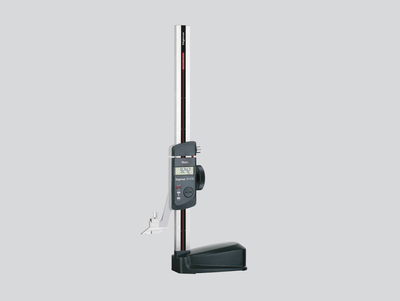
Per la tracciatura e la marcatura dei pezzi in officina. Facile misurazione di altezze e distanze.
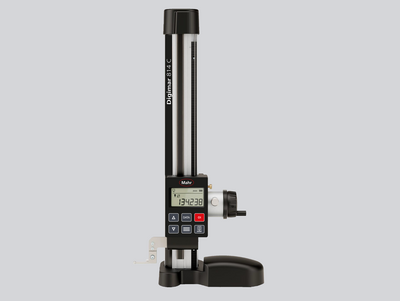
Practical measurement modes and options: The Digimar 814 C makes typical measurement tasks easy
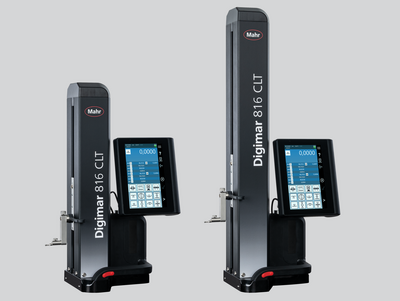
Touch operation, ergonomic handling and a wide range of evaluation options: This is what the Digimar 816 CLT height measuring device stands for.
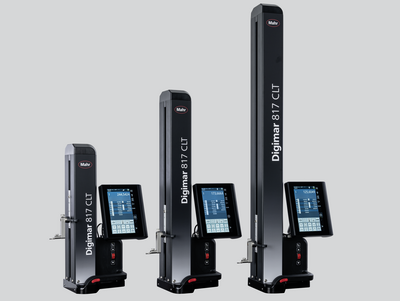
Comando tramite touchscreen, gestione ergonomica e un'ampia gamma di opzioni di valutazione: queste sono le caratteristiche dell’altimetro Digimar 817 CLT.
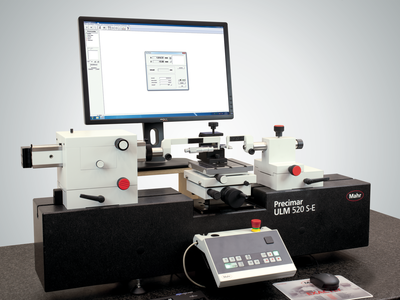
I misuratori di lunghezza si distinguono per la metrologia dimensionale ad altissima precisione - per misure assolute e relative.
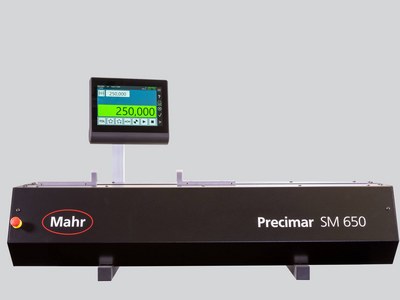
Misuratori di lunghezza e apparecchi di preset universali e facili da utilizzare per la produzione
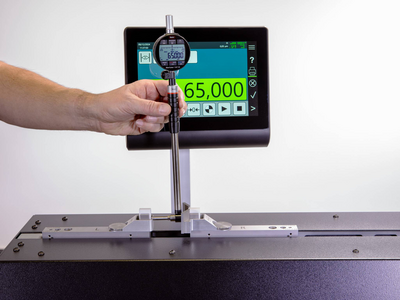
Misuratori di lunghezza e apparecchi di preset universali e facili da utilizzare per la produzione
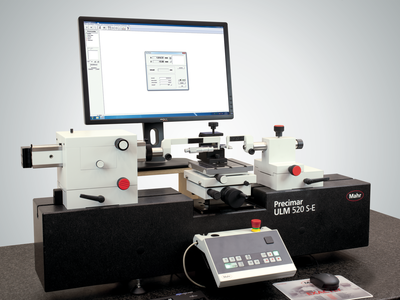
Con la sua vasta gamma di prodotti, dal semplice banco di prova blocchetti, al banco completamente automatico di prova comparatori, dagli strumenti ULM alla macchina di misura universale CiM, ultraprecisa e semiautomatizzata, Mahr offre sempre soluzioni molto flessibili per la produzione, la sala metrologica e i laboratori di calbrazione. In altre parole, metrologia ad alta precisione con processi di misura molto efficienti.
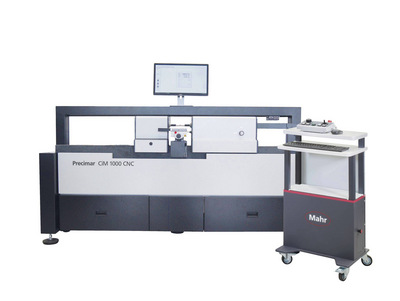
ULM classici o strumenti PLM e CiM motorizzati. Le macchine di misura lineare universali consentono una misurazione facile, veloce e sicura con la minima incertezza.
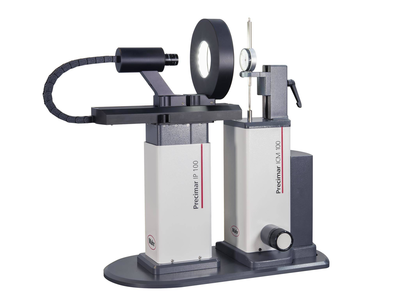
Controllo semiautomatizzato e completamente automatico di comparatori, comparatori a leva, misuratori millesimali e tastatori - in modo efficiente e preciso.
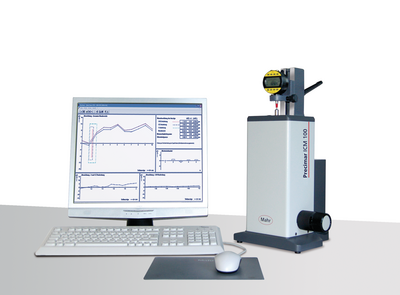
Controllo semiautomatizzato e completamente automatico di comparatori, comparatori a leva, misuratori millesimali e tastatori - in modo efficiente e preciso.
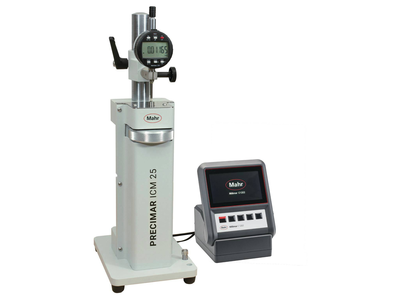
Controllo manuale di comparatori, comparatori a leva e misuratori millesimali - semplicità e precisione
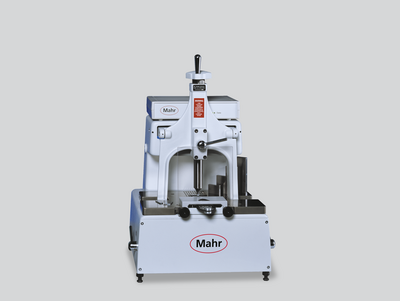
Affidatevi ai banchi di prova blocchetti Mahr - la base per il controllo preciso dei vostri campioni
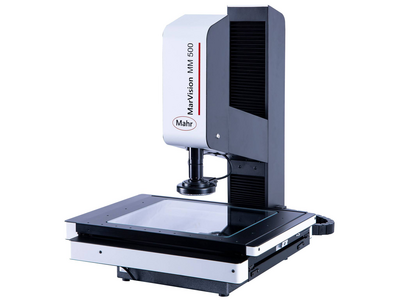
I microscopi sono utilizzati in quasi tutti i settori per il controllo rapido di distanze, raggi e angoli. In laboratorio o in ambiente di produzione.
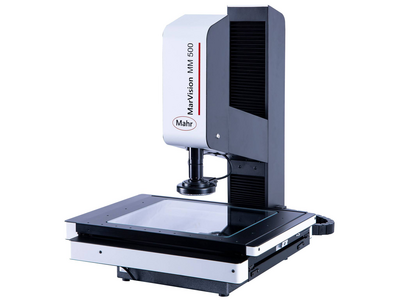
I microscopi sono utilizzati in quasi tutti i settori per il controllo rapido di distanze, raggi e angoli. In laboratorio o in ambiente di produzione.
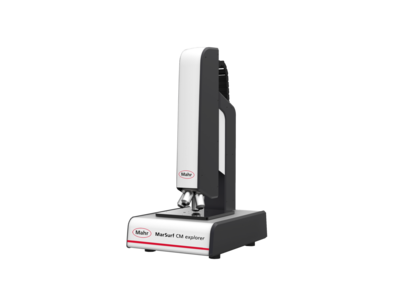
Rugosimetri per l'industria e la ricerca
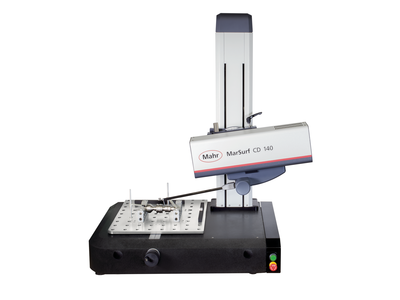
Le superfici funzionali strutturate con tolleranze strette richiedono sistemi di misura ad alta precisione che registrino in breve tempo l'intera topografia di un pezzo o di un oggetto.

La tecnologia di misura dei profili 2D serve a determinare le deviazioni di forma grossolana.

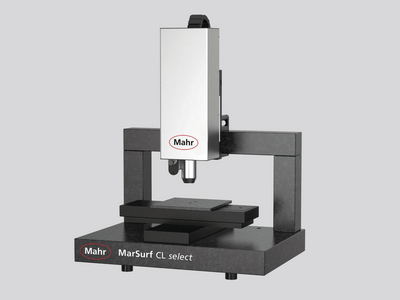
Misurazione precisa dei profili 2D con gli strumenti di misura ottici
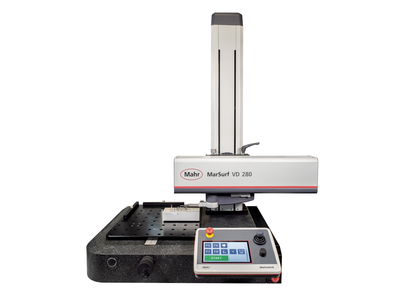
Misure di rugosità e profili 2D combinate: il professionista per tutte le applicazioni
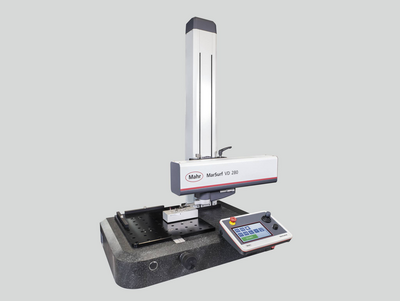
Misure di rugosità e profili 2D combinate: il professionista per tutte le applicazioni
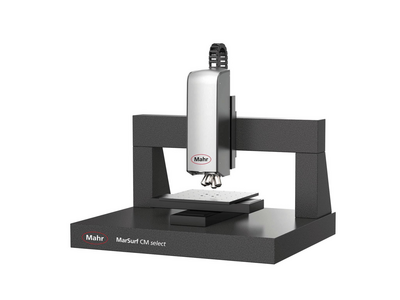
Misura di profili 2D/3D e di rugosità secondo ISO 25178 / ISO 4287
Rugosimetri 3D per l'industria e la ricerca
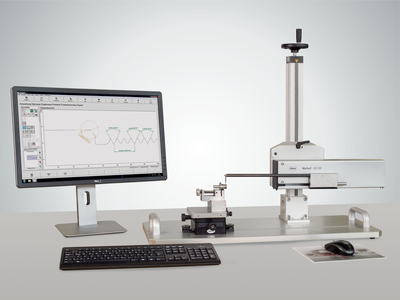
Con gli strumenti di misura portatili potete misurare ovunque!
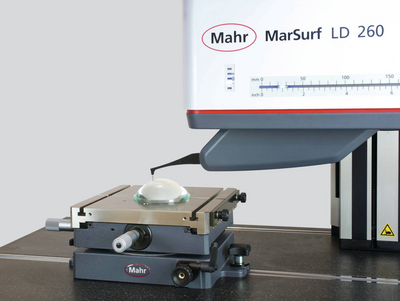
Stazioni per la misura di ottiche ad alta precisione
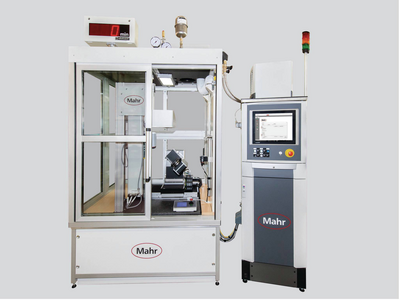
Quando lo standard non basta più: soluzioni personalizzate in base alle esigenze del cliente
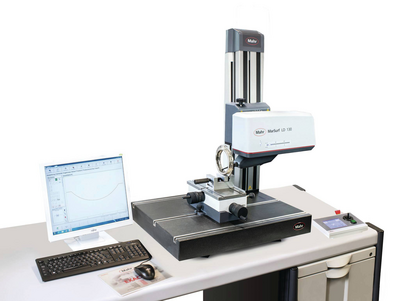
Le superfici funzionali strutturate con tolleranze strette richiedono sistemi di misura ad alta precisione che registrino in breve tempo l'intera topografia di un pezzo o di un oggetto.
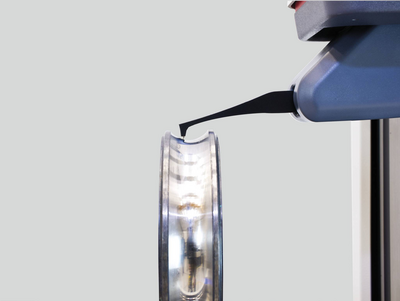
Versatili ed efficienti nella sala metrologica e in laboratorio
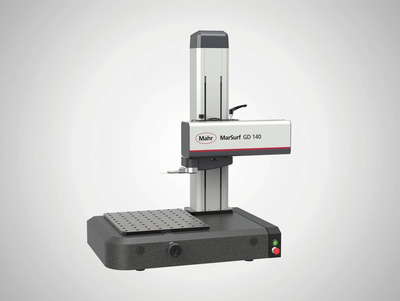
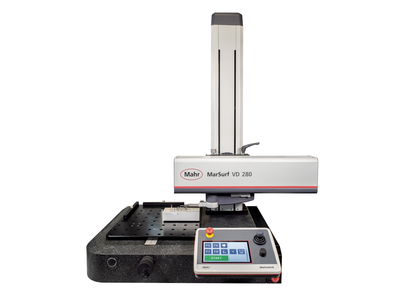
Misure di rugosità e profili 2D combinate: il professionista per tutte le applicazioni
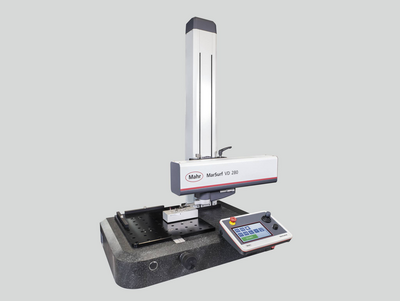
Stazioni di misura a contatto per misurazioni di rugosità e profili 2D
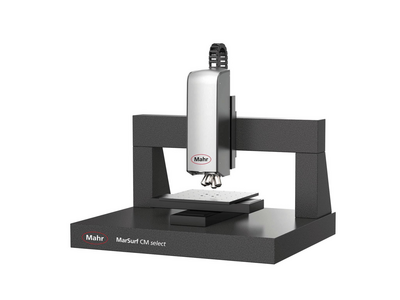
Misure di rugosità e di profili 2D/3D secondo ISO 25178 / ISO 4287
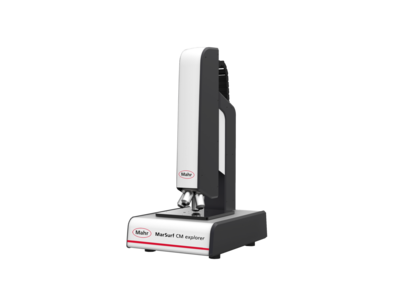
Rugosimetri 3D per l'industria e la ricerca
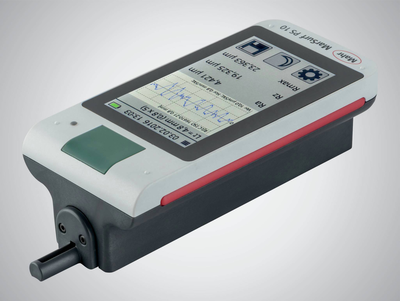
Con gli strumenti di misura portatili potete misurare ovunque!
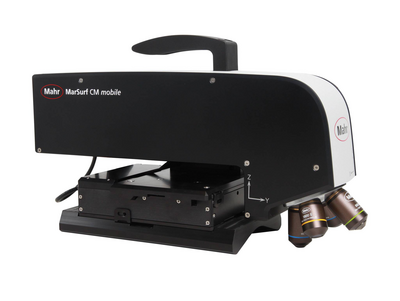
Rugosimetri 3D portatili da
utilizzare sul posto
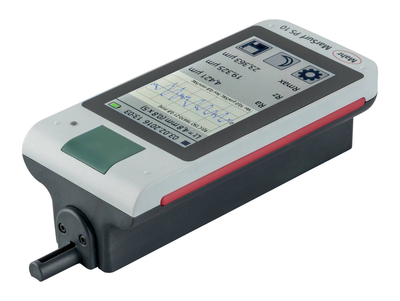
Gli strumenti di misura portatili consentono sempre di misurare esattamente nel punto in cui è necessario ottenere i risultati.
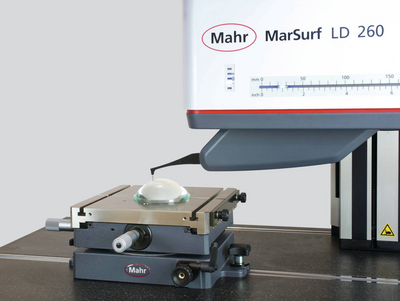
Stazioni per la misura di ottiche altamente sensibili
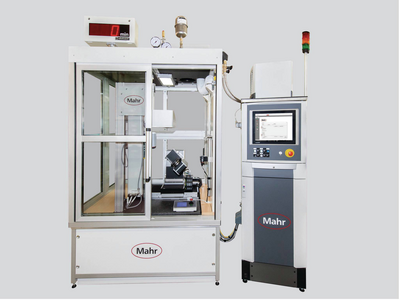
Quando lo standard non basta più: soluzioni personalizzate in base alle esigenze del cliente
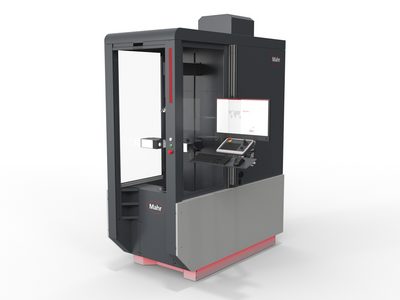
per cilindri
Scoprite le eccezionali caratteristiche di equipaggiamento coniugate a un'estrema flessibilità in termini di dimensioni dei pezzi e aumentate la produttività nell'ambiente di produzione.
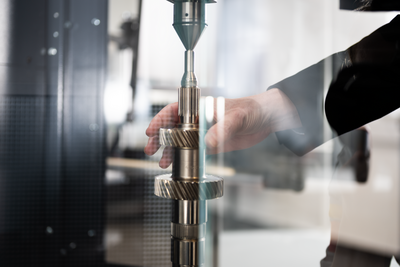
Flexible measurement of workpieces that can be clamped between centers
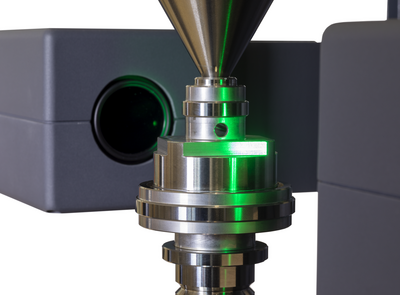
Telecamera a matrice ottica veloce abbinata a sistemi di tastatura ad alta precisione per la misura di numerose caratteristiche su pezzi a rotazione simmetrica.
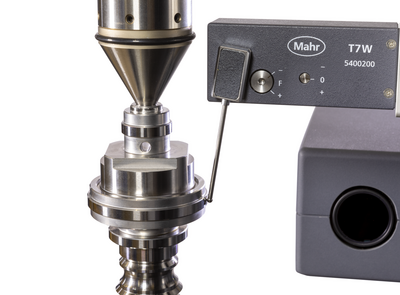
Telecamera a matrice ottica veloce abbinata a sistemi di tastatura ad alta precisione per la misura di numerose caratteristiche su pezzi a rotazione simmetrica.
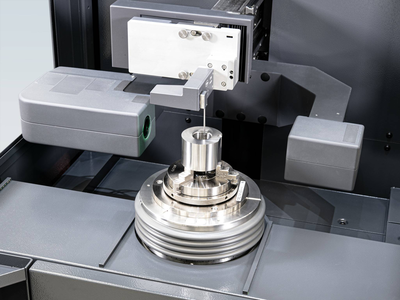
Flexible clamping options and high-precision alignment using a fully automatic centering and tilting table
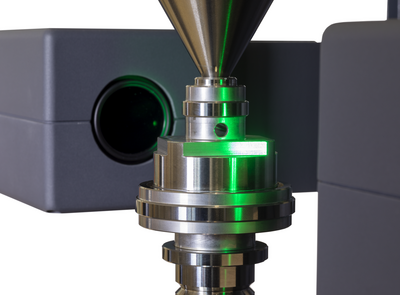
Telecamera a matrice ottica veloce abbinata a sistemi di tastatura ad alta precisione per la misura di numerose caratteristiche su pezzi a rotazione simmetrica. Integrazione di una tavola completamente automatica di centraggio e basculamento per un allineamento meccanico estremamente rapido, possibilità di serraggio flessibili e anche ad es. misure interne.
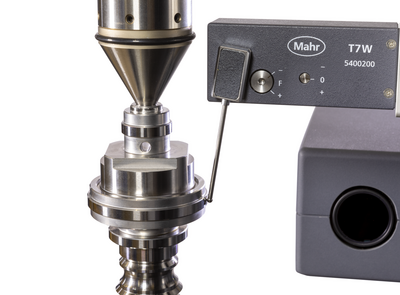
Telecamera a matrice ottica veloce abbinata a sistemi di tastatura ad alta precisione per la misura di numerose caratteristiche su pezzi a rotazione simmetrica. Integrazione di una tavola completamente automatica di centraggio e basculamento per un allineamento meccanico estremamente rapido, possibilità di serraggio flessibili e anche ad es. misure interne.
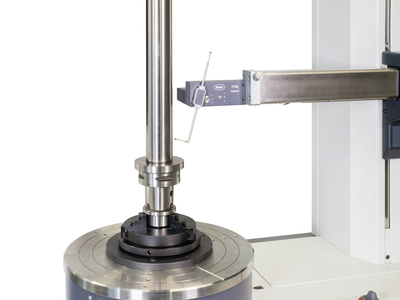
Sistemi per la misura delle tolleranze di forma e posizione, come ad esempio rotondità, planarità, rettilineità o coassialità. Manuali o completamente automatizzati.
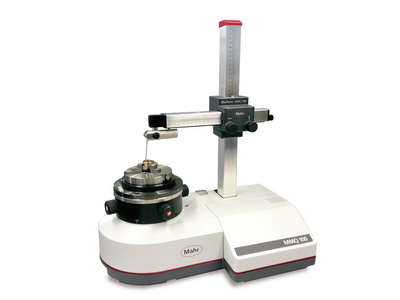
Misurate caratteristiche quali rotondità, rettilineità e oscillazione radiale in modo semplice, economico e con alta precisione. Le nostre macchine manuali di misura di forma sono adatte sia per la sala metrologica che per l'ambiente di produzione.
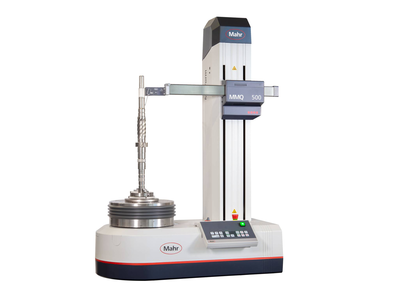
I nostri sistemi automatici di misura di forma consentono di ridurre i costi di processo senza aumentare i costi di valutazione – grazie a strumenti stabili e innovativi caratterizzati dal massimo grado di automazione, flessibilità e precisione.
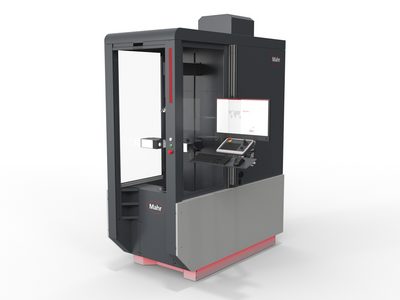
per cilindri
Scoprite le eccezionali caratteristiche di equipaggiamento coniugate a un'estrema flessibilità in termini di dimensioni dei pezzi e aumentate la produttività nell'ambiente di produzione.
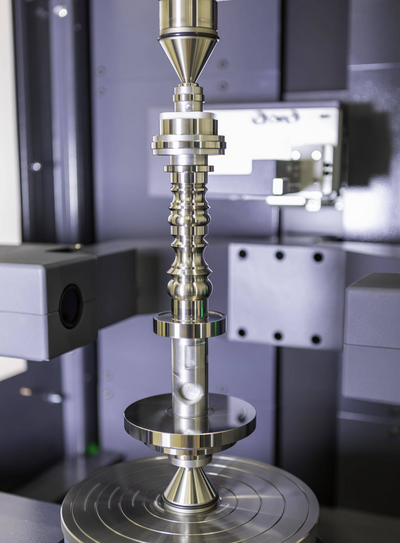
Flexible measurement of workpieces that can be clamped between centers
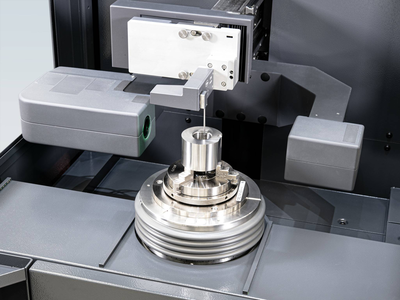
Flexible clamping options and high-precision alignment using a fully automatic centering and tilting table
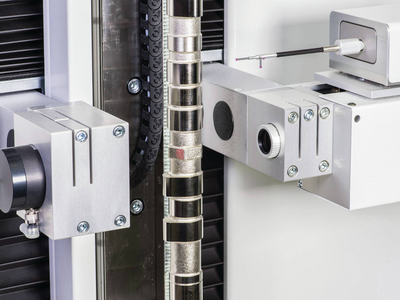
Dispositivi di misura alberi ottici e a contatto per l'uso in ambienti di produzione difficili. Misurazione completa di tutti i comuni pezzi simmetrici all'asse di rotazione.
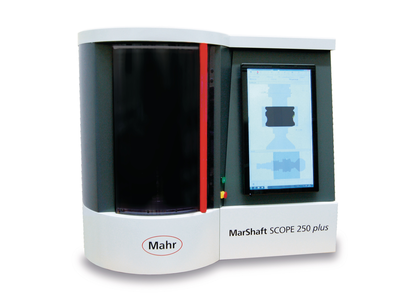
Macchine ottiche di misura alberi universali, completamente automatiche e robuste per l'uso in ambienti di produzione difficili.
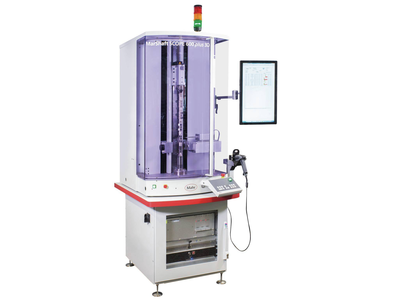
Macchine di misura alberi ottici/a contatto per l'uso in ambienti di produzione difficili. Misura completa di tutti i comuni pezzi simmetrici all'asse di rotazione.
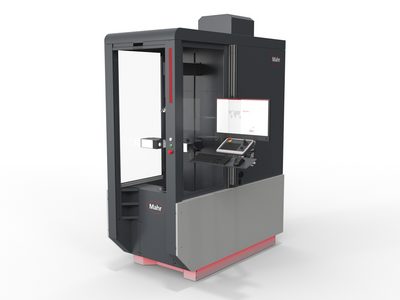
per cilindri
Scoprite le eccezionali caratteristiche di equipaggiamento coniugate a un'estrema flessibilità in termini di dimensioni dei pezzi e aumentate la produttività nell'ambiente di produzione.
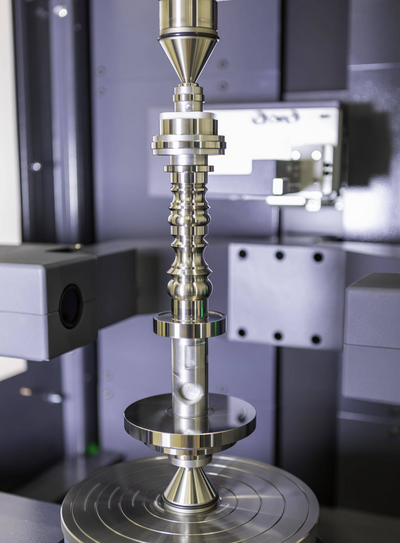
Flexible measurement of workpieces that can be clamped between centers
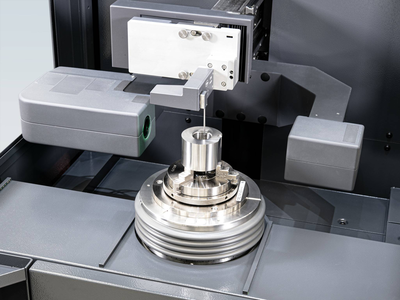
Flexible clamping options and high-precision alignment using a fully automatic centering and tilting table
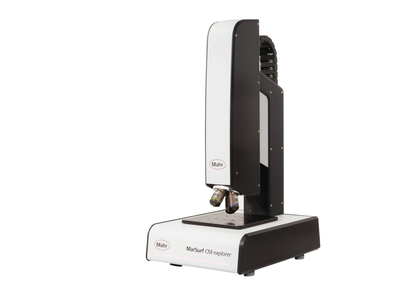
Ampia gamma di tecnologie e prodotti per il rilevamento veloce senza contatto di superfici e geometrie.
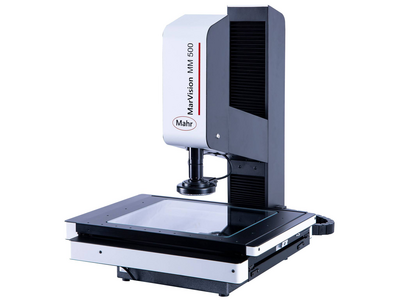
I microscopi sono utilizzati in quasi tutti i settori per il controllo rapido di distanze, raggi e angoli. In laboratorio o in ambiente di produzione.
Determinazione della rugosità, dei profili 2D e di molti altri parametri di superficie.
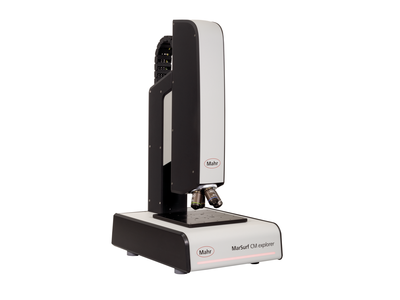
Rugosimetri per l'industria e la ricerca
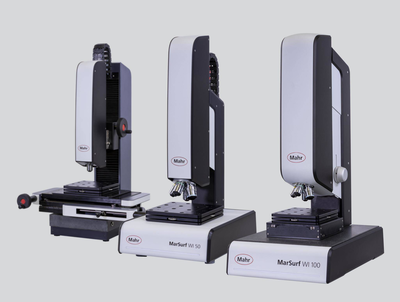
Minime rugosità con precisione nanometrica
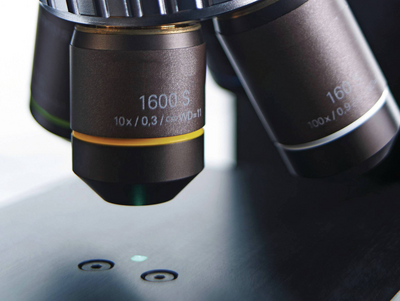
Analisi ottica di geometrie e topografie di superficie
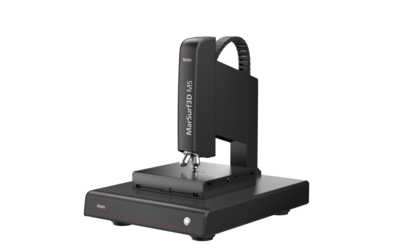
Surface metrology for industry and research
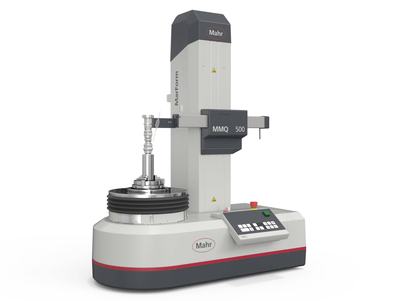
Sistemi revisionati di comprovata qualità Mahr
With AI on a knife's edge
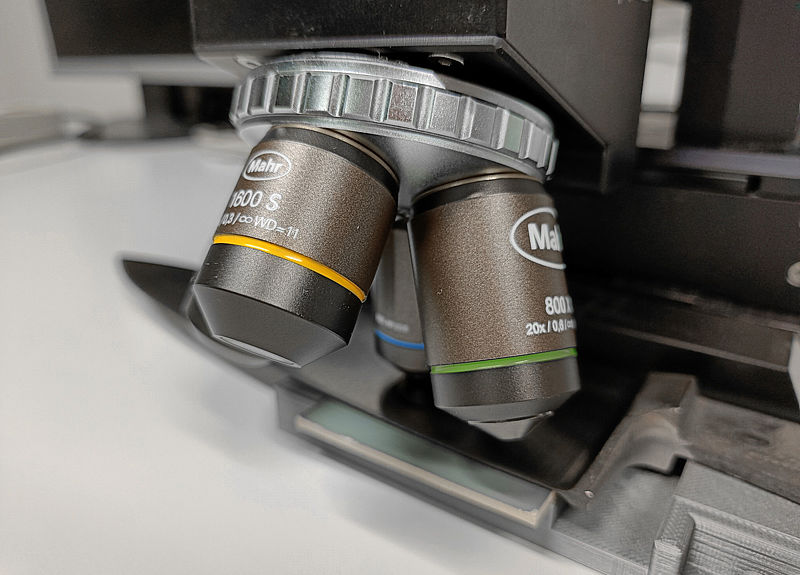
Knives, blades and other cutlery have been produced in Solingen for centuries. Even today, around 90 percent of German cutlery and flatware manufacturers come from the city in the Bergisches Land region, which has had the official name affix "Klingenstadt" since 2012.
In most cases, the quality of these metal goods is checked by the human eye or simply by finger testing. But that could soon change: The research project "MuPro2" at the Chair of Reliability Engineering and Risk Analysis (LZR) at the University of Wuppertal has spent more than three years looking at how quality control can be carried out fully automatically using artificial intelligence (AI) – and thus completely independently of the human factor.
From the tip of the blade to the bolster
As part of the project, a manufacturer of high-quality kitchen knives commissioned the chair to launch an automated, 100 percent reliable surface quality control process. The knives are forged from different steel alloys, ground, finished and inspected – up to 55 manual work steps take place, including shipping, and from the tip of the blade to the bolster, every detail must be right down to the micrometer.
The research team led by Dr.-Ing. Marcin Hinz, senior engineer at the Wuppertal chair of Professoer Stefan Bracke, has already been working on the practical application of artificial intelligence and machine learning for ten years. At the LZR, they are primarily involved in research projects, industrial cooperation and courses on complex technical products and production processes. The researchers focus on data analysis in product development and manufacturing.
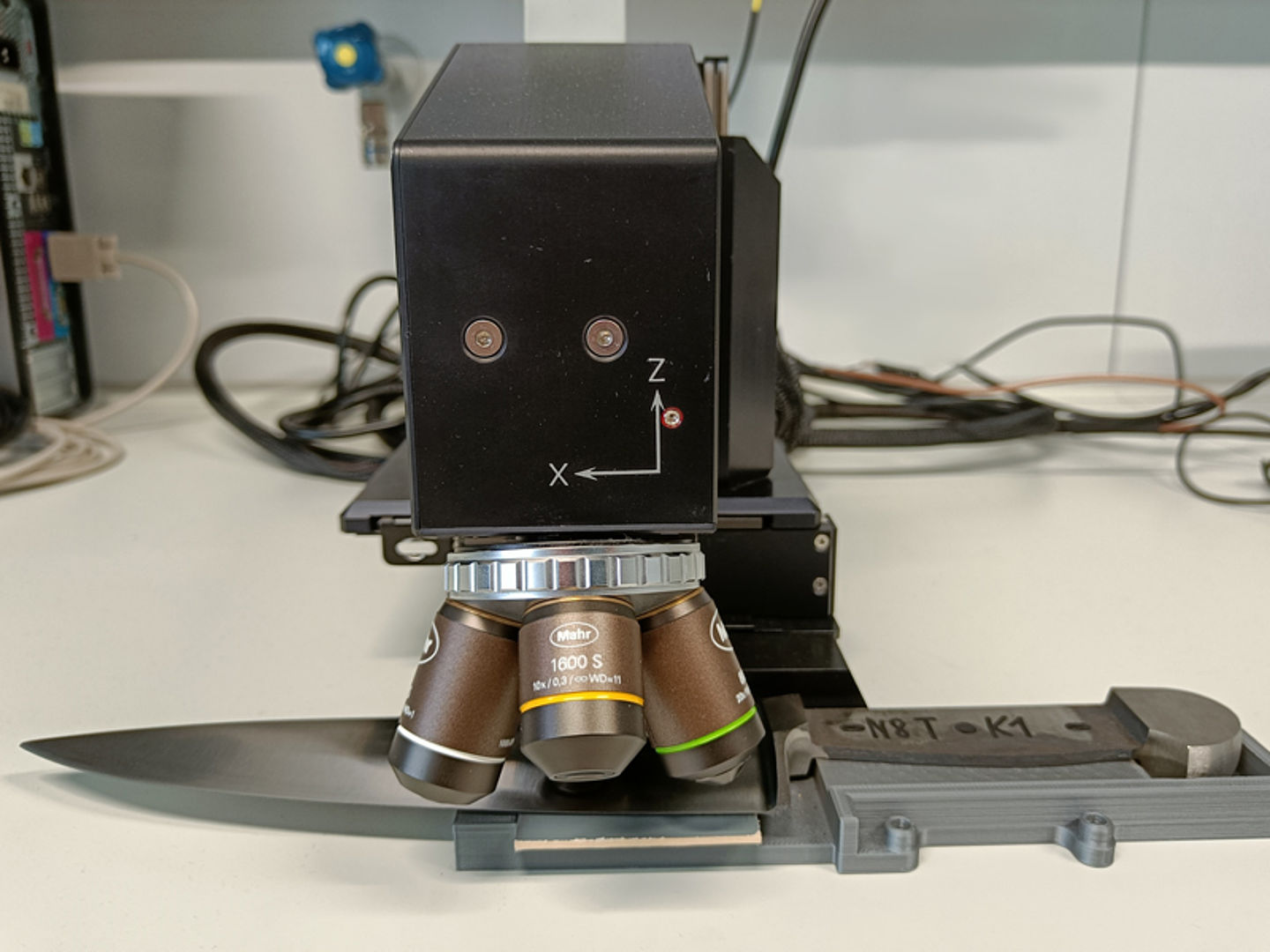
Learning on the basis of huge amounts of data
"In order to obtain the relevant information for an AI-supported image evaluation of the knife surfaces, we first needed precise 3D measurements," explains Hinz. This is because the cameras for image evaluation must be able to reliably detect defects and "learn" them beforehand through AI. Huge amounts of data are required for this.
In order to generate surface data, metrology specialist Mahr came into play. Mahr's GAM 3D Surface business unit in Oberhausen provided the researchers with a MarSurf CM mobile for two weeks to measure the surfaces of the knives for roughness using 3D scan.
The optical measurement system of Mahr's MarSurf CM mobile is based on confocal technology, and its typical measurement time is between five and ten seconds. The 3D measuring device can be used to perform ISO-compliant roughness measurements, analysis of 3D structures and measurement of geometries. The evaluation of structuring and volume parameters is automatic.
Algorithm decides on quality
For the knife project, the scientists developed two test setups with cameras for different knife types in each case. The first test rig was equipped with a standard camera system, the second additionally with a macro lens and two LED spotlights. The test specimens were knife blanks that were already shaped and finely ground – "plated," as the Solingen technical term for this is. In total, more than 2,500 knives were to be tested, 1,750 of them with the Mahr device.
In order to be able to use the corresponding Mahr evaluation software, an algorithm was written especially for the university. Several machine learning algorithms were fed with this data, trained and evaluated. In the process, the algorithm alone decided on the quality.
Hit rate of almost 100 percent
As Marcin Hinz reports, the test setups produced the desired results: "The reliability of the algorithm was extremely high, the rate was 80 percent with tactile measuring equipment, and almost 100 percent with 3D equipment."
The knife manufacturer is now looking into the possibility of installing such intelligent camera systems at upstream production stations in order to be able to intervene in ongoing processes if necessary – and thus specifically avoid scrap and reworking.
In addition, there was also the short-term consideration of integrating the measuring technology directly into production, but this was ruled out for cost reasons. "There is a lot of dust, dirt, oil residues, chips in the production line – it would be much too bad for the device. However, the CM mobile has supported us perfectly in building up a solid basic knowledge," says Hinz.
Originally, the project was not intended to be that big and was only a small study. However, the success and the simple combination of 3D surface analysis, data evaluation and teaching of the algorithm opened up a huge field of research, as Hinz explains. In this respect, one can look forward to follow-up projects.
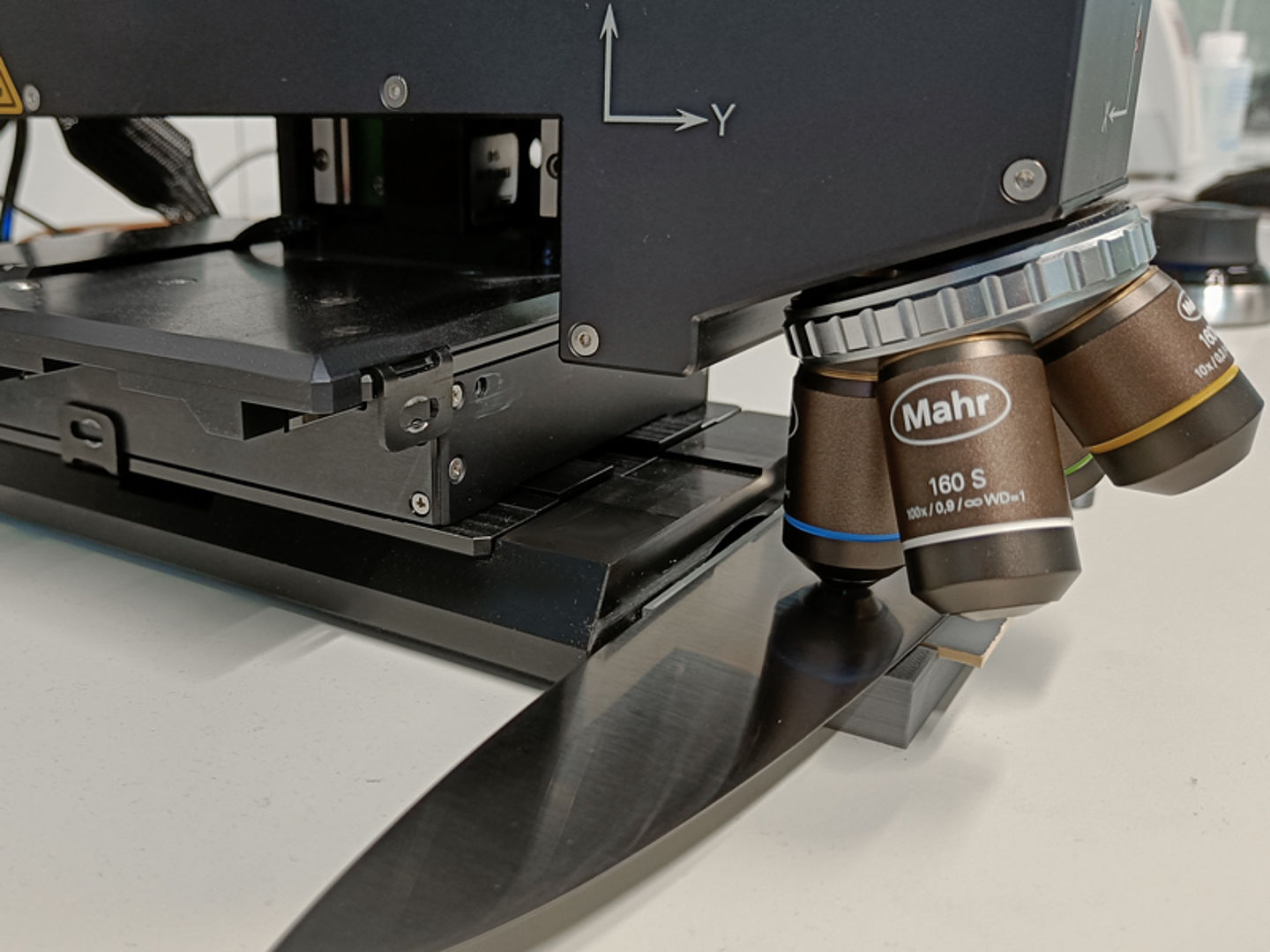